Improved routing system for driverless Agrointelli tool-carrier
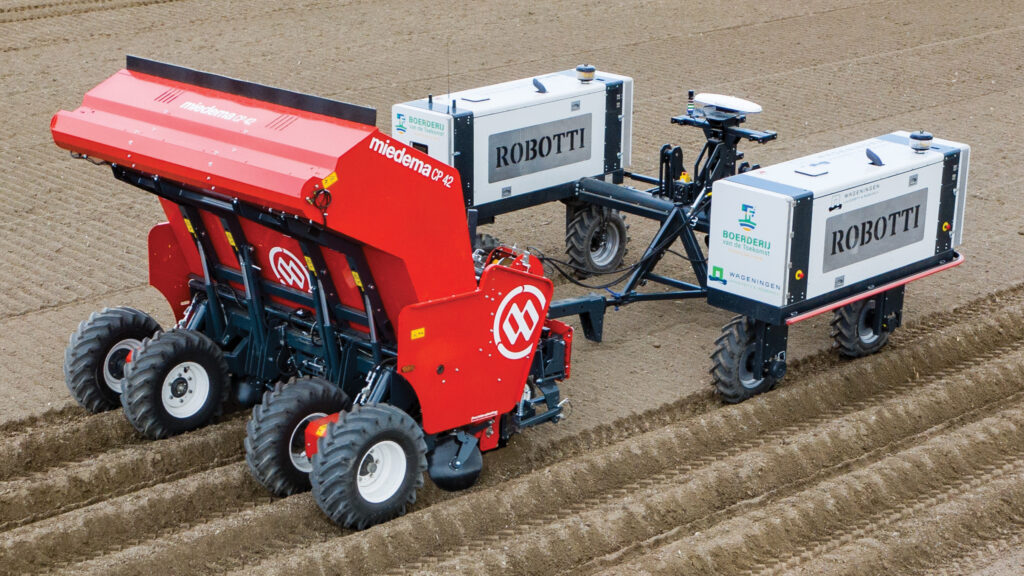
Software upgrades have brought a number of new and enhanced features to the Robotti self-driving tool carrier, including new route patterns, a dynamic route plan preview, and the ability to work in different directions within the same field.
Simpler “jobs done” documentation management is also part of the upgrades package for a machine that handles implements including planters, drills, hoes and applicators up to 2.5m wide between its four hydro-driven wheels.
See also: Video: Revolutionary driverless Robotti sets to work on UK soils
Mechanically, things are largely unchanged – the Robotti LR is powered by a single 72hp diesel engine – but the 750kg-capacity implement hitch can now be lowered and lifted on the move for smoother implement engagement with the soil, and there is electronic selection and setting up of hydraulic valves.
Two more route patterns can be configured for the self-guiding machine to follow in addition to the existing single-row and multiple-row up-and-down routes.
The so-called “coiled” pattern (row sequence 1, 3, 2, 5, 4, 6) and the “back and forth” (odd rows across the field, then even number rows back) ensure the wheels on both sides always run on soil in the same condition.
Agrointelli engineers say this helps with stability and keeps the machine on an even keel, especially in crops grown in raised beds, versus operating with two wheels on untouched soil and two on previously worked ground.
Refilling
When planting, drilling or applying sprays or fertiliser, the new work capacity-based planning feature allows users to programme the maximum distance the Robotti can cover before it must be restocked.
It will then automatically stop at the headland just before the limit is reached or move to a gateway or other predetermined location ready for a top-up.
Irregularly-shaped fields can now be divided into two or more areas with routes set at different angles as part of a single routing plan for that field, and there is a new plan preview function.
This enables users to see on-screen a walkthrough of how the Robotti will navigate the field to verify that the plan is accurate and whether some fine tuning is needed so that every detail will be precisely translated into on-field actions.
Custom log-book downloads using the new Smart Data Transfer function aims to streamline record keeping, and Robotti portal revisions include detailed operation notes and summaries, and the option to edit default job names to something more meaningful – such as “second spring weeding”, for example.
In addition, the CropEye crop and weed imaging and analysis system has been enhanced with an “action maps” function highlighting areas of the field that need attention, and routing plans can be prepared that, for example, instruct a hoeing Robotti to tackle weeds only in areas that need it.