Muck and slurry special: Separators ease storage problems
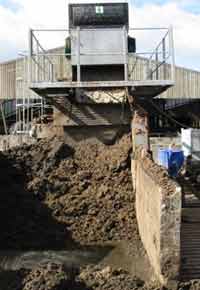
Separating solids from the liquid fraction of farm slurry can ease storage problems and improve application, and there is plenty of kit available to do the job.
Slurry is bulky stuff and not always the easiest material to handle. It flows, but not without considerable encouragement and it can be pumped, but only through large-bore pipes over relatively short distances.
When stored in tanks and lagoons, slurry settles out, so agitation is needed to maintain a fluid consistency. And while it can be spread evenly, getting it on to the land mostly involves heavy machinery.
One way around these difficulties and drawbacks is to separate the solids from the liquid so that these two very different materials can be stored and handled in ways that best suit them.
Separation reduces the volume of storage required for solids by 20-30% and the liquid can be applied to grassland or arable crops by a low-cost irrigation system. Solids extracted from slurry, meanwhile, can be stockpiled and applied to grassland or crop stubbles by conventional manure spreaders.
For some producers, this may be enough to avoid having to extend conventional storage facilities to cope with the latest NVZ spreading restrictions or herd expansion.
Most separators work by sweeping slurry across a screen that allows the liquid to drain through while retaining the solids. Others use screws that exert more pressure on the material to extract more moisture.
Groundhog
The Groundhog slurry separator from Pollution Control and the similar unit from NC Engineering are in the former camp, and have two fixed concave screens with sweeping elements working on the inner surface.
Liquid is free to drain by gravity as the material is brushed over the first screen, but in the second section a pair of rollers add a squeezing action to encourage separation.
The Groundhog unit comes in two sizes that, depending on slurry consistency, will handle liquid flows of 26cu m/hr and 54cu m/hr.
Pollution Control’s Groundhog Green Machine also uses a screen separation process to remove debris from dirty water before it is pumped and distributed automatically through portable or buried mains to a low-rate sprinkler system in the field.
Carier
The Carier Rotoscreen separator from Linton Solutions also squeezes liquid from solids. But in this case there are two pairs of rollers, one on the inside and one on the outside of a rotating barrel screen.
Raw slurry is fed from above, liquid passes through the top half of the screen and a scraper removes the solids.
The Rotoscreen comes in two sizes: the RS400 is rated at 2-30cu m/hr processing cattle slurry, while the RS1000 is rated at 8-60cu m/hr.
Alvan Blanch
Tumbling solids from liquid within a specially woven and tensioned wire mesh screen is how the Alvan Blanch rotating-barrel separator works.
Slurry is fed in at one end of the screen, which is set at an incline, and as the free liquid passes through the mesh to be piped away to a storage tank, the solids fraction works its way down the barrel in a spiral motion until it is deposited in a stockpile.
Alvan Blanch says the simplicity of the unit – there are no squeezing rollers or other mechanical devices – makes it a reliable device with relatively low maintenance requirements and costs.
There are two versions, with nominal maximum capacity of 60 and 100cu m/hr. A dewatering screw can be added to the installation to reduce the water content of the separated solids by a further 10%.
Swea
The twin-screw separator from Swedish manufacturer Swea – represented in Britain by Ocmis Irrigation – acts on material that has been dewatered initially by being swept across an upward inclined screen by a series of brushes.
This removes about 60% of the fluid, after which the twin interlocking screws remove more to produce a material of up to 45% dry matter at rates from 8-40cu m/hr.
Bauer
Bauer also has a screw device in its range, having acquired the German manufacturer FAN Separator and its solids-liquids separation technology.
Slurry is fed from above into a horizontal chamber containing a steel screw surrounded by screens. Liquid drains away through a 127mm (5in) outlet while the solids are extruded through an outlet with a weighted restrictor flap.
There are six models, with maximum outputs ranging from 50 to 350cu m/hr, though actual performance depends on the type and consistency of slurry being processed.
The relatively high dry matter material produced by the screw press separator makes it suitable for Bauer’s active composting process, which is designed to render the solids suitable for reuse as livestock bedding.
Solids are fed into a 10m (33ft) long rotating drum. During the 12 hours taken to pass through the drum, the temperature of the material increases to more than 65C, which kills off pathogens and increases dry matter content to 40-42%.
The system will produce up to 25cu m of bedding material a day, suitable for cubicles. That not only saves on the cost of preparing or buying in alternative materials, says Bauer, but also reduces the slurry-spreading burden.
Grassland UK |
---|
If you want to find out more about the latest NVZ regulations and see the latest muckspreaders and slurry application equipment in action (not to mention working demos of mowers, rakes, foragers, balers and wrappers from all the main machinery companies) come to this year’s big grassland and muck event – Grassland UK – next to the Bath and West Showground, Shepton Mallet, Somerset, on 7 May. More details from 01749 822 239 or on the Bath and West Showground website. |
Contacts
- Alvan Blanch 01666 577 333
- Bauer UK (FAN) 01628 788 074
- Linton Solutions (Carier) 028 9262 1317
- NC Engineering 028 3887 1970
- Ocmis Irrigation (Swea) 01460 241 939
- Pollution Control (Groundhog) 01772 620 066