Remoulding adds extra life to tyres
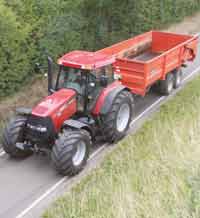
The vast majority of agricultural trailers are fitted with remould truck tyres. The strength of their casing – built originally to withstand the rigours of heavy use on motorways – makes them an excellent choice for trailer manufacturers.
For Alterever, at Brough, East Yorkshire, remoulding truck tyres for the agricultural trailer market is big busines. The company produces more than 350 of the popular 22.5in size every week.
“We take in about 25,000 of them each year, but that is just a small fraction of the total number produced by the truck business,” says company director Alan Malcolmson. “Of these, 30% will be too damaged to remould and about 15% will be used for commercial trucks. The rest go for agriculture and are marketed to trailer manufacturers.”
On arrival at the plant, the used tyres are first tested to make sure the carcass is not damaged; there is little point putting a new tread on a tyre if it is not structurally sound and safe to use. The test calls for a close visual inspection and then a pressure test of up to 70bar.
Having passed the damage test, the tyre is placed on a machine which rotates it while what remains of the old tread is removed. That operation not only takes the tyre down to just a few millimetres from the start of the carcass, but also profiles the outer shape of the tyre.
At this point any small holes or lesions caused by stones are repaired before the tyre is sprayed with a solution to prevent the newly-exposed rubber oxidising.
Right: Old tread is buffed off to a few millimetres of the carcass and a new profile created Below left: Rubber compound is wound on to the face of the tyre to build up a sufficient depth for the new tread to be created. A computer controls the depth and the profile Below right: The tyre is ready to be removed from the mould | |
| |
The tyre is then placed in a frame that rotates it so that a continuous strip of hot rubber compound is wound on to it.
The amount of rubber – and where it is goes – on the face of the tyre is critical if the tyre is to have the correct profile and depth of tread.
A series of presses then mould a new tread into the rubber that has been wound on to the carcass. This calls for the tyre to be placed in a large cast iron oven which is heated by hot steam at a temperature of 160C. The inner part of the tyre is filled with an air bladder to maintain its shape and further inflated to a pressure of 14bar to push the face of the tyre into the mould and create a new tread pattern.
The moulding process can take up to 90 minutes during which time the rubber is also vulcanised, a stabilising process which allows the rubber to always regain its shape after it has been compressed.
Once removed from the press, the tyre remould process is complete and the tyre is ready for another spell of work out on the roads and fields.
“Remoulding is an accepted and responsible way of generating extra life out of a tyre,” says Mr Malcolmson. “The tread represents only 20% of a tyre, so why dispose of a perfectly useable tyre carcass when it can be given a new tread?”