On-farm brake test: Getting trailers ready for harvest
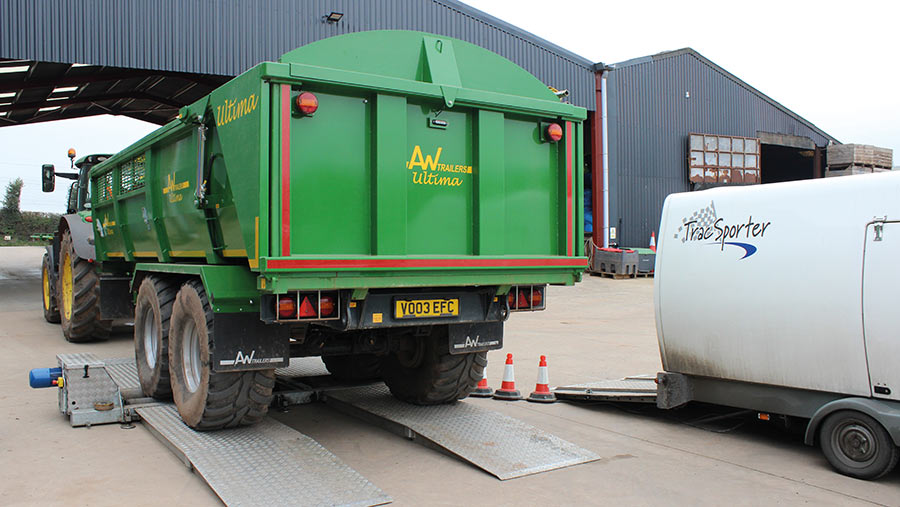
A group of Herefordshire farmers can rest easy in the knowledge that their trailer braking systems are up to scratch ahead of another busy year of field and road haulage.
Three farm businesses near Ross-on-Wye sent a steady stream of bulk and flat-bed trailers to BH Savidge & Son’s Rock Farm at Lea to undergo a static brake performance test.
In total, 24 trailers were submitted to scrutiny and all but a couple passed the service brake efficiency test for road speeds of more than 40kph (25mph).
See also: 14t and 16t silage trailer buyers guide
In five cases, that was after an initial failure led to some hasty but relatively simple adjustments and a re-test; but several fell foul of the parking brake performance requirement.
The initiative followed a successful first testing day for the same businesses last year, organised by Charlie Whitehouse at Bradley Farm, Mitcheldean, an 810ha operation involving 650ha of combinable crops grown alongside suckler cow, sheep and dairy goat enterprises.
“We thought our trailer brakes were all set up properly but last year’s tests showed that wasn’t the case,” he said.
“That was pretty sobering when we consider safety on the road to be fundamental, and I was surprised to learn that new trailers and other trailed equipment can be supplied to customers having never been tested, so we decided to repeat the exercise this year to make sure they’re up to scratch.”
Peace of mind
Mark Savidge, who put a dozen trailers over the professionally operated test equipment from his family’s 1,000ha potato and combinable crops operation, also emphasised safety on the road as an important part of farming responsibly.
“We’re often covering quite long distances with heavy outfits travelling at speed, so dedicating one day in the year to checking the performance of the trailer brakes has got to be worthwhile,” he said.
His son, Ben, highlighted the cost benefit to be had from regular inspection, servicing and testing to ensure that trailers play their full part in slowing a heavy outfit from fast road speeds.
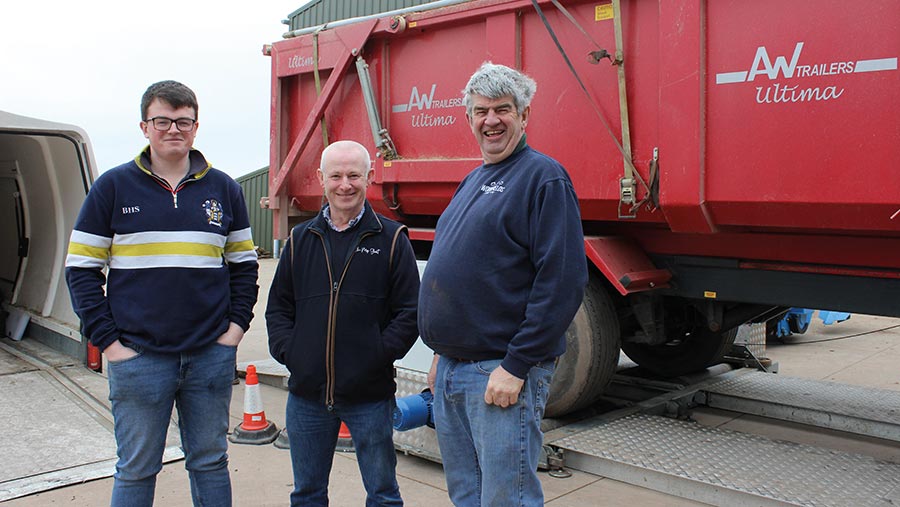
The group testing initiative was organised by Charlie Whitehouse (centre) and hosted by Mark (right) and Ben Savidge © Peter Hill
“We employ a full-time mechanic and now service all the trailer brakes every February, making adjustments and relining or replacing brake shoes as necessary, and booking a test is a good incentive to make sure that’s done,” he said.
“As a result, we now have far fewer tractor brake issues and having the brakes performance-tested gives you the added assurance they are working as they should, while the documentation shows you’ve done what you can to operate safely on the road.”
Cobrey Farms at Coughton also sent trailers for a second session this year, resulting in a selection of makes, models and sizes being put over the roller brake testing equipment.
Time and workload pressures can lead to trailers being overlooked when it comes to routine checks and maintenance, or mistakes being made with adjustments, and all organisations with an interest in this topic emphasise the importance of using qualified technicians to carry out inspections and any remedial work.
Occasionally, trailer manufacturers get it wrong, it seems, when it comes to setting up a load-sensing air-brake system, with instances of new trailers – less than a year or even six months old – failing to meet the braking performance standard, so customers cannot assume new trailers are always perfect.
Testing station
The roller test equipment used for the Herefordshire session stands on six load cells to record the weight of trailers, which need to be loaded to at least 65% of their gross weight to guarantee a good grip between the rollers and tyres for consistent readings.
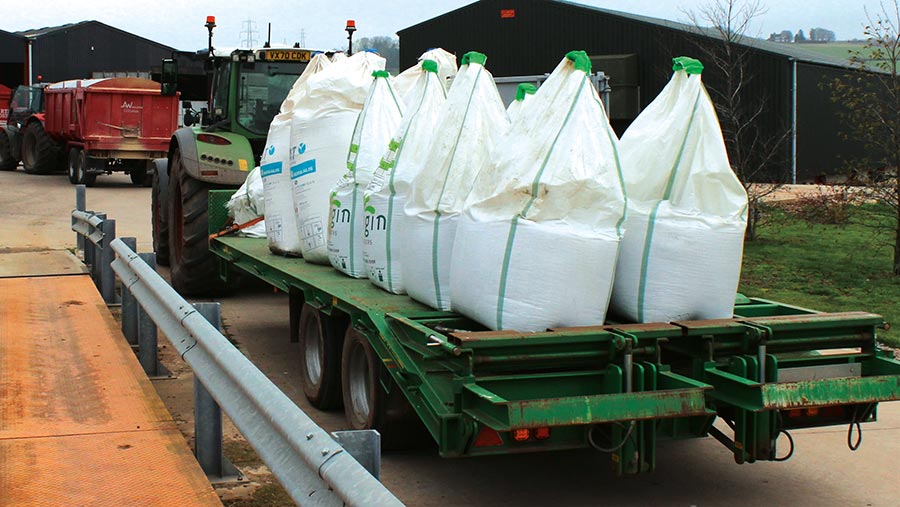
Trailers need to be loaded to at least 65% of their gross weight for reliable results © Peter Hill
There are four sets of electrically driven rollers so the service brake for each wheel on a tandem axle can be tested individually, while a laptop and bespoke software provide an overall braking efficiency percentage.
Trailers with single-line hydraulic brakes must achieve at least 25% braking efficiency, while those with twin-line hydraulic or (more commonly) air braking must achieve 45% efficiency – and both need 16% efficiency from the parking brake – to earn a “pass” certificate sticker.
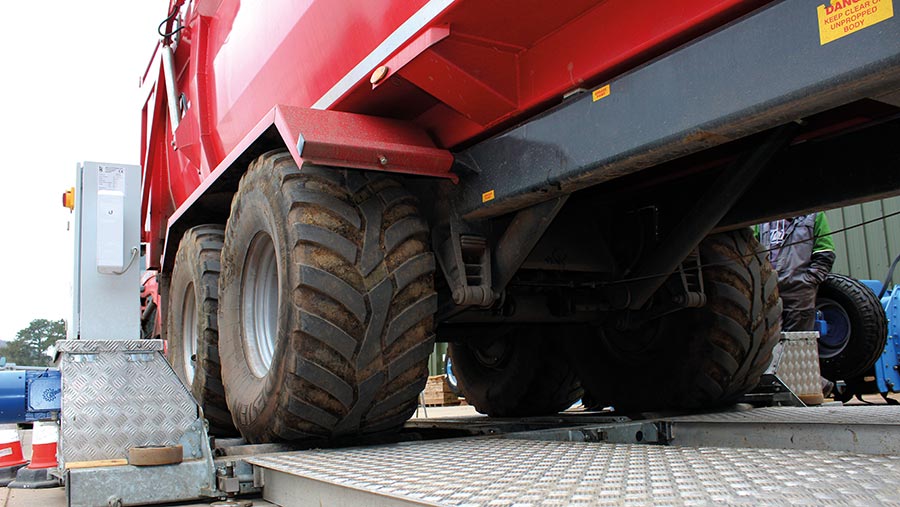
Two sets of rollers enable the brakes on each wheel to be tested individually © Peter Hill
With the ratchet mechanism and cables exposed to mud and dust, and the cables prone to stretching and snapping, the parking brake is often the downfall of trailers that comfortably pass the service brake part of the test.
If the parking brake is not used because the trailer is always dropped off on flat ground then it can deteriorate unnoticed, so parking brake failure means no pass certificate for the trailer, even if the service brakes are up to the standard required.
Trailer brake inspection and testing options
Bagma ATTS
The Bagma Agricultural Tractor Trailer Scheme (ATTS) is a much-enhanced service that now covers a detailed vehicle inspection as well as dynamic testing regime devised by the dealer trade association and partners.
It is offered by a number of machinery dealers throughout the country.
Keith Christian, recently retired Bagma director, said: “Overweight trailers and poor trailer brakes can cause expensive damage to tractor braking systems as well as being dangerous on the road and farm due to lack of braking efficiency.
“And there is no way tractor or trailer brakes can be proven to work efficiently unless a brake performance test is carried out, involving a decelerometer or roller brake tester.”
The ATTS combines brake performance testing with a new 40-point inspection and assessment of trailers or trailed equipment, plus a 58-point inspection of tractors, covering their physical condition and roadworthiness and carried out by trained technicians following procedures specially adapted from heavy goods vehicle MOT testing criteria.
This is followed by the brake performance testing, which uses the purpose-made BrakeSafe recording unit, which is secured in the tractor cab and uses an accelerometer to measure peak and mean deceleration performance.
It also records the test speed, stopping distance and time taken to stop once the brakes are applied, while a transducer or switching unit connection to the tractor’s hydraulic or air braking system records brake pedal force.
Any slope in the test course is compensated in the calculations and the results are instantly available as a printout and can be transferred to a computer.
Brakes on trailers that produce deficient results can be adjusted and tested again, with dealer technicians carrying out the test also able to inspect systems and renew or replace components as necessary.
There is no set charge for the test or any authorised remedial work.
Roller brake testing options
A number of agricultural machinery dealers own or hire-in equipment to provide a brake test service for customers.
In theory, the test equipment can be used for spreaders, tankers and other towed equipment in addition to trailers, as long as they don’t have tyres, or an overall width, too large for the rig.
Irelands Farm Machinery in Lincolnshire, for example, has a roller brake test system installed at its Carrington branch that can also be taken on-farm for testing large fleets or trailers from several customers.
Irelands’ Emily Humphreys says: “We test all our hire trailers and any second-hand trailers going out to assure buyers they’re getting a trailer in top condition, and several customers use the service for their HGV eight-weekly tests.”
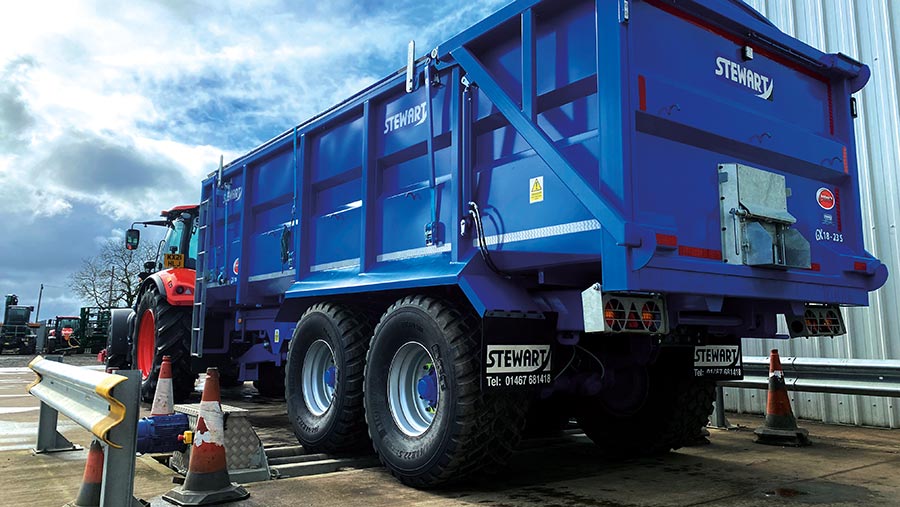
On-site trailer brake testing at Irelands Farm Machinery © Peter Hill
Concrete blocks with fork slots are used for quick and easy ballast.
In Thetford, Norfolk, JM Ayres and Sons hires-in a system for a week each year so that customers can have their trailers checked and tested, while John Day Engineering, near Hungerford, Berkshire, runs its own haulage truck fleet, so it makes sense to have a commercial roller testing system installed that is also used customer farm trailer brake testing.
“Grain trailers are typical because we’re in a mostly arable cropping area, and as they’re standing idle for much of the year, the brakes can deteriorate through condensation and corrosion,” says Robin Day.
“We do a lot of agricultural trailer testing using 3t concrete-filled IBCs for ballast, mostly through May to July ahead of harvest, with some customers bringing three or four trailers at a time, some of them brand new.”
What is braking efficiency?
Independent engineering researcher and consultant Dr Andy Scarlett emphasises the importance of achieving “balanced braking” from a tractor and trailer combination, with both the tractor and the trailer achieving the same braking effort relative to its weight.
“If the trailer doesn’t make its due contribution, the tractor brakes have to work harder to slow the outfit, which results in additional wear, higher service costs and a less stable outfit that could be prone to jack-knifing,” he points out.
By way of an example, a typical 16t tandem axle trailer with suspension, flotation tyres and a roll-over sheet will weigh about 6t unladen, and with a full load on board it shares about 3t of its gross weight with the tractor via the drawbar.
That leaves 19t on the axles, so the trailer brakes need to achieve a braking force 45-50% of that figure – 8,500-9,500 kilogram-force – to deliver braking performance that matches the capability of the tractor.