Driverless tractors: Which manufacturer is leading the race?
Creating an autonomous vehicle for farm fieldwork is a relatively straightforward task from a mechanical engineering perspective.
Choose a powertrain suited to the vehicle’s intended applications, decide between tracks and wheels, and build a chassis to accommodate it all.
No need to worry about creating a fancy cab with neatly laid-out controls, air conditioning, lots of sound-deadening material and great all-round visibility because no-one’s going to be driving it – not from on-board, at least.
See also:Â Video: Retrofit Mojow tractor kit automates arable fieldwork
The real challenge is to incorporate robust sensors and cameras, Lidar, satellite guidance and all the other technologies required in a way that will withstand the rigours of fieldwork while providing a stream of operational data and a safety system that prevents an innocent walker being knocked flat on a footpath.
So the kingpins of any autonomous farm vehicle project are the software writers and electronics engineers who can make it all work efficiently and reliably, with a digital platform for planning the machine’s tasks and enabling 24-hour remote monitoring via a mobile device.
Such machines can then be used to address two big issues in agriculture – an accelerating lack of skilled operators and the need to protect soils by using smaller, lighter machinery that delivers productivity through longer working hours.
Agrointelli Robotti
This Danish manufacturer’s Robotti tool-carrier can operate any number of different implements between its four wheels.
Examples seen in work include a 2.5m Pottinger Vitasem box drill sowing beans, oilseed rape and cereals, a four-row Monosem precision seeder for sugar beet and maize, a four-unit Stanhay vegetable precision drill for vegetable and salad crops, a flexible tine harrow for weeding, and a four-row potato planter.
There are two versions, the Robotti LR being designed for light-duty operations with a modest 750k-rated linkage assembly and powered by a single 72hp Kubota diesel engine with sufficient fuel for up to 60 hours of non-stop operation.
The 150D version, meanwhile, is upgraded for more demanding tasks, with 1,250kg of lift capacity, pto to drive powered implements, and two engines – one for propulsion, one for the pto and hydraulic functions – to deploy a total of 144hp when needed.
Both versions have a short wheelbase measuring just 1.55m and track widths from 1.8m to 3.65m; they run on 320/65 R16 tyres as standard or the narrower 260/70 R16 option.
There is front-end steering for manoeuvres, four-wheel drive for traction, and both will do 10kph when being moved under manual remote control and half that velocity in work to help maintain steering accuracy.
Agrointelli says it has supplied more than 50 examples to farms in numerous countries, including Britain where Warwickshire-based Autonomous Agri Solutions is the sales and service provider.

The Robotti has capabilities to operate varied implements © Robotti
AgXeed AgBot
There are three purpose-built autonomous tractors in the AgBot range, headed by a 156hp twin-track machine and complemented by 75hp four-wheel drive and narrow trike models to cover a wide range of applications.
They all have in common a Deutz diesel-electric power unit (so the engine drives an integrated generator supplying power to electric motors) with the option to add a 55kW (74hp) electrically driven pto at the rear.
This can rotate either clockwise or anti-clockwise, giving the vehicles the ability to work with pto-driven implements in either direction with the implement leading or trailing.
The tracked AgBot 5.115T2 is supplied with 350-litres of fuel capacity and up to four double-acting proportional spool valves, along with an 85-litre/min hydraulic pump that can be upgraded to a load-sensing system.
Implements are carried on the rear by an 8t capacity three-point linkage complemented by a 3t capacity assembly at the front – to carry a hopper for a rear-mounted drill, for example.
Numerous combinations of traction belt widths, from 300mm to 910mm, and adjustable track spacings are available to accommodate different crops and cropping systems.
While the AgBot 2.055W3 “trike” is built for orchard and vineyard applications primarily – it can be configured as little as 1.38m wide – the four-wheel 2.055W4 is a more versatile autonomous solution for farming and commercial horticulture.
Featuring front-end steering, unequal tyre diameters and tyre widths typically from 270mm to 710mm, traction or flotation type, this model’s hydraulics setup is much as for the tracked machine, albeit with up to three spools and lesser implement linkage capacities of 1.5t front and 4t rear.
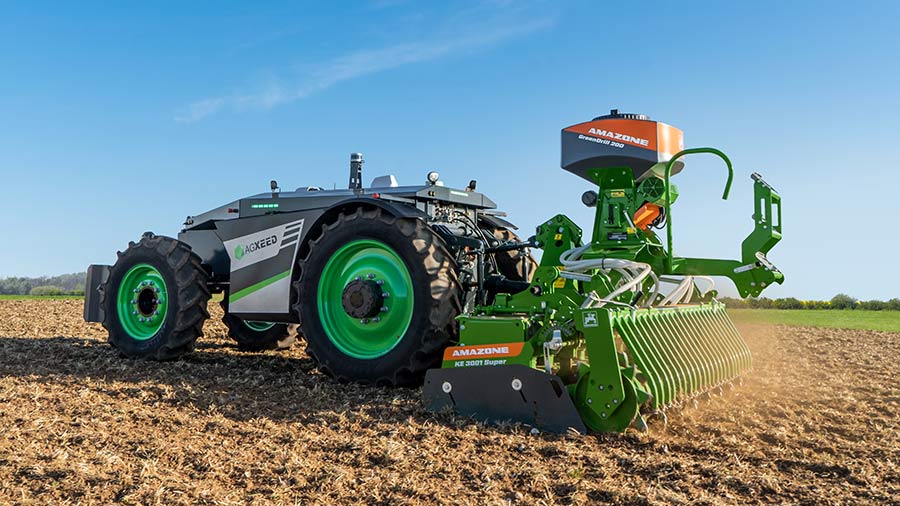
The 75hp, four-wheel drive AgBot 2.055W4 from AgXeed © AgXeed
CNH Industrial
The parent company of Case IH and New Holland is easing into commercial autonomous tech in the wake of exploratory projects such as the Case IH AVC concept – essentially a cabless Magnum – and the driver-optional New Holland NHDrive T8 with autonomous working capability.
Now, the battery electric Case IH Farmall 75C Electric and New Holland T4 Electric Power utility tractors have been unveiled for 2024 sales in the United States with some limited self-driving features.
The Follow Me function, for example, enables an operator to move the tractor – along a feed or fence line, for example, without climbing in and out of the cab simply by walking ahead of it having transmitted the appropriate command from a smartphone app.
And a similar function enables the tractor to pass through a gateway under remote command – so no more hopping on and off to open and close the gate.
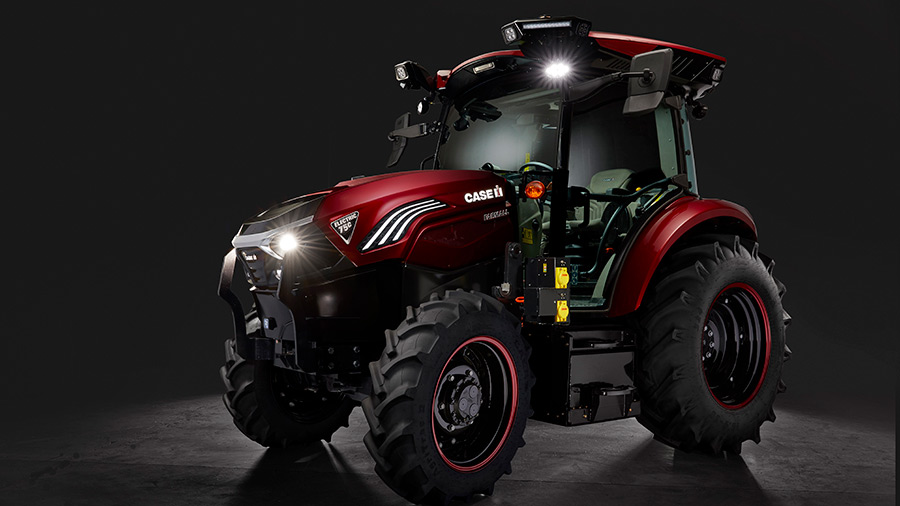
Case IH Farmall 75C Electric introduces some autonomous features © Case IH
Combined Powers
This joint venture project between grassland equipment specialist Krone and tillage machinery firm Lemken has produced a four-wheel-drive tractor dedicated to autonomous operation.
Measuring 2.7m wide and just 2.6m high, and weighing in at 7.5-8t, the vehicle runs on 23in wheel assemblies all round driven by a diesel-electric power unit with a maximum output of 170kW (230hp), so more than enough for ploughing, cultivating and seeding, as well as mowing, tedding and raking.
A key element of the tractor’s control system is that it is geared for isobus Tractor Implement Management (Tim) enabling sensors and a job computer on the implement to send control instructions to the tractor – for speed changes, hydraulic adjustments and to stop and start, for example.
Having demonstrated its field capabilities publicly in 2022, the project involves further testing in typical and extreme working conditions while collecting more feedback from farmers and contractors about the concept.
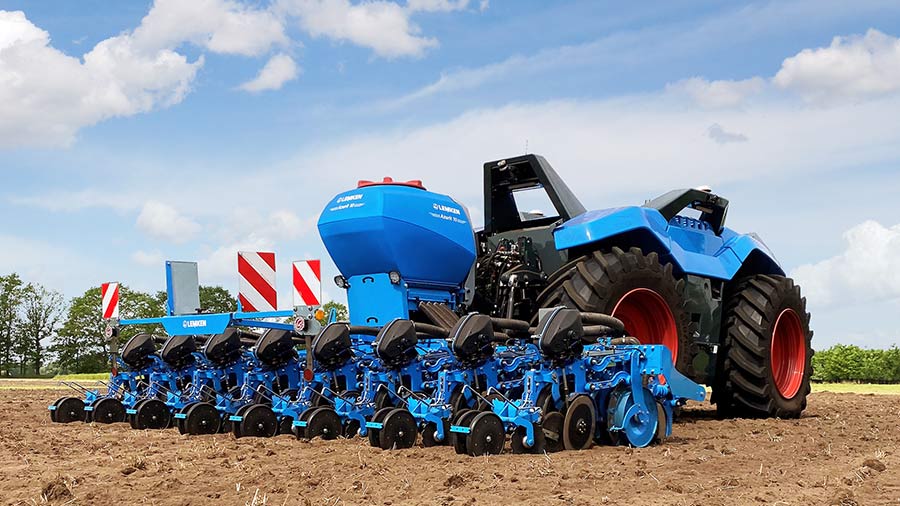
Four-wheel drive Combined Powers fully autonomous tractor © Lemken/Krone
FarmDroid
The FarmDroid FD20 is a specialist tool carrier for precision sowing and weeding, with units now operating in Britain mainly for organic sugar beet, fodder beet and vegetable production.
Usually configured with a trike undercarriage, but also available in a four-wheel format, the FD20 has battery-electric power topped up by a large solar panel canopy.
The key to its operation is task creation software that calculates the in-row spacing required to achieve a given plant population and plots where each seed will be placed, regulating the electrically driven seeding units accordingly.
And because individual seed placement has been plotted it is possible for the integral active weeding units to disturb soil within as well as between the rows for pre-emergence weed control that eliminates the need for herbicides until later in the growth stage of the crop.
The FD20 is available in four-, six- and eight-row versions with a sedate working speed of 450-950m per hour.
But it is capable of running 24-hours continuously, with its manufacturer recommending one machine for up to 20ha for seeding and a weekly weeding pass until the crop foliage meets in the row.
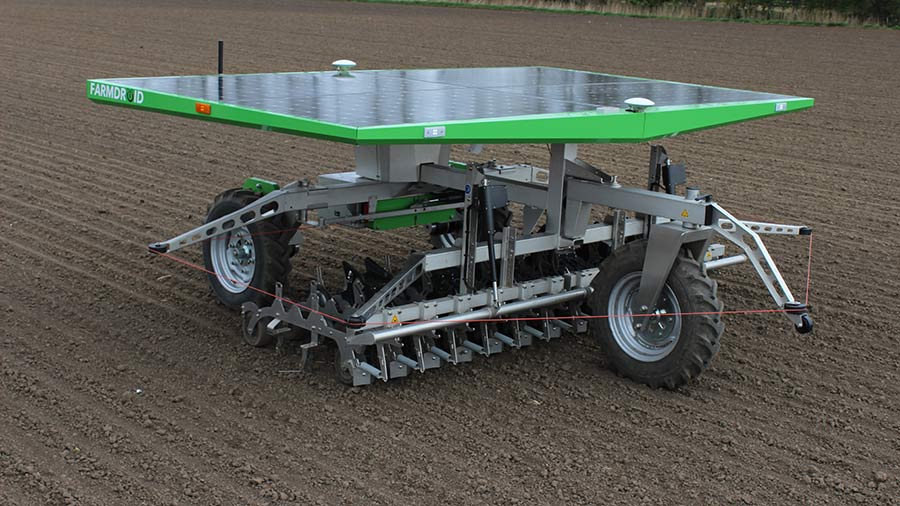
FarmDroid FD20 can start weed hoeing before the crop emerges © Peter Hill
Horsch
Two different concepts for autonomous power units are being explored by Horsch – a driverless tracked unit that operates much like a traditional field tractor, and a large tool carrier-type machine.
Official details are scarce, but the Robo independent power unit, despite being relatively compact, is understood to have a 450hp diesel engine and either hydrostatic drive or a hydro-mechanical “vario” transmission.
It certainly has remote manual control for setting up and a pull-out drawbar at the front so it can be towed to and from the field.
Running on Claas Axion Terra Trac assemblies, the Robo has been used in field trials operating a trailed Maestro precision planter in a close-coupled configuration that effectively creates a self-propelled outfit with the tracked unit sharing as much as possible of the weight of the seed cart.
Horsch Brazil’s gantry-like machine is configured as a 24m Maestro precision planter for maize, sitting on four large-diameter swivel-steer drive wheels with hydrostatic propulsion motors.
The wide frame – which travels lengthways from yard to field – carries a central power unit with a hopper either side, and with the planter units slung beneath.
Potentially closer to commercial realisation is an autonomy package for self-propelled sprayers resulting from a collaboration between Horsch and Trimble.
The partnership extends beyond autonomous control to include full workflow automation from the office to the field.
Trimble says the first phase will bring automation to the planning, machine control and logistical challenges faced by sprayer operators to improve machine performance and reduce the operator’s workload and potential errors.
In the longer term, the technology will establish a basis for operating fully autonomous machines.
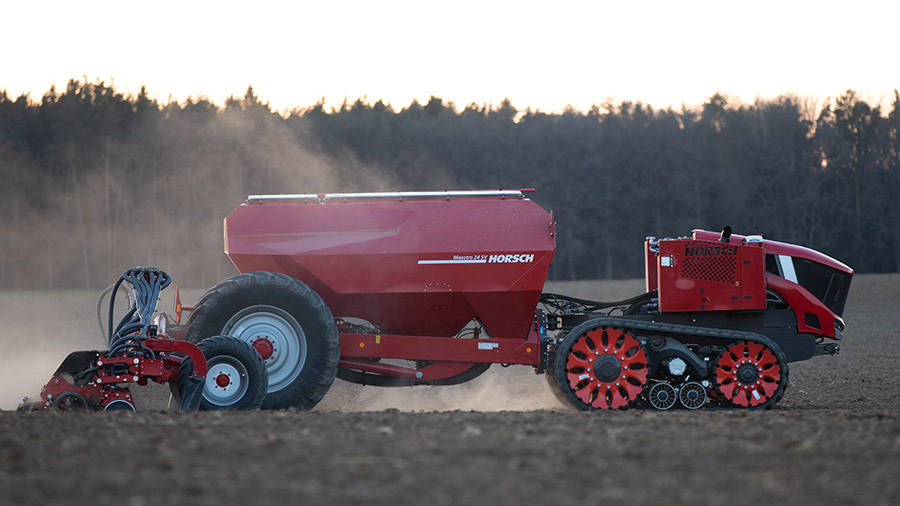
Horsch’s prototype Robo tractor with a Maestro precision planter © Horsch
John Deere
Numerous autonomy technologies and vehicle types are been explored by John Deere, including a guided tractor and sprayer with automatic re-filling for use in orchards and the like, and a purpose-built driverless sprayer configured for high-clearance maize spraying running on four track units.
There is also a 500kW (670hp) electric-drive single-axle autonomous tractor that could run on wheels or tracks when attached to cultivators, drills and similar implements.
But causing the greatest stir was Deere’s announcement in January 2022 that an autonomous version of its regular 8R series tractor would soon go on sale in the USA (although the order book is yet to open), with initial focus on chisel cultivations work using the most powerful model in this line-up.
The 8R 410 with 443hp for draft work, 458hp for pto, transport and applications with intense hydraulic demand, is configured like a conventional version, but with six pairs of stereo cameras enabling 360deg obstacle detection and distance calculation.
Images are analysed by a deep neural network that classifies each pixel in approximately 100 milliseconds and determines if the machine can continue to move or should be brought to a stop.
John Deere says building a library of both critical and benign image subjects – such as a person versus a tree branch lying on the ground – was one of the more challenging elements of the project.
Apart from the safety requirement, an ‘intelligent’ system is essential to minimise false alarms necessitating operator intervention to get the tractor going again.
As with other autonomous machines, when interventions are needed, operators can do so remotely by consulting live video and images, data and metrics using a mobile device app, which also enables remote adjustment of cultivation depth, working speed and the like.
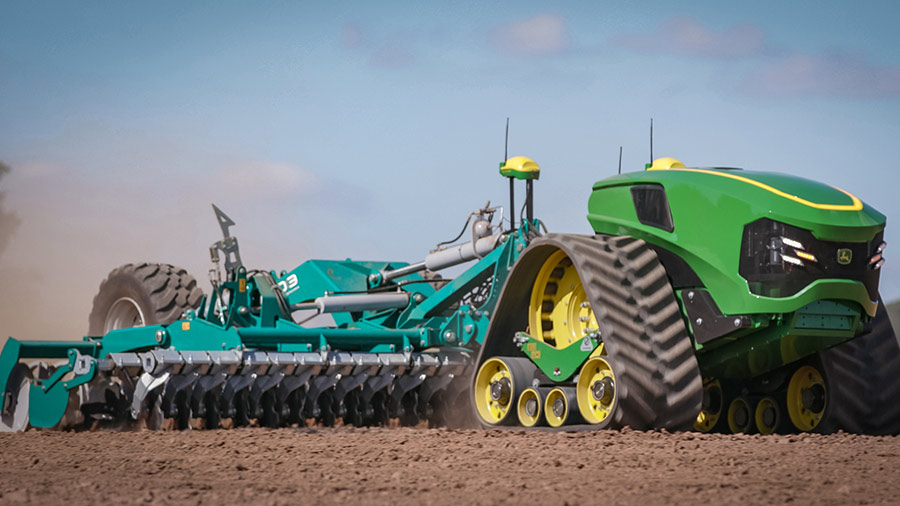
One of several John Deere concepts – a single-axle electric tractor © John Deere
Kubota
Having revealed the futuristic Kubota X four-track electric tractor concept in 2020, Kubota has since been testing a number of autonomy-capable AgriRobo wheeled tractors.
Japan has something of an approaching crisis with an ageing population of farmers and an unwillingness among younger generations to take over.
In addition to a rice transplanter and a rice combine, Kubota has introduced the 100hp MR1000A with an array of self-driving guidance and sensor technologies to help ease the farm labour situation.
Independently, US-based Sabanto has extensively trialled and refined its retrofit autonomy package through a ‘farming as a service’ contracting operation, which has attracted investment from Trimble’s venture capital arm.
The service uses 60hp and 90hp Kubota tractors equipped with the autonomous package to undertake commercial contracts with growers for cultivations, maize planting, hoeing and spreading across a number of Midwest states to demonstrate and prove the concept while earning revenue.
The Steward retrofit package to convert existing tractors to autonomous operation is now available through a number of dealers in the USA and Canada.
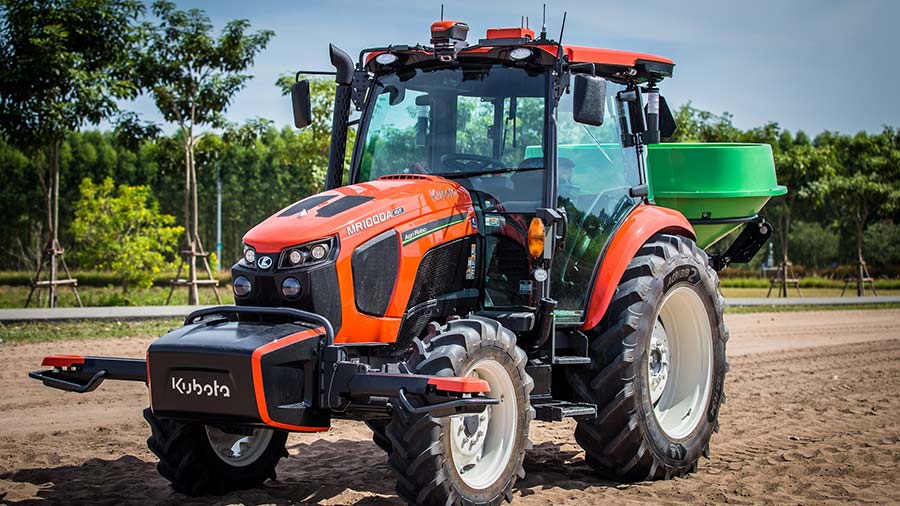
Kubota’s 100hp MR1000A AgriRobo tractor © Kubota
Raven Industries
As an electronics and software specialist rather than a vehicle manufacturer, Raven’s Autonomy division has been busy creating solutions for its parent company’s Case IH and New Holland operations, as well as all-brand retrofit solutions.
This activity has resulted in two systems for US growers – OmniDrive, which enables a combine driver to call in and synchronise an automated grain tractor and trailer, and Cart Automation, which has just the speed/heading synchroniser but can be retrofitted to any make and used for any harvesting operation, including sugar beet, for example.
There is also a newly released full autonomy solution for the Case IH Trident 5550 self-propelled fertiliser spreader.
Raven Autonomy does have one vehicle in its portfolio – the OmniPower 3200 tool carrier originally developed by Dot Technology and Seedmaster in Canada – with hydrostatic drive, four-wheel steer and interchangeable sowing, spreading and spraying modules.
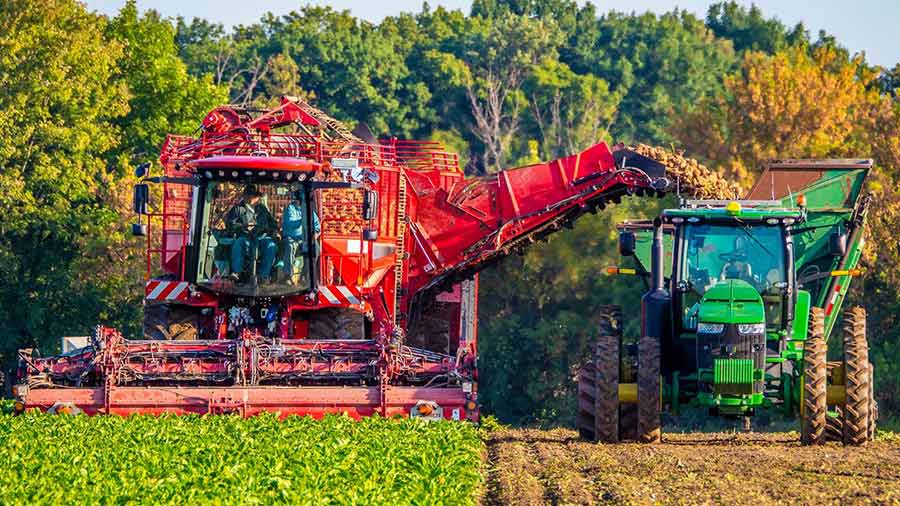
Raven AutoCart synchronises harvesters and trailers © Raven