Three row potato harvesting surges ahead
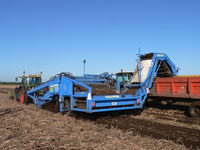
The first harvester designed for lifting three rows arrived five years ago when Standen Engineering announced its Standen-Pearson T3 trailed machine.
The idea came about during talks with a customer in Essex, says Standen’s Alex Mathias. Like many growers with a two-row machine, he wanted more output and that was when three-row harvesting was first suggested.
The aim was to offer growers with a two-row harvester an opportunity to boost their output while avoiding the cost, weight and width penalties of switching to four-row self-propelled lifting or the extra tractor and driver needed for a second two-row trailed harvester.
In theory, a three-row trailed harvester like the T3 should deliver 50% more output than a two-row machine. But David Wilson, Standen’s sales director, says the actual gain is often closer to 60%. This is because as well as the extra row and the time saved by fewer headland turns, the T3 also has an extra-large separation capacity that allows a faster forward speed.
Achieving high outputs from the T3 demands plenty of tractor power. Minimum recommended tractor size is 180hp, but Mr Wilson thinks 200-220hp is ideal. The T3 is designed mainly for growers with at least 120ha (300 acres) of potatoes, and on that acreage 200hp tractors are no longer unusual, he points out.
One of the concerns with the first T3s was the fact that as three-row planters were not available, they would mainly be lifting crops planted with two or four-row planters, causing problems if the row alignment was not accurate.
In fact, this hasn’t happened because experienced tractor drivers have been able to achieve sufficiently accurate bout matching. Also, more tractors are now equipped with GPS guidance.
The company has also introduced a three-row planter, but in spite of this about half of Standen’s T3 customers still use two- or four-row planters, the company says.
As well as pioneering the idea of three-row harvesting, Standen now offers three-row destoning equipment and has worked with Dutch company Baselier to develop a three-row topper. It is also the only company to offer growers a three-row harvester choice since the 2009 launch of the new self-propelled three-row machine from the Ploeger range, for which Standen is the UK distributor.
The Ploeger AR-3W harvester is powered by a 300hp engine and has a 1.5t holding tank for extra flexibility in the field. It even features a cab that moves backwards or forwards and swivels to allow the operator to choose the best driving position. A three-row Ploeger was sold to a UK grower before it had been officially announced last year.
The on-farm price for a new T3 harvester is about ÂŁ150,000, compared to ÂŁ110,000 for the new Standen-Pearson T2 two-row trailed harvester with a comparable specification level. A typical two-row self-propelled harvester costs about ÂŁ260,000 on the same basis.
T3 sales are increasing steadily, amounting this year to about 20% of Standen’s total UK potato harvester sales. As three-row harvesting is a UK development there was no existing export potential for the T3, but David Wilson says this may change. Some growers in Australia and on the continent are showing interest in the idea of switching to three-row systems.
“When other manufacturers introduced three-row machines to compete with the T3 we thought it was bad news, but we have started taking a much more positive view of the competition,” said David Wilson. “More companies in the market will help to establish the three-row concept in the UK and it will also help to encourage growers in other countries to consider the idea. Three-row harvesters are not going to dominate the market overnight, but they will be a growth market for many years to come.”
Grimme
Grimme also provides a range of matched three-row equipment. The list includes the GL 33T three-row planter although Grimme says that with GPS guidance four-row planting can work well with three-row lifting.
The Grimme GT 300 harvester is a trailed three-row machine featuring MultiSep separation and equipped with an unloading elevator with 1.2m wide pockets.
Ralph Powell of Grimme says one of the GT 300 harvesters has already been sold to a UK grower and he expects further sales for next year as more growers switch to three-row lifting.
“I think we will see a lot of growers switching to three-row harvesting in this country. It’s a very logical development, because bigger-acreage growers are looking for more output and changing from a two-row harvester to three rows will give about 50% more capacity,” says Mr Powell.
“Although the UK is the leading market for three-row harvesters, there is also increasing interest on the continent, particularly in Holland and Denmark where farmers are interested in the extra output and in having fewer wheelings.”
Dewulf
Alan Nicholson at Niagri, the UK distributor for DeWulf range of harvesters, is more cautious about the future. DeWulf, the newest three-row harvester company, recently announced a Kwatro self-propelled harvester that comes in both three and four-row versions.
It has a 450hp Scania engine which powers hydraulic pumps driving the harvesting mechanisms and a hydrostatic transmission. It is mounted on rubber tracks at the rear and a single wheel at the front and has a 10t bunker. Kwatro harvesters will be available in the UK next year but Mr Nicholson thinks the four-row version will attract most customers.
“The three-row harvester market will continue to expand, but I think it will be a slow process,” he says. “The main problem is price. Changing to a three-row system is expensive because you need to change the destoner and the planter as well as the harvester. I am also not convinced that you would actually get the full 50% increase in output. I think the four-row Kwatro will be the popular version.”
Switching from two rows to three
With more acres to lift, the benefits of switching from two-row to three-row lifting were obvious, according to Pete Barney, a manager for Lincolnshire Field Products.
“I would say it was a no-brainer. Harvesting three rows is about 50% faster than two rows and we need the extra output,” he explained. “We previously used three two-row harvesters, including one self-propelled, but with a bigger acreage we have been changing the two-row machines for three Standen three-row harvesters. This year our potato crop has increased to 1400 acres and we replaced the last of our two-row machines.”
|
---|
Lincolnshire Field Products, at Wykeham, Spalding, farms about 6000ha (15,000 acres) including owned, rented and contract-farmed land. Potatoes are grown for the pre-pack trade and the aim is to start lifting during the second week in August and complete the harvest by the end of October.
One of the problems the farm faces during harvest is the time spent on the road as its crop is grown on land up to 20 miles from Wykeham. This year its timetable was also delayed thanks to a late start to harvesting caused by slow crop growth early in the season. Also, the wet conditions have forced changes to the lifting programme on the mainly silt soils.
“We will probably not be finishing on time this year in spite of having the three-row harvesters, but we would be in a real muddle if we were still relying on the two-row harvesters,” he said. “Output from a T3 is anywhere between five and 10 acres per day, but in good conditions we have lifted 50 acres with the three machines.
“Apart from the extra output we are also very pleased with the performance generally. Blockages are rare, the driver has a good view of the sieving areas and there is very little damage – which is obviously important. We put a 205hp Fendt tractor on each harvester, which seems about the right amount of power and we also like the Vario transmission.”
The whole of the company’s potato crop is planted with a four-row machine, but with GPS guidance this has not caused problems with three-row harvesting, says Mr Barney. Examine the rows carefully and some variations are visible, he says, but they do not affect the harvester.