What’s in Your Shed? visits a progressive Hampshire arable farm
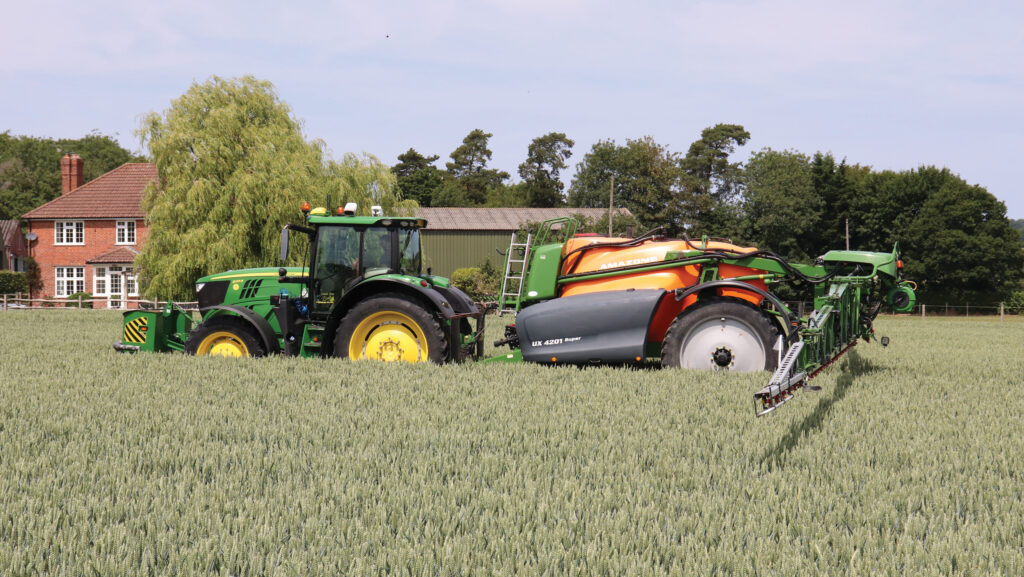
Buy quality kit and make it last. That’s the machinery policy at 1,250ha Neatham Manor Farm, near Alton, Hampshire.
Farm manager Matthew Ashton talks through the Neatham fleet.
See also: On test: Fendt’s four-cylinder, 224hp 620 – small engine, big power
Farm facts
Neatham, Neatham Manor Farm, Neatham, Hampshire
- Farm size: 1,250ha (owned)
- Cropping: Winter wheat, winter barley, spring barley, winter oilseed rape, spring oats and spring beans
- Staff: Matt Ashton, plus full-time operators Will Norgate and Sam Norman. One casual for harvest.
How did you get started?
I grew up on my family’s 80ha tenanted dairy farm near Taunton, but quickly learned that livestock wasn’t my bag.
So, after A-levels and a brief spell as a skiing instructor in Canada, I ended up back in Somerset, but working for a contractor rather than milking cows at home.
I stayed with the same contractor for eight years, operating everything from foragers to drills and balers, gradually progressing to running the firm’s 2,000ha straw contract during the harvest period.
From there, I had 18 months as an assistant farm manager on a 2,000ha estate in Berkshire, before arriving here at Neatham in 2013.
The Neatham manager moved on to a larger estate in Oxfordshire a couple of years later, at which time I was promoted to his role.
Since then, life certainly hasn’t been dull.
Along with tackling the challenges faced by all UK farmers – Brexit, the loss of Basic Payment Scheme, the introduction of the Sustainable Farming Incentive (SFI), escalating costs and a huge variation in returns – Neatham itself has undergone a period of massive change.
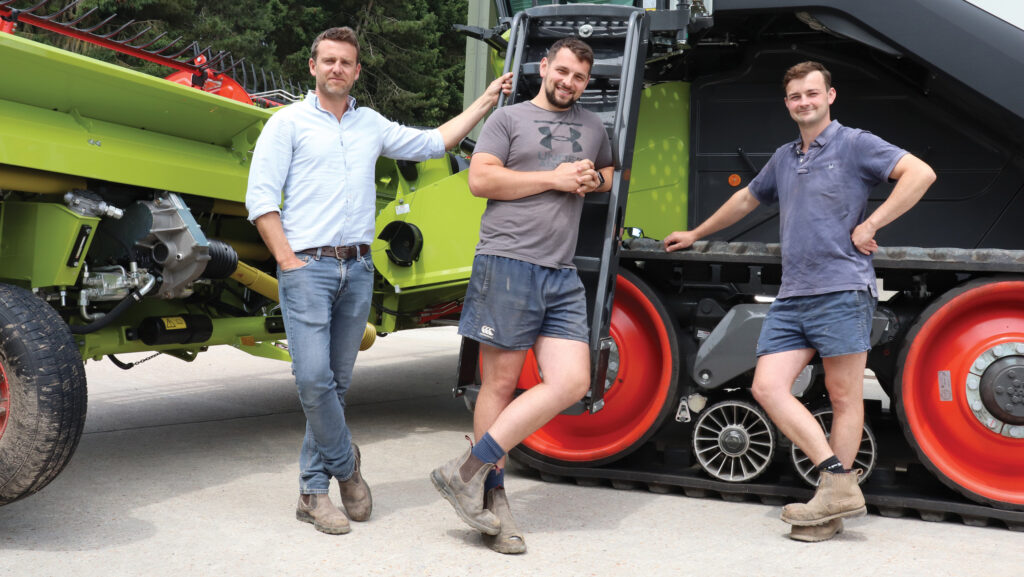
Manager Matt Ashton and full-time operators Will Norgate and Sam Norman © Andrew Faulkner
Ten years ago, the farm was about 600ha and farmed relatively conventionally, establishing crops using deep, non-inversion tillage.
Whereas today, following a change in ownership in 2019, the business has doubled in size to 1,250ha, put up a new 6,000t grain store and is still looking to grow.
The focus is now on the use of direct drilling, cover crops and SFI to maximise efficiency while still farming sustainably. And our current machinery fleet reflects that shift in direction.
How brand loyal are you?
Not really. It just so happens that we operate largely Claas, John Deere, Fendt and Amazone equipment. But that’s because we reckon it’s the most suited to the job rather than preferring a particular colour.
For example, I’m a big fan of Claas Lexion combines. I like their combination of drum, concave and rotors, believing that a mix of two threshing systems must be better than one.
On tractors, again we go for what suits the role in question and represents, in our view, the best value.
For general 200hp models, we struggle to justify the premium of a Fendt over a Deere whereas, at 300hp+ Fendt becomes more competitive on price and beats the Deere 8R on versatility.
So, that’s where we’ve ended up… with a mixed tractor fleet of Deere and Fendt. If price wasn’t a consideration, we’d probably run all Fendts.
Favourite dealer?
We’ve no complaints with any of our dealers, although the stand-outs are Crawfords’ Luke Morley and Farol’s Martin Bailiss.
They’re the keenest to get the deal and will often think outside the box to come up with a more attractive package.
On the support side, all dealers seem to have a high-ish turnover of technicians. Not that we’ve got any complaints, as all the dealer service guys here have been good.
Favourite piece of kit?
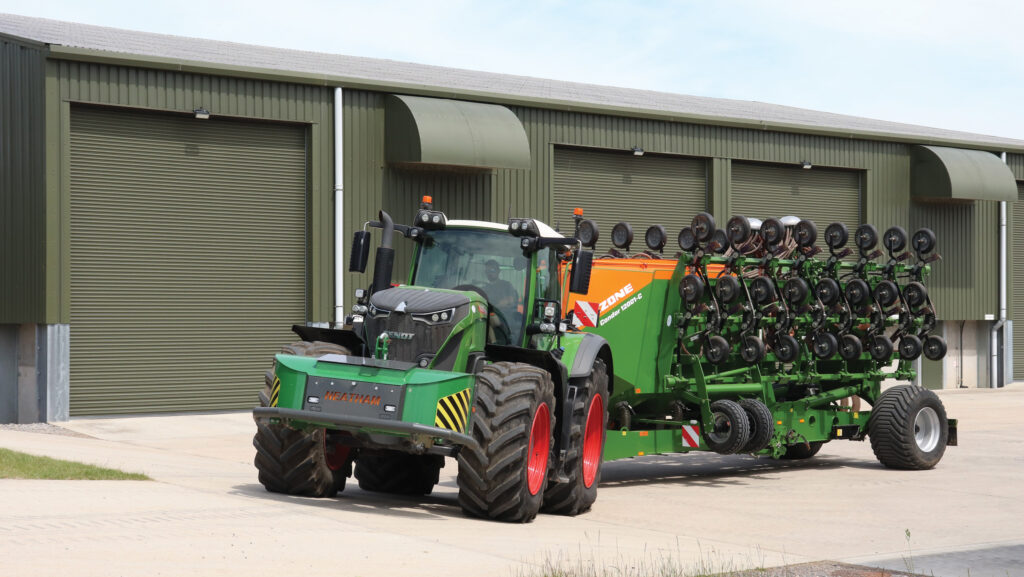
Drilling rig is a 330hp Fendt 933 and 12m Amazone Condor 12001- C © Andrew Faulkner
It’s a toss-up between the Fendt 933 and the 12m Amazone Condor drill.
For us, the Fendt is unbeatable in the 300hp bracket for its power, manoeuvrability and technology, and is so comfortable to drive.
But the main attraction is its versatility – it does all the drilling yet also doesn’t look daft on a fertiliser spreader or when pulling one of the 16t Bailey grain trailers.
With just three tractors on more than 1,000ha, they all have to be capable of doing a broad range of tasks.
As for the 12m Condor direct drill, we love its simplicity, and it rarely blocks, or gets stuck, regardless of the conditions. In combination with the 933 and its central tyre inflation system, the outfit is well matched.
And your least favourite?
That’ll be the older John Deere 6215R, which was simply supplied on the wrong tyres when we bought it new in 2019.
This was largely my fault, as I’d asked the dealer to match the spec with our outgoing Fendt 724 Vario – 65 profile tyres on 42in rims.
So, that’s what we got. What I wasn’t told is that the vast majority of 6Rs are sold with 85 profile tyres on 38in rims.
The result is that the older 6215R neither looks right nor rides right, and nobody likes driving it. We’ll probably look to part-ex it next year when it’ll be up to around 6,500 hours.
Latest purchase?
Most recent purchase is an Amazone ZA-TS 4200 fertiliser spreader, which arrived earlier this year.
Holding 4,200kg and spreading to 36m, it’s pretty much identical to the previous six-year-old ZA-TS, other than its price and having a more accurate weighing system.
In 2019 we paid £17,750, whereas the new one was £24,000.
Oldest machine still at work?
A 1974 Ford 4000 spends most of its time attached to a 2.5m Kuhn topper and is used by the keeper for estate work in the woods.
Though currently awaiting workshop attention, it generally plods on problem-free.
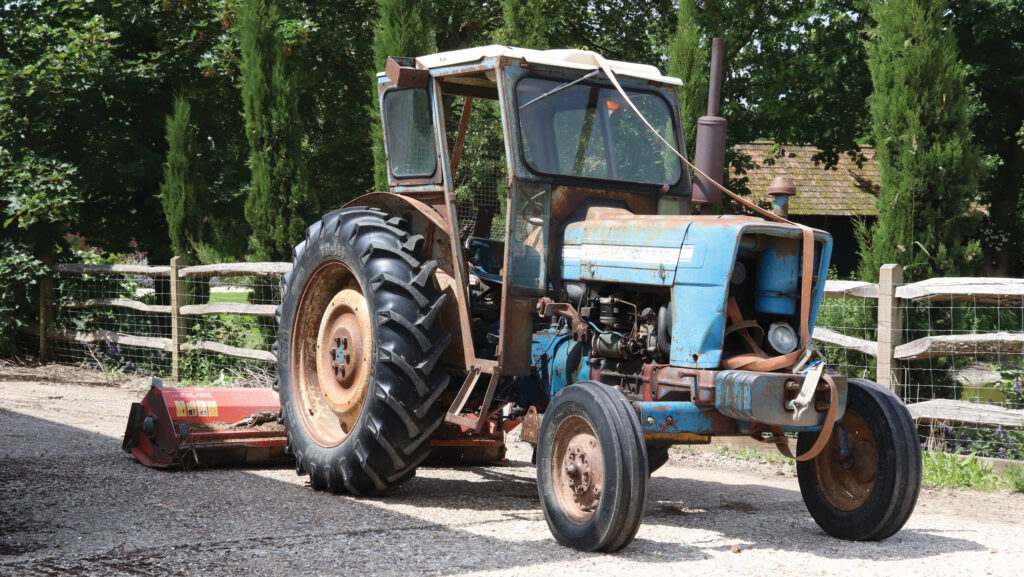
Ford 4000 © Andrew Faulkner
How long do you keep your machines?
There is no set policy, with each machine reviewed separately according to its changing workload, reliability and what deals are on offer at the time.
In recent years, the dramatic increase in farm size has been the main driver.
The previous combine, a Lexion 750 with a 9.3m header, is a good example. We’d had it for seven seasons and would have happily kept it for another two, but the extra acreage meant it was struggling.
Now with the Lexion 7700 and its 10.8m Convio Flex header, we feel like we’re back on top of the job.
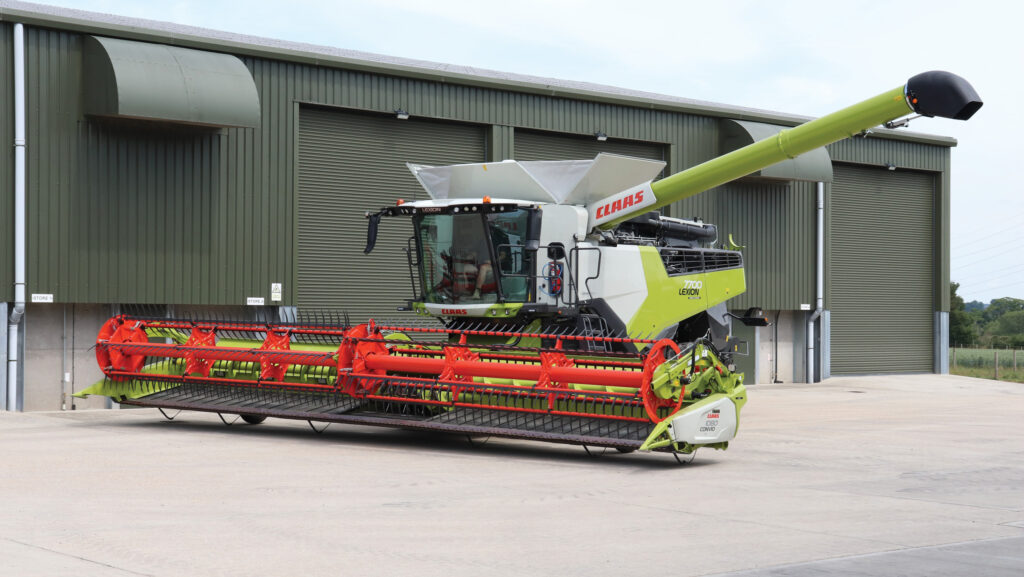
Claas Lexion 7700 with a 10.8m Convio Flex header replaced a Lexion 750 © Andrew Faulkner
Similarly with the previous Fendt 930, the change was made because of a shift in requirements.
We’d have stuck with the seven-year-old 930 for another couple of years, but Crawfords came up with an attractive deal for the Gen 7 933, complete with Variogrip tyre inflation and a bigger hydraulic pump, which made it a better match for the Condor drill.
As for the telehandlers, the plan is to hold on to them for longer.
The 20-plate Kramer KT407 was bought as an ex-demo unit and will probably do at least another five years, whereas the 13-year-old Manitou MLT 840-137 will be with us for even longer.
Costing £48,000 back in 2023, the MLT came here with 2,000 hours on the clock and spends a chunk of its time firing off clays on the farm’s simulated game days.
Running the second handler is a bit of a luxury, but one we’re reluctant to give up, as both machines are often in action at the same time, especially in the spring and early summer – hosting clay traps, handling solid fertiliser or out-loading grain.
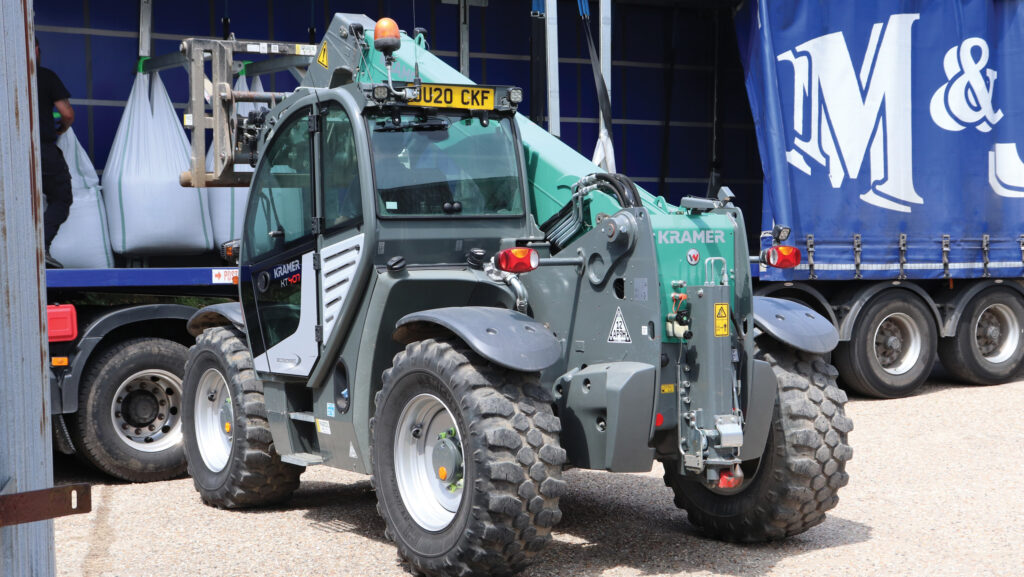
Kramer telehandler © Andrew Faulkner
Next on your wish list?
We’ll probably change the older 6215R and seven-year-old Amazone trailed sprayer next year, moving from 30m to 36m tramlines, again to cope with the increased area.
On the tractors, we’ll shift the existing, newer 20-plate 6215R off the sprayer and on to other duties, and then update the sprayer tractor.
Most embarrassing mistake?
Nothing too dramatic here, fortunately. We’ve done the classic of reversing the combine out of the shed with the steps still unfolded. That was a £2,000 bill.
And, much to the amusement of the rest of the team, I also managed to reverse my Discovery into a skip, despite having 360deg cameras.
Most expensive repair bill?
No single item sticks out, but we were hit with some hefty bills on the previous Amazone spreader – a couple of TS motors at £1,000 each and two job computers at £3,000 apiece.
Then we also had to replace a level sensor and shut-off motor, all on a spreader that was only with us for six seasons. To be fair, though, Amazone did help out on the cost.
I’m convinced we got one of those Friday afternoon machines. If not, I’m going to look pretty daft, as we’ve just bought another one.
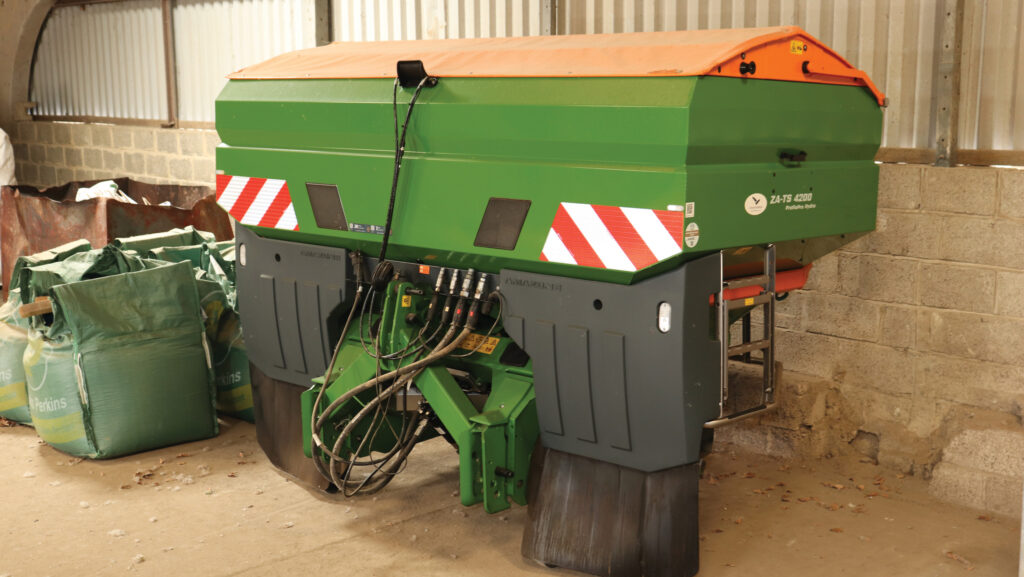
Amazone spreader © Andrew Faulkner
Most expensive spare part?
It’s those Amazone job computers at £3,000 a pop.
Best invention?
The platform for the two remotely controlled clay pigeon traps stands out.
The Manitou lifts the platform to its full height of around 8m, and then extending a couple of rams on the platform takes it up another 3m.
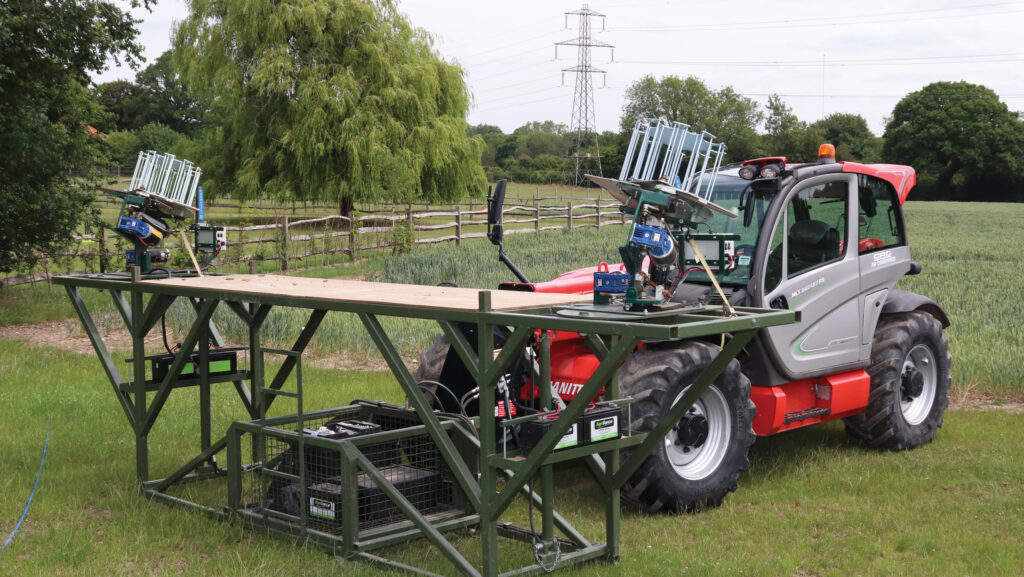
This farmbuilt, hydraulically raised platform can hoist a pair of clay traps to 11m © Andrew Faulkner
It probably cost about £1,000 to build the platform, but it’s now fundamental to the operation of our simulated game days. Basically, the higher the trap, the flatter the trajectory of the clays… and the farther they fly.
What couldn’t you live without in the workshop?
Will is big into his Milwaukee gear, and he’d least like to be without his impact gun.
Another favourite is the wheel changer for multiple tractor and sprayer wheel swaps through the season, and it’s also handy for the annual trailer fleet service, which we do ourselves.
We’re recent converts to the Merit Ag Check system for recording daily vehicle checks and even use it for monitoring fuel consumption.
Every maintenance-requiring item on the farm has its own QR code, and that includes the roller doors.
Favourite and least favourite jobs?
Drilling tops the list if it’s going well.
Compared to when we were charging across min-tilled fields at 16kph with a 6m Amazone Cayena or Vaderstad Rapid burning fuel at 55 litres/hour, the Fendt and Condor trundle along at 8kph on not much more than tickover at 30 litres/hour.
And we’re planting a comfortable 70ha/day rather than struggling to hit 50-60ha. Along with RTK guidance, it’s now a relaxed job.
Least favourites are hedgecutting and, unsurprisingly, cleaning out the grain stores.
What’s your everyday transport?
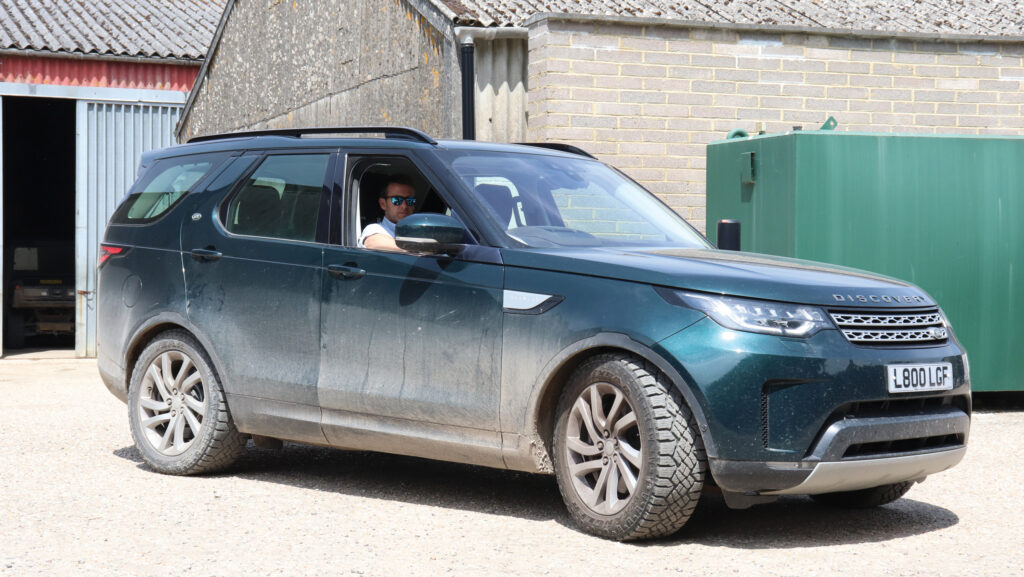
© Andrew Faulkner
A 2019-plate Land Rover Discovery with 36,000 miles on the clock, bought used at 8,000 miles. It’s a good car, comfortable and tows well, but has been far from fault-free, with a leaky windscreen and failing rear window motors.
Worst of all was a dodgy earth that took the dealer six months to sort. The vehicle would shut down – not great at a road junction – and there’d be no electrics.
So, as well as no engine, you couldn’t unlock the rear doors, the boot or even the glove box.
To get at the battery, you had to clamber over the rear seats, and then, if lucky, a fiddle with the earth strap would bring the vehicle back to life. Not ideal.
Best tractor you’ve had?
The current two-year-old Fendt 933 for the reasons mentioned earlier, although, to be fair, it hasn’t been problem-free. The turbo and injectors were done at 800 hours, all under warranty. With this in mind, we’ve recently extended the warranty for a further five years.
The previous 930 also suffered with engine issues and had to have new pistons and liners at 3,000 hours. We were looking at a bill of about £15,000, but again Fendt stood by it.
And the worst?
A few years back we hired a Claas Axion 950 for 12 months. It was big and cumbersome, and it’s CVT transmission wasn’t as smooth as the Vario.
There were no real problems with the tractor, but we were glad to see it go.
Biggest machinery bargain?
In 2020 we did a multi-machine deal with Farol for a Bomford hedgecutter, two Bailey grain trailers and a Bailey low loader. This made their individual prices extremely competitive.
Best and worst pieces of technology?
We love the RTK for its accuracy, repeatability and the fact that the signal never drops out.
And we’ve also recently invested in a £24,000 Yara N-Sensor setup, netted down to £14,000 through an FETF grant, because we were fed up with the inaccuracy of satellite imagery.
We’ve reduced nitrogen inputs by about 30% over the past five years, and the N-Sensor was the obvious next step.
There’s no worst piece of technology, although we struggled with a demo inter-row hoe earlier this year. It was laden with tech, including side shift and multiple cameras, but we couldn’t achieve the desired result.
The soil was either too dry and hard for the hoe to have an effect, or in the wet the hoe’s action simply encouraged another weed chit. We won’t be buying one.
Kit list

Due for change – the six-year-old, 5,600- hour JD 6125R © Andrew Faulkner
- Tractors: Fendt 933, John Deere 6215R x2, Ford 4000
- Combines: Claas Lexion 7700 with 10.8m Convio Flex header
- Handlers: Kramer KT407 and Manitou MLT 840-137
- Sprayer: 4,200-litre/30m Amazone UX4200 trailed
- Spreader: Amazone ZA-TS 4200
- Drill: 12m Amazone Condor 12001-C
- Cultivation kit: 4m Kockerling Vario (legs) with APV seeder unit, 6m Kockerling Rebell (discs), Lemken eight-furrow semi-mounted reversible plough, Cousins seven-leg V-Form subsoiler (low disturbance conversion), 12m Dalbo Powerroll 1230 rollers
- Other kit: 16t Bailey TB16 grain trailers x3, 14t Marshall grain trailers x2, Bomford Hawk Evo 6.5 hedgecutter, 6m Gyrax batwing mower, 3m Teagle flail topper