Windrowing can double output for some potato varieties
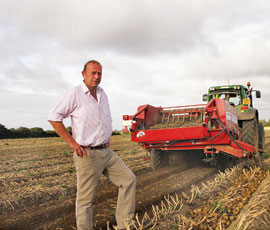
The fewer times a potato is handled, the better its chances of remaining free from bruising, says Will Gribbon (pictured). And one of the best ways to achieve this at harvest time is to windrow them, place harvested potatoes on top of a bed which has yet to be lifted and, in effect, lift two beds in one pass with the harvester.
Mr Gribbon manages Heygate Farms’ Snailpit Farm, near Swaffham, Norfolk, where the annual area of potatoes runs to about 500ha, of which one-third is grown on land rented annually. Annual production is 25,000t.
“In total, we farm 2,260ha which, apart from the potato acreage, is also used to grow 200ha of sugar beet and 800ha of cereals,” he explains. “We also rent out about 200ha each year for the production of carrots, parsnips and onions.”
In terms of soil type, the free draining sand over chalk is easily worked, but does suffer in drought conditions. For the potatoes this means irrigation is essential.
The farm grows a wide range of potato varieties to cater for the demands of the market. Pre-pack are sold through packers to multiples, processing ones go for chips, while other more specialist early varieties like the farm’s own branded Norfolk Peer are sold locally and through New Covent Garden.
Four years ago, with an expanding potato acreage and ever greater demand from marketing outlets for early delivery of ordered tonnage, Mr Gribbon was faced with the problem of increasing output.
“The obvious solution was to invest in another trailed harvester, more trailers and more labour,” he says. “But we were already running two harvesting teams and while we clearly needed more output, I didn’t believe we could justify that level of investment.”
A large multi-row self-propelled harvester was also discounted – the light land did not require engine-on traction and power and it was better to be able to unhitch a tractor and use it for other duties when the potato harvest was over.
The solution, he realised, was to take the windrowing route, which would mean the investment required would be limited to a new windrowing harvester.
Windrowed potatoes about to be harvested, along with the bed beneath.
“I reasoned that if we lifted and delivered the potatoes on to the top of the next unharvested row, one trailed harvester could lift two beds and the potatoes would be handled less overall,” he explains. “The amount of trailers, tractors, harvesters and labour would remain almost unchanged – yet output would be virtually doubled.”
In 2008 a Grimme WR200 windrower was delivered to the farm and hitched up to a John Deere 6930. Towed inline, the crop is lifted on to the main web via an intake using two Diablo rollers and four spring-loaded disc rollers.
The web employs an adjustable rotary agitator and the lifted potatoes are delivered by a cross conveyor to the right of the machine on to the centre of an adjacent row – its delivery point hydraulically set.
These are then harvested along with those still in the bed beneath by a Grimme GT170 complete with a double multi-sep cleaning system and powered by a Fendt 718 Vario. Graded by four pickers, the potatoes are then elevated and delivered to boxes via a Broadwater Fall-Breaker.
“Output using this system is about 10 acres/day, which I think is about right,” he says. “It means we can usually meet our ordered tonnage in the short time allowed each day and our second harvester can continue lifting another variety in another field. But more importantly, the crop is handled gently due to the greater volume of crop and soil being lifted by the shares and passing over the webs and cleaning systems.”
“During the four years we’ve been windrowing we’ve learned how to get the best from it,” he says. “The golden rule is to never get more than one row ahead of the harvester – if we get a rain-stopping downpour, having potatoes lying on the surface is not good news.
“We also use the windrower to open up fields on the headlands and for the first pass down the rows. The lifted row creates a space for the harvester’s off-side wheel to run in without damaging any potatoes.”
There are limitations though, and while windrowing is used to harvest the salads and early crops, the bulk of the maincrop varieties do not lend themselves so well to the system.
“There are just too many potatoes for the harvester to handle when we harvest the maincrops and extra care is needed to avoid damage, as these potatoes are likely to be in store for some time,” he says. “We just put the two harvesters together and let them get on with it.”
The Grimme GT 170 harvester works at the same forward speed as it would when harvesting a single bed.