Choosing the best piece of kit for the right task
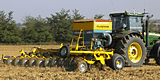
What type of kit do you need to direct drill? We’ve asked three manufacturers what they recommend.
Claydon
Simba-Horsch
Moore Unidrill
Farmer-turned-drill builder Jeff Claydon shares his views here:
The Claydon Drill was developed by Jeff and Oli Claydon for oilseed rape establishment on the family farm, offering reduced passes on their heavy clay soils. After trying the tined drill with wheat and without cultivation, its ability to operate as a direct drill was soon established.
“We band sow into a 15cm strip of cultivated soil, leaving 15cm either side of it untouched,” says Oli Claydon. “So our 4m version has just 11 coulters and needs 50hp per metre to pull.”
Working widths are 3.45m, 4m, 4.8m and 6m, and Mr Claydon says that as a cultivator drill that can be used as part of a min-till or direct drilling system, wearing metals costs are estimated to be about £1/acre.
The Claydon drill uses two rows of tines with the second directly in-line with the first.
The 19mm wide, leading tine is said to break soil beneath the seeding depth to create a drainage channel, while a wide-section A-share prepares the band into which seed is distributed. Press wheels firm the soil behind the tines.
“It can look untidy because when you’re drilling into stubble, half of the working width is untouched, so until the crop is established, it looks very much like a stubble field,” he says.
“Visually, that is the main drawback of the system and despite the appearances, we’ve had some good success working on varied soil types and wheat yields have stayed constant,” adds Mr Claydon.
Do you agree? Challenge the experts and get their feedback in our Direct Talk forum …
Claydon Drill | |
Working widths | 3.45m, 4m, 4.8m, 6m |
Key features | Two rows of tines for band cultivation |
Prices | £25,500-£42,000 |
Sales director of Simba-Horsch, Guy Leversha shares his views here:
Direct drilling only becomes an option for cost reduction when soil is in good enough condition to handle the system, says Mr Leversha.
“It’s important to take steps to get soil right before jumping into direct drilling, and even then, it’s not necessarily a full time system that can be used all the time,” he advises.
Mr Leversha says although direct drilling appears to offer cost benefits for reduced passes, there can be disadvantages too.
“If you want to try direct drilling, make it a strategy to exploit when conditions are right,” he says. “And that really is at a time when you don’t have to rely on other forms of soil movement or cultivation to deal with additional aspects of seedbed management, such as compaction.”
Soil condition above and below the surface is important if direct drilling is to be successful, regardless of the soil type.
“You also need a drill that can offer a variety of working modes,” he says. “It would be churlish to invest in a drill that can only offer direct drilling capabilities – you should consider one that can handle a variety of conditions and blend into different seedbed production systems.”
The firm’s latest Sprinter tine drill range works on a band sowing principle, which has fewer tines in contact with the ground to reduce draft and power requirement. It cuts down on wearing parts too, says the firm, and a 4m CO model, capable of outputs of 70-75 acres/day with a 150hp tractor, has running costs of about £22/acre.
Do you agree? Challenge the experts and get their feedback in our Direct Talk forum …
Horsch CO and Sprinter drills | |
---|---|
Working widths | 3m to 12m |
Key features | Duett coulter, low power requirement, trash clearance |
Prices | £25,000-£100,000 |
Inventor of the Moore Unidrill, Sam Moore airs his views here:
Sam Moore has been involved in direct drilling for 30 years and says there is a time, place and strategy in which to involve direct drilling as part of a cereal establishment regime.
“It suits spring sown crops following winter cereals, or wheat after OSR, maize and beans because the trash issues and volumes are not as intense.”
Shallow cultivations and min-till are important, as is crop rotation and soil condition, he says. “When it comes to yield, you get out what you put in.”
Perhaps no more than 25 per cent of a farm should be direct drilled in any one season, he says. “Even with disc coulters that can cut through surface trash – and the Unidrill has enough coulter pressure for effective penetration – if soil structure and condition is anything less than 100 per cent, you should be prepared to expect yield losses from direct drilling.”
Using discs, the Moore drill offers contour following, effective depth control and a 16cm row spacing and can be applied to conventional and min-till systems in addition to direct drilling.
“Compaction and lack of tilth are among the key issues that need to be addressed when looking for good soil condition,” he says. “And those, combined with a dense mat of chopped straw that provides a good home to slugs, can stack heavily against choosing to adopt direct drilling techniques.”
“But there are savings to be made if direct drilling can be incorporated on a rotational basis, in a crop establishment regime.”
Do you agree? Challenge the experts and get their feedback in our Direct Talk forum …
Moore Unidrill | |
---|---|
Working widths | 3m, 4m, 6m |
Key features | Coulter pressure, depth control |
Prices | £20,000-£40,000 |