Correct application makes the most of fertiliser
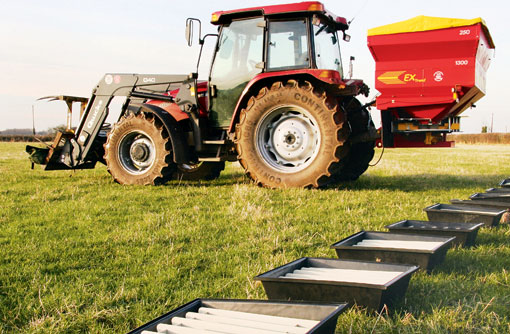
A 2011 survey of UK growers revealed that about one-quarter of growers never calibrate their fertiliser spreaders and could, therefore, be losing out in crop yields as well as missing the vital Hagberg specs for milling wheat.
The 2011 British Survey of Fertiliser Practice (BSFP) also found that a further 9% check their settings less than once a year. Ian Matts, agronomic co-ordinator of Yara, believes that with uniformity of fertiliser distribution being critical to results, farmers can be suffering sizeable losses without even realising it.
“Uniformity of distribution is measured by the coefficient of variation (CoV) and any value above the 10% that accounts for “field conditions” can have a financial impact. A poorly calibrated spreader and poor quality fertiliser are two factors which can lead to the increase of CoV which will ultimately leave some areas of the field under fertilised and other areas over applied.”
While a CoV of less than 20% may go unnoticed, with no visible signs in the field, the impact can still be costly, especially with current crop values and fertiliser prices. Above 20% and striping is usually seen in the crop. However, by this stage, the damage has already been done, stresses Mr Matts.
 |
---|
Estimates by Ian Richards of Ecopt show that a 20% CoV means a loss of ÂŁ8.79/ha based on ammonium nitrate at ÂŁ350/t and wheat at ÂŁ165/t. At 30% CoV, this rises to ÂŁ17.80.
As well as yield, the quality of a crop can be affected by poor spreading of nitrogen, adds Mr Matts. Yara trials have shown the Hagberg Falling Number in milling wheat fell from well above 250 – the level required by UK millers – where the CoV level was acceptable to 150 with a CoV of 30%. Furthermore, it is now a requirement under NVZ guidelines to calibrate spreaders.
The first step to improving spreader accuracy is tray testing, says Rob Foxall, managing director of SCS Spreader & Sprayer Testing. “This is the only way to ensure fertiliser is applied accurately and evenly.”
Trays are set out across the spreader width, then the spreader is driven across them. Fertiliser from each of the trays is then transferred into separate tubes and the contents are recorded, with the CoV calculated by measuring the variation in each tray from the average contents.
If the results of the first run are unsatisfactory, changes are made to the spreader settings and the process is carried out again until the correct setting is obtained.
Regular checking is important as material passing through the spreader can lead to veins wearing and a reduction in performance. “Material can also build up on the veins, especially sulphur during humid weather conditions,” says Mr Foxall.
Spreading tips in the field
• Machine height: check a mounted spreader is level on the linkage and the discs are at the correct height above the crop|
• Forward speed: maintaining the recommended forward speed is a vital element in achieving a consistent application rate
• Wind conditions: do not spread in windy weather
• Bout width: always work at the correct working width
• Relative humidity: manufacturers’ settings and recommendations relate to “good” spreading conditions (low humidity). In damp weather fertilisers absorb moisture and this will affect the flow rate and application accuracy
• PTO speed: check the engine rpm required to achieve the recommended pto speed and ensure this is maintained
• Headlands: leave enough space for two bouts around the field edges. Switch off the machine in time to prevent double-dosing. Employ and adjust headland border discs and check these devices and controls are working correctly.