How to avoid “CIPC legacy” residue breaches in potato stores
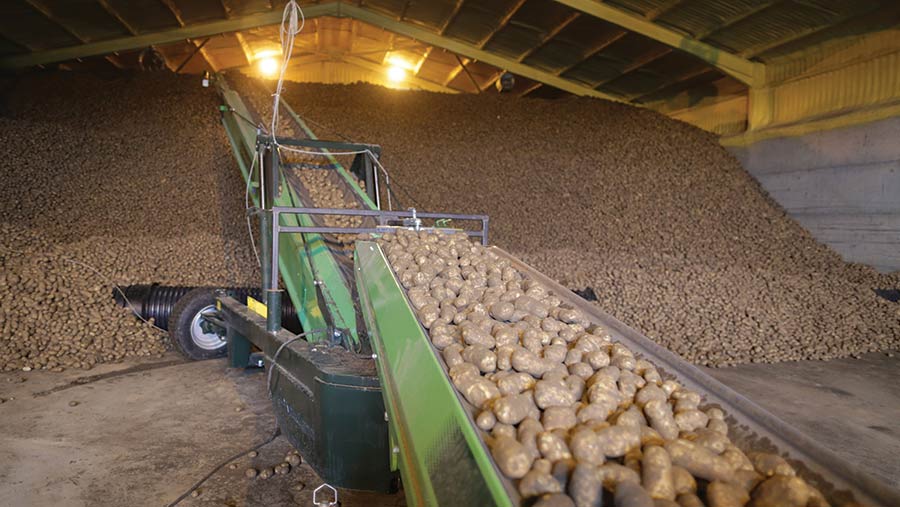
Potato growers who used sprout suppressant chlorpropham (CIPC) need to ensure stores are thoroughly after the 2020 ban to lower the risk of residue exceedances.
Plant growth regulator CIPC was the potato industry’s go-to method of controlling sprouting in store and was in commercial use from the 1960s until the the European Commission’s Standing Committee on Plants, Animals, Food and Feed (SCoPAFF) recommended CIPC’s approval for non-renewal.
See also: How to stop sprouting in potato stores without CIPC
Maximum residues
Potato growers were able to buy CIPC products until 8 January 2020 and could legally use them in potato stores up to 8 October 2020.
Typically, the maximum residue limit (MRL) – the highest level of a pesticide residue that is tolerated in or on food or feed – is dropped to the 0.01mg/kg limit of detection (LOD) once withdrawn.
In the UK, the vast majority of CIPC was applied as a hot fog, where an aerosol generator heats the liquid concentrate using LPG or petrol.
As the fog exits the generator and into the store’s ventilation system, it cools and forms microscopic crystals, which are deposited on tubers, but also all over the fabric and infrastructure within a store.
This could be walls, ceilings, fans, ducting, pressure chambers and boxes, where in use, and if the crystals are left in the store, they can volatilise in the future and contaminate untreated crops.
Quantifying risk
Recent research led by the European Potato Processors’ Association (EUPPA) has tried to quantify residue risk to untreated crops loaded into stores with a history of CIPC use.
Some 358 samples were taken across north-west Europe, and it was shown that about two-thirds had a detectable CIPC residue. Of those positive samples, 95% were below 0.4mg/kg. The current MRL is 10mg/kg.
It is unrealistic to believe farms will rebuild stores from scratch to eliminate potential MRL exceedances, so measures need to be taken to reduce the risk for growers concerned about crop rejections caused by contaminated stores.
Armed with the results of the study, plus further risk assessment data requirements, registration holders Certis and UPL have applied to the European Food Standards Agency (Efsa) for a temporary MRL that is higher than LOD.
As a condition of a temporary MRL, it is likely that the European Commission will expect the potato industry to make significant efforts to minimise any residue risk, including store cleaning.
Nick Green of store hygiene experts Stored Crop Conservation and chairman of the NAAC CIPC applicators group, says growers must be proactive in store cleaning.
He says the most obvious starting point is removing as much dust as possible from all accessible areas of the store with an industrial vacuum.
Pressure washing is also likely to be a useful tool, with the caveat that it should be done with cold water, rather than hot.
“CIPC gets into concrete, so stores may have a very high residue loading in the floor and heat will only bring more to the surface. Use cold water and repeat as often as possible.”
Replacing plywood
Other areas of concern are plywood ducts and tunnels in older stores, which may have absorbed high levels of CIPC, and replacement should be considered.
Similarly, old foam insulation may have to be removed or re-covered with fresh foam to lock in the chemical.
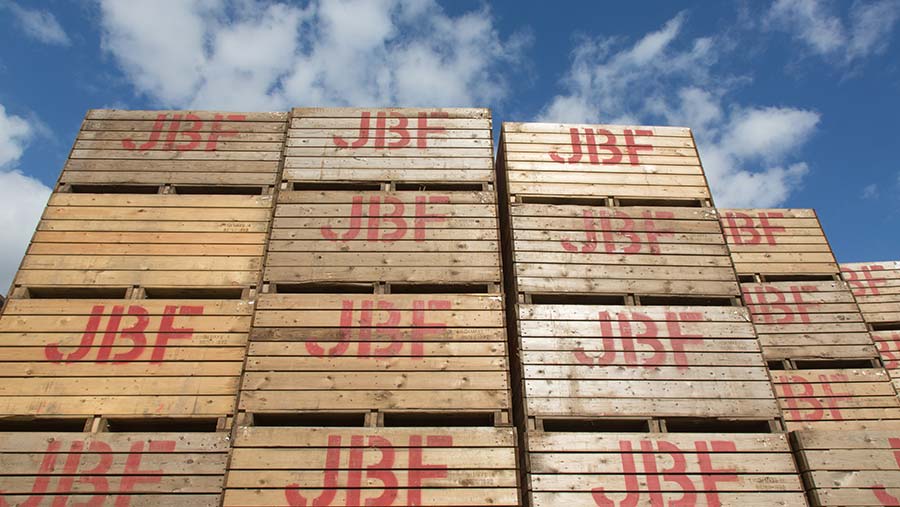
© Tim Scrivener
Mr Green also recommends leaving contaminated boxes outside and exposed to the elements, ensuring they are not stacked too high or too tight to maximise breakdown of CIPC residue locked in the timber.
“You have got to be proactive or something might be picked up and you then end up with an unsaleable crop,” he warned.