Direct drilling brings long-term rewards in Wiltshire
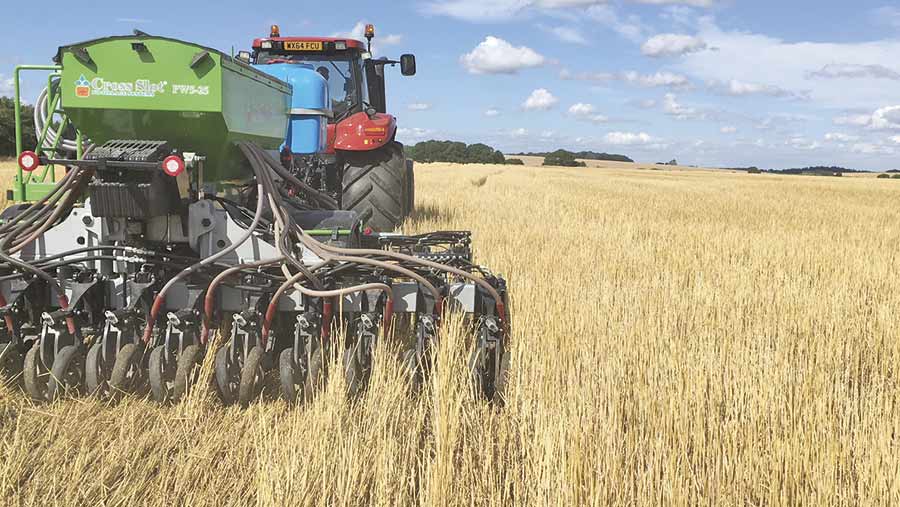
No cultivations have been carried out for the past three-and-a-half years at a Wiltshire farming business, since the decision was taken by the father-and-son team of George and Patric Hosier to move to direct drilling.
During that time, there has been a reduction in the use of crop inputs and significant savings in time and fuel use across the 450ha of crops – with further efficiencies anticipated as the system matures and soils improve.
With the focus shifting to building soil biology, the rotation has been extended and cover crops have been integrated, with the farm’s existing cattle and sheep enterprises being used to graze the majority of them.
See also: Top tips from two US no-till and cover crop veterans
Spring crops have always featured, with spring barley being a mainstay in the rotation, but now they are drilled “on the green”, with glyphosate used to destroy the preceding multispecies cover crop the day before they go in.
Soil resilience
Already, the varied soil types farmed by PT Hosier & Son at Wexcombe, near Marlborough are more resilient and able to cope with unpredictable weather, while minimal soil disturbance means the blackgrass burden is becoming more manageable.
“Our soils are holding together well and infiltration rates have improved, so there’s less risk of run-off,” says George.
“We have also seen big improvements in blackgrass control in some situations, with two crops being produced without the help of any grassweed herbicides.”
Both of those were later drilled and were in fields coming out of grass, he reveals. “In other situations, we haven’t been able to reduce weed populations as much, so we will be making more use of grass leys on our calcareous soil types to help.”
Drill choice
Six years ago, when the Hosiers were considering the purchase of a new drill, they were keen to reduce the amount of ploughing taking place, by doing more minimal tillage and extending the time between ploughing from three to six years.
“We were ploughing to help with blackgrass control, which was time consuming and costly,” he recalls.
The farm’s previous tine drill was unable to cope with chopped straw, so where ploughing hadn’t taken place all the straw had to be buried first – resulting in four passes before drilling could commence.
“We needed to change, to restructure our soils and bring our establishment costs down. Finding one system to suit all of our requirements wasn’t easy, especially as we also didn’t want to use 300hp to pull whichever system we chose.”
No-till advantage
At the time, two Nuffield scholarships on no-till farming were creating interest, so Mr Hosier went to have a look at the results from some early adopters.
“Everything I saw on their farms proved that no-till could work,” he adds.
“We went ahead and had a trial 30ha area of spring barley direct drilled by Primewest using Cross Slot technology in February 2014, with half going into a mustard cover crop and the remainder into stubble.”
That experience encouraged him to order a Cross Slot drill, which didn’t arrive until the following February. In the meantime, he had half of his winter wheat contract drilled in September 2014.
“We drilled two fields next to each other, so we could compare the old and new systems. It rained so heavily a few days later that we experienced considerable soil run-off from the conventionally drilled area. The new drill proved itself before it arrived.”
On-farm use
Since then, he has been using the drill across all of the spring and winter crops grown, as well as to establish new grass leys.
To date, spring cropping has proved to be more challenging than winter, while cover crop destruction and crop nutrition requires further fine-tuning.
A modification to the drill has given Mr Hosier the ability to apply liquid fertiliser with the seed at drilling. “It has helped our spring crops get away quickly, as without any soil disturbance you don’t get mineralisation of nitrogen occurring.”
He also admits to learning to drill spring crops when the ground conditions are suitable, rather than waiting for a certain soil temperature.
“Having been through a tricky time in years two and three, with the expected yield dip, our crops are looking good his year.”
Slugs were the biggest issue in those first two years, he acknowledges. “Two things have helped. The rotation has been extended, so that we’re now only growing oilseed rape once every 10 years, and we purchased a stripper header to help with residue management.”
Stripper header
To avoid leaving harbours for slugs and prevent chopped straw lying unevenly and forming clumps when wet, the stripper header is used for the wheat, barley and pea harvest so that straw is left standing across the fields.
With far less plant material going through the combine, the chaff is much easier to spread across the whole width and the bulk of the residue is distributed evenly.
“The stripper header has had a huge benefit on time and diesel – we were doing 200 drum hours per season before, now we are down to 139 drum hours.”
There are some losses at harvest with it, but they’re not significantly more than using a normal header, notes George.
“There are certain weather conditions where we wouldn’t use it and our oilseed rape and bean crops can’t go through it. We also use some straw on the farm for our cattle and sheep enterprises.”
Crop inputs
Some of the most immediate benefits from direct drilling have been the reduction in crop inputs, reports George Hosier.
No insecticide or seed treatment has been used on the farm for the last two years, as well as no bagged P and K.
“We are going to look at nitrogen next,” he reveals. “The system mobilises soil biology and recycles nutrients, so we might be able to reduce our nitrogen by 20%.”
Fungicides are also in his sights. While he hasn’t made any alterations to his fungicide programme so far, he would like to test things out next year in a first wheat after peas, which followed three years of grass.
Another benefit of the change to direct drilling is the farm’s slimmed down machinery fleet. “The drill was expensive,” admits George. “But it has allowed us to sell other machinery. We now operate with just a sprayer, a combine, a set of rolls, a top dresser and our drill.”