4 growers share their experiences of controlled traffic farming
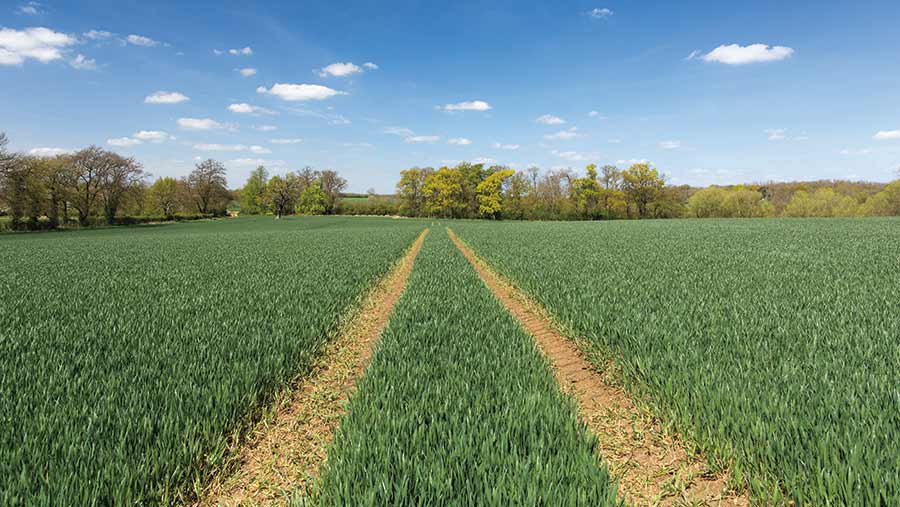
Recent years have seen a renewed interest in soil health in a bid to raise yields.
Most farmers will agree that repeatedly driving on fields with heavy machinery causes damage, especially when it’s wet.
They will also admit that soil behaves differently when it isn’t being squashed all the time, giving them opportunities to reduce the amount of tillage, drill at the optimum time, cut their fuel consumption and improve soil drainage.
So it’s not surprising that 44,000ha across Europe are now in controlled traffic farming (CTF), with a further 12,500ha in seasonal CTF and another 20,000ha planned for conversion in the coming year, to either full or seasonal CTF.
See also: How controlled traffic farming can help improve grass yields
As a concept, it makes a great deal of sense. Restricting machinery movements to permanent traffic lanes to reduce areas of compaction brings benefits to both soils and crops, helps to achieve environmental aims and can be used to reduce production costs.
But whether it brings all these benefits in every season remains to be seen, with critics highlighting the high costs of converting machinery fleets, as well as the frustrating teething problems that many converts encounter.
While there’s still much to learn about CTF and its implementation, it is gaining momentum, says Tim Chamen of CTF Europe, who adds that it has been helped by the machinery industry finally embracing the practice and bringing customised machines to the market.
“It’s something that could appeal to smaller and mixed farms too, so the prospects are good,” he believes.
What is controlled traffic farming and how do you adopt it?
CTF is the practice of running farm machinery over the same parts of the field, every year, so that compaction resulting from these passes is confined to the smallest possible proportion of the field.
CTF can be put in place in stages, on any scale and at any cost:
- Learn the basic principles.
- Do a cropping and machinery inventory – measuring all the critical dimensions of the machines.
- Decide which will fit into a CTF system.
- Plan a CTF system that minimises conversion costs.
- Thoroughly research and implement an RTK autosteer system.
- Plan a long-term machinery policy.
However, some obstacles remain, he acknowledges, with the incompatibility of current machinery fleets being the biggest problem.
“There’s also a perception that it costs a great deal to convert, as well as high numbers of farmers who simply don’t recognise compaction as a problem,” he says.
“Then there’s the mindset challenge. If you don’t know what CTF is and what it does, then you won’t appreciate what it has to offer. There are a whole host of economic and management benefits, which complement the environmental aspects.”
The drill is the key piece of kit in CTF, and its choice will depend on a whole range of factors – including cropping, rotation, residues, weed control, nutrition, soil type and field size, says Philip Wright of Wright Resolutions.
Which drill?
“The main question that growers should ask is whether they are choosing the drill to suit the crop’s requirements or to cope with the state of the field,” he stresses. “CTF does add in a few complicating factors.”
With CTF, there is an increase in direct drilling and, as a result, a greater reliance on the drill for some pre-cultivations. “The drill options are basically discs, tines or disc/tine based. But there are variations and, for many, residue management is a key requirement.”
And that’s not always easy, he acknowledges. “A big amount of loose residue on the soil surface can cause problems. When you’ve got green straw after a heavy crop of barley, for example, there’s a need for the combine to give a consistent residue chop and spread.”
Disc drills are better at coping with high levels of residue, as they offer trash cutting, he continues. “They’re good in dry conditions, and they offer low soil disturbance, but there is a hair-pinning risk with them.”
There is also a greater tendency for smear to occur if the rake angle is very deep, and it is important to match the disc diameter to the depth of work for best results, he adds.
Tine-based drills require trash clearance, as they don’t cut, he points out.
“There is a degree of cultivation included with these and they are good in wet conditions, as there’s no smearing.
“However, they are a higher soil-disturbance option, which can have implications for weed control. And residue movement ahead of the tines is possible, along with a risk of the soil moving sideways.”
Being in control of sideways soil movement is important, as where loose soil goes on to an undrilled strip it can create problems with weeds and slugs, he warns.
Where cover crops are being used, the drill has to be able to cope with surface residue, says Mr Wright. “Although residue will give a less sticky soil surface, especially if it is still rooted, it can be a problem. That has to be considered when buying your drill.”
Case study: Driver Farms, Suffolk
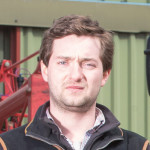
Adam Driver © Tim Scrivener
A willingness to keep an open mind and carry on learning has been essential for Suffolk grower Adam Driver as he gets to grips with CTF.
Farming 1,200ha of combinable crops on heavy clay soils from his family’s base at Brittons Farm, Brockley, near Bury St Edmunds, Mr Driver sees CTF as an important part of the conservation-agriculture approach that has been adopted on the farm in recent years.
“We’re in a transition period,” he admits. “But the only way to make the sort of changes that we needed to make was to try new things, be prepared for not all of them to work and to gain experience from the process.”
Soil health
The main reason for introducing change was to improve soil health, he says.
“Put simply, we had been chasing around too much and over-cultivating. We needed to reduce our reliance on heavy machinery and cultivations, so that soils could recover from frequent traffic and get their structure back.
“We were also losing the battle with blackgrass and having to spend too much on herbicides, without achieving a satisfactory outcome.”
His other aim was to improve timeliness, by being able to make the most of weather windows. “We have done that almost immediately,” he says. “Soils drain better if they are not compacted, so we can travel on them sooner. We are also using wider kit, which has helped to increase our work rates.”
With a mixture of owned, rented and contracted land, Mr Driver was particularly aware of the damage being done to soil structure in wet years.
However, CTF was considered to be just one way of helping to overcome these challenges – other changes have included introducing more spring cropping, the use of cover crops and companion planting and a focus on building soil organic matter with manures and sewage sludge.
“We are learning as we go along. One of the main lessons to come from our first full year is that we have to maintain a degree of flexibility. It’s the only way to be able to react to the season and the conditions.”
What was a wheat/rape rotation has changed considerably, with spring beans and spring wheat joining the line-up, as well as winter beans. “Oilseed rape is now being grown once in every five or six years,” he says. “Rotation will be key to getting the blackgrass control we need.”
Direct drilling and reduced tillage techniques are being used as much as possible, so that the fungi and bacteria needed for a healthy soil profile can flourish. Just 20% of the soil now carries traffic – a huge reduction from the previous minimum-tillage regime.
Having changed the sprayer at Driver Farms three years ago to a 36m Bateman, Mr Driver has been able to switch to a 12m CTF system by adding a 12m Horsch Joker cultivator and a 12m Horsch Sprinter drill to the fleet and using RTK GPS guidance. A new combine is expected later this year, bringing with it the necessary extended auger to reach the next tramline.
Trash management
“Considering this is our first year of using CTF, everything has gone fairly well,” says Mr Driver. “There has been a bit of an issue with trash management, as there are times when the combine is simply chucking too much stuff out of the back.”
That can have implications for slug populations and the growth of the following crop in certain situations, he explains.
“The new combine will have a better chopper, so hopefully we can get to grips with this,” he remarks. “Otherwise, it’s about being conscientious with the combine and keeping the cutter sharp.”
He is also cutting the stubble a lot higher than previously and considering the use of a straw rake.
After combining, Mr Driver relies on either a cover crop or the Horsch Joker to create a bit of tilth before drilling. Cover crops and heavy soils can be a tricky combination, so where they are used ahead of spring crops, they are sprayed off in December.
“We are still working out where cover crops can be useful,” he says. “They are being introduced fairly slowly, so that we can get the best from them.”
The higher work rates afforded by CTF are a huge bonus, he adds. “With our old cultivation regime, we could cover 40-50ha per day. Now we are up to 150ha per day.”
Case study: Crathorne Farms, North Yorkshire
North Yorkshire farmer Joe Dugdale describes himself as an amateur when it comes to CTF, having returned to the family farm only six years ago.
With 600ha of arable land and 200ha of grassland supporting a dairy herd, Crathorne Farms was running a plough-based system together with a Sumo Trio at that time, but it was coming up against soil structure problems and compaction issues.
“There were added complications caused by making muck and straw applications, often in wet conditions,” Mr Dugdale recalls. “We were aware of where the compaction was and were carrying out remedial work where it was required, but we were keen to avoid it occurring and reduce the traffic on the fields.”
The theory behind CTF is interesting and makes sense, given the importance of soil, he believes. “Keeping carbon and nitrogen in the soil is vital for its health. It also allows the retention of crop residues and protects the soil from surface run-off.”
After investigating CTF in more detail and researching the machinery options, Mr Dugdale bought a 4.6m Horsch Terrano cultivator to run at 4m, having opted for a 4/8m CTF system with 24m tramlines.
“There was no width relationship with the existing farm kit, so we had to make some changes in order to be able to do CTF.”
This was followed by the purchase of a Rapidlift, for use in front of his Vaderstad drill, and then a combine harvester with a 9m header that could be run at 8m.
“Our first harvest worked really well and convinced me that we were going along the right lines,” he recalls. “The trailers ran on the tramlines only and everything went very smoothly.”
Drilling problems
The land was then cultivated with the Terrano before the oilseed rape went in. “Again, that was great and very straightforward. But when it came to drilling our winter cereals, the drill wouldn’t run and kept bulldozing.”
In the end, he had to borrow his neighbour’s drill to get the task completed.
“That experience was our first lesson,” acknowledges Mr Dugdale. “With such a big change, don’t expect it all to run smoothly.”
His advice to those considering CTF is to aim to get the basics right, before expecting to make progress. “And make sure that the system you go for really is the right one for you.”
He also believes that it is best to try to use a machinery width of at least 6m. “If not, make sure you have a way of loosening the intermediate wheelings. With a 4m system, you are still running traffic on 40-45% of the field, which is too high.”
His other lessons are that it is unrealistic to expect contractors to stick to CTF lanes, to ensure that farm staff are on board and understand why changes have been made and to be prepared to seek advice from those who have gone before you.
“It can’t all be achieved in one hit,” he warns. “Patience is essential, as well as the right mindset.”
Case study: Foxburrow Farm, Norfolk
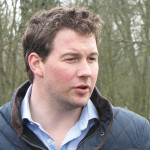
Will Goff
Mid-Norfolk farmer and contractor Will Goff of Foxburrow Farms has seen a dramatic improvement in work rates since switching to CTF in 2013.
“After just two years, we were achieving twice our previous daily work rate for the same number of hours worked, while halving our diesel use,” he reports.
“Part of the reason is that we now no longer need to deep-loosen and can just use a 10m-wide shallow disc cultivator.”
While that was the biggest difference, it wasn’t the only benefit experienced by the 2,000ha arable business, he continues.
“There has been better water infiltration, with no standing water in our fields this winter, despite the very wet weather. It may just be a coincidence, but our neighbour’s farm was almost under water.”
Farm workloads have become far easier to plan, says Mr Goff. “The Trimble guidance system was easy to set up and run. Tillage is now done with either one or two passes of the discs.
“Furthermore, we now have a lower horsepower requirement. Our 450hp machine has been swapped for one with 130hp less.”
Before making the change he was running the business as two separate entities, due to the distance between the blocks of land, complete with two sets of staff and associated costs. “That has changed and it is all run as one now. It’s much simpler to organise.”
Small fields
Mr Goff’s 10m/30m CTF system is suited to the small fields and tight, narrow lanes that are typical of his part of Norfolk, although he thinks that the best working width for CTF is 12m. “In an ideal world, that’s what we would be doing.”
His advice is to try to match the sprayer to the combine to get a harvest CTF system established, rather than starting with the cultivator.
“If you map the fields with your sprayer, then all of your heaviest equipment will stick to the tramlines. Get that right before you choose your cultivator and drill.”
His starting point came when he changed an old sprayer, replacing it with a 30m machine. “That allowed us to fit in with our 10m Claas combines.”
Mr Goff’s other recommendation is to research all the GPS manufacturers thoroughly before making a final decision. “It can be very expensive to change a system at a later date, so time spent at the beginning is a good investment.”
Case study: Shimpling Park Farm, Suffolk
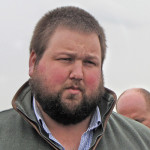
Nicholas Corp
Seasonal CTF is starting to facilitate reduced tillage on a heavy-land Suffolk organic farm.
Farm manager Nicholas Corp of Shimpling Park Farm near Bury St Edmunds explains that there are two operations that are not on CTF – combining and ploughing – but all the other operations are carried out on 8.8m traffic lanes.
“We are ploughing for two reasons,” he says. “The main one is grassweed control, as we have to rely on cultural methods for that, but we also use ploughing to terminate our grass leys. So we do have a predominantly plough-based system.”
All of the combining is done by a contractor, so that also remains outside the CTF system at present, he adds.
Cropping is a mixture of winter and spring crops, with wheat, barley, oats, beans, spelt and quinoa being grown on the 1,237ha home farm, with a further 709ha on contract. Livestock are making a reappearance, with New Zealand Romney sheep being introduced in 2014 to help recycle nutrients.
“The spring crops are helping us to get about 95% control of grassweeds,” he reveals. “They tend to appear twice in our six-year rotation, which has fertility leys for the first two years.
“We are also experimenting with cover crops between years three and four, when we are going from a winter cereal of wheat or spelt into a spring cereal of oats or quinoa.”
Timeline
Mr Corp has established a timeline to assist with the roll-out of CTF. In 2015, he established CTF lanes and reduced traffic, but didn’t do complete CTF.
“This year, all our cultivations, drilling and weeding will be on CTF,” he reports. “Next year, our wheel track gauge will move to 2.25cm centres.”
He also recognises the need to think about rotational reduced tillage and headland management, so that the farm keeps progressing.
His reasons for introducing seasonal CTF are numerous. “It reduces the risks associated with some of our cultural control methods, such as late drilling and spring crops. The soils are easier to work and they drain better.”
There is also a reduction in plant stress caused by compaction, while the weeding and hoeing operations have had improved results from not moving compacted ground in the wheelings.
“Our fuel use has reduced, for all our cultivations,” comments Mr Corp. “And it has really opened up the opportunity to reduce tillage and keep off our soils.
“Finally, it is allowing us to fully use the benefits of our RTK system.”