How Gold Cup winners are managing staff
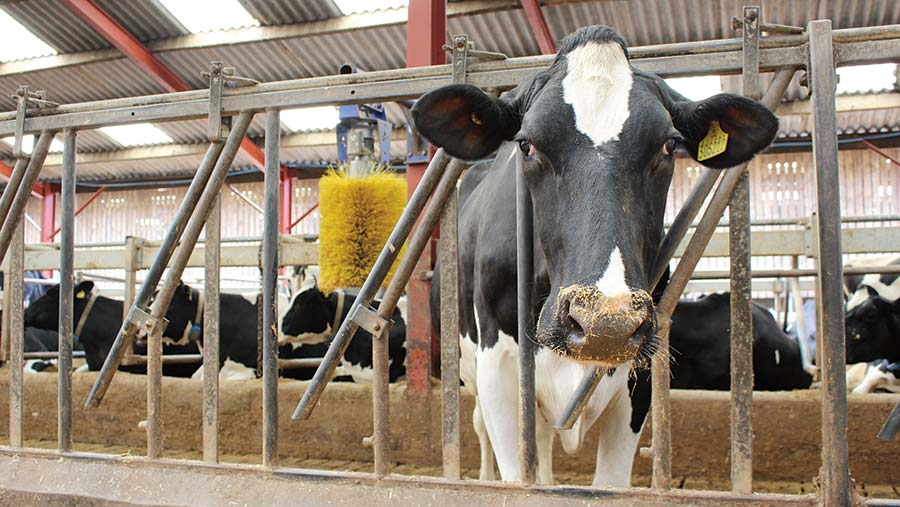
Teamwork, staff management and new technology are the three secrets to running a successful business, says Philip Metcalfe of Metcalfe Farms.
Last year the farm scooped the NMR/RABDF Gold Cup Award, with judges praising the team’s ability to push the business forward, with staff management a particular strength.
In 2016, with 900 cows, Philip managed the herd himself alongside a dairy team of mainly full-time staff.
Additional jobs outside of routine, such as tail clipping and machinery repairs, were outsourced.
However, over the past three years the farm has seen a lot of investment, with the herd size increasing from 900 to more than 1,300.
See also: Metcalfe Farms wins Gold Cup award
Accommodation has been built to house a further 400 cows and a 72-point rotary parlour has been installed.
This led to a review and restructure of the team. The farm now employs 35 full- and part-time staff, with some specific tasks outsourced.
Staff management
Existing staff were offered senior roles, with full training given. There are six senior managers overlooking five areas:
- Staff management – Aaron Armstrong
- Milking – Christine Whalley
- Calving and calf rearing – Hannah Rogers
- Cow health – Ben Greggs and Dominic Fox
- Milking routine, parlour management and mastitis control – Navada Lofthouse
The vacancies created by the promotions were initially filled by east European workers. While this initially worked, Mr Metcalfe says the attitude of some of the workers didn’t fit the business.
A decision was made to recruit candidates with no experience but with the right attitude. He says: “It’s important people have the right attitude and the ethos to work. We took the decision to replace one of the Polish couples with two new local recruits. They worked well for us and led to us replacing all the east Europeans with local workers.”
The farm has put together a staff induction handout which outlines the values of the farm, what staff can expect of each other and what the business expects of them.
Mr Metcalfe explains: “It sets out the tone of the business and gives employees the confidence in their position and role. We have found this a powerful tool as they are asked if they agree with the contents of the handout.
“We have used it before in a staff disciplinary situation, asking why they are not following the task they have agreed to.”
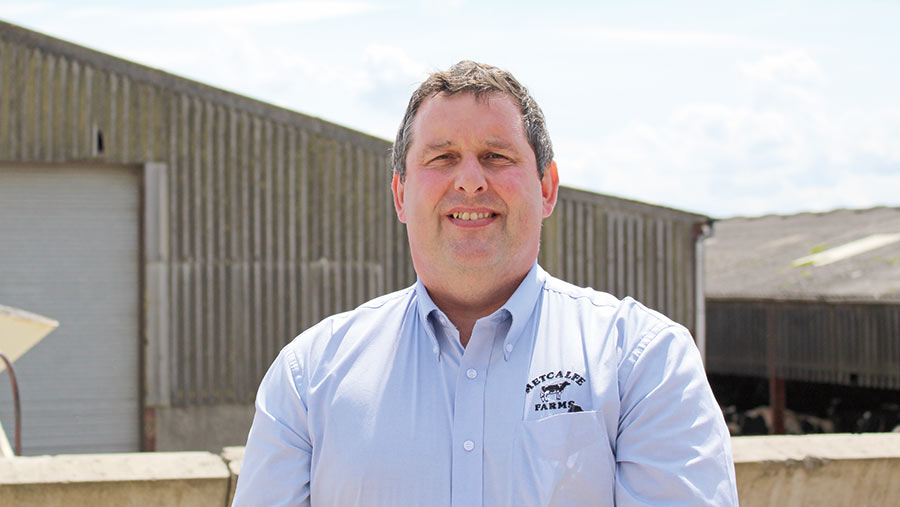
Philip Metcalfe
Investment has been made into equipment and staff facilities, with a clean kitchen, showers and toilets as well as some accommodation.
“Creating a nice environment for people to work and using technology to help make their lives easier has helped attract people to our business,” Mr Metcalfe says.
“For example, we changed the calf pens and made them easier to clean out. If we can make menial jobs easier that helps retain staff. We now have a waiting list of people wanting to work on our farm.”
Notably, two thirds of the team are women. Working shifts are based around individual needs.
Wider team
Mr Metcalfe took the decision to contract out some more specialist tasks. This has freed up his time to oversee the whole business.
The wider team consists of the following people in four key areas:
Feed:
- Hefin Richards, from Rumenation Nutrition Consultancy, provides independent nutrition advice
- KW Feed’s Anna Sutcliffe carries out feed analysis
- Mark Hall from Premier Nutrition Transition Management System advises on transition cow monitoring.
Animal Health:
- Regular vet is Philip Alcock from Bishopton Vets
- Vet techs from Bishopton carry out weekly visits to disbud calves, take genomic samples, gather up BVD tag and tests, take Johne’s blood samples and administer vaccinations
- Contract clipper visits four times a year to clip cows’ tails.
Breeding:
- An RMS technician carries out heat detection and AI and provides breeding advice
- Clarifide/RAFT Solutions analyses genomic samples and advises on breeding.
Milking:
- Ian Ohnstad from the Dairy Group independent consultancy provides advice on the milking routine.
The external team meets once a month alongside the senior management team at Metcalfe Farms to discuss herd performance, herd health, fertility and forward plan rations. They also have weekly telephone contact and all areas are reviewed quarterly.
Mr Alcock from Bishopton Vets says that when the herd was growing there was too much being asked of the herdsman as he was having to manage the herd as well as all the complex health treatments.
He explains: “When you start putting too much pressure on people things can slip and then you don’t hit the standards required.
“Now the vet tech team manages routine health tasks. It means animals are getting the right vaccines at the right time and used in the right way.”
However, Mr Metcalfe still has a firm handle on what is going on.
Any lame cows that are detected are dealt with immediately. Mr Metcalfe watches the entire herd walk into the parlour every Monday afternoon and will pull out any lame cows he sees. The foot trimmer will then come the next day to correct them.
Mr Alcock adds: “Philip has a high standard and is very good at detecting lame cows. Any cow that has been though the process more than once goes on the vet list to be looked at. The attention to detail means the farm never gets a build-up of chronic lame cows as they are being treated early.”
The aim is to have more than 90% of cows lameness free. The current mob score is 87%.
Farm facts
- Owned by brothers David, Brian and Philip Metcalfe
- 1300ha, with 200ha owned and the rest rented
- 1,306 cows average £PLI £143
- Cows housed all year round
- Cows milked three times a day through a 72-point Boumatic rotary parlour
- Supplying Paynes Dairies
- A 200kW anaerobic digester uses manure to produce electricity for the farm, green bedding and fertiliser.