European slaughter plant uses robots to stay ahead
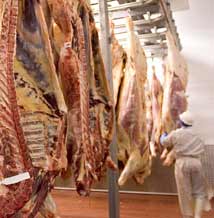
Slaughtering 93,000 pigs a week is pretty impressive stuff, let a lone regenerating 41% of all heat produced in the slaughter house. But this is the situation at Danish Crown’s Horsens abattoir, one of the biggest and most technologically-advanced slaughterhouses in Europe.
Although many processes are automated, with eight robots put to use in the slaughter line alone, nothing is wasted in the process. Animal fat is used in boilers instead of fossil fuels, saving about 5000t of CO2 a year, with all manure sent to biogas plants.
Every effort has been made to optimise energy use, with water consumption halved since 1988 and energy consumption also declining, according to Agnete Poulsen, Danish Crown.
“Environmentally effective technology is allowing such a decline, with a 15% saving of energy from a new singeing process alone, which uses a closed furnace and flame regulation,” she said.
Animal by-products are also recycled, either for energy purposes like bio-diesel or for feed. Energy consumption is 9kw/hours for each pig, with every robot also measuring water use which stands at 170 litres/pig.
Computers are also used to organise the arrival of pigs to a single minute, with a full truck being unloaded within 15 minutes into a lairage with capacity for 3800 pigs.
“The calm movement of pigs by manipulating floor design and using lights to direct the them means the lairage area is relatively stress-free. Pigs are then given an hour to settle before being moved by an automatic pushing gate to the CO2 gas stunning chamber,” said Ms Poulsen.
But, not only is pig welfare kept in hand, food safety is also a top priority. About 110 vets are employed on the line, with samples from every carcass taken and tested for various aspects. Various zoning and a well designed production flow means for example clean and dirty trucks outside the 82,000 sq m unit never cross paths.
In a blink of an eye it would be easy to loose track of a carcass as it moves around the abattoir, but with every carcass attached to a micro-chipped hanger, it means information on the carcass can be updated throughout the process, including carcass classification after passing through the Autofom classification system.
“With 1370 employees, most environmental challenges are regarded and treated as part of our daily task,” explained Ms Poulsen. “The ongoing challenges will be energy and water use, noise pollution and odour nuisance and transport issues,” she added.