Farmers Weekly Awards 2023: Farm Manager of the Year finalists
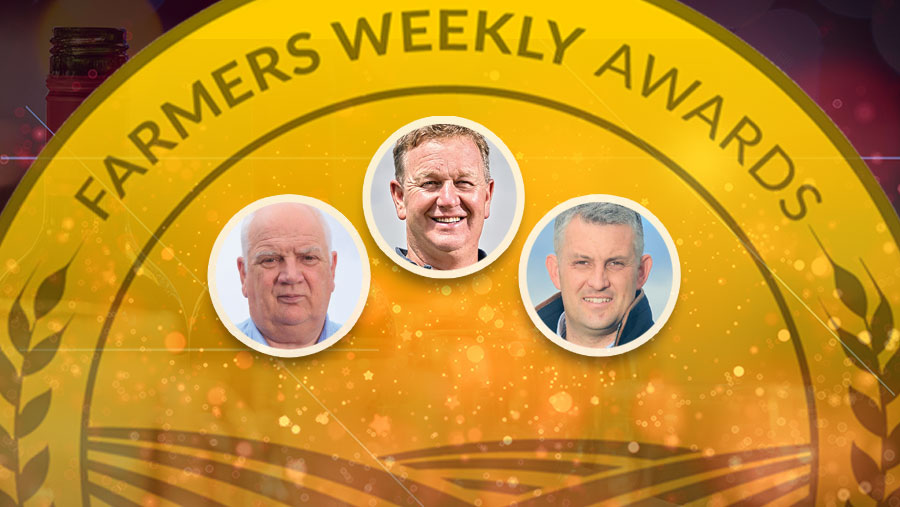
All three farm manager finalists have responsibility for very different large, complex businesses. They have all also managed much change in their roles.
See also: See the full 2023 Farmers Weekly Awards shortlist
The finalists:
Ray Beck
Welbeck Home Farm, Welbeck Estates Company, Nottinghamshire
Tom Deards
AJ & CI Snell, Windmill Hill Fruits, Herefordshire
William Haupt
Woburn Farms, Bedfordshire
The judges:
Rob McGregor
Last year’s winner
Suzie Horne
Farmers Weekly business editor
Richard Price
Independent judge
Ray Beck
Welbeck Home Farm, Welbeck Estates Company, Nottinghamshire
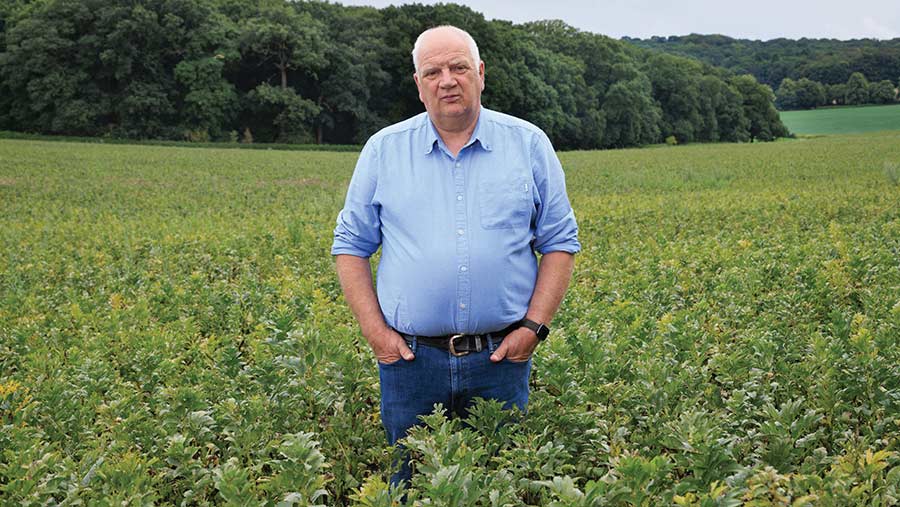
© Tim Scrivener
Farm facts
- 1,660ha owner-occupied on home farm
- Majority arable
- 250 dairy cows plus followers
- Small suckler herd of Belted Galloways
- Winter wheat, winter and spring barley, oats, OSR, spring beans, maize, sugar beet
- Annual cropping lets for onions, carrots, potatoes
- Extensive Higher Level Stewardship scheme
Ray Beck is responsible for the management, cropping, staff and day-to-day operations on the home farm of the historic Welbeck Estate.
He was appointed farm manager in 2012 and has implemented a move to min-till to address soil health generally, along with low yields on some of the diverse soil types.
These range from thin and stony limestone, variable loams to blowaway sand and heavy clay.
Much of the farm can be irrigated, but average field size is less than 7ha.
Some land is let on seasonal cropping licences to specialist vegetable growers on some of the irrigated light land, for onions, carrots and potatoes.
Most of the permanent and temporary grasses and the maize area support the 260 dairy cows, plus followers. The herd averages a yield just over 10,000 litres, with the bulk of this going to First Milk.
Added value
About 350,000 litres is sold raw to the on-farm producer of Stichelton cheese, while a further 10,000 litres of raw milk is sold through a vending machine in the Welbeck Farm Shop.
Crop marketing is done in collaboration with the farm consultant, and sugar beet is sold on contract to British Sugar.
A small area of asparagus is grown for the farm shop, along with malting barley for the estate-based micro-brewery.
There is also a newly established 32-head suckler herd of Belted Galloways.
Improved drainage and yields
On his appointment, Ray identified areas of poor drainage – much of which has been rectified.
He has initiated detailed soil analysis, enabling variable-rate application of fertiliser and inputs which has raised yields.
He has changed cultivation techniques, moving to min-till, reducing ploughing to only when essential.
Green cover crops have been introduced to add organic matter, prevent erosion and protect water sources.
Deep rooted lucerne is now grown as forage, maize is undersown with grass in a scheme with Severn Trent Water, also to reduce erosion.
Stubbles are overwintered where possible, anaerobic digestate is used to reduce bought-in fertiliser, while slurry and farmyard manure use is more efficient.
Soil health, crop husbandry, yields and profitability have improved too.
The farm has an extensive Higher Level Stewardship (HLS) scheme, and farmland bird populations have grown considerably during Ray’s tenure.
A Mid Tier scheme has been applied for and the estate was an early adopter of the Sustainable Farming Incentive.
Major investments championed by Ray include a new dairy, grain store and dryer.
As the Basic Payment Scheme reduces and commodity prices remain volatile, Ray aims to continue the improvements of the past 10 years using alternative and/or new break crops to maintain the area of first wheat and embracing environmental initiatives.
Staff
A safe working environment is priority, and training opportunities and ongoing assessments are provided.
Staff are also encouraged to join wider agricultural discussion groups, and attend farming shows and events.
There is a daily early morning meeting, along with WhatsApp groups, two-way radios and regular tool box talks.
Ray has introduced monthly staff meetings which include twice-yearly discussions about financial performance and farm strategy.
He has moved staff onto monthly salaries rather than hourly pay.
An active member of a local farmers discussion group, Ray hosts talks and training sessions for local farmers and others on topics such as health and safety, water catchment liaison, water and soil management.
What the judges say:
Ray has improved the output and profitability of the land he manages, embracing much change and also dovetailing with the requirements of the larger and diverse estate business.
Ray Beck summary
The judges liked
- Managed change over past 12 years
- Adopts new ideas and techniques
- Active involvement in local farmer discussion groups
- Hosts talks and training sessions
The numbers
- 2 full-time staff, one part-time, plus manager
- 10,000-litre average milk yield
- 40% of grain sold forward by June for 2023 harvest
- 8.5t/ha five-year average wheat yield
- 268 fields
Tom Deards
AJ & CI Snell, Windmill Hill Fruits, Herefordshire
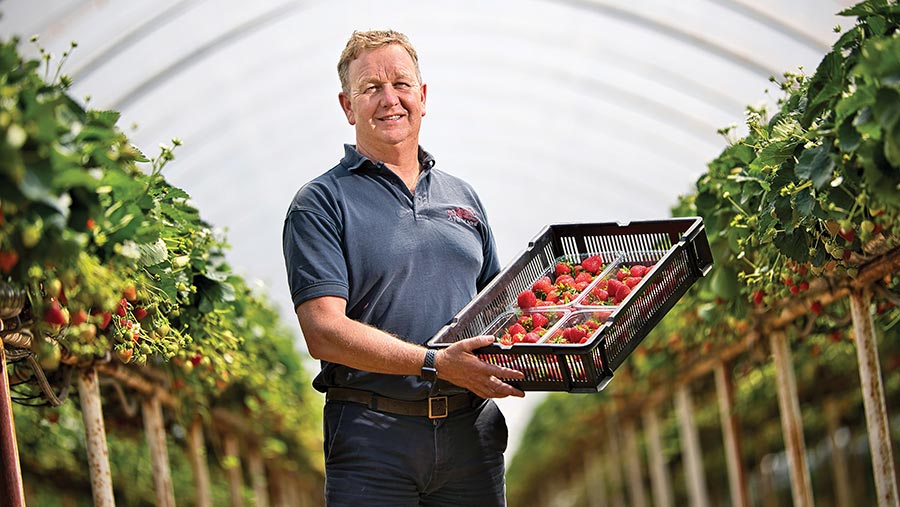
© Richard Stanton
Farm facts
- 49ha owned, 117ha rented
- Large-scale polytunnel soft fruit, field-scale blueberries, blackberries
- 166ha cropped, 8ha woodland, wildflower mixes and wetland
- Leaf demonstration farm
- Part organic
Tom Deards and the team at Windmill Hill Fruits deal with some staggering numbers.
They produce 1,000t of strawberries and 350t of raspberries for Tesco and M&S each year, along with 450t of conventional and 100t of organic blackcurrants.
A staff of 250 is needed to grow, harvest and pack these and other crops, in a high-pressure, slim-margin business.
Tom’s 11 years here, as farm manager and agronomist, have been a constant search for marginal gains which has seen expanded production from a reduced area, his introduction of soil-less systems in polytunnels, along with improvements in plant types and varieties.
Innovation
One of Tom’s most significant innovations was in 2020, spacing strawberry plants at 6/m rather than the conventional 10/m.
This was a big departure but has paid off, reducing cultural work and cost per hectare, with yields remaining similar.
He has instigated investment in stronger polytunnels, integrated pest management (IPM) and other environmental measures – including rainwater harvesting from 10ha of the polytunnels, which means the farm is, on average, 45% water self-sufficient.
Climate sensors have been introduced to help monitor polytunnel conditions, but Tom still spends much time physically assessing the environment and plants. Water is closely monitored and balanced to deliver the right nutrients.
He has also promoted the use of biofungicides and biocontrol insects – with disease modelling related to climate data, helping to ensure optimum fungicide timing, while growing degree-hour calculations and chilling models help steer plant growth.
IPM is increasingly by machine application, with £40,000 a year spent on beneficial bugs.
The team work closely with machinery manufacturers to test and refine application kit, as well as with Bayer and BASF on biofungicides.
Aside from the conventional fruits, organic blackberries (25t) blueberries (16t) and redcurrants (16t) are grown, much of which is frozen for sale through the farm website.
With labour representing half of production costs, crop type planning, planting dates and mechanising as many tasks as possible are key.
Marketing is through a grower co-operative, with a five-year adaptable production plan, backed up by an annual pre-season plan to create sales splits for the retailers.
The greatest accuracy is needed in the 13 weeks before harvest to allow flushes and shortages to be managed.
Production is benchmarked with Andersons through the grower group, which helps create targets.
Risk management
Markets are volatile if there is oversupply, hence Tom’s precise production planning.
He aims to get about one-third of strawberry production into the premium category which pays £1.20/kg more than for standard berries.
Reliance on seasonal labour means smart planning, good accommodation and a reliable amount of work for pickers.
Tom has a team of highly motivated assistant managers and supervisors, with regular meetings and communications.
Annual staff appraisals help develop managers and plan additional training. The size and structure of staff also enables development and progression.
Looking ahead
Regular meetings with the owners look at short-term progress and long-term plans to keep things on budget.
The future will involve further automation to keep labour costs low, alongside solutions for emerging pests.
Tom expects further adoption of organic methods in the conventional side of the business.
What the judges say:
Tom’s passion for improvement shines through a business producing top-quality fruit. He is an innovator and a motivator in a large and fast-paced system which demands a clear management structure.
Tom Deards summary
The judges liked
- Technically astute, identifies opportunities to improve efficiency
- Management manner and ability to communicate his plans
- Calm approach to managing high-risk business
- Enthusiasm for the success of the business and UK industry
- Depth of knowledge
- Honesty over challenges faced by soft fruit sector, drive to help meet them
The numbers
- 1,000t strawberries
- 350t raspberries
- 550t blackcurrants
- 250 staff
- 38 full-time staff
William Haupt
Woburn Farms, Bedfordshire
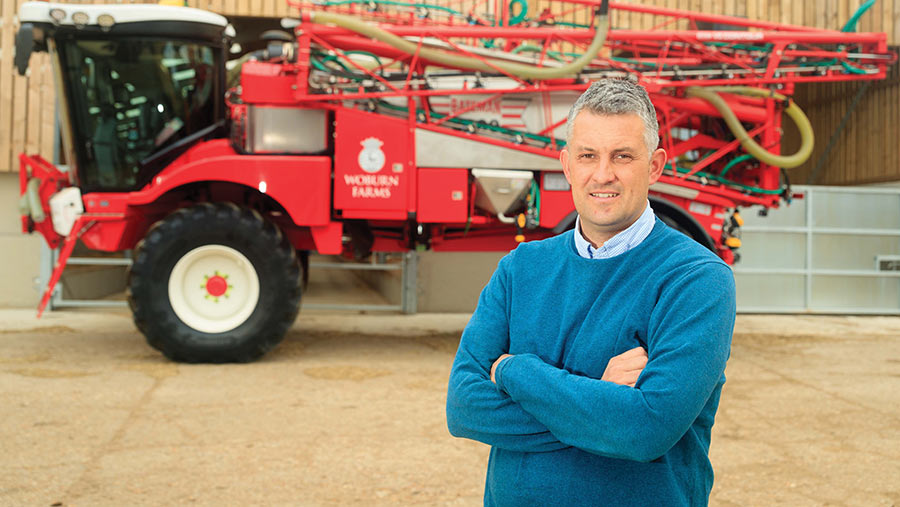
© Tim Scrivener
Farm facts
- 1,880ha in-hand (1,480ha arable, plus grassland and stewardship)
- Mainly arable plus extensive contracting and contract. farming income
- Winter and spring wheat, winter and spring barley, OSR, winter oats, spring peas, winter beans
- Pedigree Aberdeen Angus cattle
William Haupt has just completed his sixth harvest as manager of the Bedford Estates’ in-hand operation.
Farming a wide range of soil types, including sands, initial challenges included blackgrass management, rising fixed costs and lack of income outside the arable enterprise, which had a relatively narrow range of cropping.
To address this, William instigated and led a full restructure, streamlining equipment to improve timeliness and attention to detail.
This saw much of the heavy cultivation equipment sold and a move to conservation agriculture.
Expansion of contracting
He has built up contracting income from £5,000 in 2019 to £112,000 this year, while a 198ha contract farming agreement (CFA) has just been renewed for three years.
Extensive machinery investment has been accompanied by the introduction of 36m controlled traffic farming.
An in-house RTK base station now also supplies signal to neighbouring farms. The operation is paperless, with wireless data transfer and iPads.
Agronomy has been taken back in-hand with reactive support.
All major inputs are applied variably, with cropping expanded to include C1 pea seed, malting barley and milling wheat – and, this year, a three-variety spring milling wheat blend on a fixed price contract for the Wildfarmed brand.
A straw-for-muck deal has been set up with a neighbour. With the farm’s own manure, this will deliver more than 5,000t to spread this autumn.
Biosolids are used in front of oilseed rape and some first wheats, and about 400ha of rotational cover crops have been introduced.
Soil organic matter has improved by 0.1-1.3%, compared with baseline results from tests carried out in his first year.
The farm also produces all forage for the estate’s deer enterprise, including silage, and some for safari park animals.
William’s plan also included a £114,000 Mid Tier scheme, and he subsequently set up a comparable scheme on the CFA farm.
Full health screening of the cross-bred cattle in 2019 led to the sale of half the herd and a move to pedigree Aberdeen Angus.
New housing designed by William was built in 2022, also securing a grant for handling equipment.
His largest single project has been to advocate and oversee installation of a 9,000t capacity grain store, completed this summer.
It includes rooftop solar and a 40% grant-aided colour sorter to add value and earn income by processing third-party grain.
Marketing
A thorough cost of production analysis produces target grain prices.
About 30% is marketed through farmer co-op CMG and the remainder sold through other traders, fixing part of this before harvest and with local mill and processor homes in mind.
Staff retention is encouraged by investment in good machinery and accommodation, strict safety standards and a discretionary bonus scheme set up by William.
Health and safety is key, with machinery maintenance and training alongside detailed harvest and lone worker policies.
Staff involvement
William meets daily with the three full-time staff and involves them in all machinery decisions on the rolling five-year capital replacement policy.
He has set up staff training days including soil health, environment schemes and farm management strategy.
William plans to introduce or develop an assistant manager as part of his risk management strategy.
He is an adviser to Bucks YFC and also hosts farmer visits and recently took tractors to the local nursery school.
What the judges say:
William takes a very professional approach, evaluating the position of the business and seeking opportunities. He has shown leadership in his staff management over a period that has included much change.
William Haupt summary
The judges liked
- Proactive and strategic approach
- Sizeable achievements over relatively short period, and full responsibility
- Manages in a professional and diligent way
- Attention to detail to maintain very high standard of working and estate profile
The numbers
- 3 full-time staff, including manager (recruitment of further full-timer this autumn)
- 198ha arable contract farming agreement
- 440ha contracting agreement
- 60-head pedigree Aberdeen Angus