Free range egg packer develops new computer system
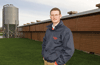
John Bowler Agriculture has spent the past two years developing its own touch-screen computer control system aimed at helping free-range egg producers manage their flocks.
As Jonathan Thompstone explains, a common complaint with many other control systems is that they are complicated and often baffling to use. “There are a lot of systems on the market, but they are difficult to use. So we decided to develop our own system.”
It replaces the old analogue fan switches and control dials, as well as bringing new functions and the ability to see at a glance vital information, such as current fan status, house temperature and energy use.
The prototype system is currently in use on a double house 6000-bird organic unit close to the company’s headquarters in Derbyshire. The system is password protected and one useful feature is the different layers of access. For example, you can give egg collectors access to view data only while managers can change settings. At the other extreme, engineers can have detailed access to calibrate systems, says Mr Thompstone.
One controller can manage several sheds and managers can stagger feeding times, so that all feeder lines don’t come on at the same time. “This saves on power use and is particularly useful when relying on generators which don’t like sudden surges in demand. It also paves the way for making the units more suitable for alternative energy sources such as wind turbines.”
The controller has a three-stage ventilation system designed for free-range sheds, says Jonathan Thompstone.
Lighting controls now come with a dawn and dusk setting, mimicking natural daylight. At the Bowler unit, lights are programmed to dim over a pre-selected length of time with the scratch area lights going off first to encourage birds to the roosting area. In the morning, the reverse happens to encourage birds to feeders and outside.
Unique to the controller is a three-stage ventilation system, specifically designed for free-range sheds. “We now have inverters fitted to fan motors so that fans can run at varying speeds. Also, this allows fans to gradually build up speed, spreading the load.
“In very old units, you can sometimes see the lights dim when the fans come on, as they are all trying to go at full speed from the start. Obviously, this means reduced power use, which is a huge bonus with continuing high energy prices. And another bonus is that you can get fresh air into the shed – for example in winter, without creating draughts.”
Phase 1 of the three-stage ventilation system is the minimal ventilation setting, where the odd numbered fans come on. Then as the temperature rises in the shed above a set point, the system goes into Phase 2 with all the fans running, but at half the speed of Phase 1. Between Phase 2 to 3, the fan speed increases according to the temperature.
But as with all ventilation equipment, things can occasionally go wrong and an alarm will notify managers by texting a message to their mobile phone. The system also has alarms for feeders and drinkers. For example, one problem sometimes seen is feed lines becoming blocked or feed bridging in the bin itself, resulting in birds missing a feed.
One feature the company is particularly proud of is the feed bin sensor. “Judging how much feed is left in a bin can be tricky with sight glasses becoming dirty and feed not being level. But with a new sensor in the bin, the system knows how much is left,” he says.
Mr Thompstone explains that the sensor works by using sound waves. “With this sensor, we believe producers will be able to accurately know when feed will run out. It’s surprising how many producers inadvertently run out of feed at weekends.”
It’s not just daily feed use that the system calculates, it also displays daily water and energy use. “Producers can use this to monitor whether one shed is consistently using more power than another. There maybe a logical reason, such as prevailing winds, but again it could point to a fault.”
And it also proves useful when changing settings seeing how it has affected energy, water and feed use, egg number, egg size and bird weight.
The next stage of the development process is to get the controller to feed all this information into the producer’s own website area. “Each producer has access to a secure web area that holds all their flock data, past and current flocks, costs, egg gradings and income. Producers can already monitor on a weekly basis the net margin and check whether each flock is on target. The new system will allow producer to access the unit from anywhere in the world using the web to check data and even amend settings should this be needed.
In conclusion, by developing this system, the company hopes to give its producers the confidence to have some time away from the flock. “Some producers feel that they are tied to their unit seven days a week, but we want to give them the confidence with this system that they can go away, with the ability to keep an eye on the flock from a distance.”
Computer controller
- Easy to use
- Allows daily monitoring of feed, water and energy use
- Remote access to house systems
- Data feeds into producer’s online financial monitoring pages