German farmers showcase biomass potential
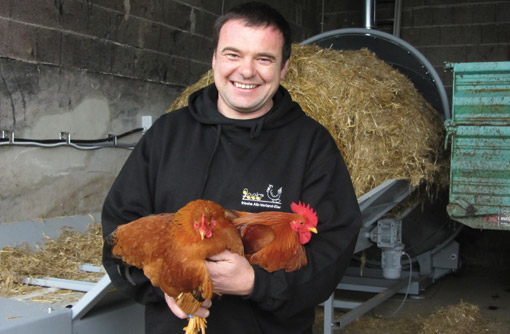
A move towards growing crops for biomass has helped secure the future of one small family farm in Hoffenheim, south-west Germany.
The Hess family moved into biomass in 2009 and currently use two boilers – 240kW and 700kW – to supply heat to more than 100 houses in their local village as part of a district heating system.
The heating business – BioEnergie Hoffenheim – offers clients a package that includes a heat exchanger, which is installed on their existing boiler, and 5m of piping from the heating mainline. Any necessary extra pipework comes at an additional cost.
The system is fuelled by 70-80% miscanthus, with woodchip making up the remainder. About 30-35ha of the crop is grown on the farm, yielding at 20-22t/ha. The miscanthus is freeze-dried before use as a fuel in the boilers.
During the summer months, when the heat demand is less, the smaller boiler is used, and in the winter months when heat demand is greater both boilers are brought into service.
Markus Hess’ system is fuelled by miscanthus and woodchip.
Farmer Markus Hess, who runs the business in conjunction with his brother and mother, says: “We sell it all in a package and the cost is about €5,000 (ÂŁ4,300). We sell the heat at 7.5c/kWh, which is 25-30% cheaper than heating oil. Customers pay every month and they get a summary invoice at the end of the year.”
Heating oil costs approximately 12c/kWh, while gas costs between 7-8p/kWh.
The system includes a 32,000-litre buffer tank and overall plans involve nearly 12km of pipework to pump hot water to houses in the village. Water goes out of the system at 80C and comes back in at 60C on a continuous cycle.
Due to the success of the scheme, the family is constructing a second heating unit to house a 800kW boiler, with the view of heating a further 300 homes and a school.
Straw
Egg producer Frank Zeeb is using a custom-made straw bale shredder to produce fuel for biomass and bedding for 13,000 layers.
Mr Zeeb has installed a 120kW Okotherm boiler on his farm in Reutlingen, south-west Germany.
The boiler will heat two houses, a farm shop, three flats and a grain dryer. And in the future Mr Zeeb plans to use the boiler to heat a nursery unit for chicks up to 20 weeks old.
Shredding
The custom-made shredder allows Mr Zeeb to load bales on to the conveyor belt, which then pulls them forward and shreds them – sending some of the end product direct to the boiler fuel-store, with the remainder piled to be used in bedding in the layer units.
“It will hopefully save on labour, because [the bedding] will need changed less,” says Mr Zeeb.
In terms of straw use, one-two bales are needed every day with 70% chopped for the boiler and 30% used as poultry bedding and then manure afterwards.
The system cost €100,00 (ÂŁ87,000) plus VAT, and Mr Zeeb estimates the payback period will be seven years. “I hope to save about €20,000 (ÂŁ17,000) in heating costs a year,” he says.
“I want the straw cut really short because if I have long straw in my chicken shed, they don’t work it too much,” says Mr Zeeb.
“The welfare and health of the chickens will improve because the bedding will be better and the manure will be dry; the chickens will work it around and it will not be wet and horrible.”
In the future, there is the option to install an additional boiler – the boiler room has been designed to allow for future expansion – and sell heat to neighbours in the village, he says.
Bringing the German concept to the UK |
---|
In a bid to replicate what the Germans are doing with biomass, miscanthus is successfully being used in a small-scale district heating system in the UK. International Energy Crops (IEC), which is the sole UK supplier of Okotherm boilers, has a 198kW biomass boiler in place at its farm in Market Drayton, Shropshire. The system is used to heat the farmhouse, two cottages, office space and three workshops – 60kW of capacity is unused, offering potential to meet further heating demand in the future. The system features a 160cu m capacity underground fuel store complete with a 5,000-litre buffer tank. IEC managing director Keith Wilson says the total project cost, including all civil works, was £160,000 with an estimated payback of five-and-a-half years including fossil fuel savings. The system is set to save £9,000 in fossil fuel costs a year, while receiving an RHI income of £24,500 per annum. RHI payments are administered in two tiers – 8.2p/kWh for tier one and 2.1p/kWh for tier two. Miscanthus is costed at £4,000 a year based on using 100t priced at £40/t because it is grown on the farm. Mr Wilson says: “We think miscanthus is a long-term fuel. The RHI is for 20 years and we think it’s important to have a boiler that lasts 20 years.” Germany is a prime example of a country using miscanthus to its full fuel potential – of the 3,000ha of the crop grown each year, 99% is used for heat, he says. Mr Wilson says this type of system best suits producers who want to grow their own miscanthus, as they can fix their growing costs at £40/t for the next 20 years. “The alternative is woodchips at £85/t and the price is rising,” he says. |
Read more articles about renewables on our Farm Energy page.