Farmers Weekly Awards 2020: Contractor of the Year
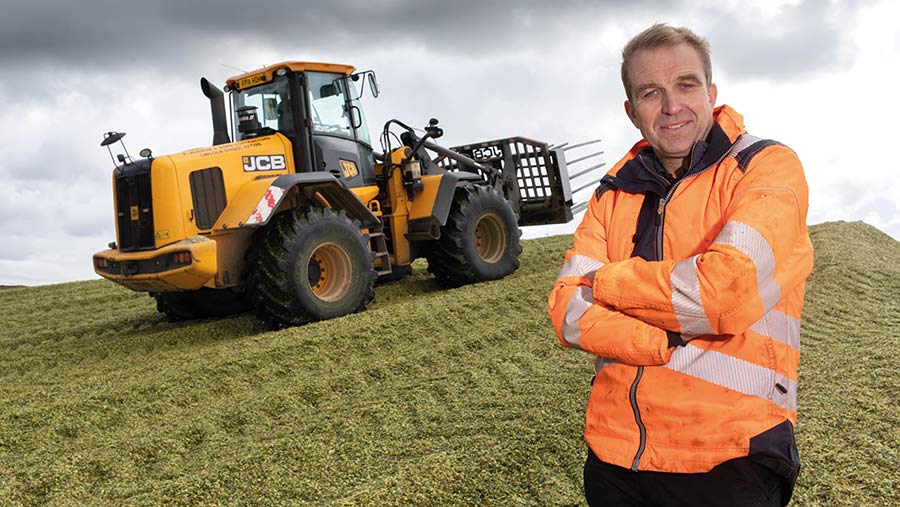
P Russon & Sons, New Farm, Burton, Lincoln, Lincolnshire
Organisation and planning are at the heart of the vast contracting outfit built by Tim Russon, whose office-based role allows him the time to manage the head-spinning logistics of a barn-load of kit and up to 30 staff at peak times.
His no-nonsense approach to pricing and payments, sharpened through his experience in the cut-throat industrial waste sector, has helped to tune his operation to run at maximum efficiency for the benefit of both the business and his customers.
Farm facts
- 32 years in agricultural contracting
- Services offered: Forage and miscanthus harvesting, drilling, grain maize combining, baling, muckspreading and digestate application
- Main customer base: Anaerobic digester plants and livestock farmers
- Area covered: Lincolnshire, Nottinghamshire, Yorkshire, Norfolk and Cambridgeshire
- Staff: 12 full-time, up to 30 during seasonal peaks
Like many budding contractors, Tim started the business as a bolt-on to the family’s dairy farm, but it quickly snowballed, as maize drilling led to harvesting and complete forage services.
His “work smarter, not harder” mantra meant he stopped driving regularly 15 years ago, instead using his time to manage a growing army of staff and machinery.
This shift has given him more time to plan jobs, manage his dozens of cost-tracking spreadsheets and promote the business to new and existing customers.
He aims to work several days ahead, organising chemical, diesel and spare parts deliveries and devising rainy-day alternatives to keep the staff busy when the weather scuppers plans.
Machinery
Tim takes a matter-of-fact approach to machinery purchases based on how much money they cost and how much they can earn. Years of diligent data recording have built a vast bank of information that details precise running costs for different tasks and the associated machinery depreciation.
New tractors are taken with extended warranties to avoid expensive and time-consuming layoffs. Most are run to 6,500 hours but, as purchase prices rise, he expects to extend this to squeeze maximum value from his investments.
That means the two on-site workshops will have a bigger role to play. They’re already impeccably organised and fully stocked, with crates of spares shunted around to make them accessible while the kit is running.
Staff
Managing up to 30 seasonal staff is no mean feat, so the business uses a clocking-in machine to track who is at work, and JCB’s Livelink telematics system to monitor machine whereabouts and usage, providing vital insights into fuel consumption and idle times that can be used to improve efficiency.
Staff are armed with daily checklists for equipment, which means any defects are recorded and problems fixed. They’re also given annual appraisals, continually assessed to make sure they are working to their full potential, and encouraged to discuss any issues they have with their role in the team.
Although it has its complexities, running such a big team with a range of skills provides the flexibility to allow time off during busy periods, and Tim is acutely aware of the risk of burnout, so often restricts team members to 14-hour days.
His work across a broad range of safety-scrutinised sectors has also given him a laser focus on health and safety. Participating in the Assured Land-based Contractors scheme necessitates the business to work within the parameters set out by the Health and Safety Executive, keep training records and complete risk assessments for all types of work.
He also expects customers to contribute with accurate site maps, including details of overhead power lines and other hazards.
Winning ways
- Well-planned workflow with back-up alternatives to keep staff busy during poor weather
- Balanced fleet with machines to suit specific jobs
- Impeccably calculated costs ensure jobs are profitable
- Organised staff management and structured training plan
- Broad range of non-ag services fits well with agricultural business
A word from our independent judge
Tim’s efficiency, drive and ambition means his big and successful business continues to evolve. Fastidious planning, meticulous costings and a professional approach to management have all helped to maintain his stellar reputation.”
Jill Hewitt, NAAC chief executive
Other finalists were
- M Metcalfe & Sons
Silver Hill Farm, Tunstall, Richmond, North Yorkshire - Tom Dirom Agricultural Contractors
Pool in Wharfedale, Otley, Yorkshire
The Farmers Weekly 2020 Contractor of the Year is sponsored by Tama UK
Tama UK specialise in providing total crop baling solutions and are focused on meeting the specific needs of the customer. Tama is a leading manufacturer of twine and netwrap, working together with the main baling machinery manufacturers. These partnerships result in the highest quality products, specifically tailored to suit all crop baling equipment.
Tama offers an unrivalled level of customer support, technical expertise and distribution excellence, together with products approved and recommended by leading machinery manufacturers such as CLAAS, CNH, Fendt, John Deere, Massey Ferguson, Kubota and SDF.