Farmers Weekly Awards: Pig Farmer finalists 2020
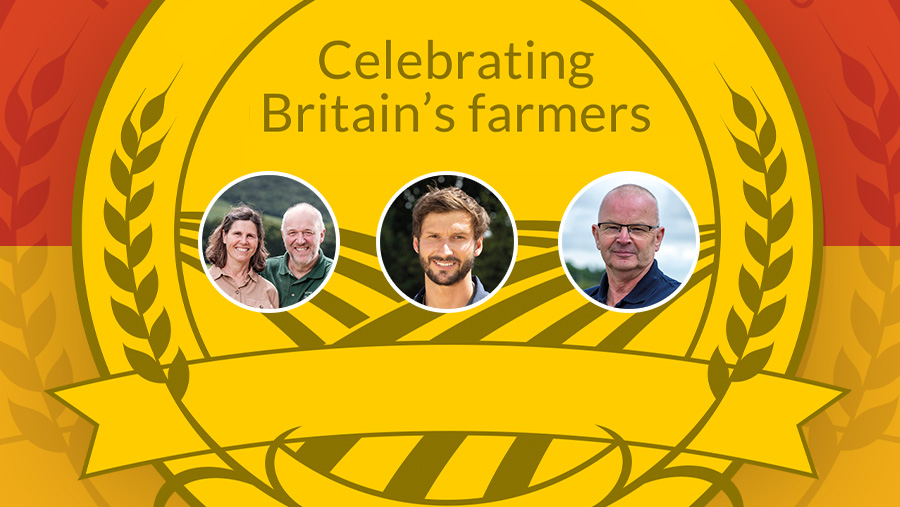
Fine-tuning performance by paying attention to detail in all aspects of management was key to maximising production across all the Pig Farmer of the Year finalists’ farms this year, with technology, good recording-keeping, tight biosecurity and cleaning regimes essential to meeting top targets.
The 2020 Pig Farmer of the Year finalists
- Colin Stone
Wayland Farms, Thetford, Norfolk - Charlie Thompson
Bridge House Farm, Long Buckby, Northamptonshire - Stephen and Karen Thompson
Povey Farm, Sheffield, Derbyshire
The judges
- Michael and Ian Baker
Last year’s winners - Zoe Davies
Chief executive of the National Pig Association - Sarah Alderton
Former Farmers Weekly livestock editor.
See also:Â Farmers Weekly Awards 2019: Pig Farmer of the Year
Colin Stone
Wayland Farms, Thetford, Norfolk
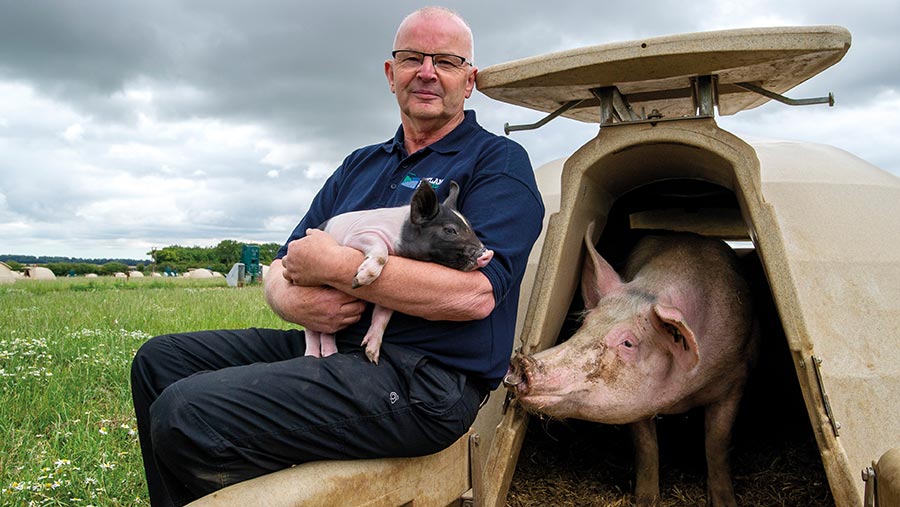
Colin Stone © Jason Bye
Wayland Farms certainly have outdoor pig production down to a fine art. As one of the largest producers of outdoor-reared pigs in the UK, it has performance that can match that of some of the best indoor-finishing herds.
The farm has a herd of 20,000 high-health breeding sows and gilts and works closely with Rattlerow Farms to continue pushing forward genetic advances. It has dedicated gilt-mating units that ensures all replacement gilts come from the same source, which aids herd health.
Six years ago, the business was acquired by Cranswick. The pork produced on the farm supplies the premium pork retail market, with much of it heading into the Tesco Finest range.
All pigs are finished on straw on farms owned by Wayland, as well as some contract finisher farms. In total, there are more than 80 sites containing pigs from breeding through to finishing.
Herd performance
When it comes to performance on an outdoor pig unit, it does not get much better than some of the figures seen at Wayland Farms, with their best outdoor breeding units achieving 28.18 pigs weaned a sow a year.
Over the past four years the farm has seen born alive figures increase from 11.73 to 12.65 and numbers sold grow from 24.84 to 26.91, partly due to using more uniform genetics. Pre-weaning mortality has also dropped to 7.3%.
Some of the improvement can be attributed to investments in sow huts, having moved to the Aardvark hut, which is fully insulated and better for welfare.
Staff management also goes a long way to producing such good figures. Wayland Farms employs 100 staff, with a strong core team of managers. Each team has budgeted figures and targets they must work towards and are paid a quarterly bonus based on performance targets.
Everyone in the business has an annual appraisal, with all managers involved in weekly meetings. There is a strong emphasis on training too.
Finished pigs are reared on straw with average daily gains of 905gm/day and 4% mortality. They are fed a three-stage, low-protein diet. By reducing the crude protein, the farm has been able to cut nitrogen excretion by 10%.
Technology
This farming enterprise is keen to use technology, with an investment in a 1,000-space finishing trial farm, where it carries out environmental research and development trials on feed, water and genetics.
It has invested in an agri-tech start-up company looking at a pen-side diagnostic test which could produce results for routine disease surveillance within just 40 minutes.
It has also been trialling the use of coconut oil in weaner diets to see if it can improve intestine microflora and work as an immunosuppressant.
Staff in the field use digital tablets to record performance, animal health and audit compliance. This allows managers to monitor trends and identify areas for improvement.
They also use digital surface water runoff and ground water mapping to appraise new fields when moving breeding units or establishing new ones.
The environment
Wayland Farms is keen to preserve and protect the environment and it works closely with Norfolk Rivers Trust to protect natural resources.
It has also conducted two carbon assessments – one in 2017 and one in 2019 – and has seen its carbon footprint drop from 3.14kg of carbon equivalent per kilo of liveweight pig produced (carbon dioxide/kg LW) to 1.63kg carbon dioxide/kg LW, mainly by using certified soya, as well as improved performance. Wayland Farms’ emissions are almost half that of the Alltech average of 3.34kg carbon dioxide/kg LW. Â
The operation has also started soil testing the land before a breeding unit is established and when it is removed after two years. A supply chain programme is currently being scoped out with Natural England to look at this in more detail and assess the possible benefits of pigs to soil health.
Some 80% of Wayland Farms’ breeding units incorporate a 6m pollen and nectar mix around the headlands. In 2018, the farm became a member of Linking Environment and Farming.
What the judges say
“As one of the largest, outdoor-reared pig producing companies in the UK, the performance across this business is exceptional, with attention to detail by staff paramount. The team is always looking at the latest developments and some of the work they are doing around pen-side diagnostic testing could be revolutionary.”
Summary
What the judges liked
• Excellent performance for an outdoor unit
• High health status
• Investing in research to develop new technologies
• Good staff training
• Working with the environment
Farm facts
• 20,000 breeding sows
• 500ha, with more than 300ha rented
• Owned by Cranswick
• Pigs supply Tesco premium pork range
• Employs 100 staff •Own feed mill and livestock haulage
Figures
• 28.18 pigs weaned a sow a year
• 12.65 number of piglets born alive a litter
• 75% self-sufficiency in feed and livestock haulage
• 6m pollen and nectar barrier established around headlands
Charlie Thompson
Bridge House Farm, Long Buckby, Northamptonshire
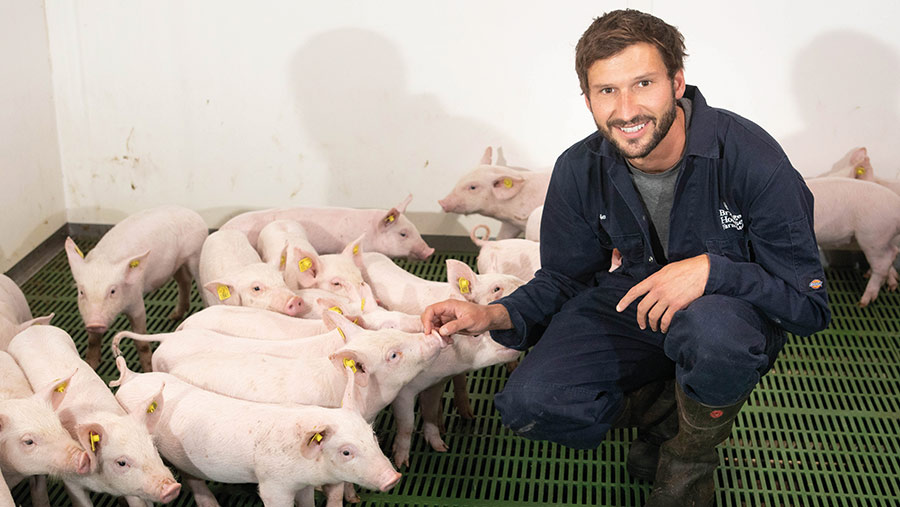
Charlie Thompson © Tim Scrivener
Data is fundamental on this high-health 650- sow breeding nucleus unit with every piglet individually monitored on its growing performance from the minute it is born using EID and ultra-high frequency tags (UHF tags)- one of the first farms in the world to do this.
Technology
Charlie has worked hard to adapt the electronic identification (EID) technology to suit his system, with everything from individual birthweights, litter performance, weaning weights, intramuscular fat as well as conformation traits measured and recorded on touchscreen tablets.
Running a purebred herd supplying breeding stock for Genesus Genetics, Charlie is breeding Yorkshire pigs for the damline and Duroc’s for the sireline. This makes accurate data vital, with all the information shared with Genesus Genetics so that continual genetic improvements can be made.
The introduction of EID has made life so much easier. Before EID, it used to take three hours to record weaning weights of 300 piglets with four members of staff. Now two members of staff can take the weights in less than two hours. Furthermore, it has improved accuracy to 100%.
Using UHF tags means they can be read in batches and from a distance. Charlie has installed fixed EID readers in the corridors, which means individual pig and group movements can be tracked between each stage of production.
Bulk reading of pigs has proved useful recently when Charlie exported his first batch of 700 pigs to Genesus Farms in China.
But the technology does not stop there. Charlie also invested in a phase-feeding system, which allows a tailored diet for each pen of pigs with pigs fed on a curve depending on their sex and breed.
Charlie estimates this is saving him about 5p a gilt a day, which over a year equates to ÂŁ35,000 across 2,000 gilt places.
Herd performance
Because diets are gradually changed, there is never a growth check or stomach upsets. It is also thought a combination of consistent feeding and genetics – with Durocs renowned for being extremely placid – is contributing to massively reducing tail biting. This means tails are not docked on this unit.
Much of the system is fully slatted, but Charlie is doing all he can to enhance the environment. He has established a relationship with a bowling ball company and uses bowling balls as enrichment. He is also trialling lots of other enrichment toys.
Bridge House Farm has been a nucleus breeding unit since 1987 but, in 2017, following a depopulation of the PIC herd, it decided to restock with Genesus genetics due to the performance of the pigs and the simplicity of the breeding.
Charlie says: “We liked the simplicity, with them only having two breeds: the Yorkshire and the Duroc. We were also blown away by the growth rates and productivity.”
The future
Exporting to China is something Charlie hopes to continue doing. He has built two 650-place quarantine units on the farm by converting two poultry sheds. He would also like to set up a secondary nucleus unit on a separate farm so he can divest some of the risk should the unit get a disease breakdown.
The plan is to increase sow numbers to 950 quite quickly to keep up with the demand. He also plans to continue developing the team of staff by putting them through training and making life easier by using technology.
What the judges say
“Charlie is young and enthusiastic, with a passion for technology. The amount of data he collects and uses means he can fine-tune his system to ensure pig welfare and performance can be optimised.”
Summary
What the judges liked
• Excellent use of technology to inform decisions
• Top production efficiency
• High welfare in an indoor unit
• Looks for new market opportunities
• Works proactively with Genesus to market stock
Farm facts
• 650-sow nucleus breeding unit
• Every pig weighed at birth, EID tagged and performance recorded throughout their life
• Breeding stock – boars and gilts sold across the UK, Europe and further afield, including China
• Pigs not sold for breeding are finished at 120kg
• Contract farm 1,000ha (2,500 acres) of arable
Figures
• 1.4kg Daily growth rate in the Durocs
• 2.05:1 Feed conversion in pigs from 50-105kg
• 17.02 Number born alive a litter in the Yorkshire damline
• 35.23 Number of pigs weaned a sow a year
• £40/t Amount saved per tonne in the finisher diet as less lysine being fed
• 4.4mg/kg Antibiotics use
Stephen and Karen Thompson
Povey Farm, Sheffield, Derbyshire
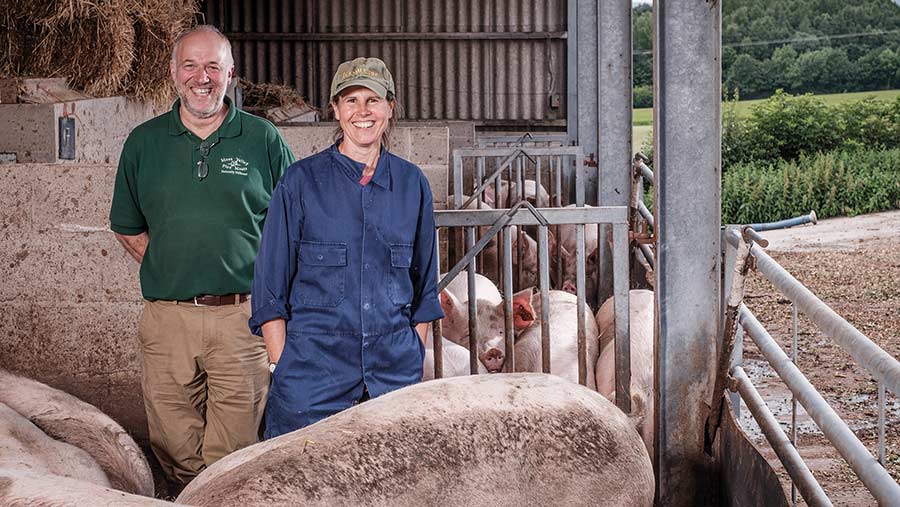
Stephen and Karen Thompson © Jim Varney
The high health status of this traditional farrow-to-finish unit is phenomenal.
The Thompsons’ attention to detail is one of the main factors that sees this farm record one of the lowest levels of antibiotics use for pig farms in the UK at about 1mg/kg.
Pigs are housed in a mix of old buildings dating back to the ninth century and newer, modern buildings, which can be easily cleaned between batches. It is testament to the Thompsons’ astute attention that such high health can be achieved without state-of-the-art technology and all new buildings. Â Â
Health
The family believe one of the main drivers for maximising herd health has been the switch to batch farrowing. Implemented several years ago, this has resulted in a big improvement in the way pigs are managed, as it allows separation of age groups and aids disease control, so older pigs cannot infect younger pigs.
Sizing the pigs and splitting sexes has allowed them to improve welfare and encourage even growth.
Additional management strategies which aid pig health includes operating a completely closed herd, water acidification, strict visitor protocols, use of non-steroidal anti-inflammatories as a first line of treatment, investment in new buildings that can be easily cleaned, temperature control and exceptional nutrition. Routine vaccination is also part of the farm’s armoury to reduce disease challenge and antibiotics use.
Herd performance
The performance of this herd has also been motoring ahead, with the switch from a damline Duroc to a Danish Duroc having a big effect on growth and finishing times.
Not only have they been able to grow the pigs heavier, they have also been able to shave at least one week off the finishing times, with pigs killed at about 88kg deadweight.
The switch has increased the daily liveweight gain from 761g to 830g and has reduced weaning to slaughter days from 131.2 days to 127.6.Â
Future-proofing
This farm is also at the top of its game when it comes to sustainability, with investments in two wind turbines, a straw burner, solar panels and a water borehole.
To top that, the family are also trying to make the business more sustainable by removing some of the market pressures. To do this they are directing 25% of their produce into their own butchery business, Moss Valley Fine Meats.
This has grown from strength to strength since its establishment in 2007, increasing from one pig going through the butchery each week to 15. The rest of the pigs are sold to a major processor. Â
The farm is supplying more than 50 local establishments and has recently expanded the butchery so it can start cooking hams and other products. Before Covid-19, the Thompsons were also in discussion with Morrisons about supplying five local stores in Sheffield with their sausages. They have turned the pressures of the pandemic into a positive by working with a local taxi firm, City Cabs, to deliver food locally. In the first two days of lockdown they sold ÂŁ1,200 worth of sausages and hams.
They are also massive advocates of vet students. They have about 30 students on the farm each year. Passionate to showcase a positive image of the British pig industry, they are also part of Just Farmers, a communications project connecting farmers with the media.
What the judges say
“The Thompsons strive to be the best at what they do, and this shows in their excellent performance and pig health. They are also continuing to look at new ways to market their produce and make their business as sustainable as possible.”
Summary
What the judges liked
• Excellent herd health
• Focus on data and monitoring changes, such as the switch in genetics
• Carbon neutral in many aspects of the business, with investments in several green energy sources
• Increasing the butchery side of the business and improving business sustainability
• Established new outlets for their meat, including a possible contract with Morrisons
Farm facts
• 210 sows
• Farrow-to-finish unit
• 25% of pigs sold through their own butchery business
• 85kW and 15kW wine turbine, as well as a straw burner and 4kW of solar PV.
• Woodchip soldÂ
Figures
• 13.3 Weaned pigs per litter
• 830g Daily liveweight gain
• 127.6 Number of days from weaning to slaughter
• 2.18 Food conversion ratio
• 50 The number of local establishments the Thompsons are supplying with their meat
Sponsors message
“When demands for pork increased, UK pig farmers rose to the challenge to continue feeding the nation. NSF are proud to have kept our farmers assured, keeping the supply chain moving.”
Anita Roberts, director agriculture, EMEA