How a Yorkshire herd lifted litres and cut labour with robots
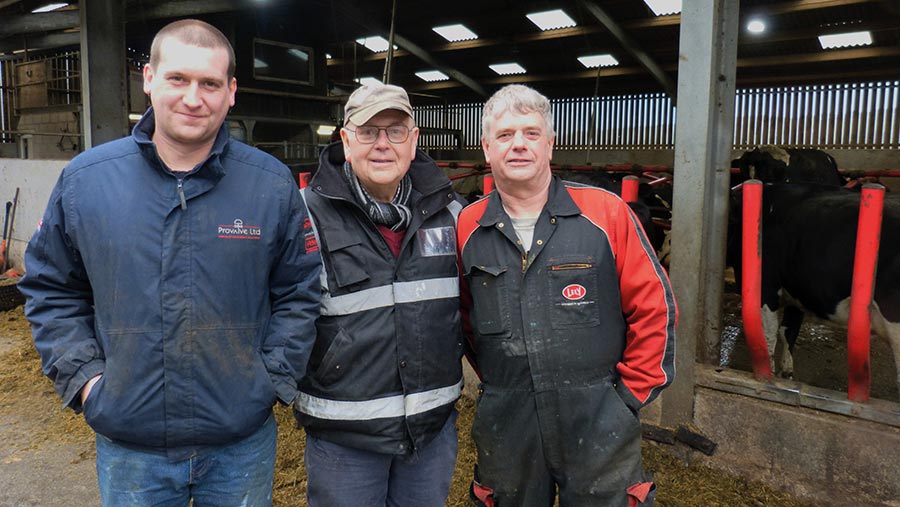
A 40% increase in milk yield and more time off each week have convinced a former milk-bottling dairy that investing in commercial farming has been the right decision.
The Wheelwrights now supply Dales Dairies after 108 years of bottling and retailing their own milk, produced at Scar Hill Farm near Halifax.
Like other farms in the area, the Wheelwrights capitalised on the urban population nearby, selling into Halifax and Huddersfield.
They sold 2,000 litres a day six days a week, which left very little spare time for rest and holidays.
See also: How Staffs dairy gets high robot visits with low cake costs
“We were tired out and ready for a change. It was more like a factory job, and we are farmers who enjoy cows and tractors,” explains Richard Wheelwright.
He has relished the challenge of increasing herd performance to claw back some of the margin lost from losing the milk round.
The business still involves the family. Richard farms with son Simon, and father Edward, who rears the calves, with the help of cousin David, who is a cow man. But the labour can now focus on farming and herd efficiency.
Farm facts: W Wheelwright and Sons
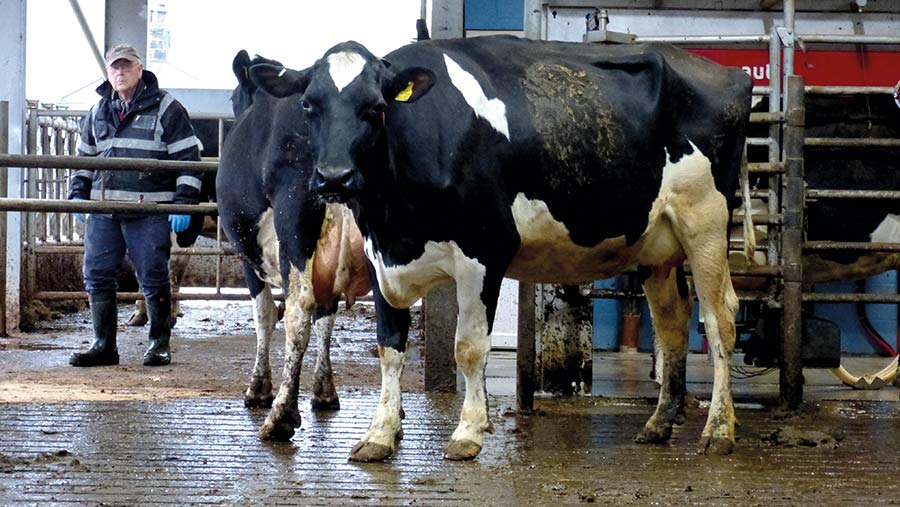
© MAG/Michael Priestley
- Milking 90 Holstein-Friesians and Friesians
- All-year-round calving, zero-grazing system
- 120ha (300 acres) on two 60ha (150-acre) sites
- 4.29% butterfat and 3.3% protein on winter ration
- Yielding upwards of 9,500 litres
- 405-day calving interval
- Supplying Dales Dairies on a liquid contract
Change of system
The Wheelwrights historically ran a “grass and cake” system, grazing 70 robust Friesian cows and averaging 7,500 litres a cow in an antiquated shed and an outdated parlour.
Now, the cows are housed 24/7, fed parlour cake through two Lely robots, and fresh grass through a zero-grazer trailer. Yield has been lifted to more than 9,000 litres and herd size is at 90 cows.
The farm has been breeding a more Holstein-Friesian-type cow. The first Holsteins are second calvers this year, which will also help lift yields long term, says Richard, who is eyeing 36-37 litres a cow a day.
Timeline of system change at Scar Hill Farm
- 2017: Building contractors levelled ground and started erecting 67mx17m shed on a grass field at the bottom of the farmyard. This was paid for with savings.
- 2018: The Wheelwrights kitted the shed out themselves to save on costs, with three tip troughs, cubicles, Jupiter F mats and slurry tanks under slats around the robots and near the 5.4m feed passage.
- 2019: A new slurry tank was added, and the first Lely Astronaut installed. The freshest half of the herd was moved onto the robot to maximise yields, as were 25 30-litre Holstein heifers, bought from Gisburn to lift output. The old 5:10 parlour milked the other half of the herd while the business saved for a second robot.
- 2022: By October 2022 the other half of the robot shed was completed and the second robot installed. The pair of robots cost close to £200,000, compared with conventional parlours at the time for £60,000-£80,000.
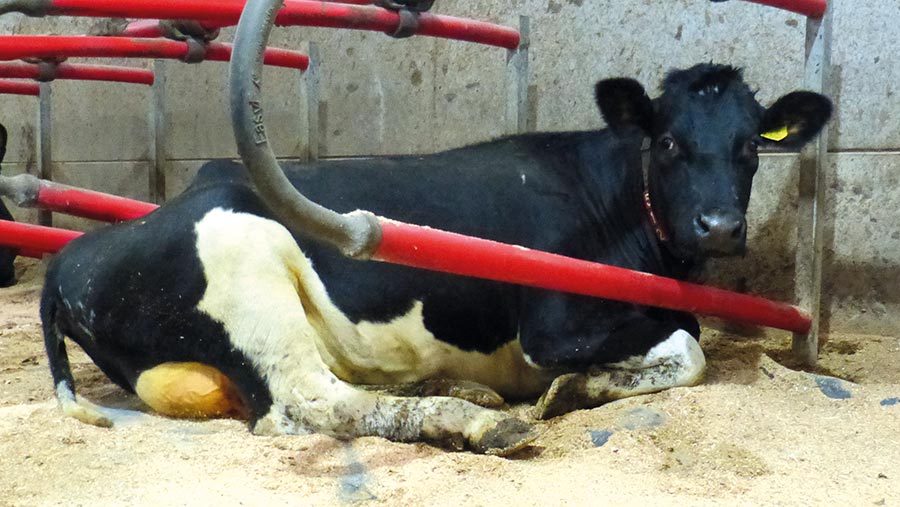
© MAG/Michael Priestley
Benefits
Average daily yield has lifted from 24 litres a day to 34 litres through the robots.
The Wheelwrights put this mainly down to a new shed, greater cow comfort, more frequent milking through the robots (3.3 times a day on average) and silage quality.
“This system lets the cows do their own thing,” explains Edward. “They can choose to be milked, fed and lie down, and that’s keeping them content.”
How the system works
Zero-grazing
- A zero-grazer trailer takes grass at 16cm and leaves a residual of at least 7cm.
- The trailer goes out an average 1.5 times a day through the growing season. Grass is cut at the home farm and the other 60ha (148-acre) block three miles away.
- This saves £5,000-£10,000 on a third cut from the contractors and allows herd expansion without building a second silage pit.
- The first zero grazer trailer cost £16,000 second-hand, and was traded in for £10,000 to buy a new £38,000 trailer.
- Supplementary fibre (chopped straw, wholecrop, hay or silage) is essential, particularly for slowing down the rumen when cows are on spring grass.
- About 7kg (freshweight) of brewers’ grains is being mixed in the silage this winter. Silage is taken with a shear grab and mixed on the pit floor before feeding.
- About 45% of milk is from forage.
Robotic feeding
- Good-quality, fresh grass through the year and better silage – achieved by reseeding 8ha (20 acres) of the farm each year since 2019 – gives a feed rate of 0.26kg/litre, which lifted to 0.28kg this winter. Parlour cake cost about 11p/litre in January, at £385/t.
- Two 12t bins are used to feed a 21% protein cake in winter and a 14% protein cake when zero-grazing.
- Silage is giving maintenance plus 12-13 litres. On fresh spring grass this lifts to maintenance plus 19-21 litres.
Labour savings
- Robotic milking saves six hours a day spent milking through the old parlour.
- A Lely software package called Horizon simplifies breeding choices and management by looking at live herd performance data on an app and in the farm office.
- Sick animals are highlighted and can be diverted from the robot to the hospital pen.
- Bulling animals can be diverted to the back pen from the robot when in heat. Richard managed this from the Horizon app while shopping in Leeds recently.
- Breeding decisions are assisted by a cow index on the app, which rates cows on production, health, reproduction, and robot efficiency, with the bottom percentile put to the farm’s Limousin stock bull.