How a leading pullet rearer keeps birds salmonella-free
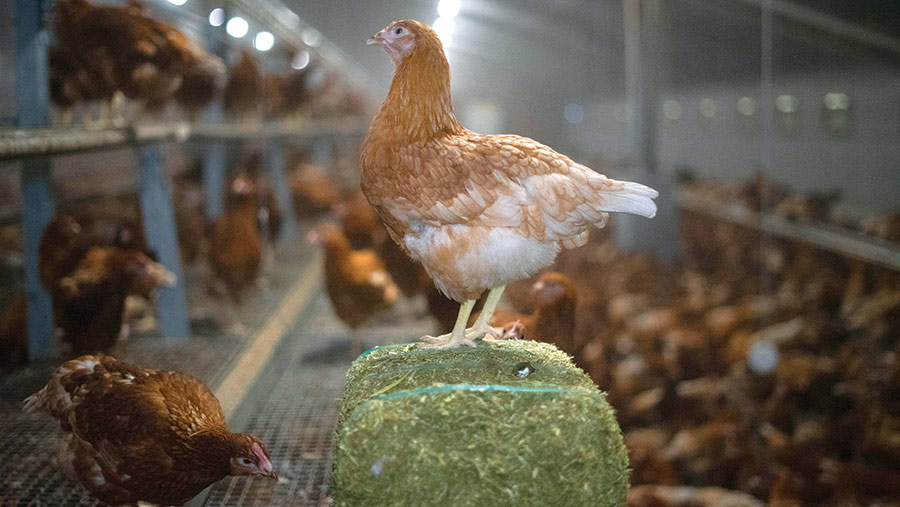
UK producers are world leaders in keeping salmonella derived from eggs out of the human food chain, thanks to stringent control measures carried out by the entire poultry sector.
At Country Fresh Pullets, the vaccination regime to protect birds from contracting the bacteria, begins when chicks are a day-old.
See also: A poultry producer’s guide to red mite control
How the vaccination programme is carried out
The company uses Avipro Salmonella Duo [from Elanco] because it covers both Salmonella enteritidis and Salmonella typhimurium.
The vaccine is delivered through water lines in three doses over the rearing cycle and mimics how a bird would get salmonella in the wild.
After being consumed by the bird, it causes mucosal immunity to be generated in the gut.
With the salmonella inoculations included, the company’s vaccination programme comprises at least 19 treatments over 16 weeks, meaning it’s critical to get things right.
It’s not only crucial for bird health, but the cost of vaccinations now accounts for about 50p of the pullet’s total price to farmers (about £4.10) at point-of-lay.
As a result, Country Fresh Pullets has worked with specialist Rosehill to set up its farms to be “vaccination friendly”.
Staff should be trained regularly in good vaccine management, and sites should be audited by a competent professional at least once a year.
There are four key ways this is achieved:
1. Storage
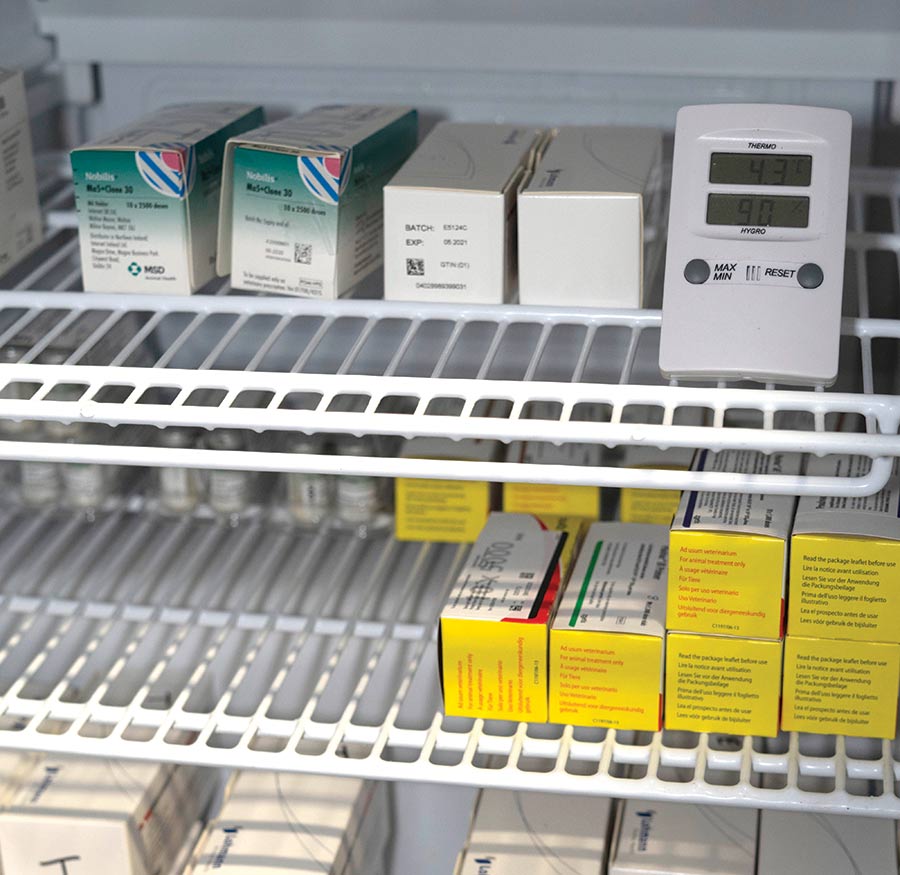
Keep vaccines in a commercial-spec fridge
Live vaccines must be kept at the correct temperature to be effective, according to Rosehill’s Dave Hodson.
As part of his role in supplying vaccine, he will recommend equipment to keep them at their best.
On farm, a commercial-spec fridge is a must. Look for a model that has fans to distribute temperature evenly with metal grille shelving rather than glass, to allow for airflow.
Check the rated accuracy of the fridge, and back-up the in-built temperature gauge with a separate thermometer that can log temperatures, so if there is a failure it can be picked up early on.
A record of the serial numbers of vaccines used must be carefully taken for batch traceability.
Before beginning treatment, confirm that the vaccines are the correct type and within their expiry date.
2. Equipment

Ensure equipment is clearly labelled and only used for vaccine use
Before beginning to mix a vaccine, consider the area in which you are working. It should be clean, clear of debris and washed down with warm water, says Mr Hodson.
Use dedicated equipment for mixing water-soluble vaccines – and label it clearly as for vaccine use only.
Any contamination in buckets or mixers that have been used for other tasks may well cause the vaccine to fail.
Likewise, nitrile gloves will protect the product from oils present on your skin.
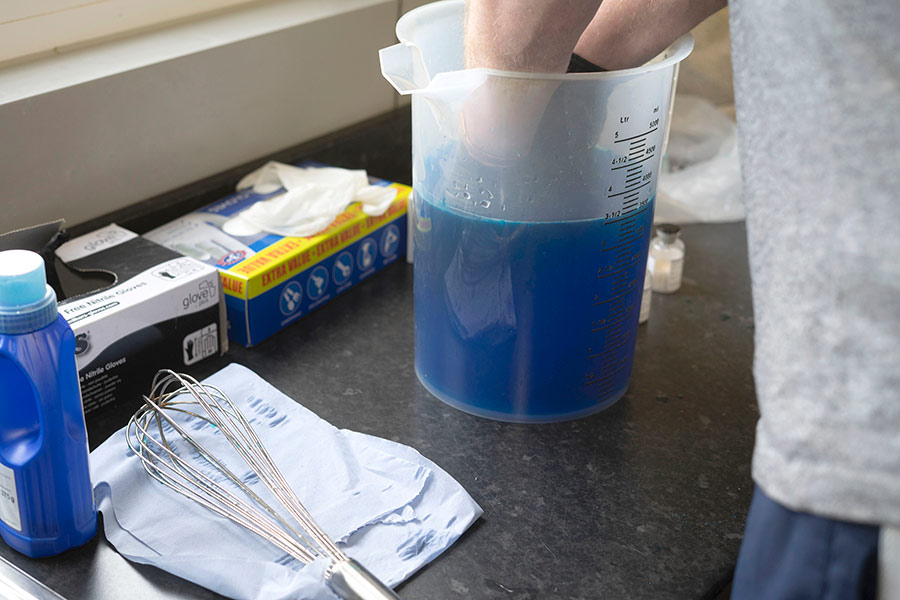
Open vaccine vials under water to prevent them from degrading
Before vaccines are added to water, it’s essential to add a stabiliser, such as Aviblue, which buffers the effects of hard water and chlorine residues.
The water colour is also changed, making it easier to see when the vaccine has reached the end of the water lines.
Open glass vials under the surface of the water as contact with air can cause the vaccine to degrade.
3. Delivery and monitoring
It’s essential to overestimate the amount of vaccine required, says Mr Hodson, to ensure that every bird receives a dose.
Birds also need to be thirsty for an effective uptake of vaccination, so water lines need to be lifted – about three hours before treatment is optimal, he suggests.
Once mixed, the lines will often need to be flushed.
Most farms will use a Dosatron machine, and their calibration should be checked before vaccination begins.
Prime the lines by draining the system until the blue-dyed water containing vaccine becomes clear.
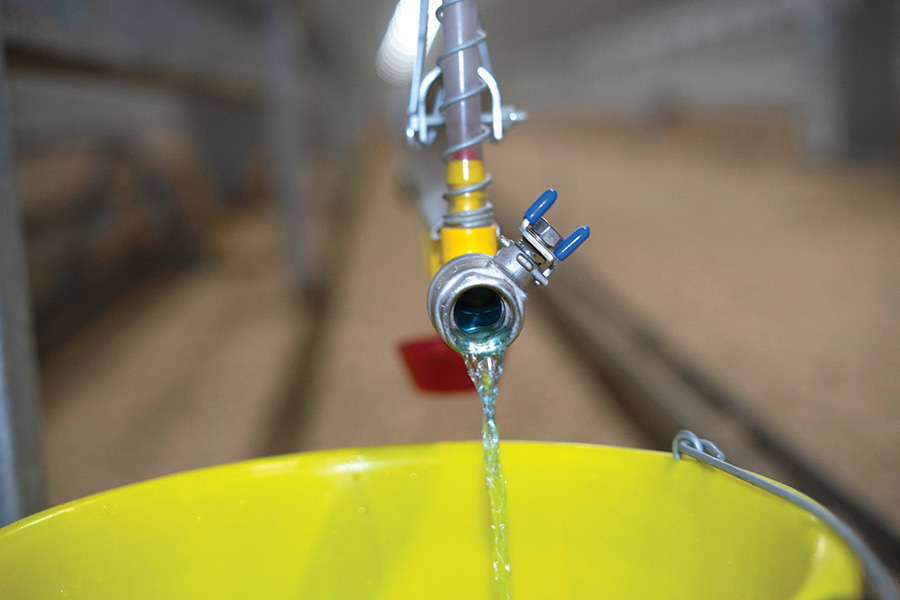
Blue liquid indicates that vaccinated water has reached the end of the drinkers
Country Fresh Pullets has opted to keep manual flushing systems, despite automatic equipment becoming available in recent years.
The reason, according to area manager Ben Hartley, is that there is no need to worry about the calibration of systems, and less risk that valuable vaccine will be wasted.
Farms in the Country Fresh Pullets estate have been fitted with drains at gable ends, making it easy to empty buckets while priming lines without leaving the shed.
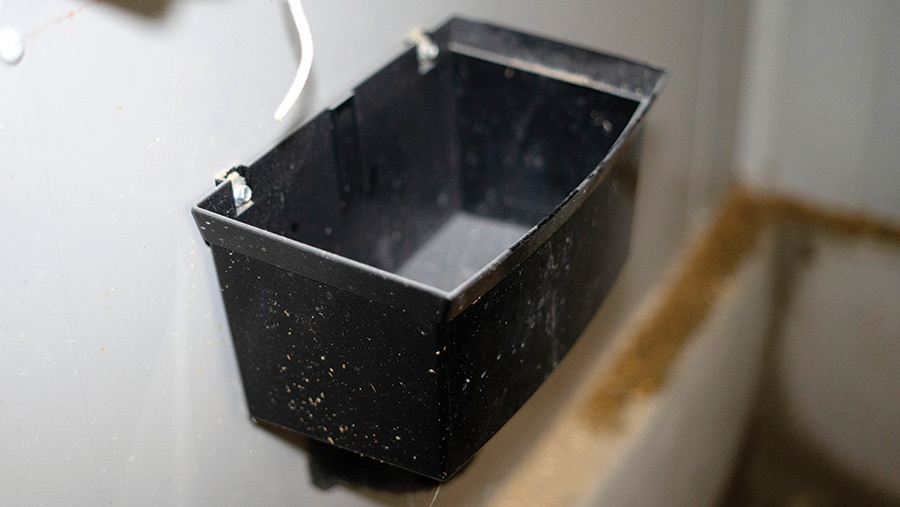
Country Fresh Pullets has installed drainage at the end of sheds to make flushing water lines easier
4. Biosecurity and pest control
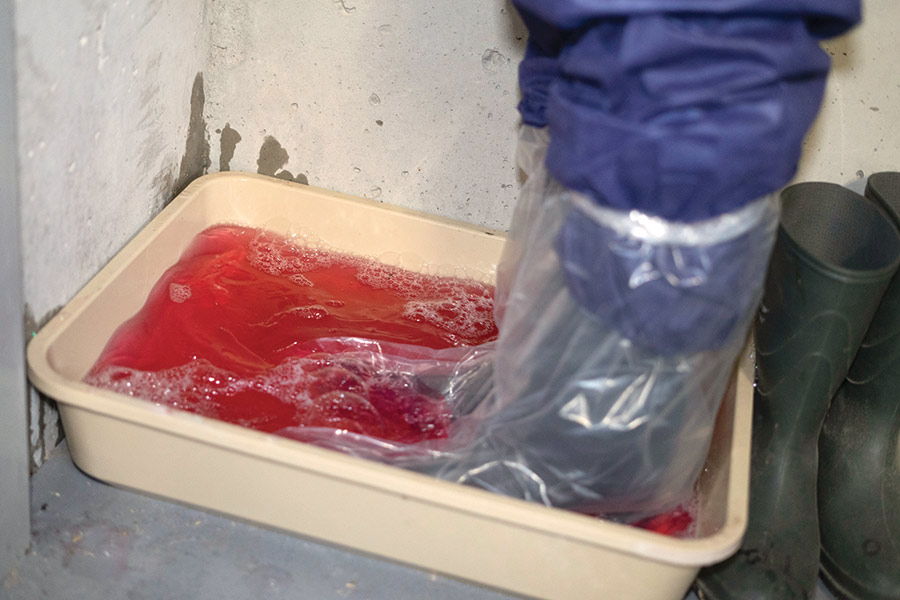
Keep the shed within a biosecure area and practise good farm hygiene
Vaccination is a critical part of salmonella protection, but it must be practised in tandem with good farm hygiene.
For instance, keeping a shed within a biosecure area that restricts visitors, and washing the wheels of any vehicles that have to visit the site.
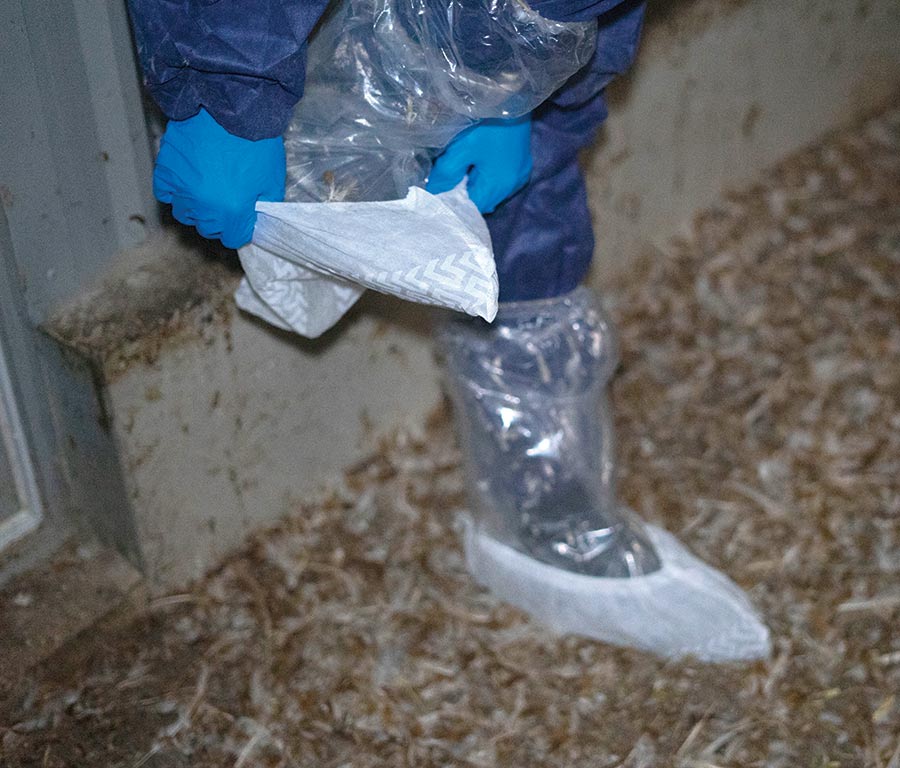
Boot swabs are used to detect if salmonella is present in the litter
Keep the site free of feed spills or detritus that can host rodents. Proper pest control is also essential.
“If you have salmonella-positive mice on your farm, there’s a very good chance it will get into the birds,” says Mr Hodson.
Clearing any dead birds regularly is also an important measure, as is ensuring carcasses are disposed of responsibly.
The state-of-the-art pullet sheds helping produce better birds
The pullet-rearing industry is a highly competitive market and companies are striving to upgrade rearing sites – traditionally a neglected part of poultry farming – to produce better birds.
At Country Fresh Pullets, there has been significant expansion over the past few years, and the firm now rears 8.5 million birds a year.
New sheds to fulfil this capacity have been modelled on the design of broiler farms, where environmental monitoring and biosecurity are built in to shed design, says Mr Hartley.
Anterooms have step-over barriers and there is a sophisticated computer control system from Fancom, supplied in the UK by JF McKenna.
That equipment allows farms to be ventilated based on carbon dioxide levels, and the kit automatically gathers bird’s daily weight gain, water and feed consumption – all giving insights into performance in near real-time.
Custom equipment in the poultry shed helps get birds used to life in a multi-tier laying farm, by providing perching and offering feed and water at several different levels.
It is folded down as birds become big enough to use the system.
How did the salmonella standards come about?
The presence of the bacteria in eggs – and comments by the then junior health minister Edwina Currie – in the late 1980s caused a collapse in the market, leading to a 60% drop in egg consumption in the following years.
From that crisis came the Lion Code, with the aim of protecting humans from salmonella at its heart.
It has evolved and today represents a rigorous set of rules and standards backed by regular audits to ensure traceability through the supply chain.
The testing regime for the laying hen sector
A significant part of the Lion Code’s salmonella control programme is auditing farms, making the source of any outbreak easier to detect.
Rearing sheds are tested before chicks are placed, and any dead-on-arrival chicks are sampled, along with the hatchery chick trays.
Blood testing and boot swabs, as well as dust, are also regularly sampled, and birds are checked before leaving the rearing farm for their life on a laying shed.
No birds can move until tests come back negative, and once on the laying farm, testing must take place every 13 weeks.
Every 12 weeks, 20 eggs from every Lion farm are sampled for salmonella; egg-packing centres are also regularly sampled.
All this testing is aimed at catching infected birds quickly. If a sample is positive for salmonella, birds cannot be moved until further, extensive, official testing has taken place.
The entire supply chain will then be audited to try to determine where the infection first appeared.
The consequences of a positive flock can be ruinous, both financially and reputationally.