The costs and benefits of installing a cow underpass

Cow underpasses can allow herds to graze less accessible acres without the trouble of halting road traffic flow.
An underpass is a large large box culvert made from precast concrete, installed under the road to allow the passage of stock and farm vehicles.
At £1,000-£1,200 a square metre of culvert area, the cost is considerable, but with that investment comes many benefits.
Jon Mathias, of Bridgend-based Vale Consultancy, has designed several underpasses on farms across the UK.
See also: 6 housing tips for better dairy production and welfare
Underpass design is site specific and requires the skills of an engineer or a suitable design-and-build contractor.
Below, Mr Mathias gives his advice on getting an underpass built to British and Eurocodes standards and meeting local authority requirements on design, installation and management.
Siting
Choose a site where its use will be most efficient, where maintenance will be minimal and where there is no pollution risk from the effluent that accumulates in the culvert.
Site location is critical because there is little that can be done later to remedy the situation if positioning is poor, and problems can be costly to resolve – for instance pumping out dirty water on an ongoing basis to prevent pollution.
Local authorities are mostly quite supportive of underpasses, but it is wise to include planning and highways departments in discussions from the beginning.
If the construction is likely to affect public bus routes and school runs, they may have preference for when construction starts.
Design
Underpasses are usually designed at right angles to the road centre line.
The depth of the culvert below the carriageway varies, depending on drainage, cables and other services which may be located below the road or in the verge.
New Construction (Design & Management) Regulations came into force in 2015 which require the appointment of a principle designer to assist with the project.
Before construction, the highways department may need to give approval in principle to the design.
Legal agreements and associated fees or bonds will need to be agreed with the local authority.

Richard Morris © Debbie James
Road closures
Road closures are not normally a problem provided there is a suitable diverted route.
Liaise with the local authority to establish how much notice must be given of the intended closure.
If a highway diverted route is not suitable, temporary roads could be designed and shown in the construction phasing plan.
Surveys
Requirements of planning mostly involve ecological surveys – to establish if the site is on a bat flight path, for instance – and this lengthens the approval process, so factor this into your timing.
A topographical survey of the area is needed for the design and planning process.
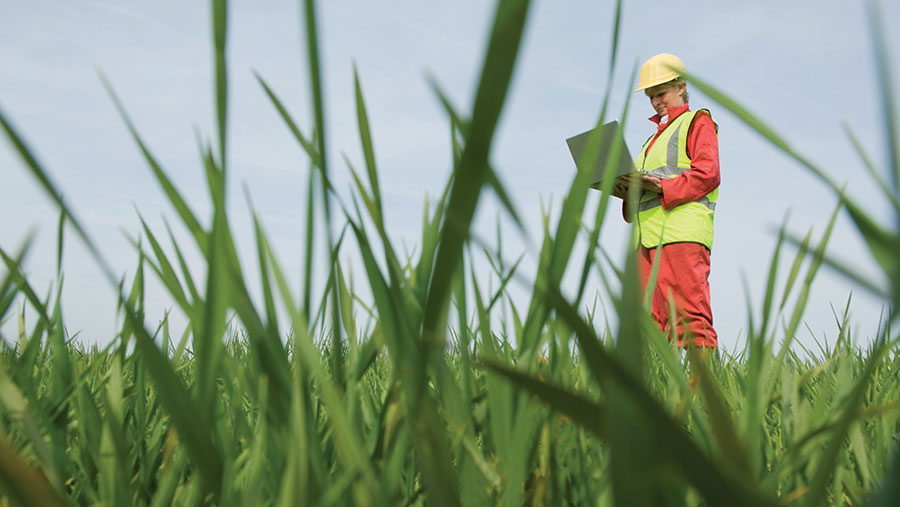
© Henry Arden/Science Photo Library
Cow flow
Avoid creating cow flow issues at the design stage:
- Take cow numbers into account when designing the size and width. These should be an adequate size for the existing herd or, if expansion is planned, for target cow numbers. As a guide, allow 3m of width per 450 cows
- Don’t create sharp turns or narrow races on either side of the underpass
- Keep the gradient as flat as possible – aim for 10:1 or flatter
- The floor should be flat at the construction phase and thereafter kept free of potholes and stones to avoid lameness issues
- Keep surface and ground water out, as surface water in the underpass is likely to create cow flow problems because stock will be slow to enter the underpass. More effluent is also likely as cattle take longer to move through.
Materials
Site investigations prior to design will confirm the ground strata.
Bedding, backfill materials, rock for the construction of head-walls, riprap and concrete should all be specified and checked by an engineer.
Installation
To assist traffic flow, construction usually involves excavation and installation of the underpass on one side of the road through to near completion before the other side is assembled.
Installation is typically tendered out to contractors.
Contractors should be identified and shown the construction phase drawing.
They will be responsible for:
- The supply of all plant, labour, and compound materials such as topsoil, sand and gravel
- The control of water during the construction phase
- Excavation of the access tracks to the underpass, removal of unsuitable foundation material and compaction of bedding material beneath the underpass
- Backfilling of the culvert to formation level and sealing
- Re-instating any services such as cables, fences and roadside drains post-construction
- Checking with traffic authorities, utility companies and any other relevant service providers, to ensure that work does not cause any disruption or damage to these services
- The general safety of the public, traffic and workers near the site.
Effluent management
Any water that enters or collects in the underpass will mix with sediment and effluent, so it should not then enter freshwater.
The underpass will need an effluent collection system but, if possible, site the underpass well away from high water tables or springs on high ground.
If it is unavoidable, there are anti-float designs that enable a site with a high water table to be used.
Effluent will need to be pumped to the effluent pond so design it to cope with the additional volume.
A precast storage unit is usually placed at one end of the underpass to collect surface water and effluent.
This should, if possible, discharge to the land via soakaways and be pumped out on a periodic basis in accordance with Environment Agency or Natural Resources Wales guidelines.
Cost
Prices for materials and for contractors to work on the planning, design and construction are extremely variable.
These largely depend on site conditions and the cost of the underpass culverts – budget about £1,000-£1,200 a square metre of culvert area.
Case study: Bowett Farm, Pembrokeshire
Building a cow underpass has helped Pembrokeshire dairy farmer Richard Morris improve his grassland management.
Cow numbers at Bowett Farm, near Pembroke, have steadily grown from 90 in 2003 to the 450 milked today.
As the herd expanded there was pressure on grazing, so 32ha of farmland, separated from the farm’s main land block by a busy road, was brought into the rotation.
Why it was built
This meant the farm’s entire 122ha could be grazed, but walking the cows across the road took up to 15 minutes, drawing hostility from motorists and causing stress for the farmers and their staff.
“Even though we stopped cow flow at intervals to let motorists through, they were becoming less tolerant as cow numbers grew,” says Mr Morris, who farms with his wife, Claire, and parents, Bill and Ann.
Three people were needed to cross the cows, which was a problem at weekends when there were fewer staff.
An underpass linking the two blocks solved the problem.
Construction costs
The family hired an architect and planning consultant with good experience of designing farm underpasses. They say securing the necessary permissions and road closures was straightforward.
The job of constructing it was given to a local contractor who had built underpasses on other farms. The whole project cost about £76,000.
There was only one setback during construction – a major water pipe that was thought to be some distance from the site was discovered to be running through it.
Rerouting the water pipe added £6,000 to costs and delayed completion. The underpass – 3m wide and 2.4m high – was built over 10 days in May 2019.
Benefits and payback
“Building the underpass is one of the best things we have ever done,” says Mr Morris. “The cows are very relaxed going out to grass and we now only need one person to move them to and from grazing, not three.
“We can manage the farm a lot better because we can graze the blocks when they need grazing, not when people are available to cross the road.’’
Farm facts:
• Autumn calving
• Milking 450 British Friesian cross Holsteins
• Cows graze for 180-200 days
• Milked through a 54-point rotary parlour
• Yielding 8,000 litres at 4.4% butterfat and 3.5% protein
• Milk sold to Glanbia Cheese.