How accurate feeding has added 1,700 litres to yield
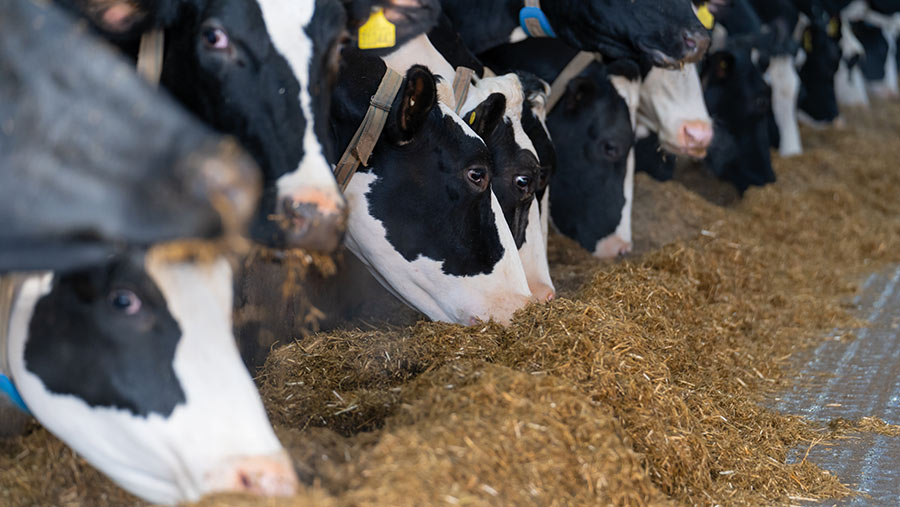
A large Yorkshire dairy has streamlined its feeding routine while adding five litres to daily cow yield over the past five years.
Metcalfe Farms, in Leyburn, North Yorkshire, is one of a growing number of larger dairy units that have simplified total mixed ration (TMR) feeding with an all-in-one vertical auger machine.
See also: Ways to reduce dairy greenhouse gas emissions to hit targets
The control and consistency it brings to feeding the herd is a key reason why yields have lifted from an average of 10,800 litres a lactation in 2018 – when the Metcalfes won the Gold Cup – to 12,500 litres a cow today.
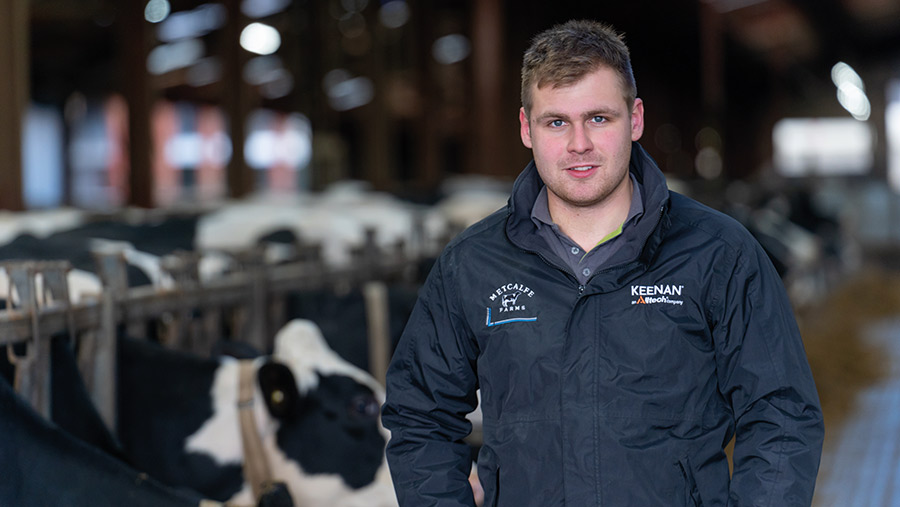
Rob Metcalfe © Hubspoke Media
This is according to Rob Metcalfe, who works on the dairy enterprise with father Phillip. They have relied solely on TMR feeding, with no parlour cake, for decades.
Mr Metcalfe says the accurate balancing and feeding of rations provides rumen stability.
Farm facts
- 1,300 Holsteins
- Farms 1,295ha (3,200 acres) over owned, rented and contract-farmed agreements
- 41.5kg of milk/day at about 12,500 litres an average lactation
- 3.8% fat and 3.35% protein at 80,000 somatic cells/ml
- Milk supplied to Paynes Dairies
- Three-times-a-day milking through a 72-point Boumatic parlour
- 200kw anaerobic digester unit
- Sawdust bedding
Big outlay
At well over £300,000 for a high-specification Keenan model today, the cost is eye watering. However, Mr Metcalfe believes any farm with a tractor on a feeder wagon 24/7 should consider a self-propelled option.
The VA2-33 model is the farm’s third self-propelled since 2017. It was bought in March 2022 and cost about £300,000.
It included a near infrared dry matter (DM) analysis system to ration cows on dry matter rather than freshweight.
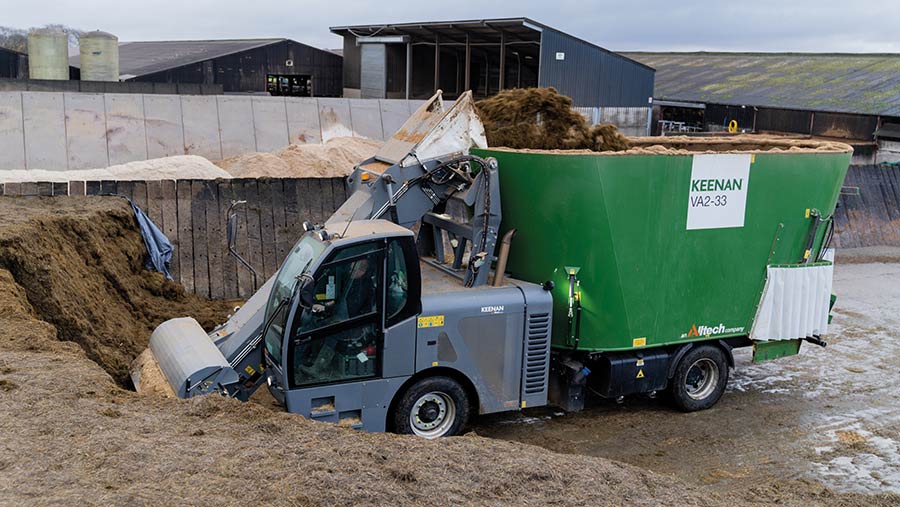
© Hubspoke Media
Operator tips for self-propelled machines
- Yards Well-concreted yards and passageways allow for easy operation. Loose hardcore and stones could damage the header
- Clamp management Training and practice to cut into the forage is essential using the tungsten-coated blades of the cutter head for a clean clamp face, with no openings or cracks
- Loading skill Instruction and practice are needed to load feeds into the mixer bucket accurately
- Maintenance A keen eye for maintenance keeps the machine operating, with only one down-day in two years. Drive shafts for the augers are greased twice a week. A service cost of £700/month covers upkeep by a specialist agricultural engineer
Source: Rob Metcalfe
Ration management
Farm feedstock manager Steve Allen has been able to balance a grass and fermented wheat wholecrop diet with cost-effective protein sources.
A pre-mix of minerals, ground maize, wood-sugar-treated rapemeal, soyabean meal, wheat syrup, limestone flour, and protected fat and methionine is added first.
Then the forage and straights are added at the clamps.
These are grass silage, fermented wholecrop wheat, wheat straw, brewers’ grains, distillers’ by-products, pressed pulp, whey permeate, bread and caustic wheat. Straw is chopped to 50mm and grass silages are 25-30mm long.
Mixing and feeding starts at 4.30am, when the cows are followed back from the parlour so they can stand and eat straight after milking.
All milker groups, dry cows (close and far-off) and in-calf heifers are fed by 10am. Each load feeds about 250-360 cows.
Growing heifers are fed with a trailed mixer wagon on a rearing farm a 20-minute tractor drive away and fed a blend and straw diet.
An afternoon feed is done at 12.30-3pm to top up feed bunks. Three Lely Juno feed pushers are programmed to push feed up six times a day.
Cows are rationed for maintenance plus 49 litres, targeting intakes of 25-28.6kg day. Energy in the ration is 12.3MJ/kg DM and crude protein is 16.5%.
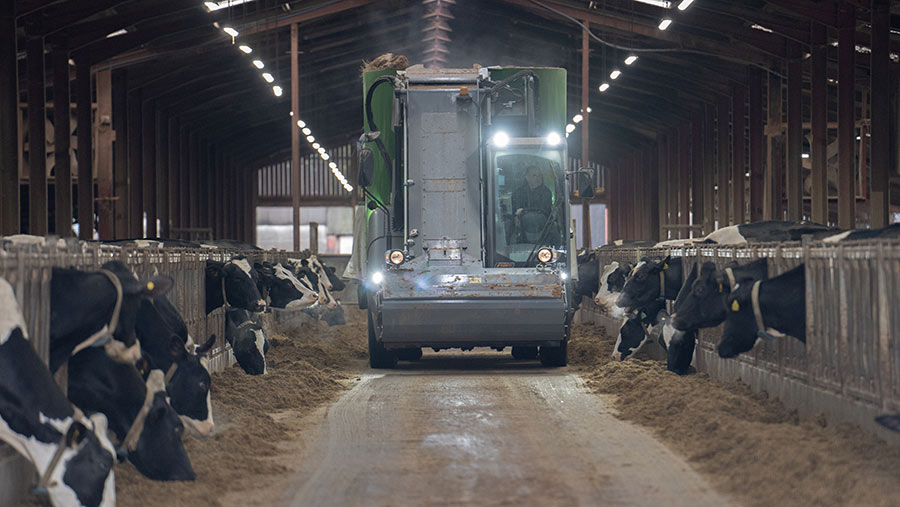
© Hubspoke Media
The numbers
- 1% Milk fever rate
- 19% Mastitis rate
- 30% Pregnancy rate
- 22 Full-time staff, plus 13 shift workers
Forage
Grass silaging starts early to capture high D-value crops. Last year, it commenced on 28 April. Subsequent cuts are taken every 28-30 days thereafter. Harvesting is done by two 990 Claas forage harvesters and two forage boxes.
The team aims for at least a 30% DM silage. More than 364ha (900 acres) is taken for first cut. Wholecrop is taken when grains are at the “cheesy” stage, at about 36-40% DM.
About 10,000t of grass silage capacity is clamped with oxygen barrier side sheets that cover the entire side panels and stretch round to the base.
This ensures no air gets in and energy losses are minimised. About 7,000t of wholecrop was ensiled in harvest 2022.
Cumulative gains
Monitoring the diet and performance of all groups of cows helps the farm make evidence-based adjustments to maintain production, says Mr Metcalfe.
Genetic progress is acknowledged using sexed semen, and genomic testing helps technical performance.
The team ensures cow comfort and lying times are good on the sawdust and mat cubicles.
Staff are empowered to make decisions and observations to ensure what they see and experience informs future management choices, he adds.
Benefits of the self-propelled machine at Metcalfe Farms
Accuracy
- Loading accuracy of feed dry matter has improved from 95-96% to 98%
- Extra feed accidentally loaded can easily be fed back in the pile by reversing the header system. When bucketing feed into a trailed wagon, the extra feed often ends up in the feeder as it is easier doing this than putting it back in the pile
- There is less temptation to cut corners when you keep up with a busy routine
Clamp face
- The header cutter shaves gently, with no gouging like a sheer grab
- It works quicker across the clamp face with less cracks and openings for oxygen to get into the silage, reducing aerobic spoilage. But it is hard to quantify as the farm switched to multicut silage in the same year it bought a self-propelled machine
Driver comfort and ease
- Rather than climbing into two machines, the operator sits in one seat and drives round the farm in a heated, air-conditioned cab
- Staff job satisfaction is important as good-quality agricultural labour is getting harder to find
Fuel and depreciation
- The self-propelled unit means one machine is used instead of three (tractor, feeder wagon and telehandler)
- One tractor is freed up in the yard. Typically, this would be a 180-190hp vehicle, which costs £90,000-£100,000
- The Metcalfes trade in their telehandler every three years. Since getting the self-propelled wagon, hours of use have halved from 6,000 to 3,000 hours in three years. This means the telehandler is worth more and the cost (purchase price minus depreciation) has halved to £8/hour
- Fuel use for the self-propelled machine is 180-200 litres/day. The direct auger drive on the previous trailed wagon used more fuel
Mechanical auger
- Mechanical auger is easier to maintain, with fewer problems than an oil-driven hydrostatic auger
Straw chopping
- Self-propelled machine chops straw itself. There is no need to hire in a straw chopper, so savings are made on contractor costs
Source: Rob Metcalfe