Painful 2019 harvest delivers valuable maize-growing lessons
The importance of preserving soil structure and exercising patience in harvesting a maize crop are among a Nottinghamshire maize grower’s key lessons from the painful 2019 harvest.
Last year’s autumn deluge provided John Jackson with plenty to reflect on. He says it taught him valuable lessons about soil structure and compaction prevention.
See also: Rain puts pressure on maize with tricky harvest
“I have learned more in the past four to six months about maize agronomy and harvesting than I did in the last 10 years,” said Mr Jackson, who is farms manager for Severn Trent Green Power.
“Many parts of the country were badly hit and in the East Midlands, where I am based, things were really difficult. We don’t want a repeat of it. However, we can learn from times like these.”
After growing and attempting to harvest 2,023ha (5,000ac) of maize last year , Mr Jackson concluded that healthy soils are a farm’s biggest asset.
Harvest facts
- Harvesting about 80,000t of maize/year on 2,023ha
- Produces 100% of the feed requirement for the Stoke Bardolph crop only AD plant
- 20,000t of wholecrop rye
- 2019 harvest cost £50,000 more than a typical year, lifting overall feedstock costs/t by 2%
- Bulk of harvesting took 12 weeks, compared to the usual seven – some fields combined for grain in February
1. Use tracks and diggers to minimise compaction
- Switching to tracks was a vital step to keep work progressing and avoiding rutting and compaction.
- Tractors on tracks were used to pull trailers around fields.
- However, to make this work, tractors on conventional low-ground-pressure tyres had trailers filled at the edge of a field, with a 360deg digger transferring piled maize into tractor trailers.
- The digger cost in the region of £40-£45/hour with a driver and was fitted with as big a bucket as possible.
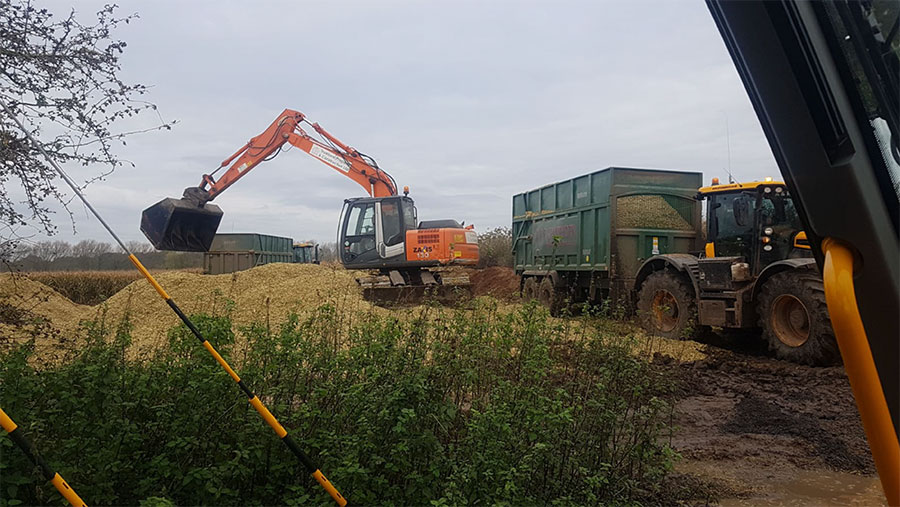
Maize by 360deg digger
2. Double up on wheels
- Kitting out the forager with dual wheels meant there was 1.5m of tyre overall at the end of each axel. This increased the surface area that the weight of the forager was spread over.
- Initially, the team was worried putting tyres on would be time consuming, but it turned out to be a five-minute job.
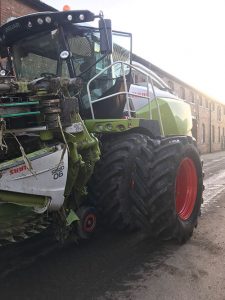
Forager with dual wheels
3. Avoid tractors going in fields all together
- Severn Trent used a sugar beet harvester (MAUS) to lift and transport already chopped maize onto tractors parked in laybys over hedges.
- This can avoid tractors on tyres going into fields, although there are only a small number of these specialist machines available to hire in the UK.
4. Clean machines before heading onto the road
- All machinery had to be cleaned and washed down before exiting the field onto a public road.
- Tyres and machines were cleaned off with water from an adapted slurry bowser with a hose fitted to it.
- This kept roads clean, avoided penalties and was good for public image.
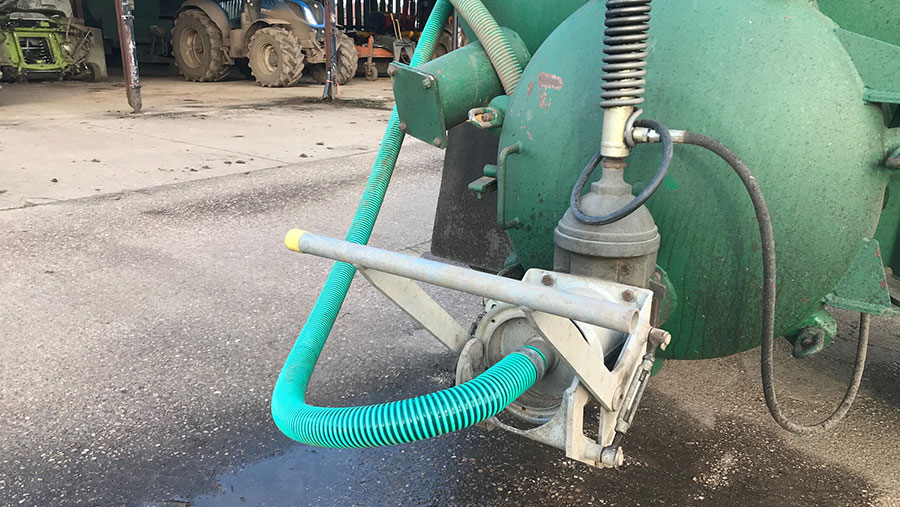
Tank with bowser
5. Cancel chopping and combine at a later date
- On the wettest land near the Trent, the team opted to delay harvest entirely, eventually combining the crop in February for grain.
- While the usual approach is to harvest maize at about 31-32% dry matter (DM) to optimise gas yield (660N sq m/t DM gas yield), 80ha maize was instead combined as grain at only 70% DM. This grain will be used to replace cereal grains that the AD plant has traditionally used.
- Grains were crimped, yielding 10-14t/ha, which saved on drying costs up to £40-£50/t (depending on heat source). This will analyse at roughly 10% crude protein, 70% starch and 14.5 MJ/kg of energy.