Targeted feeding for more efficient finishing
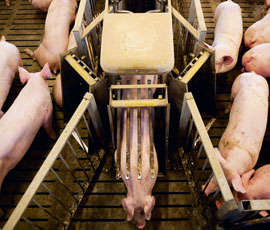
In a challenging market, producing a consistent, quality product and reducing input costs is the Holy Grail for any pig finisher
Such thinking forms the basis of management and unit design at JSR’s Decoy finishing unit, Driffield, East Yorkshire.
Set up in July 2010 at a cost of ÂŁ2.1m, Decoy is the largest finisher unit in the country, capable of housing 8,500 pigs at a time and producing 20,000 pigs a year.
Key aims
Glenn Dams, JSR managing director, explains that in order for the facility to meet its target of 325kg of pigmeat sold for every one tonne of feed consumed, diet and facilities have to be top notch.
“We need a lower feed conversion ratio, good welfare and a system that is repeatable for the team,” he says.
“We want the facility to last at least 20 years and continue to improve the efficiency of the animal over this period.”
The unit was designed to take pigs produced by the company’s 1,800-sow breeding unit. Consequently, economies of scale meant the unit could afford to invest in technology.
A sorter and automatic feeding system (right) has been installed for all pigs at the finishing stage, allowing individual pigs to be fed a tailored nutritional package according to weight. Animals can also be automatically sorted when they reach finishing weight to get the optimum slaughter price.
Weaners
Eight hundred weaners enter the facility every two to three weeks and are weighed and split by sex. Each sex is housed in one nursery room which is split into groups of 120-150. “We want to know how many kilos of pig meat are coming in and going out and how much feed we have used,” Mr Dams explains.
Weaners are fed a milk powder and creep gruel diet for the first week on the facility to acclimatise them. At this stage they also have access to a wet and dry creep diet. “The first week after weaning is a critical time so giving stock attention at the right time is really important,” says Mr Dams. Pigs then progress to a link diet, weaner diet and then a grower diet.
Environmental, enrichment and above-standard stocking rates (0.47sq m across the whole unit) also forms part of an overall drive to raise welfare standards on a slatted system.
Weaners spend 12 weeks at the nursery phase. Each nursery room is then kept as one group at the finisher stage where they stay until slaughter.
“By only having two stages, there is less movement and so less stress and increased growth rates,” says Mr Dams.
“It is also more cost effective as it requires less buildings and reduced staff time.”
And splitting according to sex enables greater control over feed intakes. “Gilts grow slower than boars, but the aim is to close the gap between sexes through nutrition and so optimise weight to finish at 108kg lw/83kg dw.”
The sorter system
On entering the finishing phase, pigs are trained for three weeks on how to go through the sorter. Each room is split into boars and gilts with each group of 375 pigs having its own sorter system made up of a weigh scales and pen system. When a pig wants feed, it enters the weigh scales and is then automatically split into one of three pens – depending on weight – and fed a specific ration.
Every day the system can calculate the average live weight gain of a pen and can predict how many pigs are going to reach market weight six weeks in advance.
According to Mr Dams, pig flow through the system is not a problem because animals are going through the sorter for a reason. “In the USA they have 500 pigs for every sorter so we are above standard.”
Feeding
“Our aim is to finish all pigs consistently like ‘peas in a pod’, and at about the same time,” says Rob Campbell, manager of the Wolds breeding and finisher units.
“The ration is made up of wheat, barley, rape, soya, wheat feed, vitamins and minerals and lysine. We know the average weight of pigs going to each feeder, so we can tailor the ration accordingly.”
There are two different nutrient packages which are blended to suit a specific growth stage. The diet is then automatically delivered from the main silos to individual pens in 40kg batches.
For example, the three feed pens may be split so that 70kg pigs are fed one ration, 80kg animals a different ration and 100kg another. After feeding, animals can then re-join the main group.
“We are finding a six-week spread in a batch, but in an ideal world our aim would be to reduce this to four weeks,” says Mr Campbell.
“We can’t control pig price, so the quality of the pig we produce is the only way we can maximise price,” says Mr Dams.
“Our aim is also to reduce feed costs for every kilo of meat produced. Three years ago feed was 50% of the cost of production, now it is 65%. We need to reduce costs of production where possible.” With this in mind, drinking and wash-down water for the unit is also supplied through a bore hole which includes an iron and manganese filter.
Feed is changed according to where animals are on the feed curve, which has been set up for a Titan boar or gilt. The recording system also allows the team to accurately predict how many pigs are going to be finished and when. As soon as pigs reach slaughter weight, the sorter system can be set up so that pigs are drafted into a separate pen to be sent to the abattoir.
Slaughter weights
Such technology may appear only relevant to large scale units, but according to Mr Campbell, sorters could have a role to play in smaller systems. “There is a lot of mileage in these sorters. People waste money feeding an incorrect ration – the key is to tailor the ration to the stage on the growth curve.” And because labour inputs are greatly reduced, efficiency is improved. In fact, the automated system at Decoy means the whole unit is managed by two members of staff – manager Antony Wilkinson, and animal technician Maciej Niznik.
Targeted feeding means pigs can be finished to suit specific slaughter contracts. “Pigs are finished in a DW range of 67-90kg, but we want as many pigs as possible to hit our target of 108kg lw/83kg dw,” says Mr Campbell.
And the latest slaughter sheet demonstrates how effective the finishing system is at targeting pigs for slaughter (see graph below).
An overflow room similar to a standard finishing unit is used for any pigs that straggle behind their group. “It is not viable for us to have 60-70 pigs running through a sorter because we want the next batch into the system. Pigs have to go within two weeks when they enter this group.”