FW Awards: Pig Farmer of the Year finalists 2018
Two contrasting family-run businesses feature as Farmers Weekly Pig Farmer of the Year finalists this year – an outdoor breeding herd finishing all progeny in straw-based sheds, and an indoor unit producing bacon with a carbon footprint some 30% lower than the UK standard.
See also: Meet the 2018 Farmers Weekly Awards finalists
The 2018 Pig Farmer of the year finalists are:
- Christian Andersen, Bedfordia Farms, Milton Earnest, Bedfordshire
- Rob and Helen Mutimer, Mutimer Partnership, Swannington, Norfolk
The judges
- Howard Revell, last year’s winner
- Johann Tasker, Farmers Weekly chief reporter
- Zoe Davies, independent judge
Christian Andersen
Bedfordia Farms, Milton Earnest, Bedfordshire
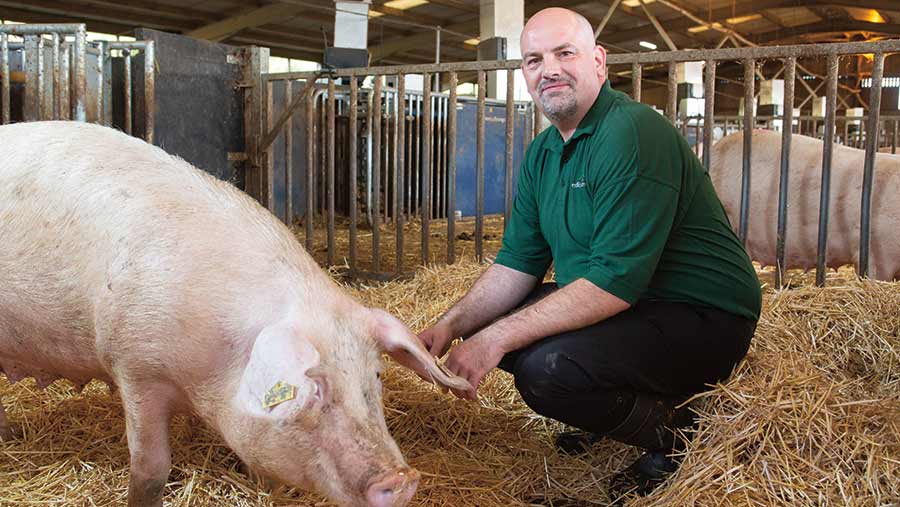
Christian Anderson © Tim Scrivener
Farm facts
- Two breeding farms each with about 560 sows and weaners up to 40kg
- Dry sows and gilts kept in straw yards with electronic sow feeders
- Fully slatted farrowing with lifting crates and fed via individual drop tubes
- All pigs on breeding farms dry-fed using auger – no hand feeding
Bedfordia Farms is a highly efficient indoor pig unit, producing Red Tractor-assured pork to high standards – which includes not using critically important antibiotics.
Pig operations manager Christian Andersen operates three indoor production sites. Two breeding farms each have about 560 sows and weaners up to 40kg. Dry sows and gilts are kept in straw yards with electronic sow feeders.
The two breeding farms operate a recently upgraded heat recovery system that means they do not require any fossil fuels for heating. Slurry from the finisher farm is pumped directly to a neighbouring biogas plant.
Business focus
All pigs are sold through Meadow Quality, with 400 pigs going to Woodheads and 180 pigs plus cull sows going to C&K Meats every week. Pigs are also supplied to a local butcher and farm shop, with some 3,000 surplus pigs sold annually at 7kg through Meadow Quality.
Pigs on the breeding farms are dry-fed. Feed is moved by auger line, with no hand feeding. Farrowing is fully slatted with lifting crates and fed via individual drop tubes. Lactating sows are fed three times daily. Weaners are on partially slatted floors with heating over the non-slatted part.
Recording and benchmarking are key business tools. On-site computers produce daily reports from the electronic sow feeders on feed consumption, flagging up any sows that aren’t eating or only partially eating their allocated ration.
Weekly and monthly reports are produced using the Agrosoft recording system and help compare performance across the industry. Growth is monitored in real time using a 3D weigher installed in the finisher buildings.
Herd health is good for a closed commercial herd. Gilts are vaccinated against erysipelas, parvo virus and E-coli. Sows are also vaccinated against erysipelas. Piglets are vaccinated against mycoplasma and PCV2.
Fixed formulations devised by an independent animal nutritionalist are used to ensure consistently high-quality feed. The wet feed system is monitored 24 hours a day to flag up any anomalies in feed consumption, which are then quickly corrected.
Staff involvement
The main challenge is to find good, competent staff in an area of the country where there are few pig farms. This means all staff need to relocate to work on the farm. The farm has an excellent relationship with local colleges.
To recruit and retain good staff, pay is above average, with a six-monthly bonus depending on performance. Employees are rewarded financially for excellent unit performance through attaining key performance indicators on a whole-team basis.
All three sites have an additional two stockman. This is a high number of staff, but ensures good employee coverage in the event of holidays or sickness. Employee reviews are carried out annually and followed up every three months.
Mr Andersen is proactive about educating the wider public about farming, and the contribution it makes to modern society. The gates at Bedfordia Farms open to visitors and local families every second year on Open Farm Sunday.
Each year, the business receives a number of veterinary students as part of their work experience. The farm also supplies pigs to the Royal Veterinary College for research and student practice purposes.
The future
The farm’s biggest achievement has been the complete removal of all in-feed medication across all three farms – driven by both the overall aim of reducing antibiotics use in food production and the cost savings, which are significant.
A major conversion of the dry yard on one farm includes new electronic sow feeders and individual stalls for serving. Recent investment in a cleaning robot will benefit staff by reducing the need for pressure washing by hand.
Expansion is on the cards to build on the business’ success. The enterprise is close to applying for planning permission for a new gilt building on one of the sow farms. It is also in the planning stage to expand the finishing farm.
The judges liked:
- A really strong production unit – including exceptionally low antibiotics use
- Well-invested facilities in a non-pig area that attracts good-calibre staff and has links to local college
- Good use of renewable energy and integration with other parts of the farm business
What the judges say:
“Bedfordia Farms is run with a military precision that staff can be proud of, with impressive production figures and low use of antibiotics. It is encouraging to see the business going from strength to strength.”
Rob and Helen Mutimer
Mutimer Partnership, Swannington, Norfolk
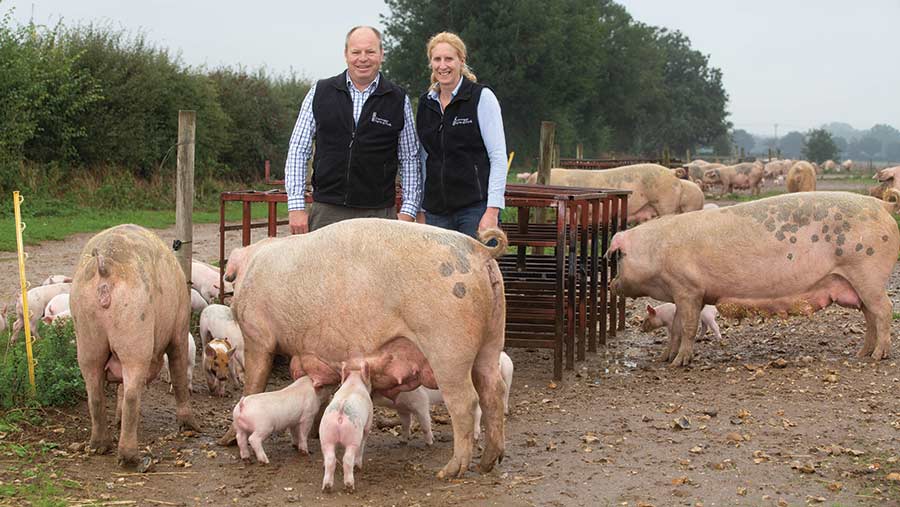
Rob and Helen Mutimer © Tim Scrivener
Farm facts
- 700 outdoor Landroc sows with Landrace grandparent herd supplying replacement gilts
- 13,000 pigs produced annually for Waitrose supply chain via Tulip
- 30 pigs a week butchered and supplied to local pubs, restaurants and colleges
- Three-weekly batch farrowing, closed herd with 100% AI
Husband-and-wife team Rob and Helen Mutimer are partners in the family business – farming a high-welfare breeding herd of 700 outdoor Landroc sows and finishing all progeny in straw-based sheds through to slaughter.
Weaners are moved into tents at 28 days on another farm three miles away, where they are grown to 25kg, producing some 14,000 pigs a year. At 25kg, they are transported to one of four finishing farms within a 10-mile radius.
Some 250 pigs a week at 105kg go into Tulip at Spalding for the Waitrose supply chain. A further 30 pigs a week are transported to the local abattoir and returned to the on-farm butchery to supply about 150 pubs, restaurants and colleges through the Swannington Farm to Fork business.
Business focus
The all-in, all-out grower-finisher system sees all accommodation fully cleaned and disinfected between batches. A Landrace grandparent herd supplies replacement gilts on a system using 100% artificial insemination and chaser boars.
A major setback in 2015 – when the breeding herd was diagnosed with swine dysentery – has proved no obstacle to success. The herd was depopulated immediately as the Mutimers realised medication was unlikely to be successful and would potentially affect other farmers in the region.
This selfless decision saw the last of the finished pigs slaughtered in April 2016, followed by a three-month rest period. All machinery, equipment and buildings underwent a strict cleaning and disinfection protocol before restocking.
Farrowing rates have since increased from 83% to 90%, with a 3% drop in pre-weaning mortality. Biosecurity improvements have included an on-farm incinerator and rearranged transport movements to eliminate any risk of cross-contamination from wheels.
Technology is key to business success. All breeding and finishing data is recorded using Agrosoft Pigvision. Electronic ear tags aid sow recognition. A carbon monoxide monitor and wind speed recorder have helped boost ventilation and so improved pig health.
Staff involvement
This is very much a people-focused business. Farm staff are viewed as an integral part of the team – and all receive the relevant training for their positions using AHDB and Poultec courses. Employees include stockmen, butchers and administrative staff.
An employee forum has proved to be a great method of harnessing fresh ideas and bringing new knowledge into the business – ensuring its ongoing success and helping to keep the enterprise ahead of the competition.
Welfare of both staff and livestock are at the forefront of thinking on this farm. A new facility has dramatically reduced the stress of both piglets and stockmen – saving 10 man hours every weaning with a payback time of just 10 months.
The future
Constantly looking to improve the business, a profit-share scheme ensures staff receive 20% of annual profits. Rewarding employees as a team, rather than individuals, has increased business performance, which is set to rise further in the future.
Rob and Helen are in negotiation to buy and develop a new pig-finishing farm. This will enable them to grow the sow herd – while researching and installing the best technologies, including clean water systems, to improve pig health, welfare and performance.
The local market for pork from Swannington Farm to Fork has been growing at about 15% annually and is expected to increase through a strong emphasis on customer-focused sales, efficiency savings through technology and stringent financial recording.
The judges liked
- Strong employee engagement, including profit-sharing scheme and staff forum
- Good succession planning and business structure that plays to the strengths of family members across the generations
- An outward-facing approach, acting as ambassadors for the industry
What the judges say:
“An outstanding business that produces top-quality, high-welfare pigs while playing to the strengths of all involved. An outward-looking approach means Rob and Helen are great ambassadors for the industry.”