Massive investment in Scottish barn egg production
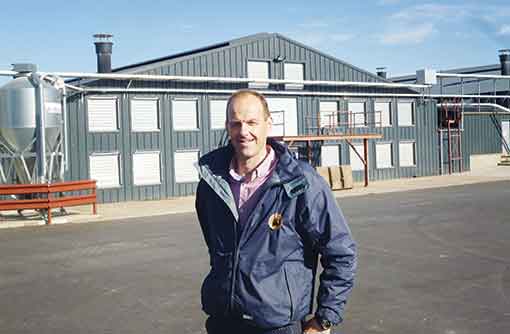
A desire to add value to grain and get out of pigs has led to a major move into egg production, including barn eggs, at one Scottish farming business, as Poultry World reports
A surprise upturn in demand for barn eggs has prompted a major investment at Duncan Farms in Aberdeenshire, where £2.5m has been spent on a new barn egg facility across two sites.
The company originally went into egg production in 2010 when Fred Duncan, the founder and former managing director of the Grampian Country Food Group, decided the time was right to get out of pigs.
“Four years ago, we were faced with the uncertainty of the pig market and we were right to be concerned,” says Duncan Farms chief executive Dave Green. The company initially invested in colony production, building up an enterprise with capacity for 300,000 birds. But when the last of the pigs went away in June 2013, management was then faced with the decision of whether to go into broilers, or increase egg production.
“A shortage of space around the sheds meant free-range was not feasible,” explains Mr Green. “We did have the space to increase our colony production, but an increase in demand for barn eggs from Noble Foods, egg packers and processors led us quickly into the barn option.”
Former pig sheds on two sites have been refurbished, with each site having the capacity to house up to 52,000 layers in two barns.
Big Dutchman’s Natura Step system has been installed, ensuring high standards of welfare and production, with 40,000 birds currently accommodated at each site.
Each barn is set up with perches, to encourage the birds to move up to roost. Feeders and drinkers are also situated high up to encourage birds to move up to the nesting boxes and discourage laying on the floor.
When the lights are switched off, any birds still on the floor are moved up manually to perch higher. “We want to make this their daily habit and in the end, reduce the numbers of eggs which end up as seconds.”
The 15-week-old Lohmann Brown pullets, which arrived in late September, hit peak production in December, dovetailing into the requirements from Noble Foods.
COLONY PRODUCTION
Duncan Farms first made its move into egg production in September 2010 when a rearing and colony production facility with a capacity for 225,000 laying hens was established at a capital investment of £7.4m.
Three out of four pig finishing sheds at the Newton of Fortrie site were converted for laying and the remaining one was turned into a grain store.
Another £1.8m state-of-the-art laying unit, providing accommodation for 76,000 birds, was commissioned in February 2013, with room for further expansion as markets are secured.
The new unit was built with length and height in mind, keeping width to a minimum. This was to ensure the most economic build and make the best use of the motors which power the automatic feed delivery augers and take away muck.
The building is 88m long and 31m wide and half of it is currently stocked, accommodating 10 tiers of colony cages up to a height of eight metres. Total capacity is 76,440 birds in 1,274 colony cages at 60 birds a cage.
All the conversions at Fortrie, including the new sheds, have been built by Titan Steel.
All four also feature a Big Dutchman computer-controlled ventilation system, which keeps the buildings at exactly the right temperature by manipulating the side and roof air vents without any artificial heating. Air mixers ensure the even distribution of heat throughout the building.
The laying units are positioned side-by-side and serviced by an auger which delivers feed to each from a central bin, and a conveyor belt which transfers eggs to a purpose-built grading and packing station for despatch to customers.
The move into egg production has provided an alternative market for grain grown on the company’s farms, adding value as well as providing high-nitrogen manure for arable crops and a hedge against high artificial fertiliser prices, says Mr Green.
“We are working towards a totally integrated and balanced farming business taking eggs from ‘farm to fork’, using most of the grain grown on our own farms and spreading all the manure on our own land.”
PULLET REARING
Production is planned in meticulous detail at the state-of-the-art pullet rearing unit for 77,000 day-old chicks. The focus is on genetics, leading ultimately to an extended laying period.
Back in 2010, rearing was taking about 15 weeks with a turnaround time of two weeks, meaning each cycle took 17 weeks. Three cycles would therefore take 51 weeks, but with each crop then laying for 56 weeks, this resulted in the rearing shed lying empty for five weeks before staring the next batch.
A change in production planning for the rearing unit has resulted in better utilisation of the shed. By shortening the rearing period to 14 weeks, and extending the laying period to 62 weeks, this has enabled the rearing unit to service four sheds instead of three.
“At very little cost, we have removed the gap in the rearing and increased the number of sheds from three to four,” says Mr Green. “This further shed only requires one extra stockman, plus 45 minutes to grade the eggs each day.
“It has been a big success rearing our own birds. They move into the colony unit in great condition and give us a spike in egg production soon after being housed in the laying shed.”
FEEDING
Feed is manufactured on site once a week – currently producing 350t – using the company’s own mobile Tropper feedmobile, which is operated by Feedmix, a Harbro Group company.
Specially designed for pig and poultry feeds, the Tropper’s outloading system reduces separation, ensuring the grist and structure of the feed is consistent.
The 13,100t of wheat and barley used annually is grown within a 10-mile radius of the laying unit, which keeps haulage costs to a minimum and reduces carbon footprint.
Rations are formulated by Harbro poultry specialist Doug Steele and these are reviewed on a monthly basis to optimise production and profitability. Feed intake is working out at 118-119g a bird a day giving excellent feed conversion.
“Our first four sheds since we started peaked at 95-96% and produced 315, 325, 330 and 328 eggs in the 54-week laying period,” says Mr Green. “Performance begins to tail off after 54 weeks of laying, but the first shed we have continued to 60 weeks of lay has achieved 350 eggs, which is a viable return on our investment.”
EGG PACKING
Eggs are delivered to the packing centre on two conveyor belts carrying the eggs from two separate sheds at the same time.
“As flocks get older and egg quality reduces, this raises the amount of ‘poor’ eggs over the 5% mark. Mixing and adjusting the flow of eggs from the four sheds has helped overcome this, taking the overall ‘seconds’ down to below a commendable 4%,” says Mr Green.
The packing station employs a Moba Omnia FT 330 egg grading and packing machine, meeting British Retail Consortium Issue 6 Standards Grade A. The grader checks for surface blemishes and cracks (using tiny in-built cameras and a set of microphones which detect non-visible cracks involving the gentle tapping of the eggs 16 times) and ultraviolet bacteria disinfection.
Capacity is 120,000 eggs an hour to allow for future expansion and the eggs are weighed, stamped with the Lion quality mark and farm code and best before date, segregated according to grade and customer (there are 12 packing lines) and packed for delivery direct to the retailer. Customers include Asda, Tesco and all Lidl stores in Scotland. Turnover of the business is £6m – and rising.
DUNCAN FARMS, ABERDEENSHIRE
- Duncan Farms now farms a total of 11,543 acres in Scotland
- Colony egg production with capacity for 300,000 birds
- New barn egg unit with capacity for 105,000 birds
- Peak production of 190,000 doz eggs a week
- Total investment in egg production and packing of almost £12m
- Grant aid of £2.1m under the Scottish Rural Development Programme and the Food Processing and Marketing Grant Scheme
- 4,800 acres of cereals grown in the Turriff-Banff area
- Recent acquisition of an estate in Helmsdale, Sutherland for wind development
- £20m investment in wind turbines, including three at the colony site
- General manager: Milan Copic from Bosnia