Ways to improve conveyor belt efficiency
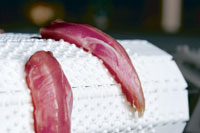
Conveyor belts are frequently taken for granted in poultry processing, yet they are a critical element, from de-boning right through to portioning and packaging.
The performance of conveyors can make a real difference to the overall efficiency and safety of a plant and the sector stands to benefit by re-assessing its conveyor and belting set-up.
Fundemental questions should be asked, such as whether they perform well enough when it comes to minimising product waste, safeguarding product quality and minimising maintenance and downtime? And importantly, do they stand up to the strict hygiene standards demanded?
Intelligent solutions
To maximise the potential output of a facility, poultry processors must ensure that they select the right conveyor belt for the right application.
Actual belt cost is always going to be an issue – now more than ever. But reducing whole-life costs through reduced maintenance is also a critical consideration as unnecessary downtime, product waste and hygiene costs have a disproportionate effect.
Whether fabric, plastic modular or power transmission, belts must be able to offer reliability, an increase in system speed, hygiene compliancy and flexibility.
Plastic modular belts, which can be used in a wide range of belting applications, are a popular choice for the poultry industry is.
The all-plastic design promotes long life and superior performance in many applications. Multiple widths are achieved by using a “bricklayed” pattern, which also promotes high lateral and diagonal belt strength and stiffness.
These belts are durable, reliable and built to withstand the demands of modern processing facilities, where belts are often required to run for long periods of time.
Plastic modular belts have also been designed to increase efficiency of production lines through their “positive drive” system. This helps reduce the problem of mis-tracking and the consequent damage to belts and potential product contamination.
Keeping it clean
Hygiene is clearly a high priority for food processors too. It is therefore vital that conveying solutions meet the stringent legislative standards.
Leading belt providers have enhanced their plastic modular belt designs to allow for improved hygiene conditions. Advanced sprocket and flat top modules, as well as CIP (clean-in-place) systems, enable faster and more reliable cleaning cycles, substantially less water-use and lower labour costs.
Like virtually all sectors, the UK poultry processing industry is facing a real challenge to get back on track as the economy emerges from recession. However, belt manufacturers have developed the products and technical support to ensure poultry manufacturing facilities continue to run at optimum efficiency.