How a sand separator improves slurry management on a dairy farm
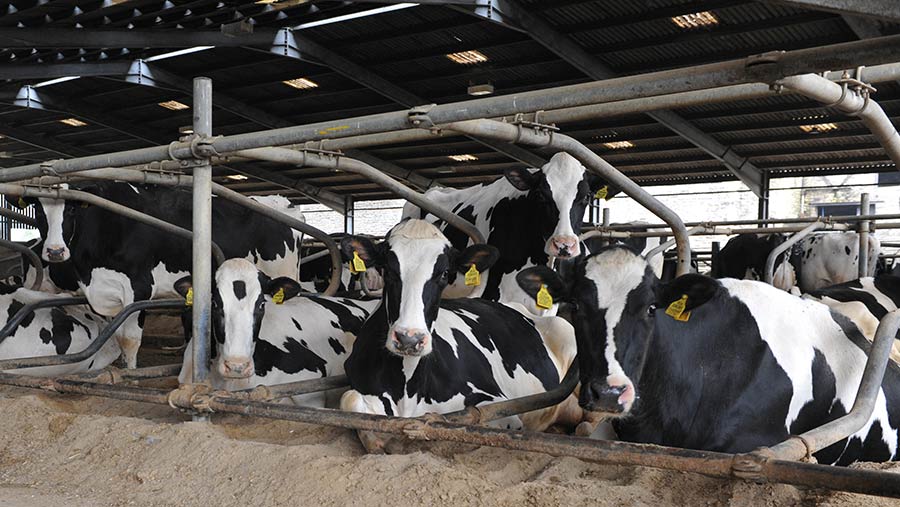
A separation system is allowing a Somerset dairy farm to remove sand bedding from manure to prevent settlement during storage and control what nutrients are spread on fields.
Alistair and Jill Hardwick had been using mattresses in combination with straw from their arable enterprise as bedding for their 350-cow high-yielding Holstein herd at Church Farm, Stanton Prior.
This policy changed in 2010 when they upgraded their cow housing.
See also: Slurry separation options compared
Farm facts: Church Farm, Stanton Prior
- 350 Holsteins housed year-round
- Average milk yield 11,500 litres on a level profile
- Average 3.85% butterfat and 3.2% protein
- Average cell count 120,000 cells/ml
- Farms 607ha (1,500 acres)
- Grows grass, maize and wheat
- Cotswold brash soils
The business had been operating from a shed built in the 1960s, but the dimensions were not compatible with the cow cubicles needed to get the best performance from the housed system.
“The cubicle design and ventilation were not appropriate for a modern system, so we either had to modernise or give up dairying,” Mr Hardwick explains.
The Hardwicks opted for a future in milk production and investigated a range of options with support from Tim McKendrick, a dairy husbandry specialist at The Dairy Group.
“We looked at all the possibilities and initially we thought we would carry on with mattresses and straw, because we had a good availability of straw from our arable operation,’’ Mr Hardwick recalls.
“Tim persuaded me that we should consider sand. After a while I came around to his way of thinking, and left the design to him.”
The shed has three pens of 100 cubicles under one roof, with deep-bedded sand in the stalls, and rubber matting in the feed passages to protect foot health.
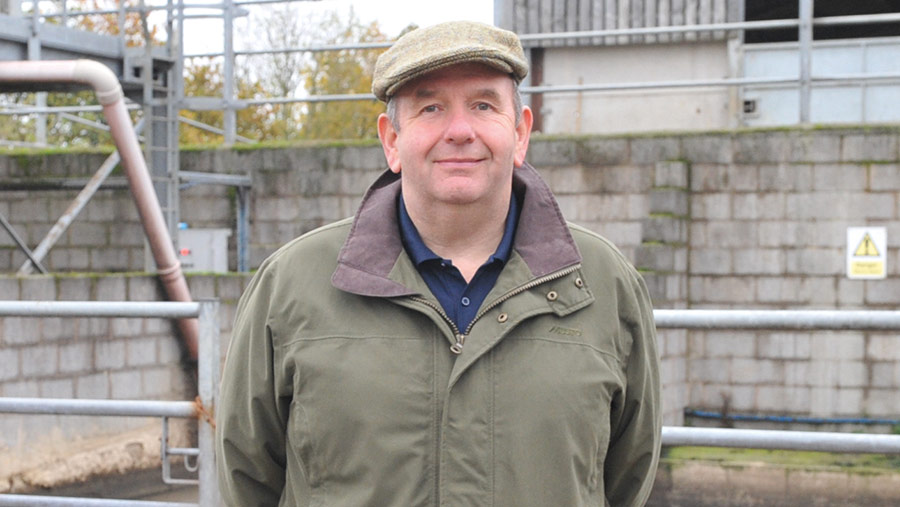
Alistair Hardwick © Debbie James
Sand separator
An important component of the design brief was to include a system that would separate the sand from the cow manure and liquids.
The high-yielding herd is fully housed and has a requirement for 5t of sand bedding a cow a year.
“Sand is perfect for cows to lie on and great for their wellbeing,” says Mr Hardwick. “But once the cow has finished with it, everything about it is difficult.
“We had to find a way of minimising those difficulties.”
The sand separation system at Church Farm is designed around a series of settlement lanes and tanks for storing liquid and the fibrous part of the manure.
All the waste passes over a separator manufactured by Sperrin, which cost £20,000 ex VAT.
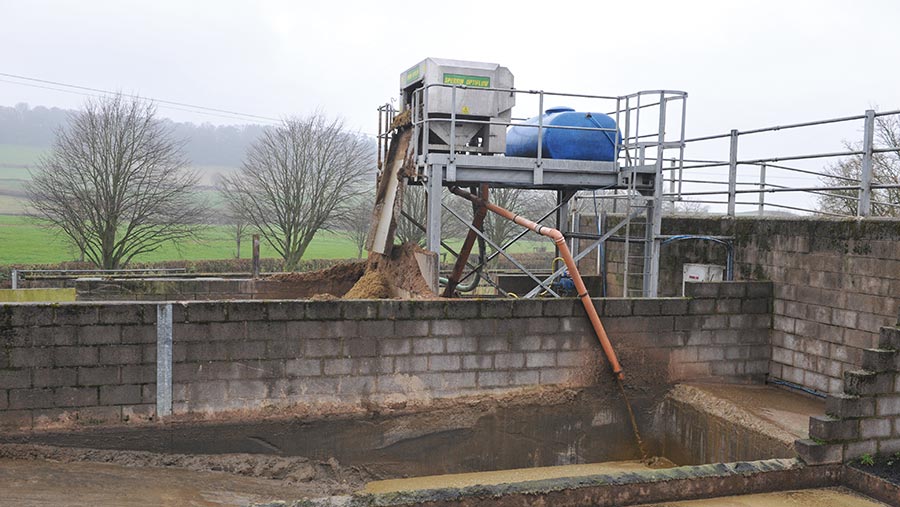
Stainless steel rollers separate the sand and fibrous material from the liquid component of the slurry © Debbie James
Separation process
Passages are scraped with a tractor and scraper and the waste is deposited in a slurry channel. Dairy washings are used to flush the slurry in the channel into a reception pit.
At that point, the waste passes over the separator; this is a simple piece of equipment with stainless steel rollers for separating the sand and the liquid from the fibrous material in the manure.
The sand and liquid drop into a three-lane settlement area, where they are kept moving by gravity.
“The material continually moves in a snake-like fashion and the sand drops into the bottom of the settlement lanes,” Mr Hardwick explains.
The separated water is stored in a circular tank and pumped into an above-ground store, ready for spreading on the land using either an umbilical method or a slurry tanker.
The wedge-shaped settlement lanes fill with sand every two weeks, at which point they are cleaned out. The manure is pumped out once a week because there is limited storage under the separator.
The sand and fibrous material are stored in separate areas and spread on the farmland when appropriate. The liquid has 3% dry matter and a high N content.
It goes into the slurry store and is spread via tanker or umbilical system on the grassland.
The fibrous part is mixed with straw-based manure from the youngstock housing, and the sand is ploughed into the maize ground.
It is the second separator that the Hardwicks have invested in since 2010. The first, manufactured by another company, used brushes as well as rollers and became unusable after nine years.
“From a maintenance point of view the separator we installed three years ago is much easier,” says Mr Hardwick.
“He opted for a roller-press separator for its durability and because it is a simple way of reducing the volume of the slurry going into the storage.
Replacement parts
Some farmers have abandoned separation systems because parts need replacing frequently, which is both expensive and inconvenient.
But Mr Hardwick says there is only one part in his setup that needs regular replacement.
This is the impeller component of the pump that moves slurry 4m from the reception pit to the above-ground tanks, and needs replacing four times a year.
While Mr Hardwick at first took some convincing of the advantages of sand bedding, he is now one of its greatest advocates.
Cow health
“Most people make the connection between sand and mastitis prevention, and that is very much the case. But from our point of view its major benefit is that it encourages the cows to lie down more,” says Mr Hardwick.
“Cows don’t get swollen hocks, so lameness has greatly reduced, cows stay cleaner, and since we built the shed we have only had one heifer that has refused to lie down in the cubicles.”
Mr McKendrick says research indicates that the softer the bed, the less chance there is of physical injury and damage to hocks and knees.
“Cows are happier getting up and down on sand and there is a benefit to feet, as cows slip less.”
The cost is competitive – sand averages about £18/t, but increased transport costs have pushed the current price to £24/t.
A downside of sand is that it is a finite resource. Unlike woodchip and straw, it can’t be grown and also takes its toll on machinery.
Recycling
At Church Farm, however, the end goal is to recycle the sand to reuse it as bedding.
“If it was straw or sawdust, we wouldn’t think of recycling it, but because it is sand it can be washed and reused,’’ says Mr Hardwick.
“Because we can reuse it, and some are showing it is possible to do so, why not?”
For obvious reasons the sand must be dried before being reused, and this has been the stumbling block to the Hardwicks investing in a high-cost recycling system.
“It works in systems in North America because the climate is different to ours,” says Mr Hardwick.
“We will hold off going down this route until we can see that is it being used successfully in our more temperate and wetter climate.