Comeback for self-emptying grainstore
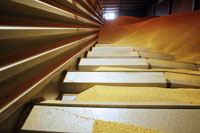
A high air-flow, self-emptying grainstore invented by a Cambridgeshire farmer more than 30 years ago is set for a comeback. David Cousins reports
Back in the 1970s, Fulbourn farmer John Lacey designed a grainstore lateral that went far beyond the usual drive-over type in use at the time. Instead of pumping low-volume ventilation air into the grain via mesh-type laterals set into the floor, he built a much bigger type with angled louvres along the sides.
A big fan forces high-pressure air through these louvres, blowing the grain towards the emptying conveyor and allowing the grainstore to self-empty very quickly.
Several hundred grainstores incorporating the Lacey Air Sweep system were installed in the 1970s. But though the system worked well, the complex, stepped shape of the laterals made them difficult to manufacture.
The result was that many collapsed and, allied to the increasing popularity of drive-over wooden floors, the system went out of favour in the 1980s.
But now, almost three decades on, the Lacey Air Sweep is about to make a comeback. A radically redesigned version – built as a co-operative venture by two UK grain equipment manufacturers, Devon firm Perry of Oakley and Pellcroft Engineering from Lincolnshire – was installed before last harvest on Mr Lacey’s farm.
It worked well enough that it is now planned to start marketing the system again.
“The Air Sweep principle was great but there wasn’t the equipment to make that sort of pressed steel lateral properly back then,” says Perry of Oakley’s sales manager, Mike Callaghan. “But now we have the equipment and the know-how.”
There’s certainly a place for them on UK farms, he reckons. While drive-over grainstore floors are quick to empty into, they can be a slow way to fill lorries even with a 2t bucket, he points out. And while good-quality wooden floors can last a long time, some cheaper versions need regular maintenance.
There is also concern that increasingly strict ACCS standards may in future not allow a loader to be used to muck out a cattle shed one day and be working in the grain store the next.
The 4000t grainstore at Mr Lacey’s farm, currently run by him and son Robert, is certainly a state-of-the-art affair, with the sort of high throughput and low labour requirement to make even a damp 2008-style harvest stress free.
Grain comes in from the reception pit to an aspirator cleaner – or rather two 60t/hour aspirators joined together to give a massive 120t/hour throughput. This takes out field rubbish like chaff, straw and wheat heads.
The corn then passes along a central 120t/hr conveyor at the top of the store, before a tripper turns it through 90Âş into a cross-conveyor. Small electric motors at each end, plus a third on the tripper, move the whole cross-conveyor backwards and forwards along the store.
The conveyor has no bottom and corn keeps flowing until it has bridged the width of the store. At that point it moves forward 200mm and the filling process begins again.
Emptying is done at the push of a button. Normally, two 60kW fans would provide airflow for the louvres, but the farm’s electricity supply wasn’t up to that. So, instead, a 82,000cu ft/min Pellcroft Typhoon fan, driven by a substantial 150hp Deere engine, provides the air.
There are control slides between the laterals and to empty the store, up to three can be opened at any one time. Air then flows through the central ventilation tunnel under the bottom of the store and into the laterals.
This high-volume air blasts out of the louvres on the sides of the laterals, pushing the corn out of the store at a rate of 60t/hour to each side of the store. While that rate of fill would keep any lorry driver in a hurry happy, there’s also a 35t hopper for ultra-fast truck-filling.
At harvest time the big fan also serves to push high-volume air through the corn to cool it and reduce moisture content. So far, no extra source of heat has been needed (other than that from the engine) but Mr Lacey says a Harvest Installations-type LPG burner could be used as a top-up source of heat.
This layout is not the cheapest option, says Mr Callaghan, but uses almost no labour.
The total bill for the equipment came to about ÂŁ220,000, including ÂŁ23,000 for the fan and engine, ÂŁ28,400 for the main ventilation tunnel, ÂŁ34,800 for the laterals, and ÂŁ5000 for the pre-cleaner. The installation costs are not included.
However, the phenomenal throughput, almost total lack of labour requirement and sheer flexibility mean that it could be an appealing prospect for many big farmers.
Mr Lacey points out that this design has lots of advantages over conventional stores.
For a start, it can be partitioned, allowing grain to be taken from any section of the store, cleaned and put back. That could be very useful if you were wanting to deal with mites or take out weed seeds, or simply needed to move corn from one area to another.
It can also deal with small seeds, such as rape, that would fall through the ventilation gaps in conventional wooden floor systems.
“It’s certainly a high-specification set-up,” says Mr Callaghan, “and 120t/hr is more throughput than some commercial stores have. It’ll handle two big combines and there’s no grainstore labour involved.”
Lacey Air Sweep
• No wooden floors to maintain
• Can accommodate small seeds such as rape
• Crops can be taken from one section, cleaned and put back again
• Quick to fill and empty
• No danger of telehandlers bringing mud and muck into the grain store
• High air-flow combined with heat from engine reduces need for extra heat
• Low dust levels
• High throughput – ÂŁ120t/hour in and out of the store. So lorries are filled quickly
• Very low labour input
• code123