Two options for levelling your yard this winter
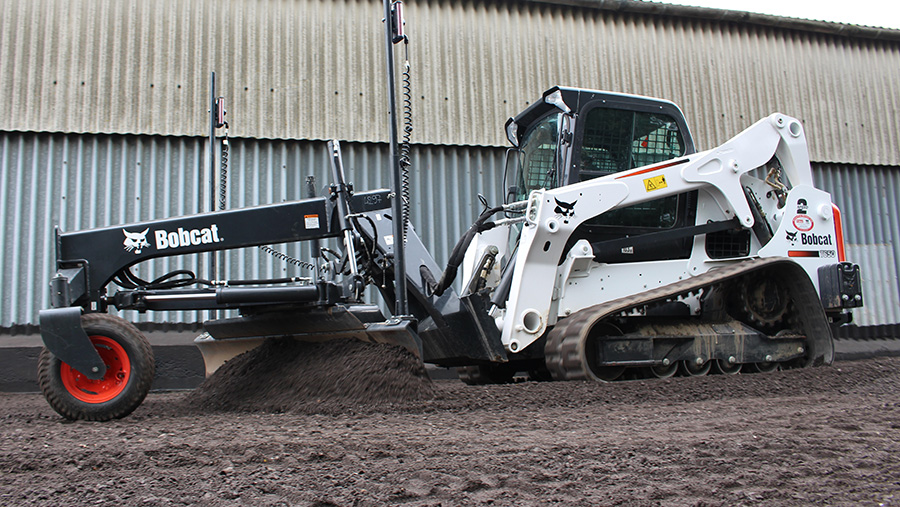
Laying a few road planings and pushing them around with a digger might keep you busy for a few winter days, but getting it done professionally to laser accuracy could see the last of that pothole-ridden yard for good.
We looked at how two companies are using different methods to save both time and money in the long term.
NF Services
Groundworks contractor NF Services is using a brace of Bobcat laser-guided graders to guarantee millimetre accuracy across large sites and slash outlay when spreading costly materials.
See also: A guide to fixing pothole-ridden farm tracks
Company owner Nick Foxton used to employ a 360deg digger to spread and level multiple materials on the yards and horse manèges his groundworks and fencing company tackles throughout east England.
However, the steady progress and requirement for highly skilled operatives along with the less-than-accurate spreading meant that jobs were taking longer than budgeted for and becoming costly.
He bought his first laser grader – a 2016 Bobcat machine – second hand in 2018, having never seen it work in the flesh.
However, he was convinced from watching multiple YouTube videos that it was the solution to upping work rates and precision.
When it was delivered, Mr Foxton admits it was a sink or swim moment as he had limited experience driving Bobcats, and getting the grader to work with differing levels across the site took some initial head scratching.
However, very quickly he realised the output from these little tracked machines made such an improvement that this year he bought a brand-new Bobcat 650 with a heavier duty blade to work alongside the older machine.
These graders can lay just about any material, including sand, gravel, road planings and soil.
Laser levels
The two Bobcats can work together on the same area if space allows, although typically one machine will grade, while the other ferries material with a bucket.
The grader runs from a Trimble Spectra theodolite base station and has two receivers for each side of the blade mounted high out of the way.
The laser can be set up to grade sites with dual falls, meaning a datum taken from a top corner can be set to fall away into a bottom corner, taking in two different levels.
For horse arenas, the graders can lay the subbase with a fall for water run-off with any subsequent drainage layers finished level.
Once the level from the datum point has been married with the base station height, the gap between the floor and staff height is then replicated on the grader from the bottom of the blade to the receiver on the mast above.
Levels can either be tapped into the Spectra unit or the screen inside the Bobcat 650. There is a readout for each side of the blade with errors clearly flashing up when one receiver isn’t working.
These sensors are linked to the machine via a Canbus system and blade height tweaks are adjusted continually as the machine moves around.
The machine’s hydraulics form the slowest part of the system as they keep up with constant laser tweaks. The blade is connected via two rams, one on either side, which act independently from the two-front wheel.
The sensors also have 360deg vision, so they can receive signals all the time, which doesn’t alter when the Bobcat is facing away.
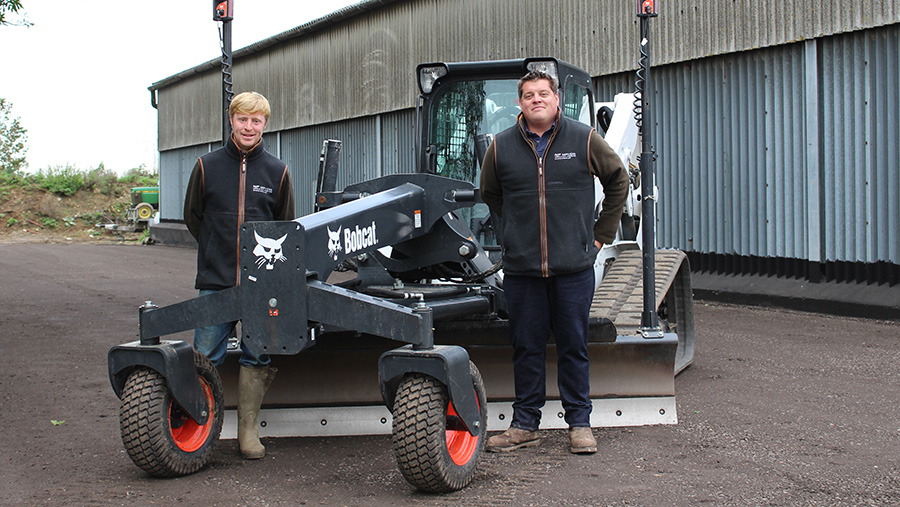
Harry Anderson and Nick Foxton at NF Services with the Bobcat 650 leveller
Work rates
The benefits for Mr Foxton have been huge, with a 50% saving on works due to the increase in speed and accuracy that the Bobcat has enabled.
He says as road planings cost around £1.50sq/m, laying them too thick across large areas has a big impact on a customer’s wallet.
One machine is able to cover around 3,000sq/m per day, depending on the product. Mr Foxton says he tries to tip material as close to the area as possible, as shifting product is the slowest part of the job.
With the millimetre adjustment from the cab, operator Harry Anderson can work in stages, bringing levels down to the required height. He has even been able to grade soil on banks when building bunds and push clay around when marking out sites.
Mr Foxton says that the tricky part with these machines is corners, as they aren’t that nimble when working in close quarters with fences and barns.
To help, the blades have sideways shift to help access tight spots but sometimes a few minutes with a shovel is just as quick.
As for cost, Mr Foxton was keen to point out that variables such as different levels, subbase construction and multiple materials will all affect end cost but as a rule of thumb, prices start at £1.20sq/m for laying road planings or hardcore.
Larc Construction
Leicestershire building firm Larc Construction has bought a German grading machine to guarantee groundwork accuracy on large construction sites.
On the back of securing a large contract to build 176 luxury holiday lodges near Padstow in Cornwall, business owners James Crisp and Josh Lee were faced with an unenviable task.
They had to lay thousands of metres of haul roads, gravel drives and build oversite along with car parks and tennis courts to top-notch standards.
Having only ever used 360deg excavators for this type of work before, they knew that to get the contract completed on time they would need something that could speed up this steady task.
They also wanted to provide the company with a new income when the machine wasn’t needed in Cornwall.
They bought a Probst PowerPlan screeding machine, which looks rather like a mini tarmacking machine.
A four-cylinder 25hp diesel engine provides the grunt and as it is under 19kw, there are no restrictions when working in environmentally sensitive areas.
It’s also very frugal on fuel and only uses 35 litres in an eight-hour shift, which is around 500% more efficient than equivalent dozers and large excavators.
The hopper holds 2.5cu m and can be filled on the go from either the side or the front once the operators are up to speed, but currently this is the slowest part of the job.
At the bottom of the hopper, there are two metre-wide trap doors that can be operated individually, giving half-width shut-off in tight areas.
As the material falls onto the ground, an initial levelling blade takes it down to the pre-set height with a following blade set to the required fall or angle.
It can lay anything from sand to type 1 hardcore, 75mm stone or even semi-dry concrete and can work to a single fall on large areas but can make a roadway fall away to both sides.
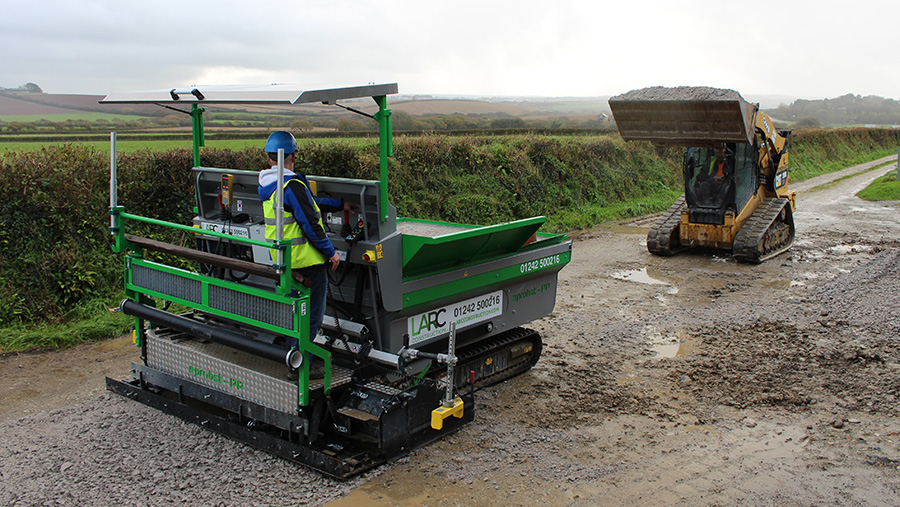
The Probst PowerPlan screeding machine
Levels
The Probst can work from a number of levelling options.
It has a sonic system, which follows contours of the existing ground – for instance, if you were laying material on top of a track, it can apply an exact thickness of material in relation to the current levels.
These sensors are on extendable arms and can work out to 6m away from the machine, so they have the option to follow curb heights or a string line to retain exact depths.
To set the machine working with sonic laser, a patch of material is laid out and screened to the correct depth.
The machine reverses and lowers the blade on the patch until it is on the area and by doing this, the depth of material is set. The blade has hydraulic rams on both sides to adjust to changing levels.
The second option is a laser level system working from a base station. This works by having two receivers on each side of the machine to raise and lower the blade depending on falls and depths required.
Output
A figure of 3,000sq m per day was quoted by Larc Construction, but this output will easily be impacted when material has to be ferried from a small distance to the hopper.
As for cost, the Probst machine with three operatives plus a loader and roller comes in around £1.50sq m, but is dependent on site restrictions and material.