FW Inventions Competition 2022: Peter Williams’ bale chaser
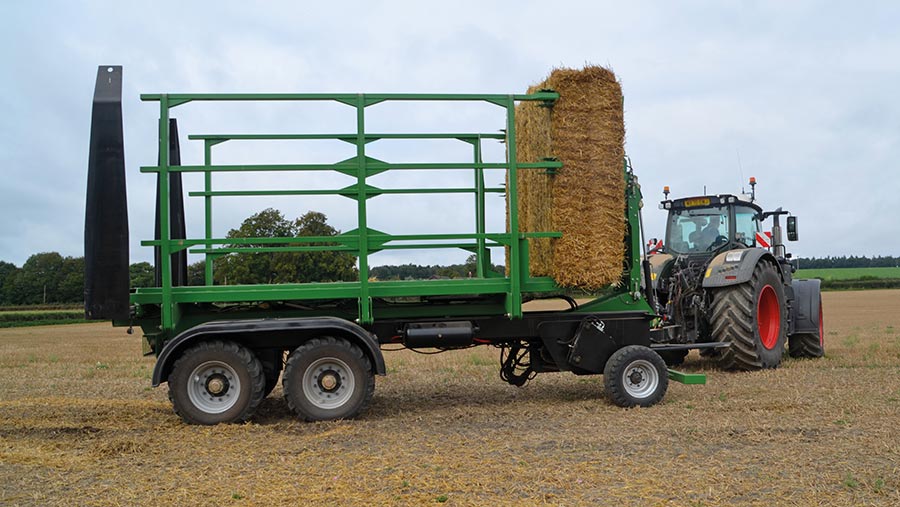
Peter Williams is our winner in the complex category in the Farmers Weekly Inventions Competition 2022, with his bale chaser.
Keen to streamline his big-bale handling operations, Wiltshire farmer and contractor Peter Williams built a state-of-the-art chaser that rotates alternate rows for a more stable stack.
Prior to this he used a squeeze trailer – also built in the farm workshop – that allowed stacks of 14 bales to be picked up and moved in one.
This worked well, but increasing pressure to clear fields faster sent him in search of a speedier alternative.
See also:Â Aussie contractor converts old bin lorries to bale chasers
His solution was to build his own chaser which, unlike conventional models that stack bales in the same orientation, alternated each row.
Much of his work is on sloping ground on the southern edge of Salisbury Plain, so he felt this was essential to give them enough stability.
It was no easy task, but he eventually devised an ingenious hydraulic arm and grab on the front that can pick up pairs of bales, load them straight or turn them 90deg, and then deposit them on the bed.
Each row of bales is shunted down the trailer by the arm and gripped tight by a pair of hydraulic gates at either side. Once full, the chaser heads to the stack and tips the load, just like a conventional model.
Air suspension helps give a smooth ride while bouncing over stubbles and allows the machine to self-level as the load changes.
The sheer number of moving parts called for an elaborate hydraulic system. This runs off the tractor’s load-sensing line and has sophisticated Canbus wiring to reduce the amount of cabling.
Opting for a setup like this means all functions can be controlled via an electronic joystick mounted on the tractor’s armrest.
This was a complex job, so freelance control systems engineer Tom Bradbury was drafted in to help put it together.
Mr Williams says the rig can shift about 80 bales/hour and he reckons this could be increased to 120 if he enlarges some of the pipework to improve hydraulic cycle times.
The machine was built entirely from scratch, and he used CAD software purchased from PC World to help get the plan together.
He largely taught himself to use it, but did have some help from retired engineer Tim Stangle.
Putting the design together virtually allowed him to work out all the angles, ram lengths and geometry, and generate drawings so that he could get the metal laser cut.
The ambitious project took him six years to complete.