Big baler innovations could help farmers cut costs
The latest batch of big square balers are packing even more straw into a heavier bale, which not only drives down the cost of baling, fewer bales also cuts down on road transport costs.
Baler operators can push on with greater confidence using aids that help them hit peak outputs and ensure the chamber is packed evenly.
Add heavier duty drivelines and feed-in systems plus tougher knotters, and it all adds up to major gains for farmers and contractors taking straw off arable fields.
See also:Â A guide to AD digestate applicators
Case IH
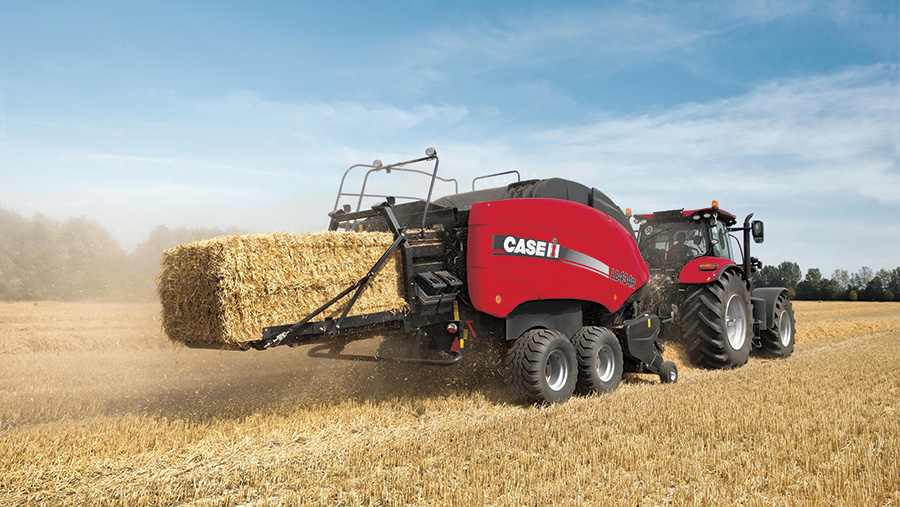
Isobus electronics on the 120x90cm LB 434 and other models in the Case IH range provide auto tractor speed control among a suite of features
A new control function on Case IH LB big square balers not only regulates the speed of the tractor along the swath, but can also be used to ensure consistency in the number and size of slices in the bale.
These features are available on the Case IH LB 424 (120x70cm) and LB 434 (120x90cm) balers, which are the two largest of four models in a range that also takes in a pair of baler producing 80cm wide bales either 70cm or 90cm deep.
The two 80cm machines are available with a plain tine packing system or with fixed knives in the base of the intake throat, as well as a helix rotor intake with selectable knives for slicing the incoming material.
Bales are tied off with a double knot arrangement in all cases after material has been accumulated in the pre-compression chamber until a pressure trigger has been released to mobilise the stuffing mechanism transferring material to the main chamber.
Connecting an Isobus virtual terminal to the baler brings up the control and monitoring screen, which provides left-right steering guidance for even filling, warnings of failed knots and sheared safety bolts, and signals when each bale is dropped.
The latest additions these functions, which requires Isobus software to the same level as on the balers, is tractor speed control.
On non-cutter versions LB 424 and LB 434, the system works in slice control mode only, regulating forward speed in relation to the volume of material in the swath to deliver a consistent number of wafers in each bale.
This can be important to some end users in terms of handling and dispensing straw once the bale has been opened.
On RotorCutter versions, on which 15 or 29 knives can be deployed beneath the 1.2m wide helix intake rotor, the baler can also be operated in charge control mode with tractor speed then varied for optimum output by using sensor paddles to measure both the throughput of crop fed into the pre-compression chamber and the time taken to fill it.
Either way, auto-tractor speed control helps the operator optimum performance and/or bale structure regardless of swath variation or fatigue during a long working day.
Other recent upgrades include a reinforced pick-up, optional castor support wheels, improved knotter cleaning fans, and individual knotter monitoring to help operators more quickly rectify miss-tie problems.
Claas
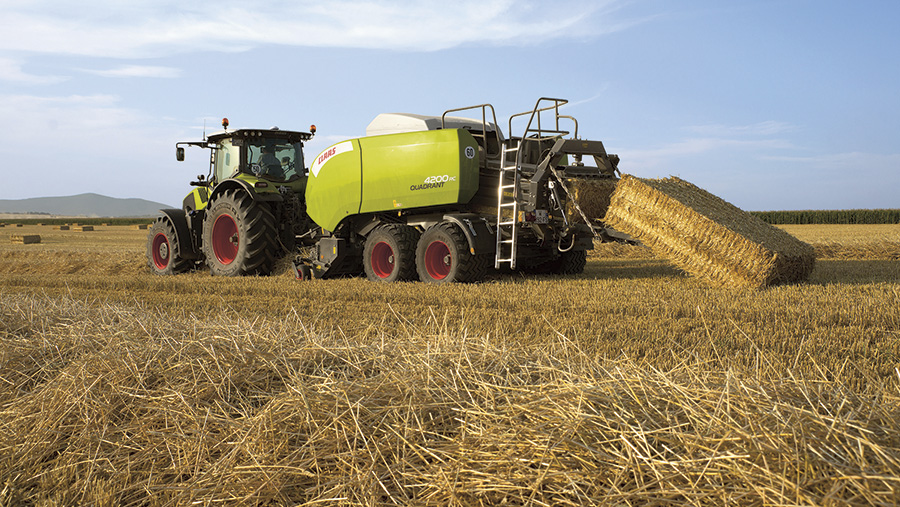
Claas Quadrant 4200 has replaced the 2200 with 10% faster plunger speed and options including hydraulic front-end drive, automatic pressure control and individual monitoring of the redesigned knotters
Longer bale chambers, stronger knotters and a new automated density control system combine to help operators work faster and pack more material into each bale from the new Quadrant 4200, 5200 and 5300 balers.
These replace the 2200, 3200 and 3300 models, respectively.
But those are just some of a host of upgrades designed to boost output from the machines, which all make bales 120cm wide; the 4200 and higher-spec 5200 build bales 70cm deep, while the 5300 produces 90cm deep bales.
These top-end balers are in a range that also includes the 80x50cm hay baling Quadrant 4000 at one extreme and the 120x100cm 3400 at the other, along with the 80x70cm Quadrant 2100.
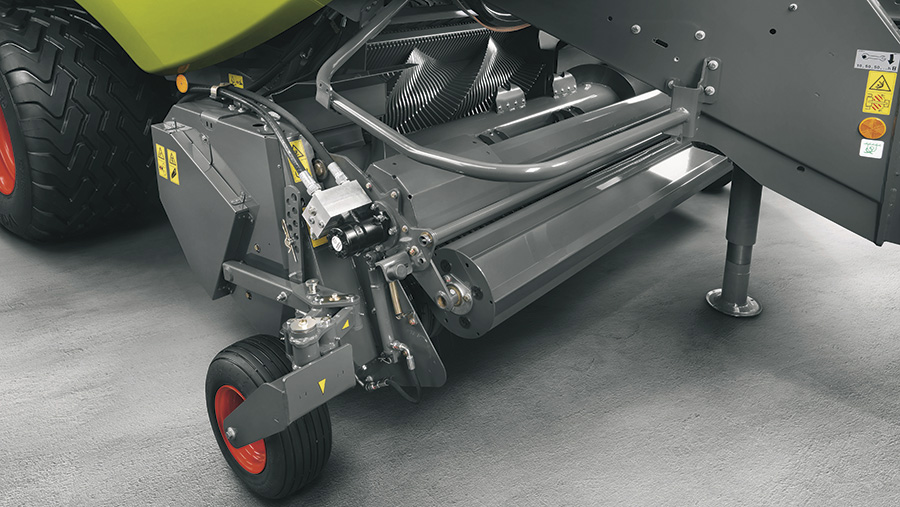
Reversible hydraulic drive adjustable between 200-260rpm for the pick-up reel, upper of two crop press rollers and the power-feed roller/auger intake rotor is a first for the Quadrant
The newcomers are available with plain RotoFeed intake rotors or the crop slicing RotoCut version, with a 51-blade FineCut unit – which may be of interest to anaerobic digestion plant operators wanting finer material – and a SpecialCut flail option also available on the 5200 and 5300.
In each case, a 2.35m pick-up with hydraulic suspension and double-roller crop press gathers the swath and this can now have hydraulic drive to the reel, top crop press and power feed auger/paddle rotor.
Apart from the last two elements being reversible to help clear a blockage, the new option allows front-end speed to be fine-tuned between 200rpm and 260rpm for either gentle handling of delicate crops such as Lucerne or to match a fast forward speed along a thin swath.
Plunger speed on the 4200 is 10% up from 2200 at 56 strokes a minute to allow faster working speeds, and while the 5300 has the same 46 strokes a minute, it gets a 13% faster rotor and increased rotor clutch and packer clutch torque limits to raise its packing potential. In addition, all models get up to 15% longer bale chambers.
Claas has redesigned its own knotter assembly to make it stronger and easier to service, retaining the single-knot per twine and introducing more powerful fans with oscillating deflectors to keep the area clear of debris.
A new approach to density management is introduced with the automatic pressure control (APC) system, which uses sensors on three of the knotters and to detect flexing of the front beam as a measure of stress on the driveline.
The APC software will then regulate pressure on the chamber to hit the target bale density entered by the operator into an Isobus control terminal along with the twine strength, with a display on the terminal confirming its abilities.
APCÂ is standard on the Quadrant 5200 and 5300 balers, optional on the 4200, and that also applies to a new knotter monitoring system that alerts the operator to a broken string or miss-tied knot.
John Deere
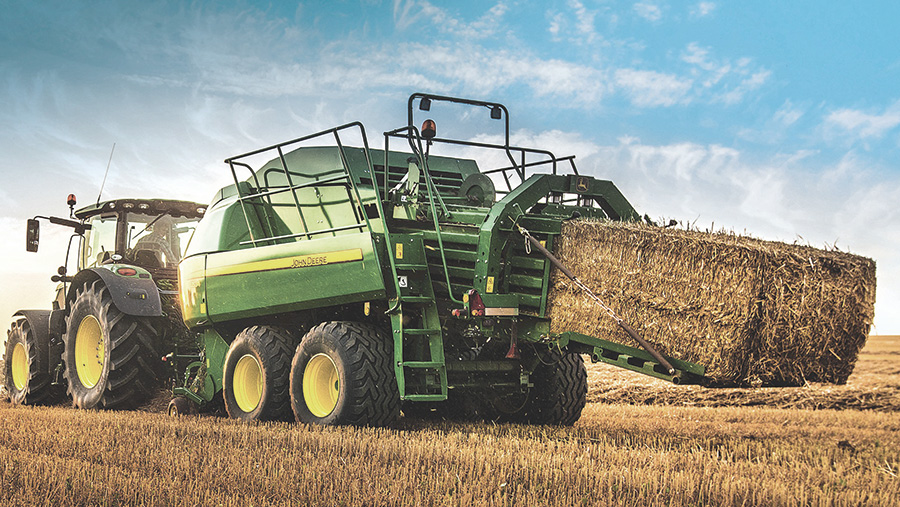
This 120x90cm L1534 MaxiCut HC is the largest baler in the John Deere range, produced in co-operation with
Kuhn © John Deere
A simpler driveline with fewer components resulting in lower power losses feature on the two L1500 series balers that, together with the 120x70cm 1424 from the previous line-up, constitute the John Deere range in the UK.
Both of the newer machines are available in plain RotaFlow HC and crop slicing MaxiCut HC form, the latter deploying up to 15 retractable blades on the 80x90cm L1533 and up to 23 on the 120x90cm L1534.
They work in conjunction with a helix feed rotor that incorporates solid spiral end sections to bring wide swaths down to the width of the pre-compression and main chamber.
A 670mm diameter flail chopper can be added to the front of the machine if a finer cut is needed.
A double knotting system was chosen as standard equipment on the L1500 series machines to relieve stress on the knotter mechanism while producing high-density bales under manual or automatic chamber pressure management.
Two high-capacity turbine fans have been adopted from John Deere combines to keep the knotter area clear of debris by providing a strong airflow, while a sealed twine box carries up to 30 balls in a single row for easier handling, routing and string tying.
With Isobus electronics installed as standard, the balers can be operated by touch screen or button control on any compliant terminal, with most adjustments, such as bale length and density, knife activation and greasing, as well as knotter monitoring all operated on screen.
Krone
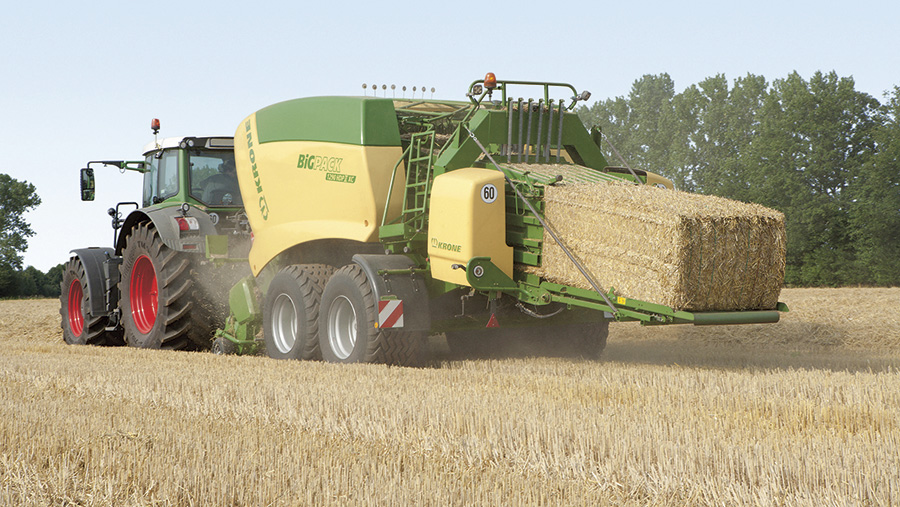
Latest addition to the Krone BiG Pack range, the 1290 HDP II, is said to be capable of delivering 50-70% more throughout than the first-generation high density press or up to 10% greater bale density © Bernard Krone
Among Krone’s comprehensive BiG Pack square baler range, the 120x90cm 1290 HDP II is the new addition with promises of significant increases in output and density.
Krone already builds two machines with these bale dimensions, the regular 1290 and the 1290 High Density Press producing up to 25% heavier bales, each with six double knotters.
The HDP II has entered the arena with eight double knotters – kept clear of debris by a fan in addition to the usual compressed air blast – and other hardware upgrades to deliver a further 10% increase in bale density and 50-70% higher throughput.
Hydraulic start assist is a feature common to all BiG Pack balers, and in the case of the 1290 HDP II it gets a flywheel increased in weight to 608kg rotating before the tractor pto takes over and an intermediate gearbox increases its speed to 1,180rpm.
The V-tine rotor in the intake area behind the 2.35m wide pick-up – which has cross press and feed rollers as standard – has been increased in diameter from the 550mm of the other models to 720mm for the new machine.
On the XCut version, this rotor can be used with 13 or 26 crop slicing knives that automatically retract of there is excessive slip at the powerband that drives the rotor or if the pre-compression chamber becomes blocked.
Along with the entire driveline, components in the variable fill system rotary accumulation and stuffing mechanism have been strengthened to match the baler’s increased capability: the three sets of packer tines are reinforced and there are larger cam rollers for the feeder arms.
Six hydraulic cylinders bear down on the bale chamber – two on each side and two on top – to achieve higher densities and a bale weighing system, with claimed accuracy of +/- 2% can be built into the discharge ramp.
The newcomer joins a BiG Pack range that includes 80x70cm, 80x90cm, 120x70cm and 120x130cm balers, with novel Multibale versions of the BiG Pack 870 and 1270 capable of producing up to nine tied-off sections within a full-size bale for easier end-use distribution.
Kuhn
A novel plunger designed to increase bale density by up to 25% without the need for a heavy-weight driveline features on the latest addition to the Kuhn LSB range.
The LSB 1290 i-Density produces 120x90cm bales using much the same intake and double knotting processes as the regular LSB 1290D.
But the newcomer’s plunger is divided into separate top and bottom sections attached to the gearbox by Y-shaped connecting rods in a way the creates two impacts on the contents of the bale chamber.
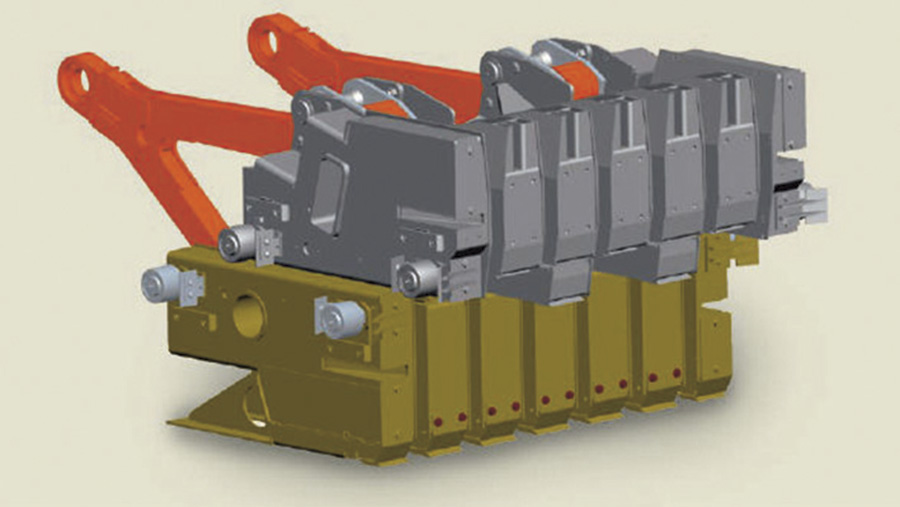
Increased bale weights without having to substantially upgrade the driveline are claimed for the i-Density version
of the 120x90cm Kuhn LSB 1290
Despite being capable of producing up to 25% denser bales, the TwinPact mechanism imposes a load on the driveline comparable with the regular model.
The Kuhn high density baler tops a range that covers all the common bale sizes from 80x70cm bar the very largest and includes the LSB 890 with the unique facility to produce 80cm wide bales either 80cm or 90cm deep.
All are produced with plain or crop slicing intakes featuring a 600mm diameter helix intake rotor with bolt-on replaceable tines and auger end sections to gather wide swaths.
A single row of tines feeds the pre-compression chamber and transfers material up into the main chamber with a longer stroke once pressure plates in the top of the pre-chamber have been tripped.
The 80x90cm and 120x90cm balers are available with single or double knotting – the former using a mechanism to reduce twine tension on the knotter as the bale is formed – and there is storage for 24 balls and 30 balls of twine, respectively in sealed cabinets that swing out for service access.
Massey Ferguson
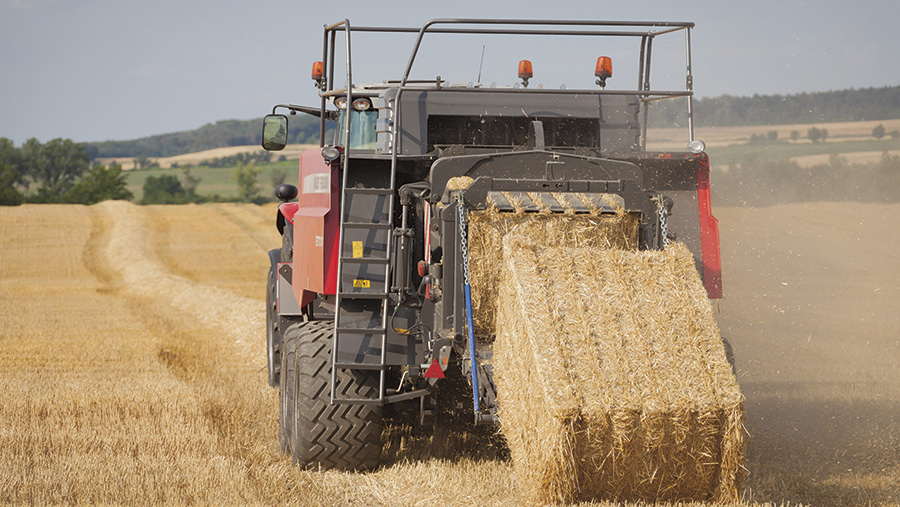
A heavier flywheel and 17% longer bale chamber contribute to the higher bale weights achieved by the ‘XD’ version of the 120x90cm MF 2270 baler
A crop-slicing system for all but the biggest baler in the Massey Ferguson 2200 Series helps maintain high bale weights and provides end users with a looser material for bedding cattle and other applications.
The ProCut system comprises a 650mm diameter rotor with replaceable finger sections arranged in a V-formation installed in place of the three-stage tine rake of the Packer version.
Crop-slicing models keep the four short augers positioned either side of the intake to draw in wide swaths and have a cassette-type knife bank with hydraulic selection of two sets of knives that can also be withdrawn altogether.
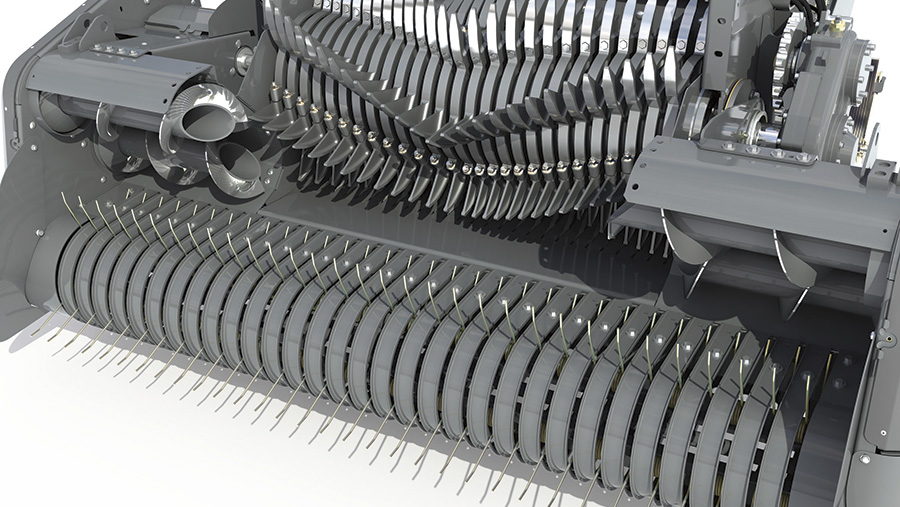
New ProCut versions of the MF 2200 series balers get a 650mm diameter intake rotor with replaceable finger sections arranged in a V-formation and selectable sets of crop-slicing knives
Like other big balers with this type of cutting system, the cassette can be lowered and slid out to one side when knives need to be sharpened or replaced.
ProCut is available on the 80x70cm MF 2240, 80x90cm MF 2250, 120x70cm MF 2260 and 120x90cm MF 2270 balers, all built in Agco’s Hesston factory in Kansas, US, as well as the higher density version of the latter machine, the MF 2270 XD.
This model has a 91% heavier flywheel – weighing 545kg – to create additional inertia and maintain the momentum needed for a 15-20% increase in bale density over the regular model.
To cope with the extra stresses, the baler also has a stronger gearbox and mountings, and the larger crank arms and bearings from the 120x130cm MF 2290 – the biggest machine in the MF range – which also shares its OptiForm bale chamber design with the XD.
This includes side pressure doors that are 17% longer than on the regular MF 2270 and curve inwards to multiply the effect of the two double-acting hydraulic cylinders.
These work through crank arms to apply resistance to the side and top panels but on the XD require less hydraulic pressure.
Bale density is regulated automatically by the baler’s Isobus-compliant electronics, using load cells that measure the force on the plunger face to calculate adjustments and also provide the operator with left-right steering guidance when working along a narrow swath.
New Holland
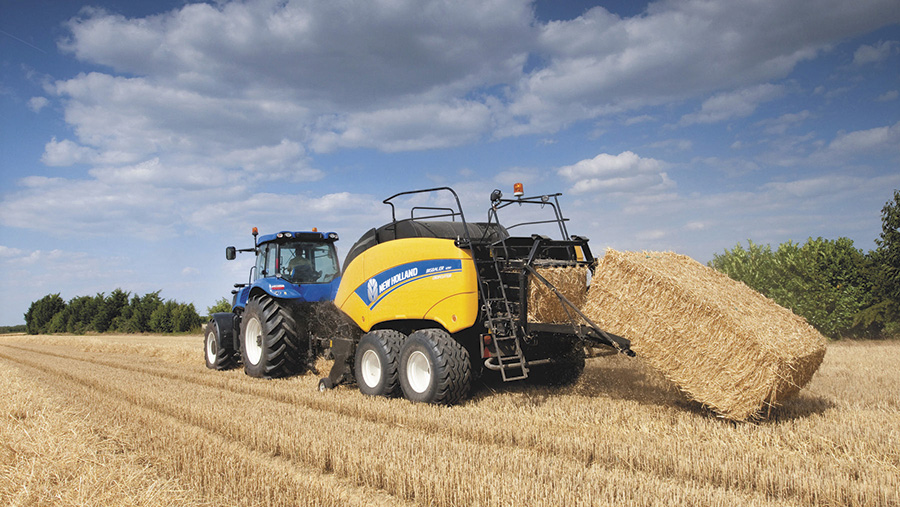
Faster working speeds along the swath for increased output and daily capacity, and bales up to 5% heavier than before are
claimed for the New Holland BB1290 and other models in the BigBaler range compared with their predecessors
When the European-built New Holland BigBaler range was introduced, it heralded a wholesale package of upgrades over previous models.
These include a heavier duty gearbox and larger diameter flywheel with direct drive from the tractor pto generating up to 48% more energy to compensate for uneven swaths.
Coupled with a 14% increase in plunger speed to 48 strokes a minute, the changes brought about faster working speeds along the swath for increased output and daily capacity, and bales up to 5% heavier than before.
The comprehensive BigBaler range comprises 80x70cm and 80x90cm machines with packer tine intake – either plain or with knives in the base of the channel – and 120x70cm and 120x90cm machines with packer tines or a spiral intake rotor with selectable crop slicing knives.
This can also be specified on the smaller balers.
The stronger, more durable MaxiSweep pick-up reel of all these balers has 6mm tines as standard, a chain-driven feed assist roll situated behind the roller windguard, and gathering augers to bring wide swaths down to intake width.
An improved pre-compression chamber with crop flow sensors gives the operator steering advice if necessary via an Isobus virtual terminal in the tractor cab.
Isobus also provides automatic driving speed control to either optimise output of rotor intake CropCutter versions along variable swaths or on all versions to regulate the number of slices in each bale to meet end-user requirements.
The filling process uses stuffer forks to accelerate the crop from the feeder tines or rotor into the pre-chamber, which is filled uniformly until the required density is reached, at which point a trip sensor activates the C-shaped shuttle to move the crop wad into the main chamber.
A double-knotting system minimises strain on the knotters and twine while each bale is being formed, with sensors providing a miss-tie alert on the tractor terminal, and debris is cleared by three fans, plus a variable interval compressed air blast if needed.