Combine headers from Biso and McDon aim to push up harvesting efficiency
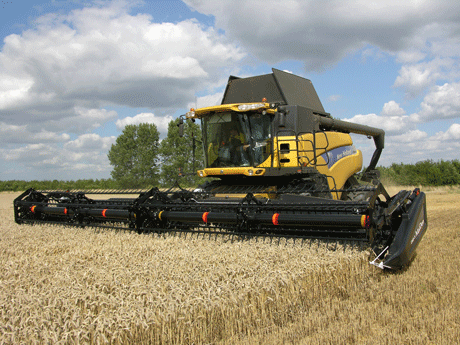
One of the more surprising things about combines is while their ability to thresh grain from a crop has increased dramatically over the years, the design of the header has remained virtually unchanged.
Yet, as any operator knows, it’s the header that dictates the volume of crop entering the combine. So, for much of the time, your combine is probably not working at full output simply because the header can’t pull in sufficient volume of crop to give an even, lump-free feed.
There have been several attempts by manufacturers to improve matters, the most notable being Massey Ferguson’s PowerFlow table which has a full-width rubber conveyor belt to take the crop straight up to the table auger.
Others, such as Claas and John Deere, have used removable plate inserts to extend or decrease the distance from the knife to the auger, eventually producing designs that let you to alter the knife-to-auger distance hydraulically at the press of a button
All of which is fine but doesn’t, perhaps, meet the problem head on, with the result that a number of companies have designed headers that potentially do a better job.
This year has seen the Canadian-built MacDon header in action for the first time in UK crops and the new Austrian Biso header has also made its debut appearance here.
MacDon
The D60 header, marketed in the UK by Shelbourne Reynolds, claims to provide a seamless flow of cut crop to the threshing drum and thereby increase throughput and harvesting efficiency.
A 10.5m version attached to a New Holland CR9090 working on a Velcourt-managed 2400 ha (6000 acre) estate at Tilney All Saints, Kings Lynn, Norfolk appeared to confirm these manufacturer’s claims.
The header uses two conveyors to take the cut crop to the centre of the table where a third conveyor set at right angles feeds the crop to the intake auger and into the elevator.
The conveyors are made from rubber-coated drapers, with a reversible V-guide for tracking and a seal on the leading edge.
To allow tall crops such as oilseed rape to be handled, a small-diameter auger is positioned on the top edge of the rear of the header to help move the crop to the intake.
MacDon’s 10.5m D60 draper header has been working in a wide variety of crops in the UK and the results are said to be good with increased output.
On the header itself, two following wheels form part of a suspension system and allow the header to float. They also pivot laterally so ground contours can be followed.
According to Shelbourne’s Neil Smith, the MacDon has worked well in a wide variety of crops and conditions and operators have reported an increase in output – although there are no direct comparison figures to support this.
“We are very pleased with it – the only modification will be an extension of the top auger so that it moves crop from the whole width of the header rather than starting a metre in from the ends of the table,” he says.
Biso
The new 12m Biso Ultralight 800 header marketed by Abrey & Son arrived in the UK a bit too late in the season for it to make a major impression but it has been widely tested in other European countries.
The striking thing about it is the effort that has gone into keeping the weight of the header to manageable proportions.
Aluminium castings form the main structure and keep overall weight down to just over 4t for the 12m version. And because the outer part of the header is made from 1.5m sections, 10.5m, 9m and 7.5m versions will also be available.
Other features include an extending cutting table which can alter the distance from the knife to the auger up to 60cm so different crops and conditions can be catered for. There’s also a gleaming stainless steel table auger which is driven mechanically from both ends of the table, and a split knife drive which sees two overlapping knives being driven from opposite ends.
In the centre of the table where the knives overlap by about 30 cm, special fingers are used with wider-than-normal gaps to allow the two knives to pass through them.
In the sails department, a control box automatically ensures they cannot be lowered to a point where their tines catch in the knives, irrespective of how little or far the table has been extended.
Biso’s 12m header weighs just four tonnes due to extensive use of aluminium castings in its main frame. An 80cm extending table floor allows on-the-move knife/auger distance adjustment to help accommodate different crop conditions.
The whole table can also be pitched forward to increase the angle at which the knife fingers present themselves to the crop.
And finally, a feature most operators will really appreciate – integral side knives that can be brought into use at the touch of a button or folded away again just as quickly when they are not required.
“It all adds up to an efficient header system that could make a significant contribution to a farm’s harvest by reducing time,” says managing director, Toby Abrey.
Such inventiveness – both of the Biso and the MacDon headers – does not come cheap or, for that matter, with the blessing of combine manufacturers who would clearly prefer to sell their own headers.
The reality is sales of alternative headers are likely to remain low for reasons of cost and manufacturer pressure.
On the brighter side though, their presence in the market should make those who design and build combines look a little harder at header design. Because if the crop doesn’t get in to the combine, the best threshing system in the world will not be fully employed.