VIDEO: Individual nozzle shut-off comes of age
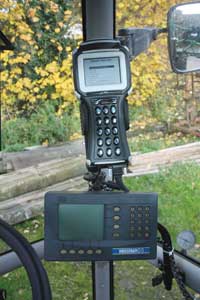
It’s rare that a new sprayer is sold these days without some sort of boom section shut-off feature. But, useful though this may be, it’s only as accurate as the size of the section. And since up to 12 nozzles can be included in any one section, classic V-shaped patches can occur all too easily.
So why can’t the same technology be used to shut off individual nozzles instead?
See our video here
“The big issue with individual nozzle shut-off is that there are few controllers that can deal with more than 32 separate sections. And on a 24m boom, there are 48 nozzles, or effectively 48 sections,” explains Altek International’s managing director Richard Riley.
Two years ago, Altek started working with US software company Harrison Ag Technologies to develop the Smart Nozzle system. The result is a retrofit system that fits nearly all brands of sprayer on the UK market and enables more than 32 separate sections to be controlled via a control box in the cab.
The original spray controller remains on the machine, even after the Smart Nozzle system has been installed. “Harrison Ag software then controls Altek direct control valves fitted to the DCU of the nozzle body on the boom itself,” says Mr Riley. The system uses CanBUS with modules mounted along the boom to enable the GPS controller to talk to each nozzle.
The company worked with sprayer specialist Wright Farm Services to identify and solve problems with bringing the US-developed software into the UK.
“We had to find ways of dealing with factors like four-wheel-steer and recirculation – features not many sprayers have in the USA.”
“Even the most experienced of sprayer operators can’t guarantee that they shut off sections at exactly the right point every pass. You can’t see that you’re overlapping and even if you did, the operator would have to wait for the whole 2m or so width of the section to pass before being able to switch off.”
Research carried out in the USA suggests that the savings can be anywhere between 15% and 20%, but that’s based on drilling by GPS. “In the UK, with conventional tramline drilling, it’s expected to be towards the higher end of the scale.”
“The beauty of the system is that there isn’t a sprayer we can’t fit this to, and should the farmer choose to change sprayer it can be taken off the old one and put directly onto a new model, with more units if required.”
“It’s a fallacy that you only see the benefits if you’re spraying large fields. It’s actually the smaller and oddly-shaped fields where this technology will come into its own.”
CASE STUDY: Richard Day, Wrawby, Brigg, Lincolnshire
Richard Day’s nine-year-old Knight Laser EU was bought three years ago. With the purchase, the farm opted to apply liquid nitrogen as well as tackling the regular spraying schedule. Mr Day grows 16ha of potatoes, 14ha of sugar beet, 14ha of winter beans and 82ha of wheat.
“We’re doing a lot of spraying on a relatively small hectarage,” he explains. “When I heard that Altek was testing this system I approached the company. They were surprised at first, as they thought it was a small acreage to be adopting such sophisticated technology, but when I explained the fact that we have a lot of garings, or irregular field shapes, it became more feasible.”
After a few phone calls, Altek, Wright Farm Services and Harrison Ag were able to use the same technology used in individual row shut-off on seeders in the USA to link up the system to Mr Day’s trailed machine.
Before having the Altek system, it was only possible to shut-off four sections of the 24m boom from the cab. “With 12 nozzles in each section, it was easy to see where parts of the field had been double-dosed by the Vs that appeared, but now it’s almost impossible to double dose, regardless of what shape the field is or how it’s been drilled.”
At ÂŁ300/m, including the cost of the GPS unit, Mr Day believes it to be worth the money. “The saving in chemical, time and operator fatigue is more than worth it.”