VIDEO: New drill will help push strip-till concept
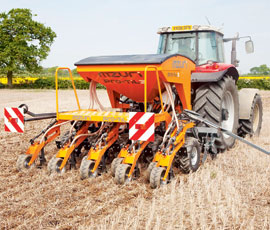
Martin Lole is hardly an amateur when it comes to designing farm machinery from scratch. As the man behind Spearhead Machinery, he is used to developing new concepts and trying to convince farmers that there are more efficient ways of doing things.
Mr Lole farmed before establishing Spearhead and knows what it’s like to deal with tough soils. After selling the company he bought a 160ha (400 acre) farm in a heavy clay area in Peopleton near Evesham, Worcestershire.
“I bought conventional machinery and tried to deal with the great clay clods that came up.” But after two back operations, Mr Lole realised he could no longer spend the hours on the tractor that breaking down these clods requires.
Mr Lole admits he loves his kit as much as any farmer. “But there comes a point when it doesn’t stack up to make repeated passes to create a seed-bed,” he adds. “It’s always interested me to try and improve how a tine cultivator works. I know we’ve had direct drilling for a while, and I am certainly not the first person to try it. We’ve just taken it a step forward by addressing the soil below the first two inches.”
Before developing the Mzuri Pro-Til (Mzuri means “good” in Swahili), Mr Lole was convinced that direct drilling had to be the way forward. “But putting my rape in with discs kept failing because our soil just kept getting dried out and the crop never established.”
So the decision was taken to opt for tines instead of discs. “The leg itself took a while to work out. Initially, I tried discs, but on our ground this dried out the clay on top too quickly. When it got wet, the soil just bulldozed itself and left large clods. I’m not knocking discs; they have their place in some systems. It just didn’t work on our farm.”
So how does the Mzuri Pro-Til drill work?
At the front of the machine, the first and second rows of tines both have what Mr Lole describes as a negative rake, meaning it’s wider at the back than at the front. “This came about during testing: a forward-facing leg brought up clods and we tried it instead with a half disc welded on, which didn’t have much of an effect, either.”
![]() Tines are followed by packer wheels before a coulter plants the seed. | The Mzuri Pro-til drill establishes cereals, OSR, beans and maize, says developer Martin Lole. ![]() | ![]() An RDS top-of-the-range control box is standard. |
---|
These tines work at between 30cm and 33cm (12in and 13in) spacings, depending on whether the drill has nine or 11 tines. “Drilling a foot apart is a relatively new concept in the UK, with the Claydon drill operating along similar lines,” he explains.
“Effectively, you’re drilling just as much or even more of the field than a conventional drill because you’re sowing a 5in width of seed in each row, rather than narrow slots closer together.”
For oilseed rape, Mr Lole believes tines need to be in 23-25cm (9-10in) to allow for a good root structure. For wheat, this can be an inch or so shallower. Tines can go to a depth of 41-46cm (16-18in).
Then what?
A 20cm (8in) wide packer wheel behind each tine consolidates the soil lifted directly in the first phase. The packer in this “reconsolidating area” started off as a 600mm press, but this covered the whole width – something Mr Lole didn’t believe fitted with the strip-till philosophy.
“And when it rained, the whole roller simply blocked,” he adds. To solve this, he replaced it with a reversed cleated rubber wheel mounted on a walking axle. This is designed to follow the field contours, thereby ensuring uniform drilling depth.
The drill coulters
“We tested the drill with both disc and tine coulters side by side, but this autumn ended any thoughts of using discs due to the wet weather,” says Mr Lole. Now, a wide tine coulter is used to dispense a 12cm (5in) band of seed per row. This coulter has angled sides that cut through the previously tilled soil to create a well for the seed to fall into.
Above the walking axle is a vertical pivot point on each side. This allows the drill coulter to stay in the centre of this previously tilled band, which eliminates the risk of clods being pulled in from the side of the row. Behind this coulter, there’s a semi-pneumatic tyre that re-consolidates the drilled soil once again.
“There is no need to harrow or roll behind the drill, but I’m aware that there will be a mindset to do this and I accept that. I’ve rolled 50% of the farm and left the other half and can’t tell a difference between the two. But the agronomist will want to see the drilled crop rolled for pre-emergence sprays.”
“This autumn has proved ideal for a drill developer as the conditions have been so challenging,” he explains.
“The first crop drilled was early on before the wet spell and came up brilliantly, but then it rained constantly. Because we just had stubble, I could choose my drilling date and didn’t have to panic as I hadn’t a prepared seed-bed to worry about.”
One of the biggest things that’s changed is Mr Lole’s mindset. “Because I only had to make one pass to establish, the sheer pressure on the farming system was drastically reduced. In fact, not having to spend hours creating a seed-bed freed up my time for hedge cutting, ditching and developing the drill.”
Cost savings
Mr Lole believes he has saved between ÂŁ100 and ÂŁ150/ha by not ploughing, power-harrowing or culti-pressing.
“By cutting these machinery costs, I believe it’s possible to make a small farm profitable. You can get rid of most of your kit, hire in a tractor suitable for pulling the drill and get your crop in with one pass.”
The drill is pulled by Mr Lole’s 230hp Massey Ferguson 6499. “I keep a large tractor for obvious reasons, but if I wasn’t developing machines then I would definitely hire one in.”
“The savings in fuel have been phenomenal. In fact, our accountant phoned up believing we had forgotten to list fuel purchases. We had only ordered one tank of fuel all season.”
So far, the Mzuri Pro-Til has been used to drill wheat, rape, beans, maize and linseed, he adds. “The linseed was drilled about three weeks ago and although the surface was dry on top, the drill still managed to place the seed into moist soil.”
Everything is built by the company in Worcestershire except for the control unit, which is sourced from local electronics specialist RDS. The metering system is Mzuri’s own and is pretty straightforward – just a cartridge you set up for the crop that’s being drilled.
There are three models available, a 3m mounted machine, a 3m trailed model with a larger tank and a 4m folding machine. Machines on show at the Cereals event will have the facility to precision place both fertiliser and seed, thanks to a split hopper, adds Mr Lole.
The Mzuri costs between ÂŁ20 and ÂŁ25/acre to run, according to Mr Lole. “If you add to this a possible saving in fertiliser of ÂŁ25, then the cost for establishing your crop is almost neutral.” Machine prices haven’t been finalised yet.