FW Awards 2009: Poultry Farmer of the Year finalist – Elwyn Griffiths
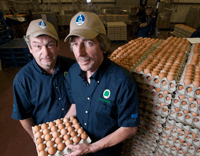
Brothers Elwyn and Gareth Griffiths have developed their own enriched colony system to achieve even higher welfare standards.
The 2012 conventional cage ban means that like many other egg producers, the Griffiths have to phase out their conventional cages.
“We wanted something different and we enjoy engineering, so we decided to develop our own unique colony system,” says Elwyn.
They tested systems with differing numbers of birds and in the end they decided to go for an 80-bird system.”
Based on the Italian Tecno colony system, the “Tecno-Griffiths” colony goes beyond the minimum provision of perches, scratch plates and nest boxes.
“We believe our new Tecno-Griffiths colony system is well ahead of the 2012 legal welfare requirement,” says Gareth.
Colonies measure 4.8m x 1.2m (15.8ft x 3.9ft) and contain four nest boxes.
“By having nest boxes at both ends, hens have a choice so they can establish communities within the colony,” says Gareth.
Another unique feature is the perches going across the colony, instead of the more common design of having a long central one. “This allows birds to move more freely inside as they can move over and under the perches.”
Results have been excellent with good feathering, a mortality of less than 2% and egg production averaging about 325 eggs a bird. “We are still collecting eggs from some flocks at 90 weeks, as birds are in such good condition.
The brothers plan to replace all their cages with colonies 18 months before the 2012 deadline.
Once laid, conveyors transport eggs directly from the hens into the packing station. In-line packing means that even an egg laid by a hen in the furthest shed 1.4km (0.9 miles) away is packed ready for dispatch within three hours.
A high level of automation means that they only require six staff at a weekend to run the packing station, which handles 0.5bn eggs a year.
“Eggs are not touched by human hand with automatic crack detection, dirt detection and blood detection.”
Eggs are sold under the Oaklands Farm brand, except for those in Iceland stores. But unlike many other producers, all are in plastic boxes rather than the traditional moulded fibre, as Elwyn believes they offer many benefits.
“They are more hygienic consumers don’t need to open them to check for damaged eggs.”
Furthermore, the packs contain any leaks from breakages, so don’t spoil other packs. “Our losses are now down to less than 1%.”
Plastic packs also bring environmental benefits. Figures calculated show that even if plastic packs went to landfill (they are recyclable), they are still have a smaller carbon footprint than moulded fibre packs. This is because of the energy needed to treat pulp.
They also require less fuel, as plastic packs take up much less space. “As soon as we switched to plastic, 60% of the trucks carrying packaging were no longer needed.”
Another environmental measure is the rain harvesting system. “We have a significant area of buildings and concrete and we were seeing some flash flooding after heavy downpours,” says Elwyn. Water is now collected, stored in lagoons, treated and used as drinking water for the birds.
The brothers are also passionate about traceability and they were the first UK packer to adopt on-farm egg stamping.
“We invested in stamping as we wanted consistency across all our contracted flocks and we picked up all the costs ourselves so there was no cost to the producers.”
The code gives the method of production, country of origin and a unique farm identity number. This coupled with the in-cab data logger gives full traceability of eggs.
Another way the family has removed costs from the business is by developing its egg products division with all class B eggs broken on site. Oaklands recently launched a new liquid egg product “Egg in an instant” into retail stores aimed at widening the appeal of eggs.
So by controlling costs at all stages, the brothers believe they have a business that is more cost effective than their competitors. As Elwyn says: “I believe no one can produce eggs as cost effectively as we can.”
Farm facts
- Established by Aled and Olwen Griffiths
- Farm 4500 acres of arable on share farming basis
- 1.6m birds housed on-site
- Employ 160 staff
- Produces 500m eggs a year
- 27 contracted free-range flocks
- Suppliers to the food service market and discounters
- Every egg is utilised by processing or packing
What the judges liked
- “The Griffiths have driven cost out of production and packing to such a level it has almost become an artform. I would defy any producer in the country to better their performance.”
Three achievements
- Developed own enriched colony system
- Successfully launched a liquid egg product
- Captured 60% of the food service market