How better sprayer operation can up output and cut pollution
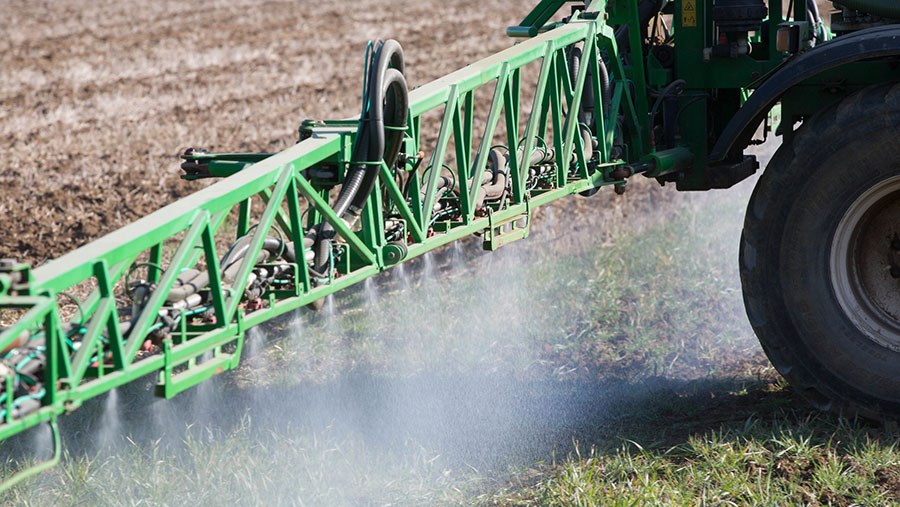
Improving sprayer fill-up areas and installing a bioremediation system such as a biobed can reduce pesticide pollution and boost sprayer output.
The British climate throws up some nasty surprises through key spraying periods, limiting opportunities to spray at the right time.
With an increasingly limited chemical armoury and some products losing efficacy, timing is ever more important to get the most from every application.
Increasing sprayer output can be done in a number of ways, but some of the tricks growers adopt can have a negative impact on application quality.
See also: Champion sprayer operator builds “Rolls Royce” of fill up areas
For example, modern rate controllers allow fast forward speeds while maintaining application rate, but the subsequent increase in pressure and turbulence produces finer droplets and increased drift.
Killer downtime
This leads David Felce, Agrii’s eastern technical manager and application expert to conclude that improving spray operation logistics is the best way to increase output.
“Forward speed has the least impact and is counter productive to spray quality. In my opinion, downtime kills output and timely application,” he adds.
So where are operators losing time and how can they claw it back?
When conditions are suitable for spraying, any period the sprayer is not in the field applying product is eating into a valuable work window.
Filling and rinsing are big contributors to downtime and independent mechanisation consultant Bill Basford says reviewing and redesigning fill-up areas can significantly increase spray opportunities.
“If you sort your fill-up area out, your filling process will be under control and will take a shorter time,” he adds.
Installing a purpose built fill-up area is becoming a popular choice for big arable units, comprising a bunded concrete pad to contain all spills and washings.
The pesticide store can also be installed just a stone’s throw away to ensure minimal time is taken moving product to the sprayer induction hopper.
Bioremediation
The icing on the cake is covering the fill-up area with a roof to minimise the volume of water captured by the bund, which is then connected to a bioremediation system.
Choices include a biobed, biofilter or a Phytobac (see ‘Phytobac – the next generation biobed’,below), which all use soil and organic matter to reduce pesticide pollutants in wastewater.
While many associate these systems with environmental benefit, they can also speed up the tank rinsing process when switching crops or products.
They allow operators to rinse out the tank without leaving the yard, disposing of washings through the system rather than on an undertreated area of a field.
“Good logistics and facilities improve all aspects of spray application and also protect the environment, which is increasingly important as we move into a more aware world,” says Mr Felce.
He adds a good fill up area and bioremediation system also demonstrates best practice if an Environment Agency or Rural Payments Agency inspector shows up.
“The first thing they look at is your chemical store and fill-up area and if you show them good facilities, they would almost be walking away already.”
Quick fill
Where possible, Mr Felce also advises the installation of a dedicated pump and induction hopper, rather than using the sprayer’s own pump to self-fill.
He uses an example of a 240 litres/min piston diaphragm pump giving 100 litres/min through an induction hopper on a sprayer’s self-fill system taking about 20 minutes to fill a 2,000-litre tank.
Using a separate pump and induction hopper can boost that to 300 litres/min, taking just seven minutes to fill and saving 13 minutes on each fill.
Over four loads, that equates to 52 minutes gained and the chance to squeeze another load into the day – an extra 20ha at a water rate of 100litres/ha.
“That’s one extra load without going faster and compromising spray quality,” says Mr Felce.
Phytobac – the next generation biobed
First developed in Sweden in the mid-1990s, biobeds represented a huge step forward in reducing the environmental impact of pesticide application.
Agrochemical company Bayer CropScience has supported the development of the Phytobac – a next generation biobed – of which there are about 3,000 units across Europe and one so far in the UK.
The system uses a biomix of 70% topsoil and 30% straw contained in an above or below ground-sealed concrete bunker, with contaminated water drip-irrigated evenly across the surface of the mixture (see diagram).
Bayer’s Alice Johnston says a raised roof eliminates rainfall entering the system and also promotes airflow and evaporation from the surface, with the closed system producing no final discharge for the farmer to deal with.
“We are bringing a lot of knowledge to the UK from our experience in Europe and all the information farmers need to construct a Phytobac is on our website, with a tool that calculates what it required on your farm,” adds Miss Johnston.
The system is easy to construct from widely available materials and is estimated to cost in the region of £7,000.
Farms may be eligible for a Catchment Sensitive Farm Capital Grant to help with funding. More information can be found on Bayer’s website.
First UK Phytobac reduces downtime
With a complex rotation of combinable, root and onion crops, both conventional and organic, one Cambridgeshire farm has boosted sprayer efficiency with an improved fill up area and Phytobac system.
Adapting a bay in an existing building, a covered, bunded concrete pad allows easy filling and washing and all waste is contained and pumped to a nearby Phytobac.
Ralph Grindling, farm manager at Duxford-based Russell Smith Farms, says all spraying is carried out within an 11-mile radius of one filling site.
Switching between the variety of conventional and organic crop types can require many tank rinses and now, instead of travelling backwards and forwards to the field, it can all be done in the yard.
“We have to wash out more than most and it means we are not missing an opportunity.
“We are also working to a target [of washings] that our Phytobac is designed for.
“It has focussed more attention on minimising waste and I think we have reduced the amount of washings in the year [since installation],” explains Mr Grindling.
He says construction was straightforward, with concrete panels similar to grain store walling sat on an existing concrete pad and then sealed watertight.