How one farmer adds value with ‘worthless’ wool and bracken
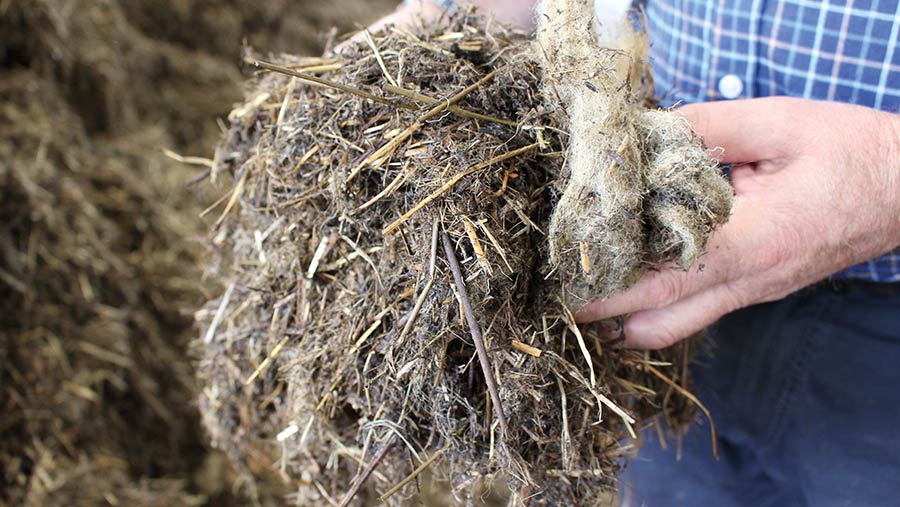
Bracken is a scourge for many hill farmers, eating up valuable grazing land, providing an ideal habit for ticks, and proving difficult to control.
But a farmer in Cumbria has turned this worthless weed into a valuable and highly sought-after product.
Simon Bland, who farms at Dalefoot in the valley of Heltondale in the Lake District, has been producing peat-free compost for the past 22 years using various natural products. The two main ingredients he uses are bracken and wool.
See also: How to make the most of wool in a depressed market
On his own farm, which rises from 800ft above sea level to 2,000ft, he is harvesting about 20ha (50 acres) of bracken each year.
Farm facts
- 400 Cheviot ewes and 123 Whitefaced Woodlands. All are lambed indoors and turned out straight to the fell after lambing
- 49ha (120 acres) of in-bye grassland rising to 2,000ft. 24-28ha (60-70 acres) cut three times each year for silage
- Upland area in Higher Level Stewardship scheme
- United Utilities tenanted farm
- Composting business is the Bland’s way of trying to farm without subsidies
However, with compost orders doubling year-on-year, Mr Bland is seeking other farmers to harvest bracken to make up the total 7,000 big bales he requires to produce 700,000 bags of compost.
Farmers Weekly spoke to him to find out more about harvesting, returns and how he makes it into compost.
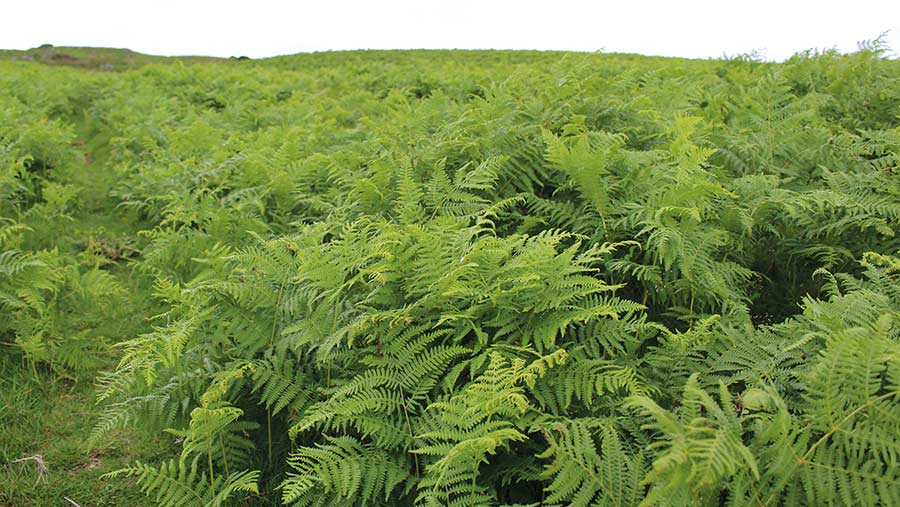
About 20ha of bracken is harvested each year at the Dalefoot Farm. © Sarah Alderton
Benefits of harvesting bracken
- Harvesting bracken helps make it easier to gather sheep off the fell
- Dense bracken can limit grass growth on the fells as it blocks out light. Better vegetation as open canopy improves conditions for plants such as fritillaries and ground-nesting birds
- Improves grazing quality for stock
- Health of stock improves as it reduces the habitat for ticks
- Receive a payment for a crop that grows for free
Financial rewards
Mr Bland is paying farmers an average of £22 a bale delivered to his farm, with prices varying if haulage is required.
“We can organise haulage but that will be an additional cost. We also have contracting teams that can harvest the bracken and had a contractor in Bristol supplying us with bracken last year,” he adds.
Mr Bland is trying to connect with farmers and develop strong and sustainable relationships by offering to take their wool too. This is also made into compost and he pays a premium of 40p/kg for hill breed wool.
He can only take undipped wool as the compost is certified organic and OP dip locks up in the wool’s lanolin. Farmers must sign a declaration the wool has not been dipped.
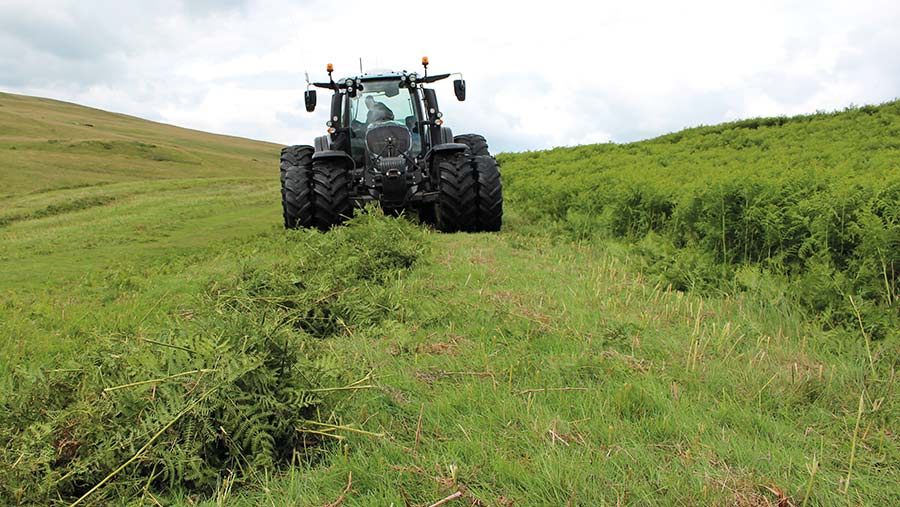
© Sarah Alderton
How to harvest bracken
Bracken can be harvested every year from about the second week in July onwards. The crop should be in full leaf – not when the leaf is still in curl – and should be cut down to about 30cm in height. Cutting too early not only affects the yield but it cuts the vigour of the plant back quite a lot.
Once cut, the crop should be left for about 10 days to dry before being baled. The crop should be as dry as straw and hay at the point of baling. On average, farmers can expect to yield between 10-17 bales/ha (4-7 bales/acre).
A normal three-point linkage mower with a standard 2.7m cut can be used along with a standard round-baler. Depending on the ground conditions, dual wheels may be needed on extreme terrain or where ground is wet. However, for farmers in stewardship schemes, it is important not to damage the land.
Mr Bland has been harvesting bracken on the fields surrounding his farm for the past two decades. The use of satellite technology in recent years has made it a lot easier as they have logged where all the big rocks are.
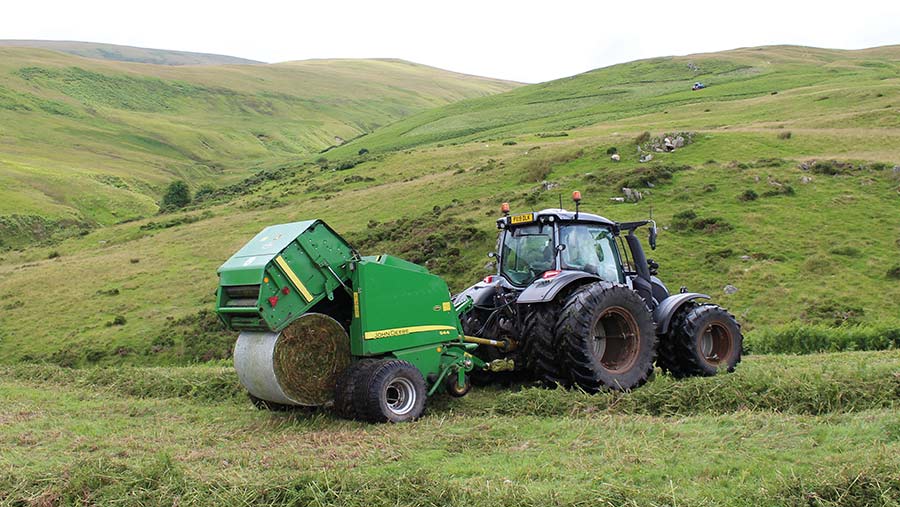
© Sarah Alderton
How bracken is made into compost
The bales are put through a chopper and added with other ingredients, depending on the type of compost they are making. Dalefoot Compost produces eight different compost varieties. Each mix varies in ingredients, but can include components such as wool, bracken and grass. Mr Bland is harvesting about three cuts of grass silage a year from 24-28ha (60-70 acres) of in-bye land for composting.
The compost mix is then piled in a heap and turned every day. Quite quickly the temperature in the heap will increase to about 70C. At this temperature, it sterilises any seeds or pathogens.
Turning it every day is necessary to provide an even heat profile throughout the heap by allowing some of the heat to be released. If the temperature is even, the bacterial activity is stable throughout. It is important to keep the bacteria aerobic and not anaerobic, as the latter will affect fermentation and make the product unusable as compost.
The turning process must continue for eight weeks. After this, the compost will be ready for bagging. Prior to being bagged, the compost is put through a screen filter to remove any large particles.
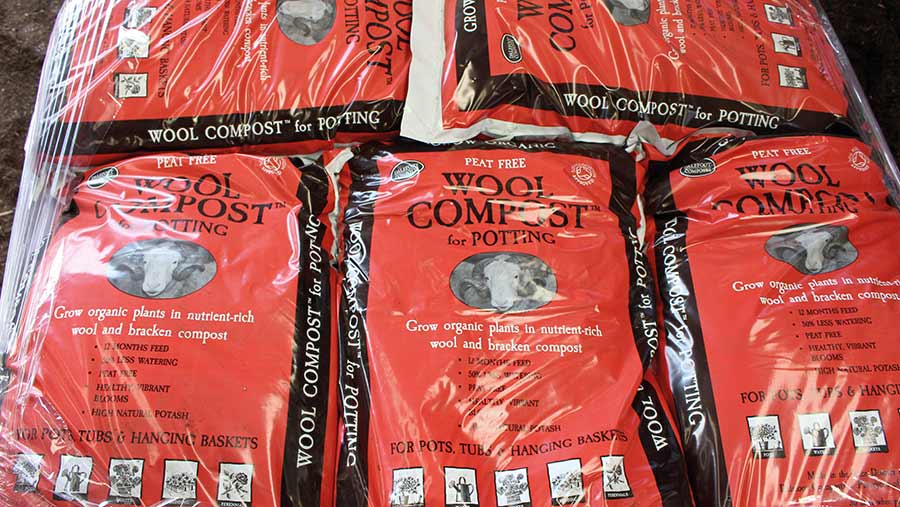
© Sarah Alderton
Compost market
Mr Bland is supplying garden centres as well as mail order. More gardeners are becoming aware of the unsustainable nature of peat composts and are looking for alternatives, he says.
During the pandemic, Mr Bland and his team saw mail orders increase by 15,000% due to many people taking up gardening.
He says: “We can easily sell what we produce which is why we are looking at working with more farmers and forging sustainable long-term relationships.
“The pandemic highlighted the weakness in the supply chain for peat-free alternative composts, such as Coir which is imported from places such as Sri Lanka. It has emphasised the importance of sustainability.”
If you are interested in supplying bracken, get in touch with Dalefoot Compost on 01931 713281 or visit dalefootcomposts.co.uk