Flexible feed strategy to overcome forage concerns
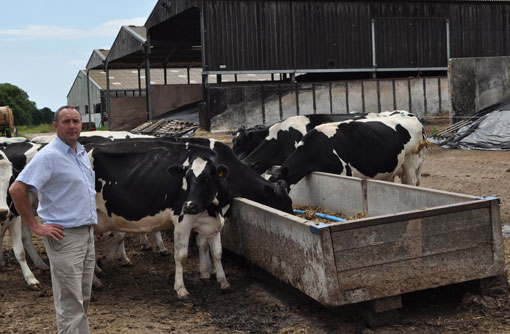
The second consecutive dry spring has prompted some changes to the feed strategy at Clinton Devon Farms.
Poor grass growth during May and June meant forage stocks were being eaten into at an alarming rate, while early silage yields were pretty hit and miss, says manager George Perrott.
First-cut grass silage taken between 3 and 26 May, typically averaged 15-20t/ha (6-8t/acre), although ranged anywhere between 5t/ha (2t/acre) and 30t/ha (12t/acre) with a high dry matter. Second-cut finished at the end of June and generally fared slightly better, although with lower dry matter, due to much-needed rain earlier in the month.
“This year we’ve definitely had the biggest yield range I’ve ever known,” Mr Perrott says. “Because it’s been so dry, there have been days where we’ve virtually been on full winter rations, feeding up to 20t of silage a day across the two 250-cow herds. It was getting pretty tight for a while, but grass came back just in time and I’m hoping we can do enough now to get us through.”
Dairy cake use for spring-calving cows was increased from 3kg to 5kg/cow/day due to the lack of grazing in a bid to keep cows in good condition at service. This has been dropped to nearer 4kg, alongside cereals, silage and minerals (see table). “The autumn-calving herd should start on 1 July and this tends to fit our grass growth cycle better in a dry year when we are drying off cows in May or June,” he notes.
Insurance policy
Three weeks after first-cut silage was taken, the dry weather meant regrowth had been poor, so Mr Perrott decided to take silage from 80ha (200 acres) of rotational mulching grass as an “insurance policy”. Normally this would have been left to plough back in for fertility building.
“We did a similar thing last year. It may or may not have an impact on following cereal yields, but I think the weather’s likely to be a bigger factor, especially this year,” he says
Shortly after he did this, rain finally arrived and boosted grass growth just in time for second-cut silage. “Yields were better, but quality probably wasn’t as good as first cut,” he says.
In total 176ha (435acres) of first-cut, plus the mulching silage, and 115ha (283acres) of second-cut silage has been taken. This will be complemented by 60-80ha (150-200 acres) of wholecrop oats, wheat and triticale silage, due to be cut in the next week or so. “Generally we’ll wholecrop fields with a lot of weeds, bare patches, or those that were later drilled and likely to take longer to ripen. It’s one of the real advantages of having our own kit, in that it lets us do the odd field here and there without having to rely on a contractor who’s unlikely to drop everything for a small job.”
Mr Perrott says he tries to take wholecrop from fields where stubble turnips can be sown straight away. “The quicker we can get them in, the better the crop will be. Getting more turnips in – ideally before the end of July – means we can leave spring calving cows out as dry cows around Christmas, reducing the amount of silage we need.”
Clamping
Mr Perrott manages to clamp wholecrop by calculating the likely total tonnage available and dividing it by 365 days to make sure it can be rationed out through the year. He tops up clamps with the right amount of grass silage to ensure the desired amount of wholecrop is exposed once the clamp is opened. Wholecrop silage tends to be biased towards freshly-calved cows.
The farm has recently moved away from using sheets weighed down with tyres to cover clamps and instead now uses a thin, clear plastic under sheet, covered with the normal black plastic on top, weighed down with net and gravels bags. The thin undersheet effectively “clings” to the surface, creating a better seal and reducing wastage, Mr Perrott says.
The nets and bags make it easier to cover/ uncover the clamp and reduce the risk of tyre wire contaminating the silage. “It’s not cheap; we probably spent about £3,500 on nets and bags for the six clamps (6,500t) in total, but it should save time, wastage and protect cow health, so we should be better off in the long term. It also means we can re-use more of the top sheets as they haven’t been pierced or ripped by wires from old tyres.”
A new Strimech high capacity shear grab has just been purchased and Mr Perrott is also in the process of buying a new tub mixer feeder wagon, at a cost of £20-30k. “Our current feeder wagon is only three years old, but it’s such a fundamental piece of kit that we rely on, we look to change it every three years.”
A lot of road miles are done each year, so good running gear – brakes and tyres – are a key factor in what to go for, he notes. “I’m wary that potential new regulations for road transport could be introduced in the future, so we’re just trying to stay a step ahead.” With that in mind, he is also looking to upgrade the 14t silage trailers to all have air brakes.
Technology investment
Mr Perrott is also investing around £30,000 in a new automatic identification and auto-shedding system for the dairy herds, following a recent veterinary meeting with the farm staff that highlighted the need to improve milking routines.
Each dairyman currently looks after 250 cows and it was felt more time was needed for pre-milking health routines and checks, in order to improve cell counts and bactoscans. Rather than taking on extra milking staff, Mr Perrott says the auto-ID system should free-up time at milking by not having to enter cow numbers manually in the parlour.
Essentially the system uses EID tags, costing £2-3 each. An electronic curtain reader identifies cows as they enter the parlour and allows feed to be targeted individually. The auto-shedding means cows can be separated, based on a predetermined variety of criteria, such as health, vet routines or activity level.
Some 250 activity collars have also been purchased. These will be linked to the parlour’s computer system via an aerial in the collecting yard and will automatically identify particularly active bulling cows or inactive sick or lame cows. “It’ll help us pick out the ones to serve and once they’re in calf, we’ll move the collar to another cow. The collars aren’t cheap, which is why we didn’t buy them for all 500 cows.”
A portable PDA can read the electronic tags, giving the user instant access to individual cow records in the field. This system also works with the electronic weighing scales, reducing the time spent manually recording data. “It’s a big investment, but we’ll be saving on labour time spent every day, so it should pay for itself, improve cow health and reduce the risks of mistakes being made.”
More information on Clinton Devon Farms
More information on other Management Matters farms