Slow RHI uptake reflects support concerns
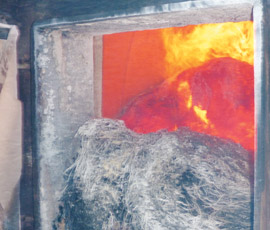
The Renewable Heat Incentive (RHI) was introduced in November 2011 to encourage investment in technology like biomass boilers, ground source heat pumps and solar thermal panels.
RHI pays up to 8.9p/kWh, index-linked, for 20 years, but confidence in the fledgling scheme has suffered from the knock-on effect of cuts to previously agreed solar support rates earlier this year.
By the end of June, just 93 RHI installations had been accredited, 85 of which were for biomass boilers.
“Farmers are nervous of investing in renewable technology when the government’s contract is subject to change,” says Harry Cottrell, president of the Country Land and Business Association.
“People have seen what the government has done to the FiTs and are nervous of investing in renewable heat as a result.”
However, Ian Goodchild, business development manager at renewables designer and installer Fair Energy, says the results of the recent spending review should engender a little more confidence. This stipulated that the RHI scheme would provide up to ÂŁ70m a year, with any applications above that threshold suspended until the following year.
“It’s a much better and fairer way of trying to manage the process than the way they handled the FiTs,” he says. “Interest is now starting to pick up in the commercial sector, but demand in the first year is still unlikely to exceed ÂŁ40m.”
One of the stumbling blocks is the lack of information about domestic installations, he adds. Although the Renewable Heat Premium Payment scheme offers grants of up to ÂŁ1,250 towards the cost of domestic projects, the annual payment currently only applies to commercial proposals.
The domestic RHI was originally scheduled to come online last year, but has since been delayed to this year, and then to summer 2013. “There is no real government commitment to support it; at the moment domestic clients don’t know what they have to do to be eligible, or what they will be entitled to.”
Commercial installations must supply heat to a business premises or to two separately-rated domestic dwellings; so while a farmhouse would not be eligible, heating a dairy and the farmhouse may qualify.
“Depending on your existing infrastructure, payback with the RHI could be as little as three to four years,” says Mr Goodchild. “Without the RHI, it could be 10-15 years.”
In the case of biomass technology – worth up to 8.3p/kWh in government payments, farmers must also consider the cost of a building to house the boiler and feedstock, plus pipework and metering. Feedstock can vary from solid timber to woodchips, pellets, straw and miscanthus.
David Knox, marketing manager at Treco, which supplies, installs and maintains biomass boiler heating systems, says the level of promotion for the RHI has been considerably lower than for the FiT.
“There just isn’t the level of awareness out there – the majority of people we speak to haven’t heard of the RHI. There is great demand for domestic biomass boilers, but we’re telling people to hold off to make sure they get the right equipment to be eligible for the scheme; we just need more clarity on what the government is planning to do.”
Many claims for commercial installations have also been rejected due to insufficient or confusing information on the application form. “The quality of your application has a direct impact on the time it takes to get accredited, so take expert advice and get it right first time.”
Case study: John Seed, Duns, Scottish Borders
John Seed installed a biomass boiler at Woodend Farm, Duns, in the Scottish Borders, last year to power the farm’s grain dryer. “I wanted to stop the haemorrhaging of cash on heat and power, with a system that would suit an arable enterprise,” says Mr Seed.
He powers the 450kW boiler with 170t of oilseed rape straw a year – although it can also burn woodchip and other biomass fuels. Solar panels also provide electricity for the farm.
“It’s been fairly simple to replace the boiler, but it’s been quite a job getting the RHI because we are all learning as we go along.”
He has replaced the old continuous flow dryer with an on-floor system with ducts and grain stirrers, but says a new building isn’t essential. “These drying systems can be easily retrofitted to many grain stores.” The ash from the boiler is applied as a soil conditioner, helping to reduce fertiliser bills. By passing the exhaust gases from the boiler through the accumulator tank, Mr Seed has increased the overall boiler efficiency to 88%.
As well as the grain dryer, the boiler heats the farmhouse, offices, cottages and, soon, a new poultry business. Installing the correct metering to meet RHI requirements has been particularly time consuming, but it will certainly be worth it.
“In 2011 we saved £38,500 in gas and heating oil, and we expect to receive RHI payments of £25,000 a year. The Overdahl system, district heating and central heating systems cost around £250,000, while the on-floor grain dryer cost a further £95,000, so we are looking at a payback of around seven years.”