2014 Farmers Weekly Awards Sustainable finalists revealed
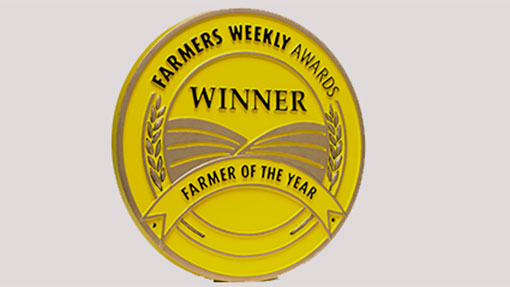
The farm businesses of the finalists in this category couldn’t have been more chalk and cheese – from a small farm tenancy to a multimillion pound food operation.
But all of them are united in their efforts to create a positive legacy for their children and the countryside. Debbie Beaton reports.
Kevin and Julie Bateman
Martinsfield Farm, Devon
Kevin and Julie Bateman have transformed the soil, biodiversity and connection to their local community on the farm that they took over as tenants within the National Trust’s (NT) Killerton Estate seven years ago.
Their total farming business is 220ha (540 acres), which includes the NT tenancy on Martinsfield Farm, several other different tenancies and a grazing licence in this beautiful rolling Devon landscape.
One of the requirements of the NT tenancy is that the farming has to be part-time in order to focus on environmental objectives.
Restricted development
But there’s nothing part-time about the Batemans who, despite the nature of their tenancy, are passionate advocates that farming and environmental management can go hand in hand.
The “whole farm” plan restrictions the couple signed up to in their 10-year tenancy include limitations on stocking rates, forage crops, breed choice, outwintering, fertiliser and supplementary feeding.
They’ve adhered to all of the constraints and somehow managed to create a viable core farming organic enterprise from their 800 ewes. This, without doubt, is Kevin’s proudest achievement: “I want to manage farmland in a way that delivers a benefit for everyone – farmers, wildlife and the public as a whole.”
His sheep – a mix of whitefaced Dartmoor, Mules and pure-bred Dorsets – are benchmarked with Eblex Stocktake and last year the net flock margin exceeded £12 a head, which was well above the average and in the top third.
One of the earliest, and most important, decisions Kevin made when they took on the farm was to address the soil structure, which was a critical limiting factor to grass growth and productivity.
One-third of their productive grassland is lifted each year. This, as well as overseeding and a tine weeder, are helping to encourage soil organic matter and rejuvenate swards cost effectively.
Developing a system that doesn’t require big machinery investment is also at the heart of another major improvement to productivity – the all-grass wintering (AGW).
For 100 days prior to lambing the sheep are grazed on a rotational paddock system, managed with electric fencing, and moved daily to maximise grass growth and availability.
“AGW has made us focus on producing quality meat from grass as well as cut concentrate costs by £4,500/year,” says Kevin.
The system also led them to being involved with Eversfield Organics, a local company that pays the average organic list price without reductions. The animals are killed locally, which minimises stress: “It’s a great working relationship – they provide valuable abattoir and customer feedback and we welcome their purchasers to the farm to see how their products are produced,” says Kevin.
Farm facts
- National Trust Tenancy
- 220ha (540 acres)
- 800 organic ewes
- 20 Red Ruby Devon sucklers
- Environmental schemes – HLS,
- Diversifications – rural surveying and holiday let
Rush bedding
Broadclyst Moor – a tussocky area full of wildlife and a diversity of plants – is an important wildlife haven on the farm. Cutting sections of soft rush on the moor provides useful cattle bedding as well as encouraging a great range of plant species.
A small suckler herd of Red Ruby Devon’s graze during the summer, along with some rescued Exmoor ponies, leaving behind dung – a critical feed source for Barbastelle bats roosting in the nearby forest.
Reinstating 2,500m of hedge bank and restoring a further 4,000m of hedgerow provides important corridors and habitats for the bats, dormice and many other important bird and animal species. In total, the Batemans have planted 16,000 hedge plants and erected more than 17,500m of protective fencing.
Education matters
They have also planted two orchards next to the farmhouse and restored a traditional farm building that is used by Julie to host school visits and workshops. She has applied her expertise as a speech and language teacher and special needs co-ordinator to develop an educational facility at Martinsfield.
In the past four years, Julie has hosted more than 160 educational visits for more than 2,500 people. As well as regular school visits, there are forest activities and a six-week course for fathers who do not live with their children.
Educational access is a vital part of the farm and although partly subsidised, it’s an investment the Batemans believe is essential for local community engagement.
The couple have put their all, and nearly £200,000 of their own money as well as the same in grants, into making their farming business viable and sustainable. Their extraordinary achievement delivers positive results for everyone.
Clothier family
Wyke Farms, Somerset
The Clothier family have been producing milk and making cheese in Somerset since 1861. Today, five Clothiers sit on the family board of Wyke Farms, the largest independent cheesemaker and milk processor in the UK.
At the heart of this multimillion-pound food business is a dairy farm, running 1,000 Friesians plus followers on about 600ha near Bruton in Somerset. The farm provides 8% of the milk used to produce 14,000t of cheese a year – the rest comes from 150 dairy farming businesses with many supplying Wyke for more than 30 years.
Milk and energy are the major costs in this business and were the key drivers of the family’s ambitious “100% green” sustainability plan, says managing director Rich Clothier (pictured).
“The business needed to be robust for the future and it quickly became clear that using our waste would not only cut our costs but have a positive impact on the environment and stabilise supplies of energy and water.”
Their goal, to create a sustainable working farm that generates its own gas and electricity from farm and factory waste is well on track.
100% green
The family’s ambitious 100% green plan started five years ago and includes the installation of a £10m biogas plant to convert 75,000t of slurry into energy, a water reusage plant, solar panels on two farm buildings and three electric cars.
Three biogas digesters, which have been sited carefully to avoid spoiling the beautiful Somerset views, have a capacity of 4,600cu m each. They take all of the farm’s own cattle slurry, which is piped from the two units to a holding lagoon next to the AD plant, as well as pig slurry from a neighbouring unit.
The plant produces methane gas, which is piped to a generator to be converted into electricity and heat for the dairy and cheese factory. Any excess is sold to the grid.
The addition of pig slurry has been an important “buffer” for the lactose waste coming from the cheesemaking. This learning, and so many other aspects of using farm waste effectively, make Wyke Farms a crucial pioneer for the whole farming industry. They have built a green energy visitor centre next to the biogas plant to share all their learning with other farms, retailers, businesses, schools and the local community.
The digestate from the biogas plant, which is rich in N, P and K, goes back on to their own fields as fertiliser, explains Roger who, with his brother David, runs the farming side of the business: “It’s not only saving us £50,000-60,000/year in inorganic N but it’s easy to handle and a lot more popular than slurry with the neighbours because it doesn’t smell.”
They have invested in storage for the biogas by-product so that the fertiliser is available when needed and are also working with local farmers and advisers to determine when and how to use the digestate most effectively.
Farm facts
- Clothier family business since 1861
- 607ha (1,500 acres)
- 1,000 dairy cows plus followers
- Produce 14,000t cheese a year
- 100% self-sufficient in electricity
Energy self-sufficiency
Five years into the 100% green project Wyke Farms is self-sufficient in electricity – a saving of £30,000/month. It’s the first UK national cheddar brand to achieve this. The second phase of the AD project will ensure Wyke is also self-sufficient in gas.
A new water reusage plant will save up to 850,000m litres/day which, combined with the AD plant, enables the business to cut total energy and water bills by £2m/year.
But it’s not all about money; the impact on road traffic has been dramatic because the waste is no longer hauled away.
The family also organise a conference every year for their suppliers, bringing in outside speakers, to help share knowledge and ideas.
Recipe for success
Wyke Farms is on an extraordinary journey. It’s a far cry from the early days of grandmother Ivy making cheese in a small backroom in the farmhouse. Her recipe remains the cornerstone of Wyke’s cheeses, which are now sold in 160 countries – a fact that would amaze their grandmother since she never travelled on a plane.
Lyndon Edwards
Severndale Farm, Monmouthshire
Lyndon Edwards’ philosophy is to supply food to the local community that people can trust. It’s a simple statement but one that defines his business and aspirations.
Lyndon (pictured with son Thomas) took over the family farm at the age of 21 and had clearly inherited his mother’s interest in pedigree livestock because he focused his energy on genetics and breeding, supplying Cogent with some of its first bulls. He has since built up a 200-cow pedigree Holstein and Brown Swiss herd, which was converted to organic in 2001. “We used very few inputs so it seemed logical to go organic,” he says.
Today, Severndale comprises 240ha (600 acres) of organic mixed dairy, beef and arable for feed. The cropping rotation is three to four years of a clover ley or lucerne, followed by maize, then triticale or barley and finally peas or beans undersown with barley, lucerne or clover.
Five years ago he implemented a New Zealand style grazing system, using central tracks and paddocks to provide the cows with fresh grass every day. The cows also receive a mixed ration of their own home-produced feed and purchased protein such as organic lupins, soya and pulses.
Efficient thinking
He’s purchasing a tanker and trailed shoe to spread slurry more effectively – allowing more nitrogen to get closer to the soil and generate less smell. He’s also recently invested in a new cattle building, GPS guidance and an electric car to improve efficiencies as well as cut back on fuel usage.
His milk goes to Omsco, the organic milk suppliers’ co-operative of which he is also the deputy chairman and executive director. “I’m proud of what the co-op is doing for its members and sitting on the board gives me a unique insight on market developments, which help to inform my own farm business,” he says.
Farm facts
Milk yields average 8,000 litres on nearly 2t of concentrate and the organic milk price is 41p. The dairy is the core of the farming business, but Lyndon has created a number of new income streams including converting redundant farm buildings into a vet clinic and 14-office business unit. Both are fully let.
In addition he opened Hanley Farm Shop and café last year, which already turns over £7,000/week. The shop is largely powered by solar panels and uses a thermal hot water system. There’s also an electric charging point for vehicles in the car park.
Plans are in progress too for a wind turbine which will power the farm and 300 local houses, as well as contribute £25,000 to the local community.
Community growth
Of all the new developments taking place at Severnside it is the local community work that gives Lyndon most pride. He works with Transition Network Chepstow to help educate people about where their food comes from and recently ploughed up two acres of his land to encourage local people to grow their own food.
This “landshare” plot sits adjacent to his farm shop, where their produce can be sold. All sections of the butchery and kitchen are glass fronted so customers are encouraged to see every step of the food making process – from hanging to butchery and cooking.
Lyndon leads by example; an on-going battle with Johne’s disease inspired him to take up the role chairman of the national Johne’s action group.
Family man
He’s a director on many farming boards and is passionate about helping to drive the industry forward for the good of organic, and conventional businesses. Yet, he’s a family man at heart with son Thomas, daughter Laura and his wife all heavily involved in the business. They, along with other key staff, are motivated to drive the business forward with a profit share scheme.
Lyndon believes organic production is the gold standard for enhancing biodiversity and protecting natural resources – something he willingly shares with others in the community.
Sponsor’s message
“Farmers are at the centre of protecting the world’s natural resources, which is why the world’s largest tyre manufacturer has introduced a revolutionary new range that will reduce fuel consumption on farms and protect the valuable topsoil this season and for future generations.”
Barry Coleman
Bridgestone
Find out more about the 2014 Farmers Weekly Awards