6 lean management techniques to improve dairy efficiency
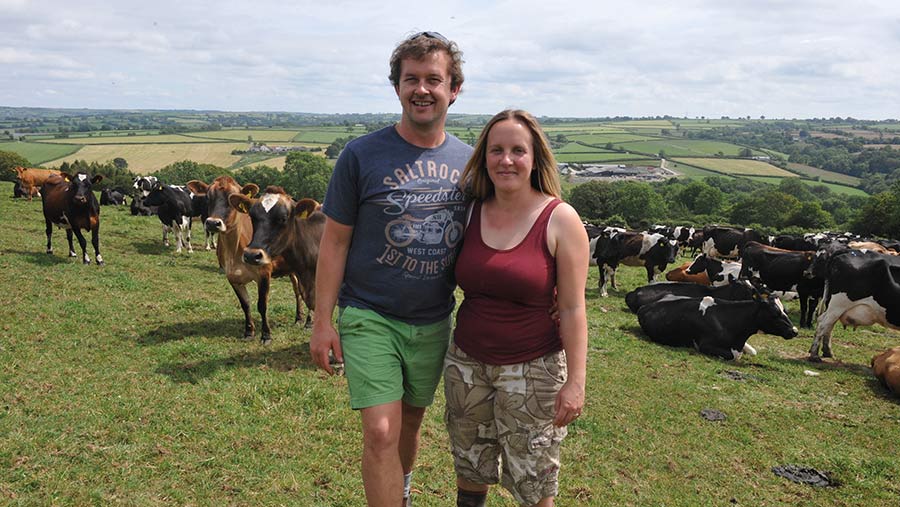
Applying lean management principles to running a dairy farm has reduced wastage and increased efficiency at Tyddyn yr Eglwys, near Llanfyrnach in Pembrokeshire.
Dylan and Hannah Harries have been working with lean management consultant Jana Hocken, from New Zealand, to improve performance on the 550-cow, spring-calving unit by streamlining tasks and delegating some of the everyday responsibilities to their team of four.
See also: How to light dairy parlours for cows, staff and milk quality
“There was never an issue with staff – it was a case of me doing my job better by creating a more organised and disciplined system that reduces wastage and gets things done at the right time,” explains Mr Harries.
Below, we find out how he has put lean management into practice and what benefits he has seen.
Farm facts
- Contract-farming agreement with farm owners Kim and Bryony Petty
- 283ha (700 acres) farmed
- 550 Friesian cross Jerseys
- 130 heifer replacements
- 50:100 swingover milking parlour
- Milk sold on a solids contract to Dairy Partners
- Averages 5,416 litres at 458kg milk solids annually
- AHDB strategic dairy farm
1. Whiteboard communication system
Daily management tasks and key targets – such as the weekly grazing rotation, jobs that need doing, and supplies required – are written on a 2.5×1.8m whiteboard. This is fixed to a wall in the dairy where staff see it multiple times a day.
Mr Harries has used 3mm tape to create tables and columns for different days and tasks.
“When you manage a team of people, it makes the day run more smoothly if there is a point of reference for what needs doing that day, to get those things done without needing to ask me,” he says.
It means the farm can be run without Mr and Mrs Harries needing to be on site. However, there can still be pinch points. “If we have made a grazing plan and we get a week of very wet or very dry weather, I will need to tweak that plan,” Mr Harries explains.
2. Flipchart for key performance indicators
Targets for monthly milk production, feed consumption and veterinary and medicine use are listed on a flipchart in the canteen, which is updated every month.
Although the Harries family don’t share all their figures with their staff, providing these targets helps the team understand the financial implications of actions.
“For anyone not paying the bills, costs can be dismissed as something that others will pick up, and are not really considered. But by sharing these figures, everyone in the team knows the cost of each action,” says Mr Harries.
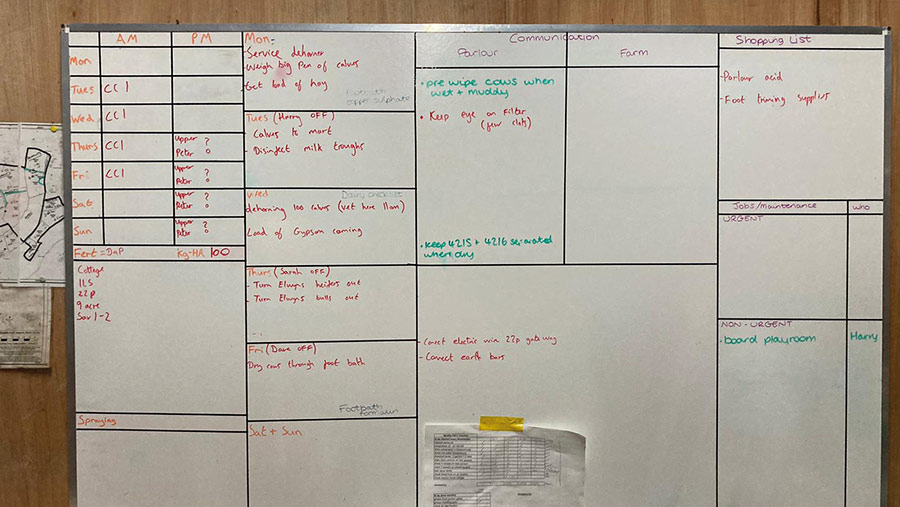
© Dylan Harries
3. Designating a team member to oversee routine checks
A member of the team carries out routine checks weekly – a different person has this role for a month.
In that month, they are responsible for checks in the parlour and the dairy. These checks include making sure there is enough dip and oil in the compressor, for example.
“It creates a sense of ownership and it means we don’t suddenly run out of things like dairy chemicals, which creates problems and inefficiencies.” Mr Harries explains.
4. Weekly team meeting
The Harrieses eat lunch with their staff once a week and have an informal discussion with them about aspects of the business. This might be about cashflow or the money allocated for veterinary care and medicine.
“If we have gone over budget, we will delve into it together – it might be that we have used more mastitis treatments than expected and we will try to work out why.
“By examining these things and including everyone in that process, we can work out the reasons for extra costs and discuss how we can improve on that,” explains Mr Harries.
Staff are made aware of the cost of products and services. “For instance, if they know the cost of a bottle of antibiotics, they can question if the animal they are about to treat really needs it and whether they should be using antibiotics,” he says. “It shifts the balance from staff not fully realising the cost of their decisions and actions.”
5. Farm safety chart
A traffic light system for accidents and near-misses is a visual reminder of health and safety considerations. If any member of the team has an accident, this is shown on a chart in red for that week. Near-misses are highlighted in orange and, in a week when all safety targets are achieved, these are marked in green.
“We don’t have a health-and-safety issue, but when we are at our most busy and tired, we might see a pattern of near-misses occurring. This chart is a visual reminder and one that we can act on by perhaps getting in some relief labour or offering staff time off,” says Mr Harries.
6. Reduce time wastage
Simple processes that improve labour efficiencies, including making better use of the time when cows are collected for milking, have been put in place.
A bucket, stocked with fencing and plumbing hardware and tools, and stored near the quad, allows small jobs to be tackled as cows are coming in – perhaps a fencing insulator or bungee is broken or a ball valve needs tightening.
With the cows walking distances of up to 1.5km from the farthest paddocks, this makes good use of otherwise “dead” time and means somebody doesn’t need to drive back to that location later to get the job done. “It’s not about taking hours away from the staff; it is about encouraging them to work smarter by getting things done in a more organised fashion,” says Mr Harries.
Some labour efficiency ideas have been trialled but not implemented, such as using one person to milk the 550 cows to free up a labour unit for other tasks during milking.
“If push comes to shove we know we can do it and it might be something we do when there are fewer cows milking later in the season, but we felt it put too much pressure on one person. I am certain our staff turnover would be high if we did that when all the herd was in milk, and there is a cost to that,” he adds.
Outcomes
Mr Harries says it is too soon to work out if the actions have improved the financial performance of the business, but adds: “I would be very surprised if they hadn’t.”
The measures have had a positive influence on the workforce. Mr Harries says it has given staff a chance to progress by giving them more responsibility. “We have seen it during calving this spring. The roles have, in some ways, been flipped, with them taking the lead rather than me initiating it.”
The Harries family’s top tips lean management tips
- The process can be daunting initially, but work through it bit by bit and it will come together over time
- Get staff on board from the beginning by inviting input from the whole team
- Push the boundaries – it is easy to get complacent
- Be flexible – it can take multiple attempts to set up the whiteboards in a clear manner