How water treatment tech could cut dairy slurry storage
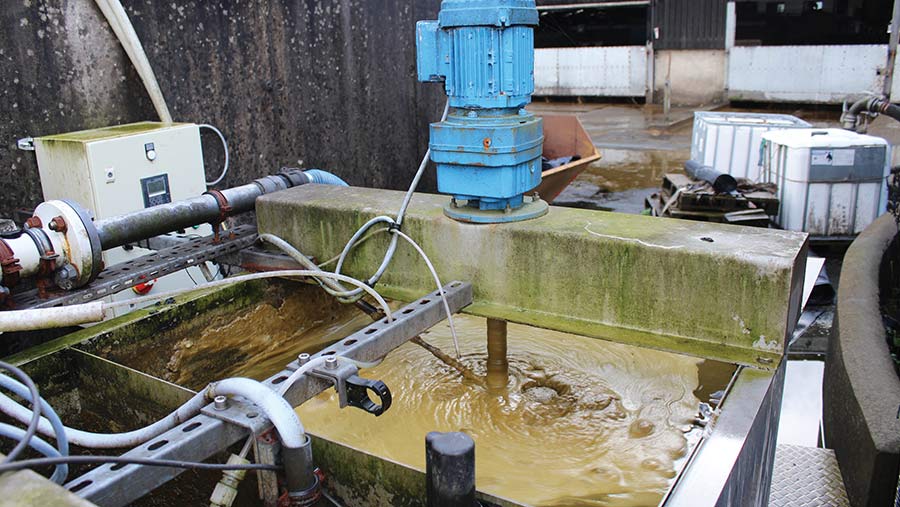
Adapting water treatment technology to a farm setting could reduce slurry storage requirements by 10-15%, make better use of farm nutrients and produce an effluent that is suitable for discharge into watercourses.
Research (carried out as part of the Tywi Farm Nutrient Partnership) adapted, combined and repackaged technology typically used by water companies for removing water and capturing nutrients from slurry.
See also: New slurry tech for storage and handling benefits pig farm
Such an approach could be attractive to dairy farmers under pressure to limit nutrient loss and water pollution.
Policy changes in Wales mean farmers will have to give notice and submit an application to apply organic manures at 250kg N/ha for 2024 under the Enhanced Nutrient Management Approach.
After this time, the plan is to adopt a 170kg N/ha requirement, which could see some producers having to reduce stock numbers or take on more land to spread slurry.
Welsh slurry storage requirements are also set to increase to five months’ capacity from August 2024, bringing them in line with current requirements for English producers in nitrate vulnerable zones.
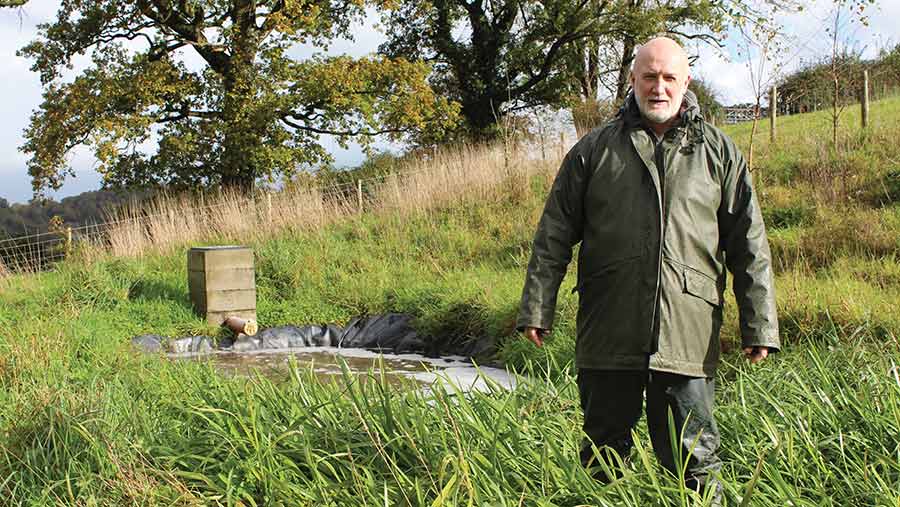
Neil Nicholas at the entry point of the reed bed © Aly Balsom
Pollution risk
About 90% of slurry is water. This water is the main source of pollution, through surface and groundwater run-off, says Neil Nicholas, research and development co-ordinator for Coleg Sir Gar in Carmarthenshire.
“De-watering” slurry splits the solids from the water, creating the potential to reduce storage requirements and improve nutrient management.
The system trialled by Coleg Sir Gar’s Agriculture Research Centre also looked at various methods of chemical treatment and filtration with the view to creating water of high enough quality that it could enter watercourses.
Farm Facts: Coleg Sir Gar’s Agriculture Research Centre, Gelli Aur
- 338ha (188ha owned and 150ha rented)
- 500 cows split into spring- and autumn-calving herds, managed on two sites but milked through the same parlour
- Yielding 6,200 litres at 4.5% butterfat and 3.6% protein
- 6-8ha barley grown
Slurry de-watering and nutrient capture: How it works
- Slurry is pumped through a screw press separator and the coarse solids (fibre/bedding) are collected.
- The liquid then goes to a reaction tank where chemical water conditioners are added, with the aim of clumping together any dissolved solids.
- The first tank produces pin-prick sized solids. In the second tank, these are bound together through chemical reaction to produce “Rice Krispies”-sized solids.
- The material is pumped to a decanter centrifuge where the solids are split from the liquid through centrifugal action and filtration.
- The solids are collected and the liquid goes into a dissolved air flotation unit (DAF). This is typically used in wastewater plants to clean water. Compressed air and chemicals are introduced. Micro-bubbles form and attach to any remaining solids that rise to the surface as a “foam”. This can be skimmed off.
- The final liquid from the DAF moves to a balance tank before being pumped to a reed bed.
- The liquid is gravity fed through the system from entry point. The reed bed includes three channels divided into solid (pea gravel and reeds) and liquid cells.
- Some of the cells are oxygenated and some are deoxygenated. Aerobic bacteria in the oxygenated cells help convert ammonia to nitrite and nitrate (nitrification); anaerobic bacteria in the deoxygenated cells convert nitrate to nitrogen gas, which is released into the atmosphere.
- Bacteria on the gravel and reed roots make use of any remaining nutrients in the liquid to survive, grow and reproduce.
- The liquid is retained in the beds for 180 days.
- At this point, it is potentially of high enough quality to be pumped into watercourses.

The reed bed © Aly Balsom
Key findings
Neil runs through the key findings from the study:
1. Storage requirements
Removing the solids from the liquid reduced slurry storage requirements by 10-15%.
2. Nutrient management
The process produced a concentrated solid that could be easily stored and applied when needed.
This promotes more efficient use of nutrients, as farmers are not under pressure to spread slurry simply to manage slurry levels, which can lead to nutrient wastage and increased pollution risk.
3. Sward contamination
After five weeks, there was no significant difference in leaf contamination between ground that had received no nutrients and plots that had received the separated solids.
Cows could also graze a week after applying the solids, two weeks sooner than after slurry application.
4. Flexibility
At the point of solid/liquid separation in the decanter centrifuge (See “Slurry de-watering and nutrient capture: How it works”), the liquid fraction contained less total nitrogen than the 0.5kg/cu m permitted under the AHDB’s Nutrient Management Guide RB209 for “dirty water”.
Under current guidelines, this separated liquid could be spread all year round, alleviating pressure on slurry stores.
Solids could also be exported if not enough land was available. They could provide valuable nutrients for arable farms or be used in anaerobic digester plants.
5. Discharge into watercourses
Recent data indicated that the total nitrogen level in the treated water at the end of the process was below the 15mg/litre required to meet discharge consent limits.
So if a discharge licence was sought and approved, the water could enter watercourses.
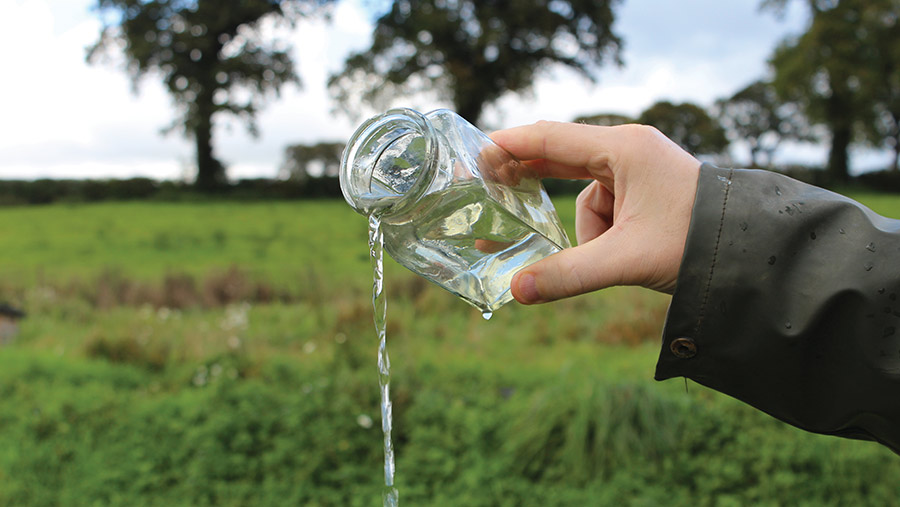
The water at the end of the process, which should be clean enough to go into watercourses © Aly Balsom
Scope for commercial use
Neil says the system shows promise, but cost would prohibit uptake by many farmers. For a 250-cow herd, he estimates a cost of about £165,000, excluding the reed bed.
The reed bed used in the trial cost £140,000, but this could be cheaper if a farm did its own groundwork. Operating costs are about £15/cu m of slurry.
As an alternative, the process could be stopped after the decanter centrifuge stage, as this would produce a liquid that could be applied as dirty water.
This would save £60,000 on the cost of a dissolved air flotation unit and avoid the cost of the reed bed.
A three-phase electricity supply is also needed, plus a full-time operator to manage the system.
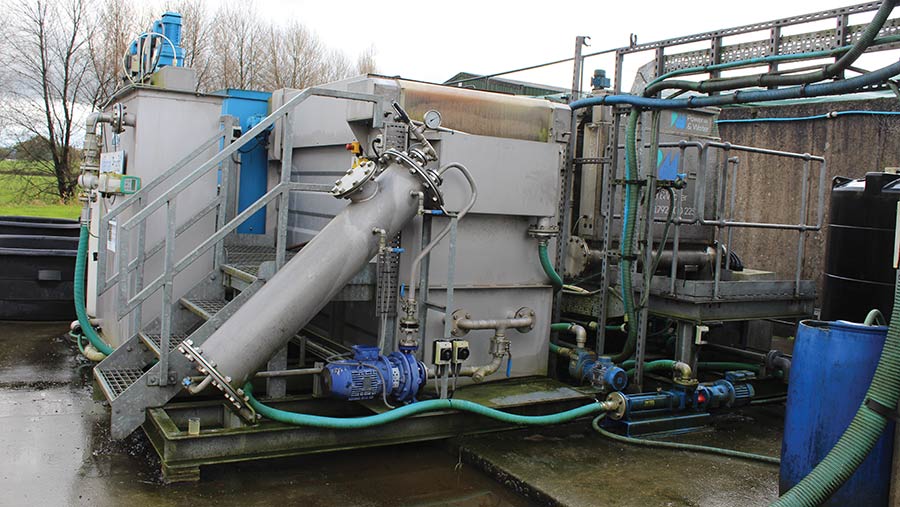
The dissolved air flotation unit © Aly Balsom
As a result, Neil sees the system having a role in:
Larger herds
The cost of the system makes it more relevant to herds of more than 500 cows. Larger equipment would be needed than that used at Coleg Sir Gar, which would be more expensive, but not double the cost.
Regional treatment facilities
A centralised treatment plant with a slurry dewatering system and biochar production would allow farmers to export excess slurry to a central hub.
Methane could be collected from a covered slurry lagoon, converted into fuel and used to power trucks to collect the slurry from farms.
After the de-watering and nutrient capture process at the hub, liquid could be discharged into watercourses and the solid processed into biochar.
Biochar is produced when organic matter is carbonised at high temperature in the absence of oxygen.
Neil says biochar has numerous benefits, including improving carbon sequestration when applied to land, and lowering methane emissions by 15-50% when used as a feed supplement for ruminants.