Contractor retrofits nutrient analysis to Claas Jag 830
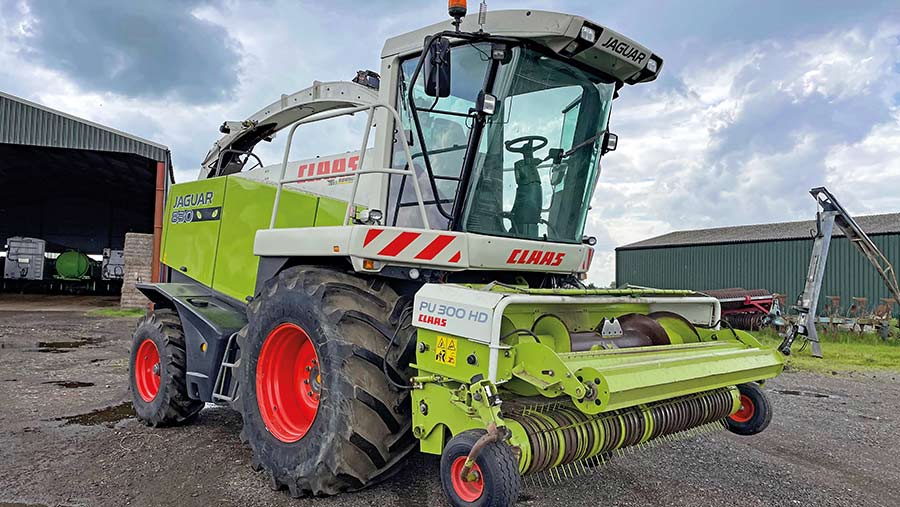
Keen to get a better handle on the dry matter content of his Italian ryegrass destined for local anaerobic digestion plants, Ady Drewery invested in a near-infrared system for his forager harvester.
Prior to this, he either had to send a sample to the anaerobic digestion (AD) plant for testing or take a punt on the crop being ready.
The former often meant sacrificing precious harvesting time, and the latter ran the risk of losing money either from deductions or lost weight due to harvesting when it was too dry.
“It needs to be cut at about 28% dry matter and there’s not much room to manoeuvre,” says Ady.
“Obviously, the plant won’t be happy if it goes in too wet, and if it’s drier than 28% I’m losing valuable tonnage.”
Plus, having his own set of readings meant he wouldn’t be entirely relying on information given to him by his customers.
After seeing a Harvest Lab near-infrared (NIR) sensor working on a John Deere forage harvester, he was convinced such a system would significantly streamline his operations.
But with 142ha to cut, he couldn’t justify upgrading to a more modern chopper already fitted with the kit.
So, instead, he went in search of a retrofit option for his tidy 2009 Claas Jaguar 830.
See also: How to get more from slurry and silage kit with infrared sensors
Evo NIR
The most affordable offering came in the form of the Dinamica Generale Evo NIR system sold in the UK by North Yorkshire firm Greenforage.
Three years ago, this set him back about £16,000, fully installed and set up, although he did cut the hole in the spout for the crop-sensing lens to get a glimpse of the material as it whizzes by.
For such a sophisticated piece of technology, there aren’t that many elements to the system.
The sensor itself mounts on the spout and this feeds information directly to a control box in the cab.
Here, Ady can view real-time dry matter and yield readings as he is cutting, as well as grass quality data such as metabolisable energy, sugar, protein and fibre.
“For me, the dry matter and yield readings are the only ones of interest, but there’s a lot more on offer for those who want extra information.”
Since Greenforage installed the system, Ady hasn’t had to carry out any additional calibration and, after three seasons’ work, it is still tallying with the AD plants’ testing equipment.
At the end of the job, the results for each field can be transferred onto a memory stick or sent via a 3G modem to the firm’s Field Trace cloud software.
This information can then be downloaded to the office computer.
Harvesting
According to Ady, the system is simple to use, with little more effort required than turning on the box in the cab before pulling into the field.
For the first couple of heavier early cuts, he typically mows with a front-and-rear Fella setup on one of his McCormick X7.680 tractors.
He’ll then ted it out and leave it down for a day, before rowing up.
However, for lighter cuts later in the season – he can take as many as five – he’ll often reduce the workload by direct cutting with a 6m Direct Disc wholecrop header.
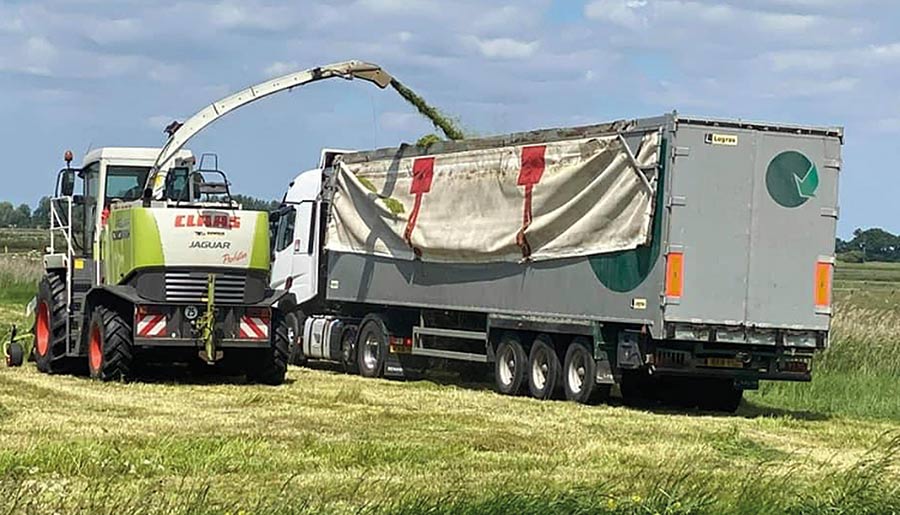
Claas forager with NIR © Ady Drewery
Another time saver is the fact he loads directly into his own walking-floor HGV trailers, towed by Renault tractor units.
These can hold about 30t of grass, which is significantly more than standard tippers, and means he has fewer journeys back and forth.
The tall sides make loading a challenge, but thanks to a camera on the spout, he’s able to see what he’s doing.
The HGV drivers have the biggest battle though, as they are far ahead of the forager when loading the rear of the trailer and have no reference point.
“We get by with constant communication on walkie talkies, but it isn’t easy for them,” he says.
For opening out, or when the ground is a bit too soft, he also runs a handful of tractor-drawn trailers.
When using these, they’ll typically tip in his yard, where a JCB 437 loading shovel will transfer the crop into a waiting HGV.
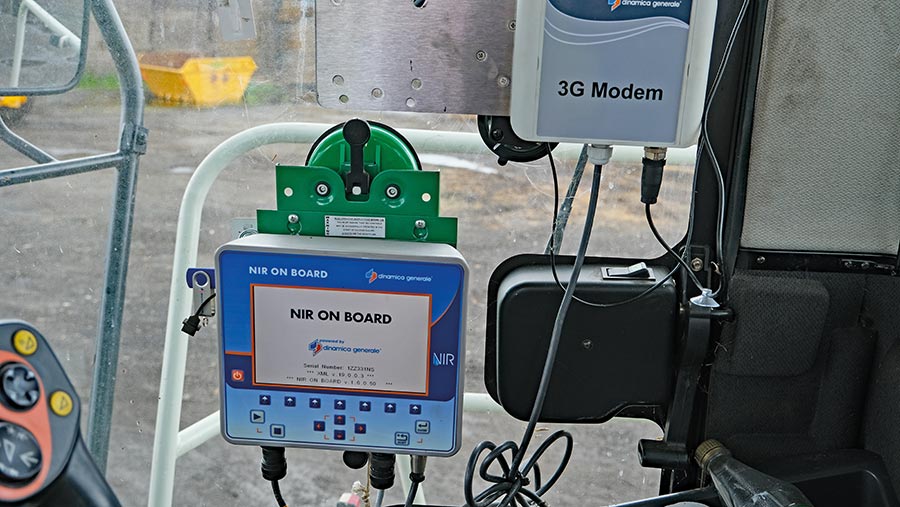
In-cab controls © Ady Drewery
Reseeding
Yield is crucial for making a profit when providing grass as an AD feedstock, and Ady is looking for an average of about 37t/ha.
For this reason, his Italian ryegrass is on a strict two-year rotation.
When each block is due for renewal, it is generally ploughed down to reduce the risk of volunteers, and power-harrowed to get a decent seed-bed before the seeds are put in with a Moore Unidrill.
His heavy clay soils require careful timing and plenty of horsepower to achieve good establishment, so he is considering trialling a less intensive cultivation regime, as well as direct drilling.
With the plough-based system, the ground can also be a little fragile for carrying HGVs in the early part of the first year, so he sometimes reverts to using tractors and trailers.
But if he can get good results without turning the soil over, he might be able to travel earlier with the trucks.
Digestate hauling
Another arm of Ady’s business is hauling both solid and liquid digestate away from AD plants, ready to be spread by fellow contractor R Hyslop & Son.
His four BMI walking floor trailers are used to move the solid material and he has a fleet of VanHool tankers for carting the liquid.
Together, these will shift 600-1,200t of digestate/day, mostly in Lincolnshire. However, he does travel as far as Hampshire.
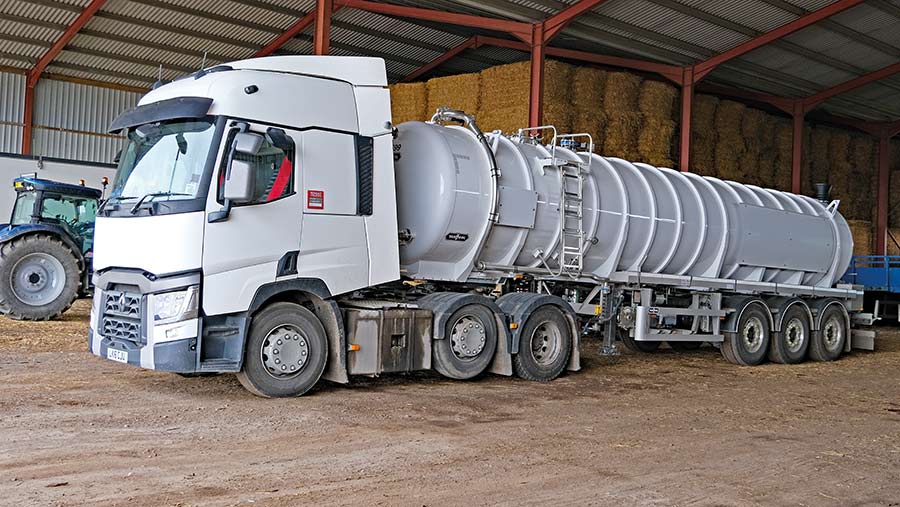
Digestate tanker © James Andrews
Getting to grips with near-infrared systems
Near-infrared (NIR) systems work by shining a beam of broad-spectrum NIR light at the silage, slurry or grain that needs to be analysed.
Depending on the make-up of the sample, different amounts of this light are absorbed, reflected or scattered when they contact it.
A sensor within the system records the quantity of light being reflected back off the material and compares the figures it receives to a database of samples tested in a lab.
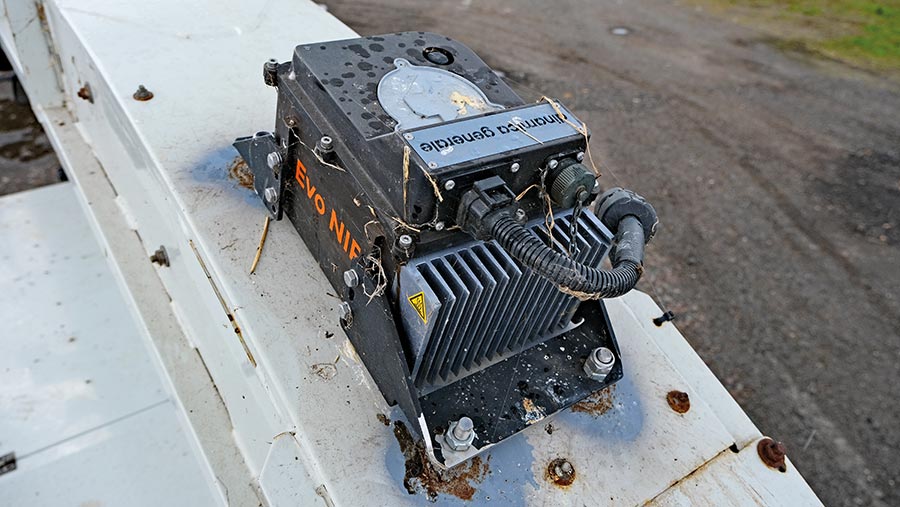
NIR sensor © James Andrews
Many readings can be taken per second, and providing the reference data is up to date, the results should be very accurate.
Thanks to its ability to improve the accuracy of applications, NIR systems are sometimes eligible for grant funding, which helps make them more affordable.
But if paying full price, the Evo NIR 4.0 system from Dinamica Generale costs £15,000-£20,000, depending on the configuration.
The same unit can be used on both forage harvesters and slurry applicators, with the latter offering the ability to measure nutrient content, such as nitrogen, phosphorous and potassium.
If a user wants to quantify a constituent that isn’t included in the system, Dinamica Generale offers a service to add it.
The tech-savvy can also do this themselves, as the software is open to having new calibrations added by a third party.
For those with a modern forager featuring an isobus-compatible screen, the Evo NIR will connect directly into this.
However, there is still the option of using the firm’s own smart display.