Military trucks converted into spray bowser and fert flatbed
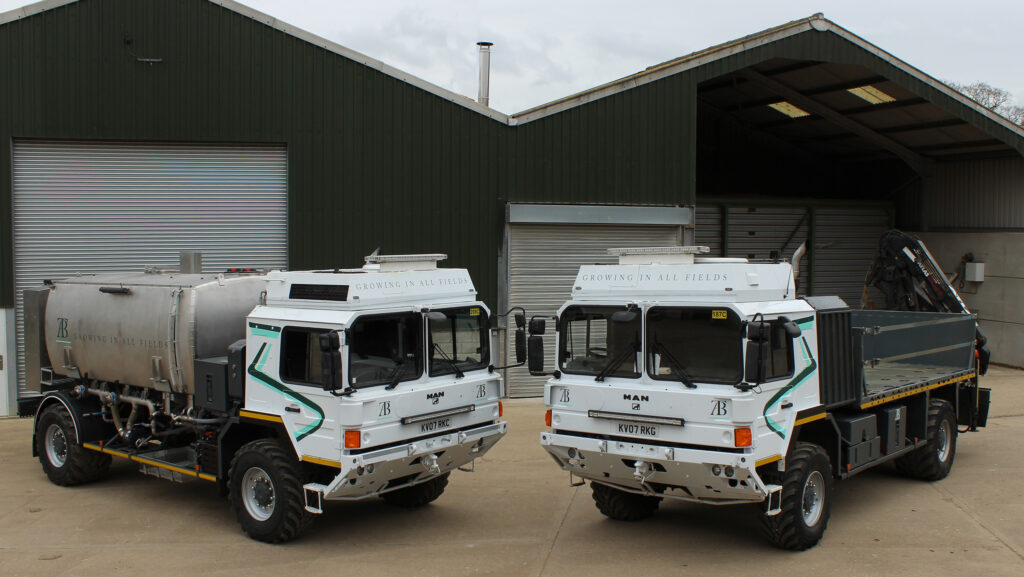
Drilling, spraying and fertiliser spreading across the 3,850ha farmed by the Bone family in Hertfordshire may not be run with military precision – though it is a pretty slick operation – but two ex-army trucks do play a crucial role in getting maximum capacity out of field equipment.
One is kitted out as a flatbed to carry eight big bags of seed or fertiliser loaded and off-loaded by a rear-mounted Atlas hydraulic crane, and the other carries a 9,000-litre stainless steel tank with all the facilities needed to operate as a spraying bowser.
See also: Driver’s view: Ryetec self-propelled lime and fertiliser spreader
“We don’t like having a costly tractor sitting idle on a trailer or bowser when it could be earning its keep,” says James Ashley, farm operations manager at AT Bone & Sons.
“The trucks are ideal for their roles, with a good road speed, flotation tyres for in the field, and capacity matched to the equipment they support, all resulting in efficient fill-ups.”
Military vehicles
The trucks
- Model MAN KAT A1 4×4
- Engine 330hp MAN six-cyl diesel
- Transmission Eight-speed ZF torque converter auto; two- and four-wheel drive
- Top speed 56mph
- Tyres Alliance Flotation 398 HS 445/65R 22.5 MPT
- Suspension Uprated multi-leaf spring
Flatbed
- Capacity Eight IBCs
- Deck Extended chassis, webbing strap side restraints
- Crane Atlas 120.2E; 1t lift at 9m reach
Bowser
- Capacity 10,000 litres in three compartments
- Tank Watson & Brookman stainless steel
- Pumps 1,270-litre/min centrifugal water pump, 500-litre/min diaphragm chemical pump
The two trucks, purpose-built by lorry maker MAN for military work, were purchased for £27,000 each with about 25,000km (15,500 miles) on the clock.
The total cost came out at around £50,000 for the flatbed and £60,000 for the bowser – a very worthwhile investment as far as the farm team is concerned, given that a bowser trailer can cost upwards of £30,000 before putting a tractor on the front at £40-£50/hour.
Low hours in relation to vehicle age is typical of army hardware that has to be kept in good shape and available for deployment at a moment’s notice but doesn’t get a particularly hard life in the meantime.
Selectable four-wheel drive makes them competent off-roaders, a 330hp six-pot diesel gives them plenty of oomph, while power steering and an eight-speed ZF auto transmission means they are a pleasure to drive on the road, notes James.
“We fitted a CB radio and air conditioning for a bit more comfort in what is a pretty basic cab,” he adds.
“The lack of anything fancy, which you would get in a commercial lorry, means there’s less to go wrong, and actually they’re quite fun to drive.”
Seating for a driver and two passengers and good visibility add to the appeal of a pair of trucks that have some quite lengthy runs given the extent of the business’s in-hand and contract farming operations.
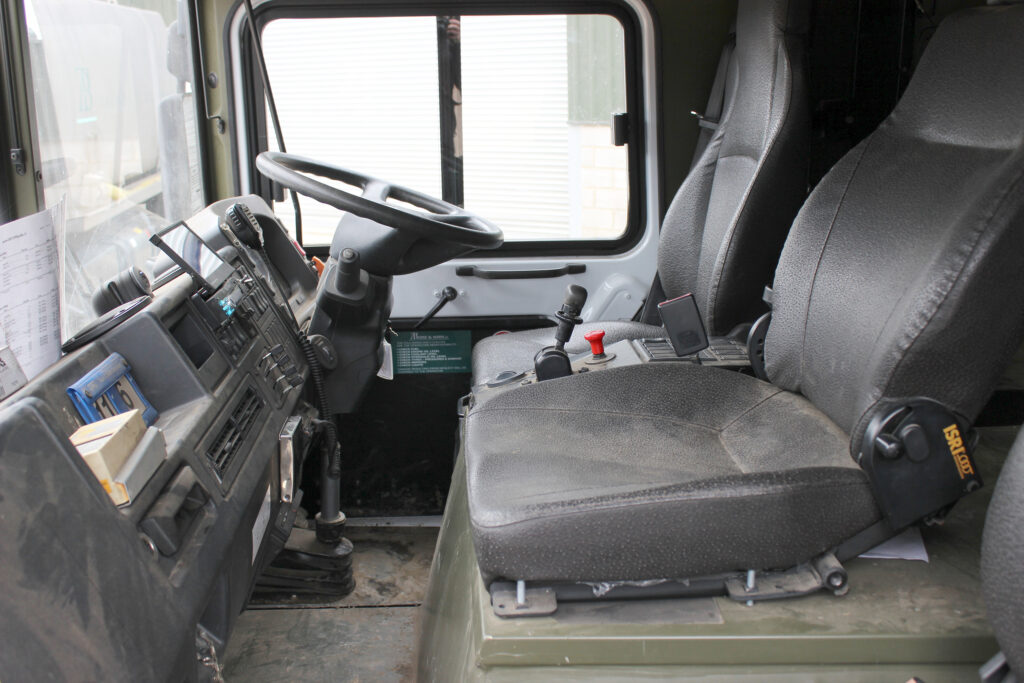
There is seating for the three in the full-width cab © Peter Hill
“They’re also a lot less bulky and imposing when driven along country lanes and through villages,” James adds. “And we’re conscious that we need to farm with the least negative impact on other people in the area.”
Modifications
Once driven into the busy yard at AT Bone & Sons’ Clements Farm base near Hertford, thoughts turned to the changes needed for the trucks’ new roles carrying farm inputs rather than artillery shells and other military hardware.
Directors Russell and Daniel Bone, together with operators and the workshop team, pooled ideas for the conversions and drew on their experience of the similar MAN and Renault ex-army trucks operated previously.
Once the engineering work was completed, both were shot-blasted to bare metal and given a handsome livery consisting of a grey chassis and a white cab, finished off with yellow reflective strips down the sides and numerous LED hazard and work lights.
Mechanical changes include additional leaves for the leaf spring suspension – an upgrade by Paddington Springs in Wembley that increased the 7.5t standard payload capacity to about 10t – and a new set of 10-stud rims produced by Brocks Wheel & Tyre.
These are shod with Alliance Flotation 398 HS radials in the size 445/65R 22.5 MPT, providing more favourable in-field characteristics than the stiff originals, while still having a 62kph (38mph) speed rating.
On both vehicles, the spare wheel cradle behind the low-slung cab has been ditched to make way for deck access steps on the flatbed, and on the bowser, one of two storage lockers that came with the vehicles.
These are still in their original locations on either side of the chassis on the flatbed truck, which also has a carrier for a spare press wheel for the farm’s Vaderstad Rapid seed drills, and an airline for blowing down the drill when switching between different crops.
Carrying capacity
Other kit located between the cab and original deck, comprising a hydraulic oil tank, much of the MAN six-cylinder engine, and the cooling radiator with a large side-mounted perforated steel screen, could not be moved without excessive engineering work.
So the flatbed truck has a rear chassis extension to mount a second-hand Atlas hydraulic crane without reducing the load area of the original deck, which has more suitable head- and tail-boards installed along with a pair of load-retaining webbing straps down each side.
“The finished truck has space to carry eight 1t bags of fertiliser or seed, and the hopper on our Amazone ZG-TS 10001 trailed spreader will comfortably take 8t of fertiliser,” James says.
“So we have a two-man operation – one on a Fastrac 4220 pulling the spreader and one on the truck ferrying and loading.”
The flatbed also supports the company’s two 8m Rapid drills, and the 12m Amazone Condor tine drill used for all the oilseed rape and for cereal crops when soil type and ground conditions allow.
Similarly, the bowser truck is capacity-matched to the new 8,000-litre Horsch self-propelled sprayer that replaced the farm’s 6,000-litre version this year, as well as the 4,000-litre Bateman unit, both on 36m booms.
Like the Watson & Brookman tank, the plumbing is a stainless steel and plastic work of art, with couplings purposely positioned at a comfortable waist height and easily accessible down the offside of the vehicle.
Sprayer filling
For fill-ups, the bowser truck is reversed into a bunded shed where an equally neat set of fixed pipes and couplings give access to a water supply, the liquid fertiliser storage tank, and a means of taking onboard materials such as manganese and other low-volume products.
These are contained in a 1,000-litre – one IBC-worth – compartment at the front end of the tank, with the rest divided into an 8,000-litre section of water for the sprayer and 1,000-litres of clean rinse water.
At present, spray mix is prepared in the field but there are plans to move that to the water filling point alongside the secured chemical store in the same building.
The bowser truck’s built-in auxiliary hydraulic drive is electrically operated to power the two pumps individually or both at the same time – a 1,270-litre/min Pacer centrifugal water pump and a 500-litre/min Annovi Reverberi diaphragm pump for the chemical.
Pipework is all 3in for the main tank and 1.5in for the chemical tank, and an important addition is the compressed air used to purge the pipe when filling to avoid any spillage.
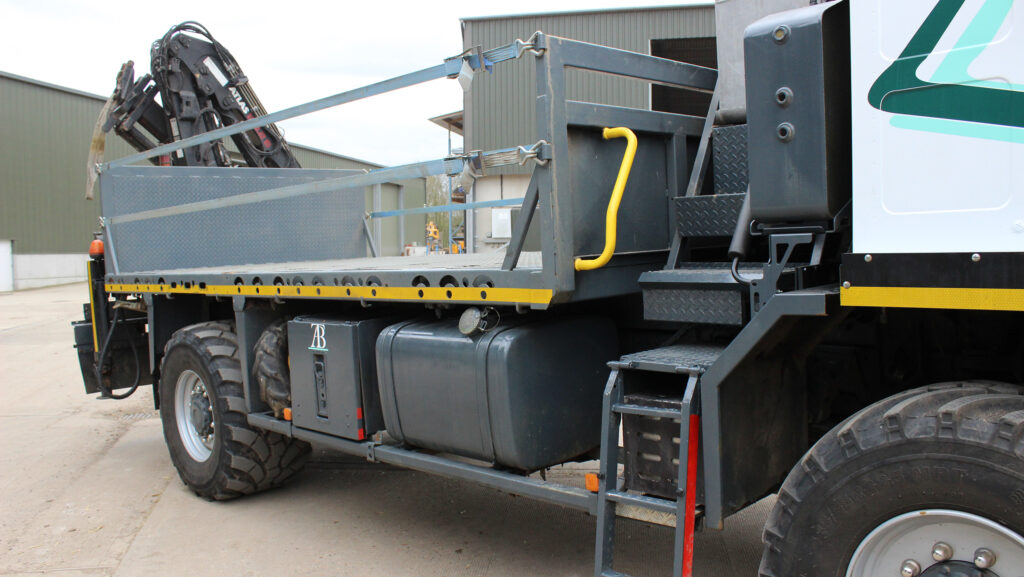
Fuel tank, storage locker and space for a spare drill wheel © Peter Hill
A large cabinet at the back, with one compartment accessed by a door lifting on struts and a smaller one via barn doors, provides storage for protective clothing and the other essentials needed for a day’s spraying.
“To get maximum output, each load is pre-mixed at the store, loaded and then taken to the field, where the truck will be taken along tramlines if necessary to get to wherever the sprayer needs re-filling,” explains James.
“That way we eliminate as much downtime as possible and get maximum output from the big sprayers.”
A multi-operation business
Farming remains at the core of the AT Bone & Sons business – 80% of cropping is oilseeds, wheat, barley and gluten-free oats, plus maize and sugar beet.
But the team led by Russell and Daniel Bone – and now involving Russell’s daughter and fellow director Becky – have turned it into a diverse business offering sports and amenity ground services, civil engineering and buildings construction, and road transport.
And its environmental operations include the production and spreading of about 50,000t a year of green waste compost from woodland and hedge management.
Ex-military trucks are not the only vehicles subject to conversions as the business has created several light truck-based spraying vehicles for amenity grounds spraying.
Its most recently completed project is an amenity spraying rig based on a new Lindner Unitrac “alpine load carrier” reckoned to be the only one in the UK.