Options expanded for closed-transfer sprayer filling
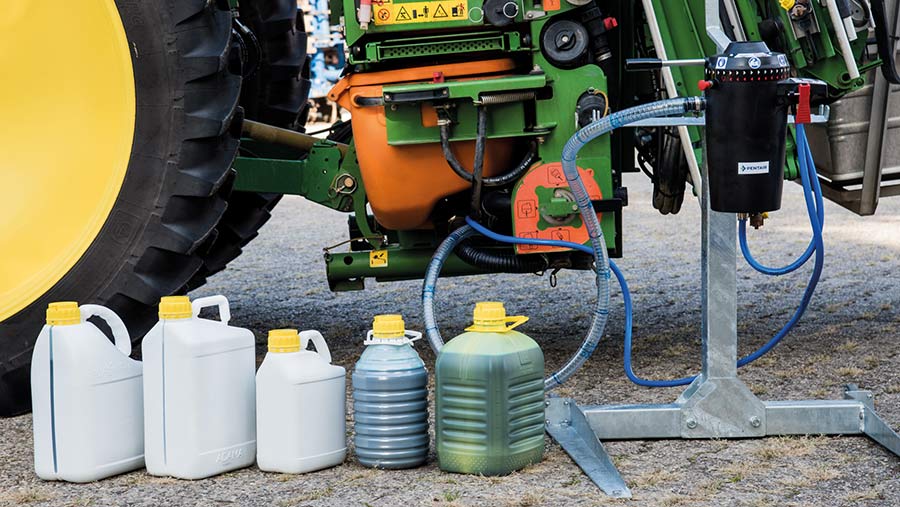
Serious concerns about operator and environmental safety when climbing onto sprayers to pour neat chemical into the top of tanks were raised by safety regulators as far back as the 1980s.
After many years and plenty of disagreement on a common approach to eliminate this risk, it finally looks as if the foundations have been laid for closed-transfer systems (CTS) to become the norm for sprayers across Europe.
The first big step forward has been major agrochemical manufacturers agreeing to use the EasyConnect system, originally developed by BASF, on a large range of liquid pesticide containers with capacities of between 1 and 20 litres.
The EasyConnect Working Group (ECWG), which has been driving the introduction of CTS, is now 10 strong and other parties are interested in joining, including those selling biological products and liquid fertilisers.
See also: Driven trailed sprayer axle cuts downtime for contractor
Primary parts
Two components are central to the system – the cap and a coupler. The pre-fitted cap locks into the coupler, which pushes a probe inside to release its plastic seal, thus allowing the chemical to be drawn out.
The container is then rinsed, the probe removed, and the container released for disposal. If using a part can, the probe is withdrawn, the seal snapped back into place and the coupling and transfer lines rinsed before the container is freed.
This agreed standard solution on packaging has been important, but not having an ISO standard for CTS equipment was causing problems for engineers of coupler systems.
That changed last year when ISO 21191 was published. It defines exactly what a CTS is, and outlines the characteristics and criteria that the systems must meet to comply.
This will be reinforced by a large-scale CropLife Europe (formally the European Crop Protection Association) study, which is testing three systems applying for ISO certification.
It aims to show more than 90% operator exposure reduction when using the GoatThroat, easyFlow M and Cleanload Nexus, setting a benchmark for future systems to adhere to.
Tightening regulations
Regulatory requirements for CTS are starting to appear in Europe, with the Netherlands making it compulsory on liquid formulations by 2024.
Denmark will follow a similar path by 2024-25 and Belgium by 2026, while the Czech Republic already stipulates about 12 separate products must be used in combination with CTS, and a blanket requirement is under discussion.
The UK doesn’t yet have any concrete targets, but engineering controls have long been part of Control of Substances Hazardous to Health risk assessments and can replace personal protective equipment where CTS is shown to provide equal or better protection.
A key driver here could be water companies – each year they spend millions of pounds cleaning pesticides out of raw water to meet drinking water standards.
To try to rein in these costs, many are working at catchment level with farmers to reduce pollution at source. One example is the voluntary Seven Trent Environmental Protection Scheme (Steps).
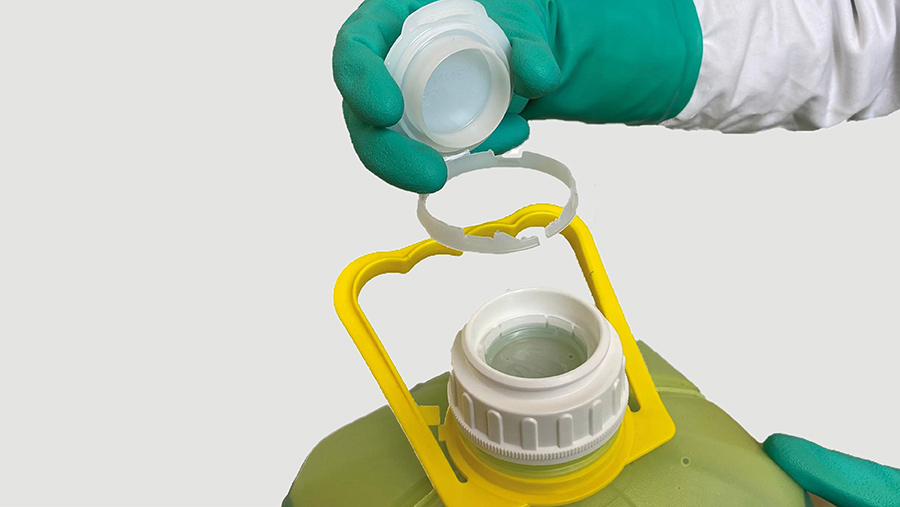
© Pentair
Grant funding
Steps is essentially a grant programme where the firm will provide farmers with up to £30,000/farm/year (up to 2025) to help make changes that will improve catchment water quality, including the reduction of pesticide pollution risk.
Seven Trent’s Alex Cooke says it is match-funding, so the company expects farmers to be investing an equal amount themselves.
Items reducing pesticide risk, such as wash-down areas and biofilters, are looked on favourably during applications, she adds.
“We see closed transfer being part of [the scheme] – we are already being asked about closed-transfer systems by our farming community. They want to invest in it, but we are not quite at that point. As a water industry we are keen for this to go ahead as quickly as possible.”
Sprayer operators that have been testing EasyConnect have been very positive about its performance, and Nick Light of Suffolk-based EJ Barker & Sons is in his third season with a Cleanload Nexus.
He is excited by the co-operation between product manufacturers and the publication of the ISO, which should lead to CTS becoming a standard offering on crop sprayers.
Faster filling
Mr Light has been using a standalone system installed in his fill-up area, which is attached to the sprayer’s suction side with a dry-break coupling, and one surprise has been how quickly it fills through the CTS.
“For an inexperienced user, filling will be as quick as pouring into an induction bowl, but once you are up and running it’s about 10-20% faster,” he explains.
The ECWG’s implementation plan suggests a launch of the system on some products in Denmark and the Netherlands this year, with the UK, France and Germany to follow in 2023.
Further countries and products will be added during 2024 and 2025, when the product portfolio compatible with EasyConnect is expected to be complete.
So, what are the coupler systems that farmers can or will be able to buy as EasyConnect is rolled out? We examine the options.
1. Cleanload Nexus
One system that is already being tested on farm is Pentair Hypro’s Cleanload Nexus.
Connected to the sprayer’s venturi system either permanently or by using dry-break couplings, it is entirely mechanical and has just two manual controls.
The first is a lever that locks the cap in place. Rotating the lever controls the emptying rate, which is between 0.5 and 1 litre/sec at -4bar pressure, depending on liquid viscosity.
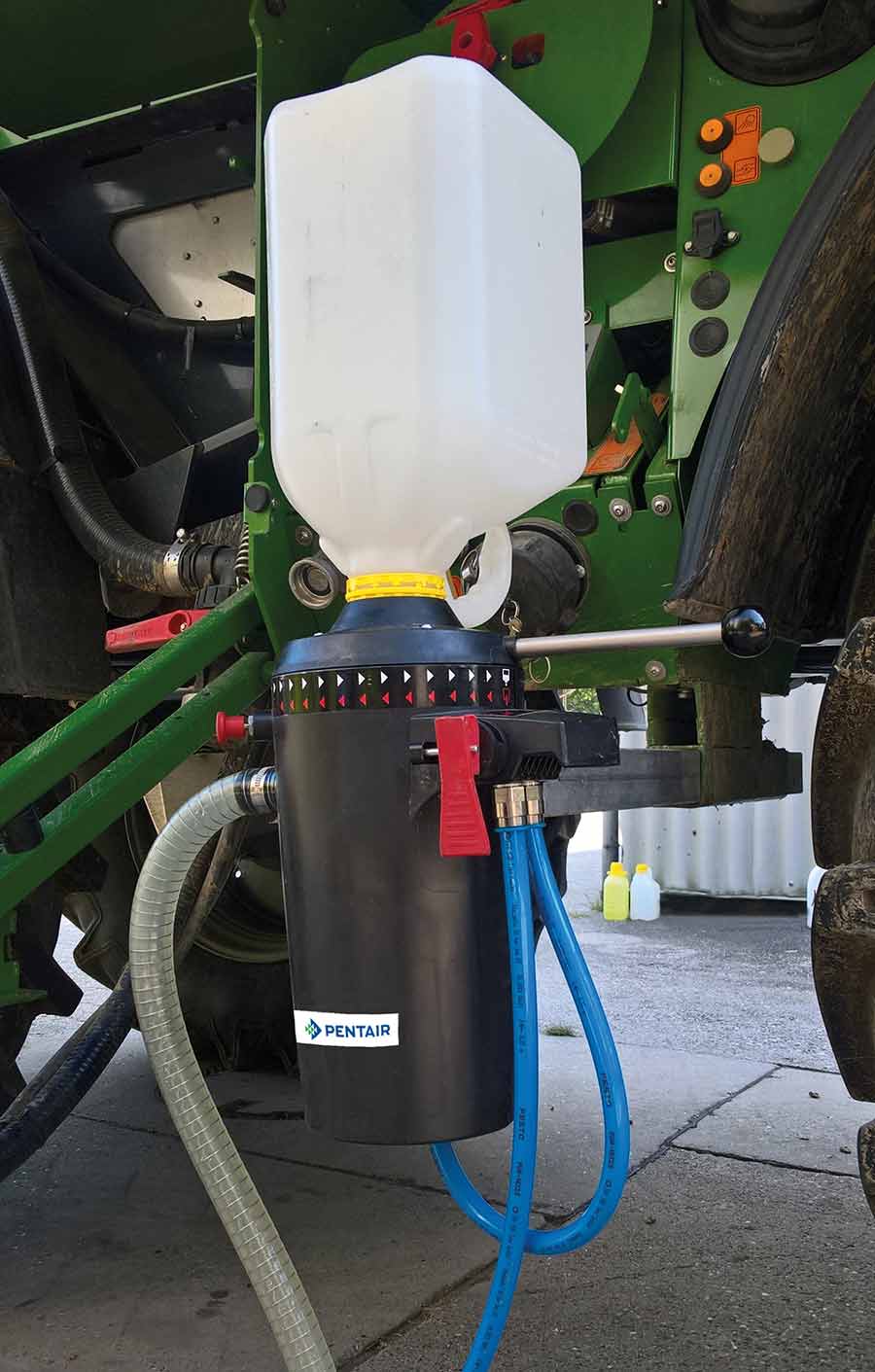
© Pentair
For dosing, it relies on the operator using scale markings on the side of containers or the hose connected to the sprayer when dealing with larger volumes.
These methods cannot achieve the ISO +/- 2.5% dosing accuracy, so the firm has developed a prototype dosing cylinder add-on that sits between the Cleanload Nexus and the sprayer.
This allows the operator to transfer the desired amount of neat chemical into the cylinder before it is sucked into the sprayer tank at +/- 1% accuracy, before the whole system is rinsed out.
The Cleanload Nexus is now being
produced at scale and the dosing cylinder is set to be launched at the EIMA machinery event in Bologna, Italy, in November.
The system won’t be sold direct, with sprayer manufacturers and dealers offering it as a new or retrofit option. It’s expected to add £3,000-£4,000 to the price of a new machine.
2. GoatThroat
Connecticut-based GoatThroat has supplied North American farmers since 2001 and will now look to enter the European market as uptake increases.
Its system currently works by attaching an adapter with a siphon tube to the product container, which is then pressurised, forcing chemical into a measuring cylinder before it is sucked into the sprayer. A clean water line then rinses the can and all transfer lines before decoupling.
The adapter can be left on containers if using part cans, with pipes attached via dry-break couplings.
The GoatThroat works with any container, from a 1-litre can to a 1,000-litre IBC with the appropriate adapter, and will be available with an EasyConnect-compatible version soon.
On some of its systems, pressure is applied with a hand pump but, for efficiency, operators are likely to integrate a compressor or use a sprayer’s suction to empty containers.
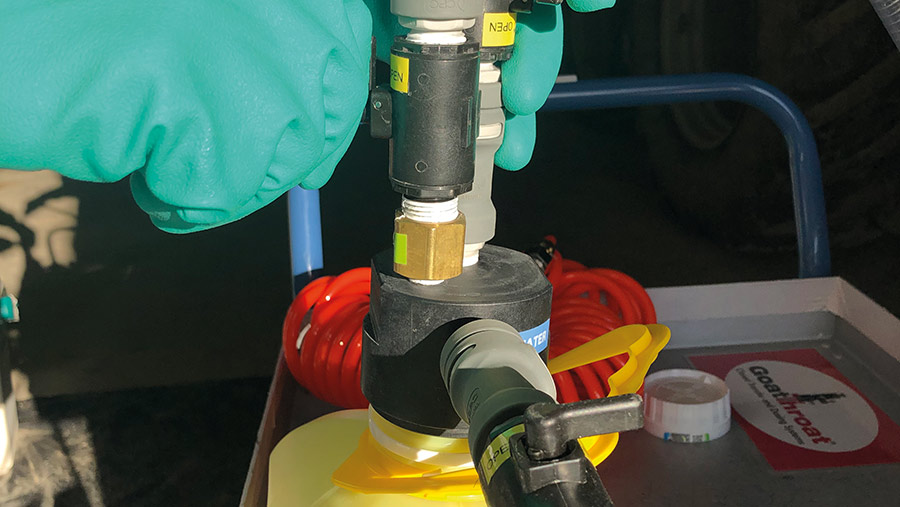
© GoatThroat
The GoatThroat can’t match the filling speed of alternative systems, but its measuring cylinder feature offers very accurate dosing down to 10ml, and is seen as a good option if using small quantities of multiple products, such as in some horticultural situations or research farms.
This is an area the company is looking to target initially in the UK and Europe.
GoatThroat president Nancy Westcott says the price for a standalone GoatThroat system will be about €700-€800 (£600-£680), with each additional adapter costing €50-€75 (£42-£64). This doesn’t include a compressor and plumbing into the sprayer.
The firm’s European contact is Belgian sprayer technology expert AAMS, which will be officially launching the system on 10 June to 150-200 fruit growers in Sint-Truiden, west of Brussels.
3. Tefen AccuRite
Tefen is well known worldwide for its dosing pumps and flow products, and is now entering the pesticide closed-transfer system market with AccuRite.
The Israeli firm says its priority was to make it user friendly and simple to use, and it has developed a simple digital interface to operate the filling process.
The operator simply switches it on to couple and lock on to the container, then selects full or partial emptying.
If partial, the desired amount is selected, the start button pressed, and the correct amount dispensed into the sprayer’s venturi suction system.
If a container is fully drained, it is rinsed and released for removal. Where a part-load is required, the can is sealed, and connections rinsed before releasing for storage.
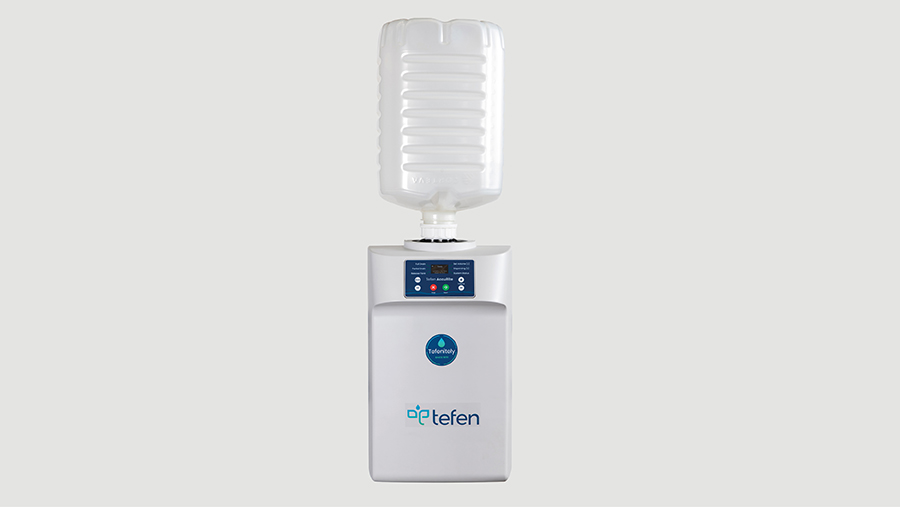
© Tefen
The company claims it meets all ISO standards, including +/- 2.5% dosing accuracy and, based on its market research, delivers a minimum of 0.5 litres during partial emptying.
However, this could be changed in the future should customers require dosing in smaller quantities, according to Tefen’s Chaim Schwartz.
Field testing will commence in Israel in June and July and, if all goes well, it should be ready for the wider market towards the end of 2022.
The cost of each unit to distribution is likely to be about €1,500-€2,000 (£1,270-£1,700), so with fitting and seller’s margin, overall cost is likely to be comparable with other similar options.
4. Agrotop easyFlow M
The easyFlow M has been on the market for about 10 years and is available through Essex-based dealer Billericay Farm Services.
Developed with the backing of agrochemical manufacturer Bayer, about 40-50 of the systems are said to be in operation on British farms, with Linking Environment and Farming-accredited businesses some of the beneficiaries.
Key to the standalone or integrated easyFlow M system is its adapter, which fits any container with a 63mm opening.
The adapter is screwed into place and a built-in knife cuts the foil seal when locked to the coupler. The system could be compatible with EasyConnect caps in the future.
Once securely joined to the top of the easyFlow M, the chemical can either be sucked straight into the sprayer or, if using part cans, via an integrated measuring unit just below the mounting point.
Empty containers are then rinsed before removal, or part cans closed, and adapter rinsed, before going back into store.
Most UK farmers tend to opt for a standalone easyFlow M unit mounted on a trolley with pipework and fittings.
The whole package costs about £1,200, but this might vary between sprayer brands.
Agrotop also offer a gravity-based system, where the coupler is fitted to the top of the tank on smaller sprayers.
This costs roughly €150 (£128) and additional adapters for storing part cans are €40 (£34) each.
5. Lechler prototype
Stuttgart-based application kit specialist Lechler is developing a prototype CTS that incorporates more electrification and automation than existing products.
A small metering motor automatically moves the probe that enters the container to adjust emptying rate.
Combined with an electronic valve, the firm claims this will facilitate automatic dosing to a set volume with the required +/- 2.5% accuracy, whatever the liquid viscosity.
The system will be controlled via a smartphone app, where the operator can choose partial or full emptying of product containers, and control the operating and rinsing processes.
At present, the concept is being tested and a first prototype could be demonstrated this autumn. If all goes smoothly, it could be ready for market in 2024.
Information for this article was sourced from the Association of Applied Biologists’ closed-transfer systems workshop at Silsoe Spray Applications Unit, Bedfordshire.
What about bulk containers?
The use of plant protection and crop nutrition products delivered in bulk containers is gaining popularity, and Wisdom Systems’ Fastran 850 helps safely transfer liquid from IBCs into the sprayer.
The Fastran assembly attaches to the IBC via a micromatic coupling and to the sprayer through a fitting plumbed into the venturi system.
The product is then sucked out of the bulk container via a dipstick and digital flow meter, which delivers the desired volume into the sprayer tank at a rate of up to 25 litres/min.
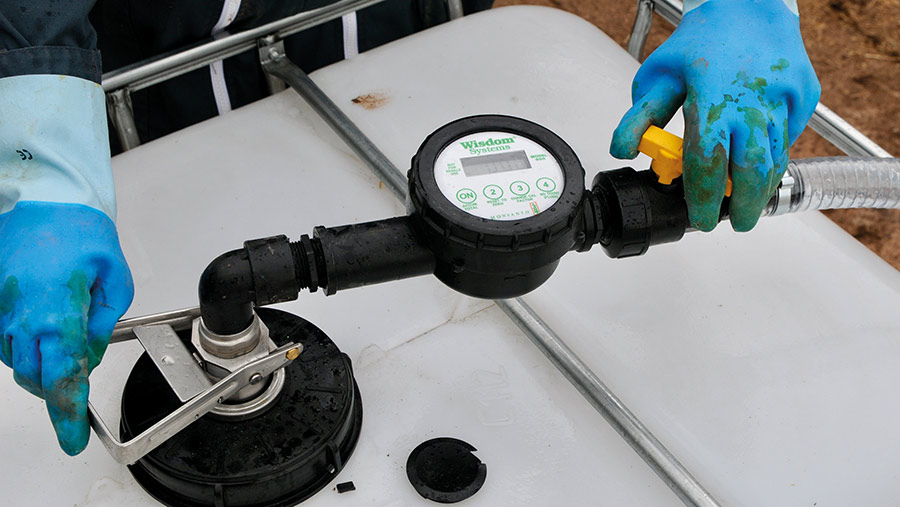
© Wisdom Systems
Rinsing of the coupling is possible with an additional clean water attachment that sits between the container and micromatic coupler, so it fully complies with the recent closed-transfer system ISO.
The device needs calibrating for different liquid viscosities, with Wisdom Systems providing calibration factors for a range of products, including some herbicides and macro- and micronutrients.
The company says it speeds up the filling process significantly, allowing operators to cover more ground in a day.
Packaging waste is also reduced, with some IBCs returned free of charge for recycling and other products being offered by distributor Frontier coming in refillable IBCs that are recycled after five years.
A Fastran 850 costs £595 and comes with a 3m hose with an open end. Customers then decide which couplings they use to attach the hose to the sprayer.
Manufacturer view – Andrew Tingey, Househam Sprayers
Househam Sprayers’ engineering manager, Andrew Tingey, sees a future where sprayers might be kitted out with three separate means of closed chemical transfer.
Current options include systems for liquid transfer out of containers up to 20 litres via the EasyConnect cap and transfer out of IBCs using Wisdom Systems’ Fastran 850, and all require plumbing into a sprayer’s venturi.
There is not currently a desire for the industry to find a solution for powder formulations, but that may change in the future.
Mr Tingey says the biggest challenge for manufacturers is how these systems will be engineered into sprayers, as there is unlikely to be a standard setup.
“There are several ways systems can be installed, whether that’s on a machine, off a machine, with quick couplers or hard connections.
“It comes down to understanding what each individual customer’s requirements are and adapting the installation to suit them.
“We are likely to choose our preferred system and promote it, but we’ll always be open to listening to customers’ needs and put a closed-transfer system together in exactly the way they want it to be,” explains Mr Tingey.
Where multiple systems are installed, he sees them working individually where 100% transfer efficiency is needed, with the potential of them all operating at the same time.
However, there could be issues with adequate back pressure and maintaining acceptable transfer rates, and the systems must be more efficient than traditional filling methods to be viable.
“There are going to be some more steps involved, but the benefits for reducing operator exposure are clear, and it gives an extra level of safety.”