Thompson Brothers’ bespoke umbilical slurry pumping trailer
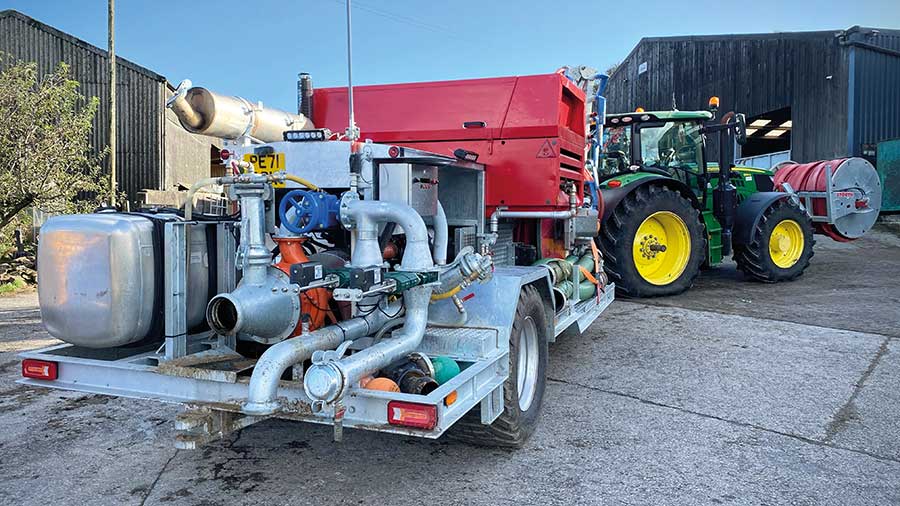
With the hourly cost of running a tractor soaring, Lancashire farming and contracting outfit Thompson Brothers decided to build a self-contained, remotely controlled umbilical pumping trailer.
This would save its prime movers mindlessly clocking time parked up with the pto spinning.
Previously, pto-powered pumps and compressors were charged with spreading up to 25m gallons of slurry a year, of which 1.3m gallons comes from the business’ own 240-strong dairy herd plus 300 followers.
See also:Â Simple 24m mounted sprayers for less than ÂŁ30,000
However, the tractors were roaring away to the tune of £17/clock hour – £8,500 for the 500 hours they might spend on the job annually.
This came with the added challenge of finding and paying someone to sit on the seat seven days a week during the spring peak.
The decision to design and build a pumping rig to reduce their costs coincided with a successful application for grant funding towards a second 12m Storth dribble bar and two bobbin pipe reelers.
This offered the prospect of drastically increasing their daily output.
Thompson Brothers’ self-propelled pumping trailer
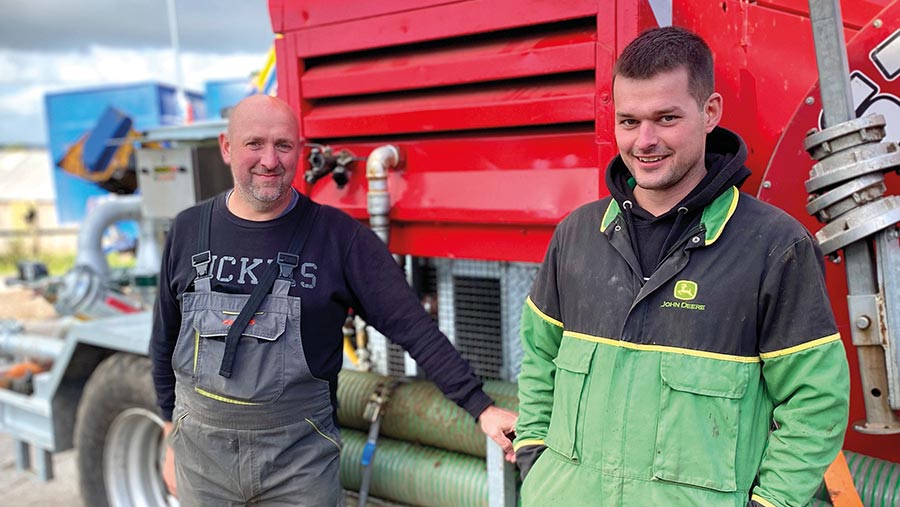
Mick Thompson and David Kirkham © MAG/Oliver Mark
- Engine 210hp Cummins six-cylinder
- Pump Doda
- Compressor Atlas Copco 275cfm
- Priming setup Home-made venturi system using compressor air flow
- Flow control Engine rpm and dribble bar flow meter
- Build cost ÂŁ43,000
Making the bed
Mick Thompson, the firm’s seasoned fabricator, was tasked with designing and building the trailer.
His challenge was to shoehorn in a reeler, compressor, engine, pump and suction pipes, and leave space for a dribble bar and reel to be mounted on the tractor’s linkage.
After sizing up the components, he welded together a 6m-long stepped frame and chequer plate bed, had it galvanised, and fitted artic trailer jacks to the corners.
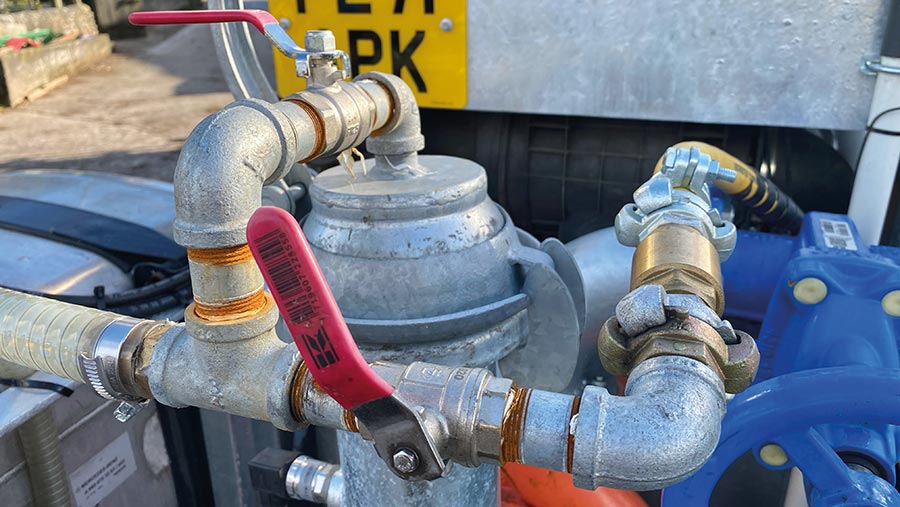
Mick Thompson built his own venturi priming system for just £30 © MAG/Oliver Mark
Below the bed went a single 10-stud axle with hydraulic brakes, sourced second-hand from Marshall Trailers in Aberdeen for just ÂŁ500, which he paired with new rims and a set of 550/45 R22.5 tyres.
At the back, there is a clevis hitch to drag a small trailer and, at the front, an extendable drawbar.
For this he used a 6m-long, 150mm box section steel, which offers the flex and strength required to stretch the outfit by 1.5m.
This leaves just enough space to accommodate the tractor-mounted attachments.
Cummins power
The engine was the centrepiece of the build, mounted directly above the axle and away from the compressor.
This makes it easy to get at and eliminates the risk of a hidden oil leak perishing any rubber pipes.
When it came to shopping for a suitable block, Mr Thompson had a good idea of what he was after.
“We wanted a simple Cummins six-cylinder without a common rail system and the complexities that go with it – that way I know I can fix it with a hammer and a spanner.
“Plus, spare parts are easy to get hold of.”
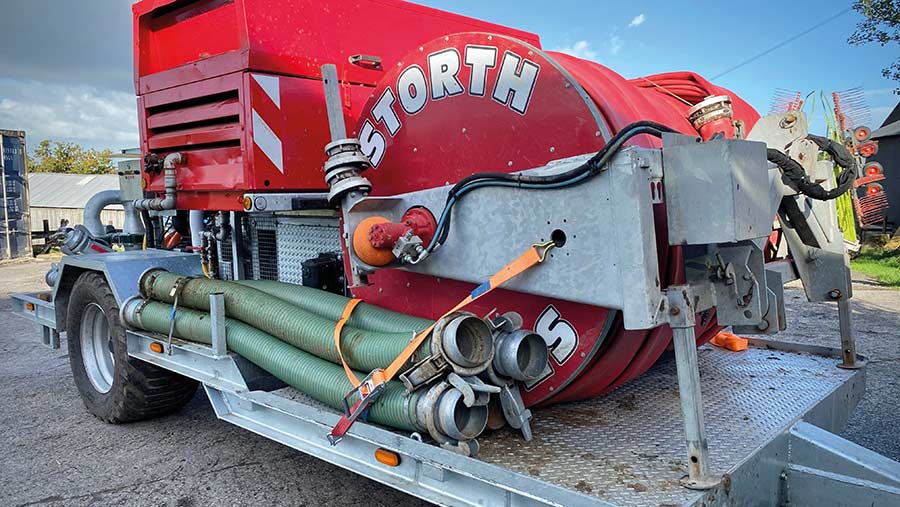
© MAG/Oliver Mark
That led them to a 210hp, 5.9-litre, six-cylinder 6BTA that was hacked off the front of a DAF fuel tanker by commercial vehicle breaker Walsh and Dearden at Darwen, just south of Blackburn.
“We had no idea how many hours it had done, but they fired it up and it ran sweetly,” says Mr Thompson.
It set them back ÂŁ2,200, plus another ÂŁ300 for the 390-litre fuel tank and exhaust, which had to be extended once positioned on the trailer.
The deal also included a radiator but, with concerns about heat dissipation given the engine would be static (rather than in a moving vehicle), it was upgraded to a copper core system.
While he was at it, Mr Thompson also decided to switch to a 12V system by fitting a new alternator and starter motor, making it easy to jump-start off the compressor’s power unit in the case of a flat battery.Â
Drive from the engine runs straight to the impeller. This means it rumbles along at 1,900-2,000rpm, which has reduced fuel consumption by about 12 litres/hour compared with the tractor.Â
“With diesel at £1/litre, that is saving us about £130/day compared with running the old tractor pump,” says operator David Kirkham.
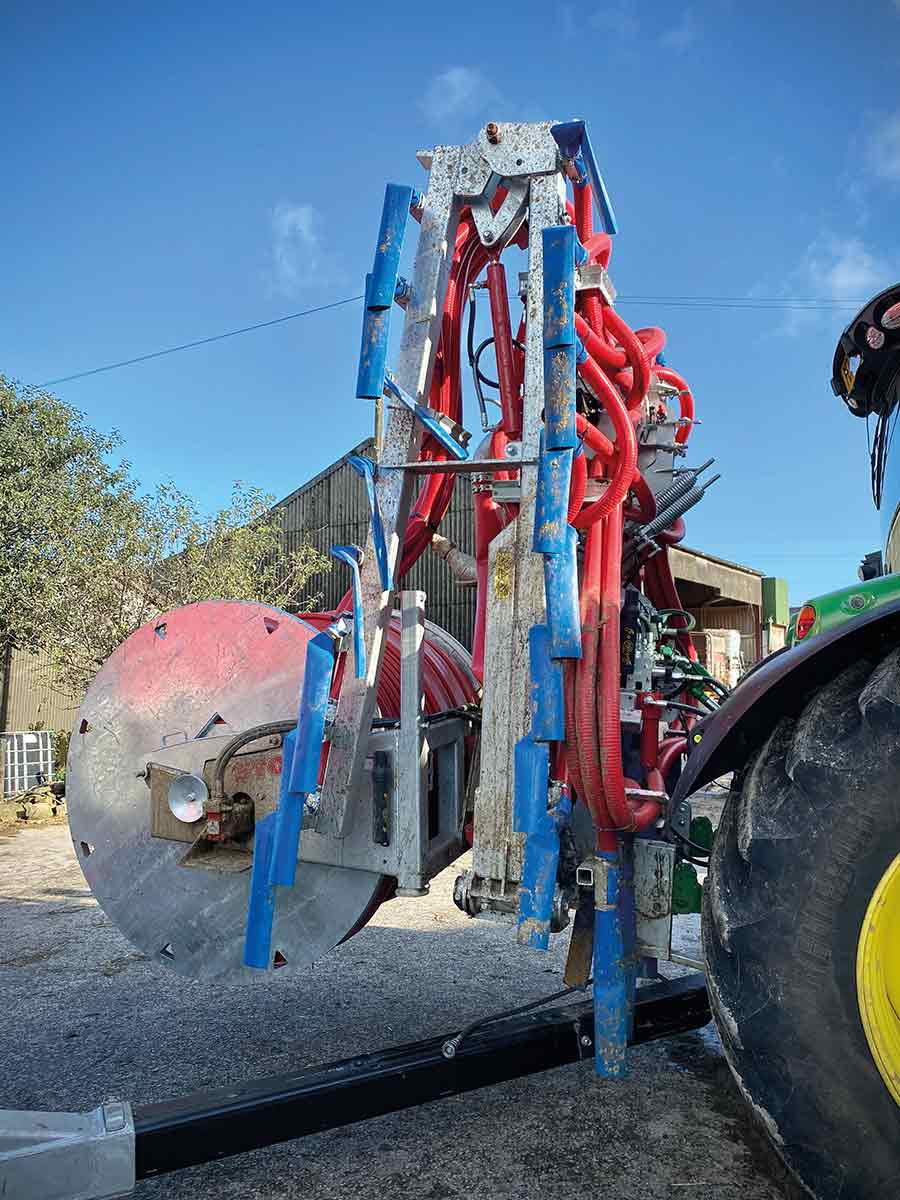
The tractor carries a dribble bar and up to 2,600m of pipe © MAG/Oliver Mark
Pump and pipes
The business already owned two Doda tractor-driven pumps, so they opted to stick with what they knew – an L35 Pedestal that uses the same impeller and seals as the others.
It is primed by a home-made venturi vacuum system, rigged up at a cost of just ÂŁ30.
This works by funnelling air from the on-board compressor through a reducer that halves the size of the bore as it passes the junction with the pumping line.
In doing so, the speed of the air increases, causing negative pressure that draws fluid through just seconds after the vacuum tap is opened.
A slurry mist then forms in the exhaust port, indicating that the system is primed.
“It’s so strong it could suck through a lump of concrete,” says Mr Kirkham.
“Plus, it’s simpler than a petrol-powered primer – there’s no faff of getting a petrol engine started, there is no need to find space for it on the trailer, and no risk of it getting pinched.”
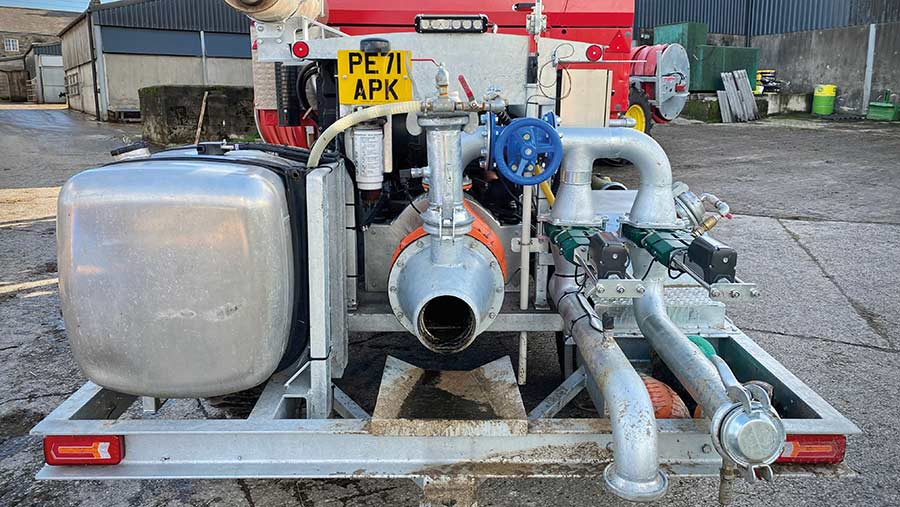
Knife gates determine whether the slurry is sent to the field or recirculated back to the tower © MAG/Oliver Mark
The main slurry pipe splits once it leaves the pump, with one line dedicated to spreading and a second for “return to tower” recirculation.
This is a simpler setup than a three-way valve, he says, with no risk of it clogging up.
The route the slurry takes is determined by 6in knife gates in each pipe, controlled by electronic actuators that open and close them to start and stop the flow.
A pressure sensor is mounted downstream of the knife gate on the spreading outlet, allowing the operator to monitor the flow of slurry.
During work, it’s typically at 6-8bar for application rates of 5,000-10,000gal/ha.
For situations where the pump is working halfway along an umbilical line, there is a second sensor on the input pipe to keeps tabs on the inbound flow and ensure the pump isn’t being starved.
Zero-effort blow-out
The most expensive single element of the build was the ÂŁ10,000 Atlas Copco compressor and accompanying 3.3-litre, four-cylinder Kubota engine.
This is rated to 275cu ft/min (cfm), which seemed a reasonable balance between what they already had.
Previously, they had a 90cfm that is too small for steep uphill runs, and a 350cfm version that would have been too big and heavy for the trailer.
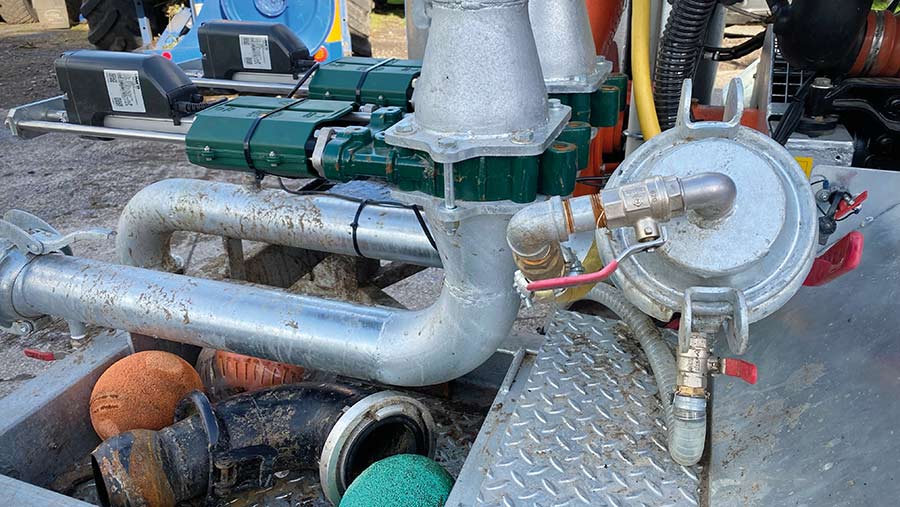
Pipe blow-out can be initiated from the cab © MAG/Oliver Mark
It’s permanently plumbed into the blow-out system, saving the operator wrestling with a tangle of mucky pipes at the end of the job.
And better still, it can be prepped for action when setting up, and operated entirely from the tractor cab.
To do so, Mr Thompson fitted a couple of one-way valves into the line, so the air taps can be opened and the sponge loaded prior to pumping.
Using this setup, there is no risk of any slurry finding its way upwind to the compressor.
When finished, the operator simply diverts the slurry flow to “return to tower”, waits for the “field” outlet pressure to fall to zero, and fires up the compressor to send the sponge down the pipes.
Remote control
Local firm Glasson Electronics was roped in to wire up the gauges and controls for the engine, compressor and electronically actuated flow gates.
This included several neat features, such as automatic cut-out if the engine temperature exceeds 90C or the oil pressure drops below 1.2bar.
Controls are duplicated on a trailer-mounted box and a terminal in the cab.
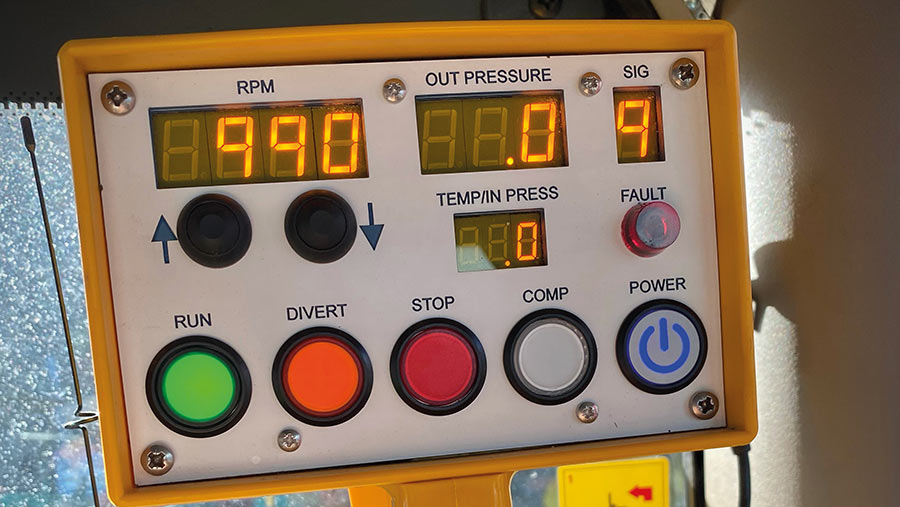
Remote control © MAG/Oliver Mark
Both can fire up the engine and alter its revs, turn on the compressor and divert the flow between the two output gates.
They show all the key read-outs, such as engine rpm, input pressure, output pressure and temperature.
But while the external box is hardwired to each element, the one in the tractor cab is plugged into an aerial.
This has a range of up to 16 miles on fenland, but more like six on the rolling hills of Lancashire.
How much did it cost?
The total bill came to £43,000 – a sum that won’t take long to claw back given the depreciation savings on the tractor, says Mr Kirkham.
“We’re saving hours on the tractor, have reduced fuel consumption and now have the capacity to carry 2,600m of pipe to each job.
“Plus we can run two dribble bars on single-pump jobs next spring, which is half of our workload, so it will really increase output.”