Autonomous sugar beet planting and weeding shows promise
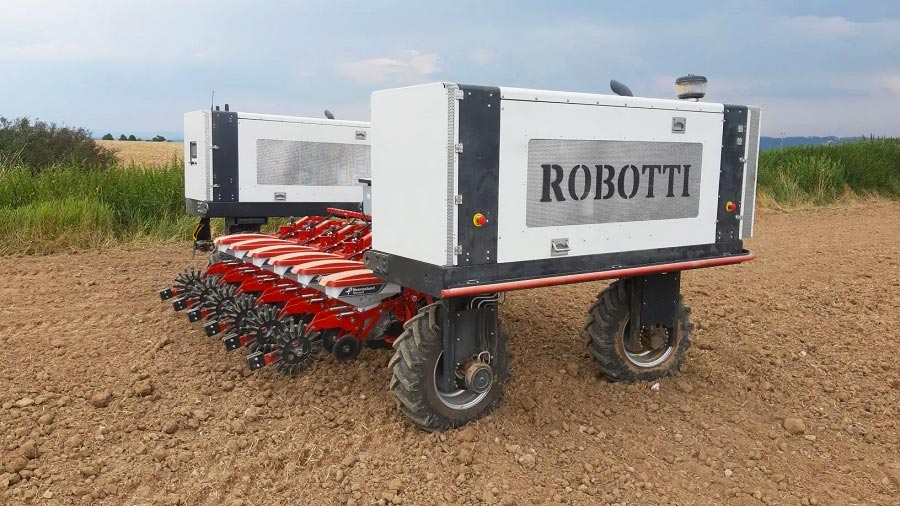
Sugar beet yields of 90t/ha from a field planted and weeded using an autonomous robot have underscored the potential of using a system that can reduce herbicide costs by up to 80%.
However, as with any new technology, first-year field-scale trials have also highlighted some of the challenges that still need to be overcome.
Around 150ha of sugar beet were drilled as part of the two-year project using an imported Robotti LR at two Sentry farms in spring 2022 in Cambridgeshire and Lincolnshire.
See also: How to control wireworm in potatoes effectively
A key aim for Sentry on its farms is to optimise applications, reduce waste and look after the surrounding environment, explains its director of farming, John Barrett.
“This project is a way of achieving that,” he says. “By drilling it with a Robotti there was reduced impact on the soil because of the lightweight machine and reduced use of herbicides.”
How it works
The Robotti LR, which was developed by Danish manufacturer Agrointelli and imported into the UK by Tom Beach at Autonomous Agri Solutions, works like a gantry system to carry various implements using a three-point hitch.
Powered by a 150hp Kubota diesel engine, computer-controlled and fitted with various cameras and sensors, such as lidar, that can identify and react to any hazards to avoid collisions, it can run for up to 60 hours before needing to be refuelled.
For drilling, a bespoke Stanhay Webb seven-row sugar beet drill was fitted to the Robotti frame. “A seven-row beet drill is unusual,” John admits.
It meant pre-drilling cultivations were important to produce a level seed-bed so the Robotti could travel without much movement and keep to 50cm row spacings to allow the crop to be harvested successfully with a six-row beet harvester.
Drilling
Before starting, Tom had to map field boundaries and obstacles in every field, so the Robotti could generate a drilling plan and a route map.
In a difficult wet spring for sugar beet drilling, the range of soil types on the two farms – black fen soil on the 50ha in Cambridgeshire and Grade 1 silts ranging to slightly heavier soils in Lincolnshire – was helpful to match soil type with weather.
Drilling began at the end of March and took until the end of April to finish. “That’s longer than we would expect, but wasn’t unusual for the season even for those using conventional equipment,” says John.
One challenge was the software controlling operations, which meant the robot would stop before dropping the drill and then going forward.
“That isn’t great because that’s how you block up a drill, especially when it’s wet, so we had to make some adjustments and use a manual override to lower the drill while moving,” he adds.
A software update should overcome that issue for the coming season, he adds.
Other small details during drilling could also be improved, although most were due to operator inexperience rather than the system.
“It was things like the ends overlapped a little, and the robot snaked around the corners on headlands a little rather than leaving straight edges, which is obviously difficult for the harvester. But these are things that are easy to improve in year two of the project.”
Drilling speed at around 1ha/hr is also slower than a conventional system, perhaps not surprisingly, when comparing a seven-row drill to 12-row systems, although John suggests forward speeds to around 7km/hour with the Robotti might not be far off what you would drill with a 12-row classic Monosem sugar beet drill.
But with no automatic sensing of when the drill hopper was empty or for blockages, the Robotti also needed monitoring, which limited output compared with a fully autonomous system.
In year two, John and Tom hope to complete drilling in around 10 days through the identified improvements in logistics and performance.
Ultimately, British Beet Research Organisation plant counts showed similar plant establishment between a conventionally drilled field and a neighbouring Robotti-planted field set up as a comparison in Lincolnshire at 96,000 plants/ha and 93,000, respectively.
Weed control
As well as drilling, the project, supported by some British Sugar funding, is also testing weed control with a purpose-built seven-row Schmotzer hoe combined with band spraying in a fully autonomous one-pass system.
The Robotti is fitted with a camera capable of identifying and mapping number and type of weeds to help understand weed pressure and inform decision making.
Future developments could involve spot spraying, but for this project the sugar beet rows were band sprayed between the rows hoed. “It was going back to our principles of reducing waste and optimising applications.
“I’ve always struggled to square in my head spraying bare soil between sugar beet rows, especially if it is a biostimulant or trace element, which seems pretty pointless. So I like the idea of reducing waste, and the aim was to reduce herbicides by 80% by only spraying 20cm over the top of the rows,” John says.
Other applications, such as insecticides and trace elements, were also applied using the band sprayer. Fungicides were applied conventionally as the crop was at full canopy.
While the principle is sound, the initial weed control results have been disappointing, with more refinement required for both band sprayer and inter-row hoe.
“There was quite a lot of learning as we went on,” John says. “To begin with there were issues with [the] hoe throwing soil on top of the sugar beet and we had to change the nozzles for the band spraying as they were too narrow with too fine a spray. As a result the weed control was not as good as the conventional approach, which used the same herbicides.
“While we did save about £90/ha on herbicides, it came at the cost of some yield, as the Robotti comparison field yielded 90t/ha, but the conventional system achieved 99t/ha,” John says. “It’s not a big difference, but at £40/t for beet, you don’t need a lot of difference.”
The trial was designed to be cost neutral, with the cost of drilling, four spray passes and chemical savings calculated to be around £300/ha, which is what Autonomous Agri Solutions charged to run the Robotti over 150ha.
If the concept is successful, the company is planning to offer it as a service, albeit not necessarily at that cost, rather than sell individual machines to farmers, although both business models are possible.
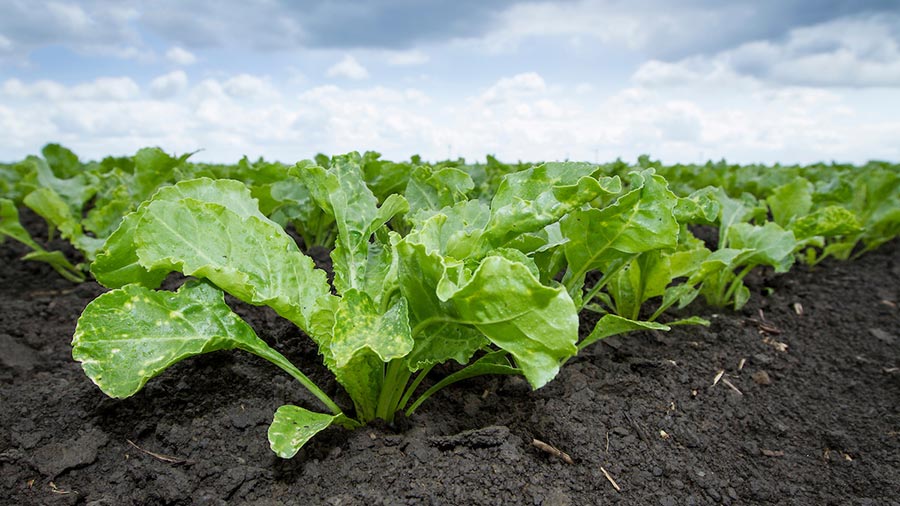
© Gary Naylor Photography
Year two
Year two of the project will see some further tweaks, with the potential to add fertiliser placement at drilling, and possibly to look at Conviso Smart herbicide-tolerant varieties, which would reduce the number of weed control spray passes to just one. “I think it is an option, but the spraying of the row would have to be perfect,” John says.
Potentially that would help with one other drawback highlighted by this year’s trial, that of keeping up with the weed control programme using one machine with a limited operating width over 150ha.
“We did have to spray the Cambridgeshire trial on the black soil, where weeds grew quickly, conventionally in between using the Robotti,” John notes.“It was difficult to get the timing right with the intensity of weed pressure, whereas in Lincolnshire we had one field that only needed spraying twice.”
The trial is providing evidence that an autonomous approach to drilling and weeding sugar beet could be possible, albeit with some challenges to overcome.